― Mazda Digital Innovation(MDI)―
マツダデジタル革新(MDI)の概要
産業革命以来の製造業にインパクトを与えつつあるデジタル革新の波が、自動車業界にも押し寄せつつあります。マツダは、プロセス革新と併せて、最新のインフォメーションテクノロジー(IT)を使った、企画から量産までの製造業としてのデジタル革新に着手しました。
マツダデジタル革新プロジェクトは、製造業としてのデジタル革新をすることによって、その企業構造をAgile(小回りが利く、軽快、柔軟)に、小ロットでも利益が出る構造へと変革し、競争力の抜本的強化を図り、21世紀の製造業として、この面から世界最先端の企業に成るべく、挑戦するものです。
マツダデジタル革新の具体的な内容は、
- 製品設計や生産設計を3次元設計し、全てデジタルデータ化された製品の「デジタルモックアップ」を作り、同時に、全てデジタルデータ化されたプロセス/要具/設備の「デジタルファクトリー」を作り、実際に"物"を造る前にバーチャルシミュレーション(デジタルデータで仮想的に設計や製造をする)を行います。
- 開発活動に関連する品質、性能、コスト等のプロダクトデータ及び開発プロセスのデータも併せてデジタル化して、企画から生産までの各マイルストーンを通して、リアルタイムの「プロダクトインフォメーションマネジメント(PIM)」(商品情報管理)を行います。
- デジタルデータと実際の"物"のデータの関係付けを一致・統合できるコンピュータメジャリング機能付の加工・組立装置を投入し、プロセス、作業時間、品質管理等を含めた「デジタルショップフロアマネジメント」(コンピュータによる工場の現場管理)を行います。
- インターフェースが保証されたデータに基づいて、各々独立に造られた部品が、支障なく、ダイレクトに、組み立て出来るようにしていきます。
- CADデータに基づいて、違った製品でも、専用ではなく汎用のインテリジェントな設備で生産できる、「デジタルフレキシブルマニュファクチャリング」(コンピュータデータに基づいて柔軟に製造する)にしていきます。
製品設計、生産設計を通してバーチャルシミュレーションをコンカレント(同時併行)に、協働作業で、行えるようにし、又、デジタルな世界と実際の"物"の生産の世界迄をシームレス(継目なく)につなぐことによって、開発期間の短縮、開発費/工数の削減、設備投資の削減、品質の革新を行います。
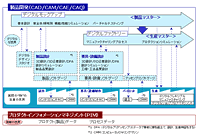
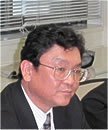
福武 映憲
福武 自動車産業は、日本の製造業の6~7割が関連する裾野が広く、日本をささえる基幹産業と言われています。
今、日本のすべての製造業は、低コスト、高品質、短納期に挑戦されています。このことが実現できなければ生き残れない状況です。
中でも、スピーディな商品(製品)開発により、お客様のニーズに迅速かつ的確に応えることが、主な課題になっていると思います。
マツダデジタルイノベーション(Mazda Digital Innovation以下MDI)により、すばらしい成果を挙げてこられた御社の取り組みについてお話いただければ、私たちのお客様にも大変参考になると思います。
MDIの歩み
木谷 MDIがスタートしたのは1996年ですが、それ以前は、設計部門で作成されたCADデータが完璧でないために試作・生産技術部門でフィレットをかける等の追加のCAD作業を行ないながら金型設計やNCデータ作成を行なっていました。また、全ての部品が3次元データ化されていなかったため、試作車の組立段階で干渉問題が発生し、金型修正・設計変更等の手戻りが発生する構造になっていました。
1995年に初代のデミオの開発で、設計段階から全ての部品を完璧に3次元データ化し、試作・生産技術部門での手戻りを削減させるプロセスをトライアルし、MDIの有効性を確認しました。その成果を受けて、新車の開発から生産に至る全プロセスをデジタル化し、開発の効率と製品の品質などを向上させることを目指して、1996年8月に全社トップダウンでMDIがスタートしました。
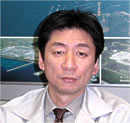
室長 木谷 昭博 様
「MDIは、商品開発プロセス革新の強力なキーイネーブラー。」
【MDI フェーズⅠ】
フェーズⅠでは、車すべてについて、設計のすべてのデータを3次元データ化する「デジタルモックアップ」を実現しました。
これにより、CAD/CAMを使っている金型メーカー、部品メーカーから、金型設計が非常にやりやすくなったという声をよく耳にしました。全自動車メーカーの金型を製作しているサプライヤーさんからも、マツダのCADデータが一番品質がよく、よくできているというお褒めの言葉をいただきました。
【MDI フェーズⅡ】
試作、生産技術、検査などの領域でも、設計のCADデータを使った3次元の治具設計など「デジタルファクトリ」を実現しました。
モノ作りのところも製品の3次元データ、金型の3次元データが揃い、モデルを作らないで直彫り、仕上げレスができるようになりました。
工作機の精度が高いので、CADデータの面の品質がそのまま反映されます。仕上げレスにするには、CADデータの面の品質が重要です。
当時は、CAMでカッターパスひとつ計算するにしても、計算時間も莫大になり、職人さんが仕上げるのが早いのか、機械で長時間加工するのがいいのか、問題にぶつかりました。やっと今、計算時間も早くなり、仕上げレスで採算ベースにのってきました。
【MDI フェーズⅢ】
2000年4月から始まったフェーズⅢでは、試作レス、実験の設備やバーチャルテスティングに苦労して取り組んできました。CAEの利用を加速するのがフェーズⅢです。現実の物理現象にはばらつきがありますから、CAEの結果と現実の物理現象を一致させることに関しては、まだ発展途上です。
多くの部品を扱っていますので、開発活動に関連する品質、性能、コストなどのプロダクトデータや開発プロセスのデータもデジタル化して、開発車種の目標管理、進捗管理、作業指示、履歴管理などをリアルタイムの「PIM(Product Information Management)」(商品情報管理)を運用しています。
小規模の金型メーカーも、CAD/CAM/CAE、金型部品の管理、構成情報などをどう扱うか、という点では同じですから、それの拡大版だと思っていただくとわかりやすいと思います。
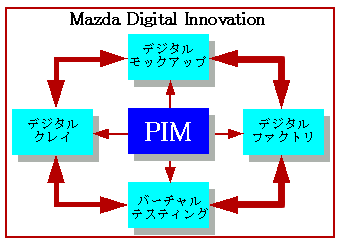
【MDIフェーズⅢ】
2001年度、マツダはMDIフェーズⅢを引き続き実施し、開発期間の一層の短縮、車両性能の向上を目的に、新たに20台の最新鋭設備とバーチャルテスティングシミュレーション設備を導入しました。また、フォードグループとの共同開発を行う上で、共通のデータベースを構築することももう一つの目的です。
当期、マツダはフェーズⅢで予定している内、約80%のフィジカルテスティング設備と50%のバーチャルテスティングシミュレーション設備を導入しました。フェーズⅢの完了により、マツダは新車開発におけるデザイン決定から量産開始までの開発期間を、これまでの18ヶ月から14ヶ月と4ヶ月短縮すると共に、一層の効率化による開発費の大幅な削減を目指します。これにより、マツダは市場に導入するまでの期間を短縮し、お客様のニーズにあった商品をタイムリーに市場に導入することができるようになります。フェーズⅢの総投資額は175億円で、1996年の導入以来MDIへの累計投資額は410億円となる予定です。
コンカレントに協働作業で
福武 CAD/CAM/CAE/PIMをトップダウンで実施され、さらにサプライヤーさんとも連携して進めてこられたのは、日本ではマツダさんが最初ではないかと思います。
3次元化の取り組みで、3次元情報がもたらす効果は何でしょうか。
木谷 従来は物になってまたは物を見て設計上・生産上の問題が発見される構造でした。3次元CAD化により物を作る前に問題が容易に発見できるようになりました。3次元CADデータと基にしたデザインレビューも商品開発の各段階で頻繁に行なわれています。
3次元設計データの展開により、金型部門では3次元金型設計や金型の直彫りCAMが容易になり、金型の品質向上と期間短縮さらにコスト低減が進みました。
大切なのは、3次元情報を使用して自分達の業務プロセスをどう変えるかを時間をかけて地道に構築することにつきると思います。
福武 3次元データを使いこなして効果を出さないと、サプライヤーさんも生き残れないのですね。
木谷 マツダの3次元データ化が進み、CADを買ったけれどなかなかうまくいかないという相談を、MDI導入当初は受けました。
マツダも技術指導やCAD自身の機能改善を行なって、導入したCADが無駄にならないように支援しました。サプライヤーさん自身もかなり工夫や改善をされて、現在では3次元化が日常的なレベルになっています。
田神 MDIをはじめて200社ぐらいのサプライヤーさんに同じCAD環境を揃えていただきました。8割ぐらいの自動車部品は、サプライヤーさんに製作していただいて納めていただくという構造になっていますので、マツダだけがデジタル化をして頑張りましても、高品質、安価、短納期ということは実現しません。
マツダと足並みをそろえてサプライヤーさん自身にもイノベーションをしていただかないと、MDIは実現しませんので、我々と一体となって取り組んでいただきました。
また、サプライヤーさんの多くは複数のOEMさんと取引きをされており、マツダだけではなく国内外のOEMさんから新しい開発のスタンダードとしてデジタル化が求められています。
大変でしたが、サプライヤーさん自身が生き残りのための施策として取り組まれたと思います。
滝口 マツダはMDIを始めるのだと、200社ぐらいサプライヤーさんを集めて2~3回説明会を開催しました。そのときにサプライヤーさんに、皆さんもこれについてこないと、マツダの仕事がなくなるというのではなく、グローバルなビジネスの中で生き残れない、だからやらなくてはいけないんだということを、かなり強いトーンでお願いしました。
ただ、当時のCADシステムはまだ品質も悪く、ずいぶん迷惑をかけて大変だったのです。MDIを始めて7年になり、やっと今当たり前のツールになってきました。
バーチャルテスティング
福武 ボーイングでは、777の開発において、試作をせずに、短納期で作り上げました。車作りにおいて、フェーズⅢで取り組まれたバーチャルテストの適用がどれくらい進んでいるのか教えていただけますか。
木谷 バーチャルテスティングの導入により、試作回数や試作車の台数もかなり減ってきたのは確かです。しかし、完全に試作車が要らなくなるというところまではきていません。
福武 新型のエンジンを作られると、走行テストはやはり人が乗って走らせるのですか。
木谷 そうです。走行テストは官能評価の領域が多く、これをバーチャルテストで代替するのは相当難しいと聞いています。
福武 耐久性などはどうでしょうか。
滝口 三次自動車試験場に、耐久試験路があります。ここで、テストドライバーが24時間365日走ります。
MDIではITだけではなく、実験設備、試作設備にも投資しています。耐久試験では、実際に走ったデータをロードシミュレータにインプットして、実車走行と台上走行とのコリレーションをとっています。台上走行試験を、さらにバーチャルテスティングで置き換えます。これを繰り返し、かなりのレベルでコリレーションがとれるようになってきました。
まだ簡単にはいかないですが、将来的には耐久試験をなくすことができるようになると思います。
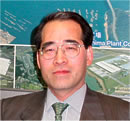
推進部
部長 滝口 哲郎 様
「車をシステム、コンポーネントに体系的にばらして、すべての性能に実験設備を作って検証し、すべてバーチャルテスティングに置き換えるというものです。」
木下 耐久性、剛性評価、振動系など、そのようなデータをいかに使うかがポイントですね。
木谷 ラボテストのデータをもとに、どう定量化して、バーチャルテスティング、CAEのソフトに組み込むかを自動車メーカーは力を入れて取り組んでいますし、そこが技術開発のひとつのポイントでしょうね。
田神 MDIでCAD化が進んだ結果、CAEの適用も一段と加速されましたが、性能全体から見ますと、カバーできている範囲はまだまだ満足のいくものではありません。今後解析技術の開発が必要であり、そのためにも実際の現象を正確に把握し、再現し、更に予測技術へとつなげていくバーチャルテスティングの考え方が一層重要になると考えます。
マツダではバーチャルテスティングを支える仕組みの一つとして、設計意図と得られた性能とを車両からコンポーネントまでの各レベルで管理する仕組みの構築を進めています。設計要件や部品などのCADの情報と連携させて、それがどのような性能を示すかを徹底的に管理していく。これもノウハウのひとつであるという観点で、性能情報管理のシステムを構築しています。
このように精度の高いデータベースが蓄積されると、CAEの予測精度も上がると考えています。その領域をTIM(Testing Information Management)という名前で、HZSさんに開発のご協力をお願いしています。
滝口 バーチャルテスティングをフェーズⅢから本格的に取り組みました。大きな考え方は、車をシステム、コンポーネントに体系的にばらして、すべての性能に実験設備を作って検証して、すべてバーチャルテスティングに置き換えるというものです。それが全部できあがり、多くのデータが蓄積されると、早い段階でバーチャルで車を作って評価できるようになります。これが大きな目標です。それを管理するのがHZSさんに手伝っていただいているTIMです。今は、3次元デジタル化の基盤ができてバーチャルテスティングやTIMに着手した段階です。
今、一番難しいところに差し掛かってきたと思います。
木下 そのようなデータをサプライヤーさんにも公開して、部品設計に活用するということもありますか。
田神 あります。逆にサプライヤーさんのほうが豊富な情報を持っている可能性が高いので、是非いただきたいです。CADの領域、形状のコラボレーションはだいぶできてきましたから、今後は、Deep Styleなコラボレーションという意味で、性能の領域に関してもコラボレーションを進めたいと思っています。
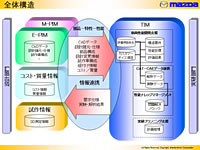
RX-8の開発
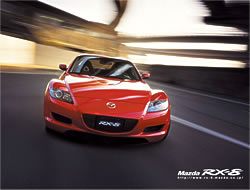
福武 RX-8の開発におけるMDIの成果など、お話いただけますか。
木谷 RX-8は新しいことづくめです。新しいロータリーエンジン、観音開きのセンターピラーレスのセンターオープン式フリースタイルドアという車の構造等々。これら新しい挑戦が短期間で量産できたのは、MDIの貢献も大きいと確信しています。
RX-8の量産化をスタートするにあたり、新型ロータリーエンジン「RENESIS」を組み立てる工場を大幅にテコ入れしました。これまで、主要部品は熟練した技能工の手で一つ一つ高精度の部品加工を施していましたが、コンピュ-タを使ったデジタル技術をフルに活用して自動化を行い、大幅に進化しました。
田神 具体的には、RX-7と比較し、デザイン決定から量産開始までの開発期間を、27ヶ月から19ヶ月と8ヶ月短縮するとともに、価格面でも、RX-7では、294~399万円でしたが、RX-8では、240万円~275万円でご提供できるようになりました。
これも、MDIにおける効率化による開発費の大幅な削減の成果であり、市場に導入するまでの期間を短縮し、お客様のニーズにあった商品をタイムリーにご提供できるようになりました。
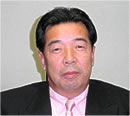
推進部
CAE/CATグループ
マネージャ
田神 章一 様
「情報を挿げ替えることによって、全体の性能を予測できるような構造を作り上げていく必要があります。」
滝口 最終工程の組立ラインでは、品質上欠かせない数多くのテストシステムを導入しました。従来、熟練工の腕(技)で判断してきた物を、データ化し、工程毎にエンジン機能を定量的に計測し全数保証するものです。クラキング・リーク・コンプレッション・コールドテストをはじめ、11ものテストシステムを導入しています。
福武 アテンザは、2003年のカーオブサイヤーを獲得され、コストパフォーマンスが非常にいい車といわれていますが、これもMDIの賜物でしょうか。
田神 マツダのブランドDNAは、「Stylish:センスの良い」、「Insightful:創意に富む」、「Spirited:はつらつとした」。これは明確にターゲットされた市場を対象に設定されており、アテンザは、どのようなお客様にどのような車を提供するかを本当に体現した車です。3次元で設計し、シミュレーションして、いろいろな挙動を解析するなど、実現するための道具立てとして、MDIで展開したものが大いに役立ちました。
福武 データが蓄積されてくると、お客様のニーズをうけて、車のコンセプトを入力すると、それを満足する仕様がアウトプットされるということも可能でしょうか。
田神 お客様がこんな車が欲しいといったときにデザインが出てくるということはありませんが、仕様に関しては、蓄積したノウハウ情報から導くことはかなりのレベルで出来ると思います。超短期に派生車を開発する場合などは、大いに役立つものと考えられます。ただ、お客様のニーズが劇的に変化しており、データそのものの鮮度をどのように保つかという点はこの分野でも大きな課題です。
設計の再利用
福武 御社は先駆けて革新的なことに挑戦されてきていますね。
岡村 これまではコストを下げて、短期間で車を開発するために、部品の再利用を行ってきました。これからは、個々の部品だけでなく設計を再利用するということを考える必要があり、それがバーチャルテスティングにつながるのではないかと思っています。物を再利用するだけではなく、以前に設計したものを再利用して短期間で作る。コンセプトから物を作るのも、過去に設計したものが再利用できれば、可能になると思います。
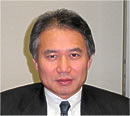
推進部
CAD/CAM/PIMグループ
マネージャ
岡村 一徳 様
「これからは設計を再利用するということを考える必要があり、それがバーチャルテスティングではないかと思っています。」
滝口 同業他社も自動化に取り組まれています。マツダは、違う意味で自動化を試行していかないと、競争に勝っていけません。他社比較で十分競争力があると思います。
岡村 MDIで開発の方法は変わってきましたが、その前段階でどういう車を作れば売れるのかということを、MDIというITで支援していければいいと思っています。
設計というのは基本的に試行錯誤ですから、いい車を作るには、やはり試行錯誤があります。
新しい道具がそろって開発の方法も変わりましたので、その中でいかに効率化するかということがこれからの課題です。
CAEツールとエンジニア
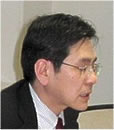
木下 篤
木下 CAEのツールが手軽に使えるようになり、使うべき人が使うようになったと思います。サプライヤーさんも含めて、CAEの利用についてはどうでしょうか。
木谷 サプライヤーさんも含めて、プレスの成形性解析、流動・凝固解析等の活用は、製品設計及び金型設計プロセスに定着しています。
自動車メーカー間の価格競争は厳しく、既存の生産技術で難しいことでも、挑戦して厳しい目標を達成する必要があります。何回も物を作って試すより、CAEを駆使して目標を達成するプロセス構築がとても重要になっています。挙動の可視化により不具合要因の解明も物で行うより容易になっているケースもあります。
木下 技術と道具を用意しないと要求に応えられなくなりますね。我々のお客様で一番困られているのが技術者を育てることです。
木谷 我々のところでもベテランのノウハウの伝承や技術者の育成は課題です。
CAEを活用してプレスの成形技術者を育成する試みをやったことがあります。ベテランの人からは技能伝承教育が容易になると好評でした。
木下 サプライヤーさんも入り込んで一緒にやっているという仕掛けもあるのですか。
田神 商品開発の早い段階からサプライヤーさんと共同で開発を進めることは非常に多いです。CAEの分野におきましても、マツダの環境を使っていただきながら自社の製品について様々な解析を行っていただくケースがあります。CAEの人材育成という観点から見ますと、私どももサプライヤーさんのエンジニア育成に積極的に協力させていただいておりますが、サプライヤーさん自体が貪欲に解析技術を身に付けようとされる傾向が強くなっています。
CAEの分野に限ったわけではありませんが、人材育成は大変ですが非常に大事ですね。特にCAEの場合、設計や製造の知識をもった解析者が求められる訳で、そういうエンジニアがモデルや解析条件などをチューンアップすることで初めて使えるツールとなり、開発プロセスの中でCAEを根付かせることが出来ると思います。でも、やはりこれは大変なことです。
マツダの場合は、フルサービスサプライヤー制度という、設計から製造、市場へ出荷した後の品質保証まで一貫してサプライヤーさんにお願いするという制度もあります。そうなりますと、CAEなどを駆使していただいて、解析的にも問題のない部品を提供していただくということが当然の条件になってきます。
滝口 MDIで挑戦したのはCAD/CAM革新でした。これからは、CAEと情報管理が重要なテーマになっていくのではないでしょうか。
HZSへ
福武 最後に当社へのメッセージ、アドバイスなどお伺いできますか。
田神 HZSさんは、真心の会社であり、大変信頼感もありますが、正直すぎるように感じます。我々も、イノベーションを与えてくれる会社を求めています。もう少し夢を見せてくれるような提案もあったほうがいいのではないでしょうか。
福武 本日は、デジタル化による御社のさまざまな取り組みについて貴重なお話をしていただき、どうもありがとうございました。