一人ひとりの理想の義歯づくりを追求
和田精密歯研様は、1958年の創業から50年以上にもわたり歯科技工業界のパイオニアとして、一人ひとりの患者さまに合った入れ歯・差し歯を作り続けています。
その理想の義歯づくりのこだわりは、いつでもおいしく食べられる口もとが「口福(こうふく)」につながるという想いがあるからです。従来の技工製品に加え、オリジナル製品や最新デジタル技術による審美性に優れた製品、新素材の製品を次々に研究・開発され、3Dプリンター(レーザーシンタリング技術)によるクラウン(差し歯)、入れ歯の製造も、その取り組みの一つといえます。
今回は、医療用ハイエンド3Dプリンター「EOSINT M 270 Dental」の活用法や歯科技工技術の取り組み、今後の展開などのお話をお伺いしました。
日本における歯科技工の技術革新
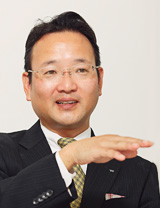
和田 主実 様
当社は、創業者の和田弘毅が歯科技工という業種に着目し、和田精密鋳造研究所を1958年に開設したことに始まります。当時は、ニッケルクロムなどの材料で金属床(入れ歯の土台)やクラウンを鋳造し、大阪で営業をしていました。
それが、全国へと大きく飛躍したのは、差し歯としてメタルボンドポーセレンクラウン(陶材焼き付け鋳造冠)の製造を始めてからでした。この技術は、七宝焼と同じ原理で金属の上に陶材を焼き付けるものです。当初、歯科用のその技術、材料が日本にはなく、1962年に和田弘毅が米国へ渡り日本へ技術を持ち帰ってきました。そして、材料のレシピを試行錯誤しながら考案し、メタルボンドポーセレンによるクラウンの製造を始めたのです。その当時、日本では一部の歯科医師の先生や数人の技工士が同じように海外から技術を学んでいましたが、全国に供給できる数ではありませんでした。そこで、各地の歯科医師の先生から当社へご要望をいただくようになり、全国への普及活動に取り組みました。
現在では、全国各地に事業所と製造拠点(ラボ)があり、約670名の歯科技工士が差し歯や入れ歯を製造しています。
進化する歯科技工の技術と材料
CAD/CAMシステムと加工機を導入
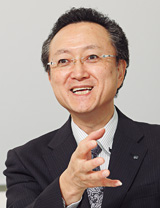
樋口 鎮央 様
日本の歯科技工所では、鋳造するロストワックス法での製造が一般的でしたが、十数年前から材料や技術が進化してきました。
2000年ごろには、日本でも差し歯の材料としてセラミックスのジルコニアが使われ始めました。このジルコニアは、金属アレルギーの心配がなく、非常に硬いため耐久性に優れ腐食しにくいなど、さまざまな利点があります。以前は、あまりにも硬すぎて加工が困難だったジルコニアでしたが、CAD/CAMによる歯科専用の加工システムが実用化されたことで、日本でも広がってきました。さらに2014年4月から小臼歯に限ってCAD/CAM冠(CAD/CAM製作による複合樹脂クラウン)が保険適用となった背景もあり、小型で低価格な加工機が普及してきました。
当社は、早い段階から加工機に注目していたので、初めて導入した1993年からその時代に適応したCAD/CAMシステムと加工機を導入し、製品作りに活用しています。
クラウン製造で広がるレーザーシンタリング
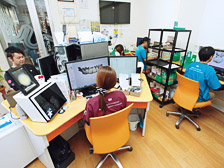
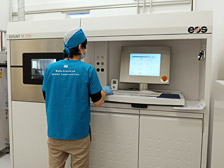
もともとメタルボンドクラウンは、貴金属のフレームにセラミックスを焼き付けた構造でした。それが、2008年ごろから貴金属の高騰が続いたため、価格が安定したコバルトクロムを使うケースが増えてきました。ただし、コバルトクロムは貴金属に比べ、鋳造でぴったり合わせるように作るには手間がかかるという問題がありました。また、CAD/CAMを利用して、鋳造と同じものを削り始めていましたが、材料の7~8割は削って捨てる部分になり、無駄が多いという問題もありました。
そこで、鋳造法のように手間と時間がかからず、加工機のように材料が無駄にならない製造方法として注目されていたのが、3Dプリンティング技術の一つであるレーザーシンタリングでした。海外ではクラウンの製造などで既に普及が進んでいます。
当社では、海外で開催される歯科医療の国際展示会などを通じてレーザーシンタリングの可能性に着目し、製品や技術の情報を収集してきました。そして、いくつかの装置を比較・検討し、歯科医療分野で実績のある独EOS社の3Dプリンター「EOSINT M 270 Dental」(以下EOSINT)を導入しました。この装置の国内総代理店がNTTデータエンジニアリングシステムズ(以下NDES)でした。
EOSINT M 270 Dentalの活用
EOSINT本稼働までの試行錯誤
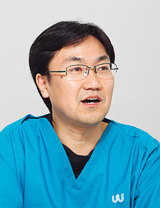
主任 森島 正治 様
現在も国内でレーザーシンタリングを導入している歯科技工所は当社だけです。ですから、導入後は手探りの状態からの立ち上げになり、非常に苦労しました。
EOSINTの操作方法については、NDESに問い合わせれば的確に答えていただけるので造形はできます。
しかし、当社は歯科医院からお預かりした患者さまの歯型にぴったり合うクラウンを作る必要があり、それは手作業で行っている鋳造法と同等の品質が求められます。そのため、さまざまなテストを実施してきました。
まずは、歯型の模型に対して、ぴったりと適合したクラウンを作るために、パラメータなどの調整を始めました。その造形するクラウンは、1本だけのものから14本までつながっているものもあります。そのさまざまな形状のクラウンをEOSINTの造形領域250ミリ角の中に配置するので、その位置によっても適合性が変わります。このようなノウハウも蓄積していきながら、いろいろなパターンのテストを実施しました。これは、適合精度を向上させる狙いもあります。
その他にも、鋳造欠陥が起こる鋳造法に対し、レーザーシンタリングの場合は、その現象が発生しないことも実証する必要があります。造形したものをカットして顕微鏡による状態の検査も行いました。
また、大学に依頼したテストもあります。例えば、金属イオンの溶出によって歯茎が黒ずむ可能性に関してデータの収集・分析を行いました。
こうしたテスト・調査の結果、鋳造法と比較してもそれ以上の品質を保てることが実証できたため、自信を持ってEOSINTの本格稼働を開始したのです。
デザインから造形までの作業の流れ
全国の当社ラボには、3Dスキャナーを導入しています。まず、そこで造形するものをデータ化してデザインが終わると、大阪本社のサーバーにデータを入れます。次に、大阪のCAD/CAMセンターでは、サーバーからデータを取り、250ミリ角のプレートへの配置やサポートの設計などのCAM操作を行います。この筒状のサポートは造形後に切除して、その部分を研磨するため、実際の歯と接着する部分には絶対に立てることはできません。そのため、クラウンでは歯の外側にサポートを付けて、できるだけ数を減らすように設計しています。
EOSINTでの造形は夜間に行い、1日に平均200~250個のクラウンを作っています。その1本当たりの造形時間は約3分となり、鋳造法と比較しても生産性は向上しています。
こうして造形したクラウンは各地のラボに送り、技工士がセラミックスなどを焼き付けて加工した後に歯科医院に届けます。歯科医院の先生方から、EOSINTで造形したクラウンは、歯型にぴったり合うという評価をいただいています。
負担軽減と生産効率アップを実現
各地のラボの効果として、クラウンの一部をEOSINTの造形に置き換えることで、技工士の負担軽減と生産効率の向上が挙げられます。また、技工士としての能力を高めるため、日々進歩する歯科技工において、新技術・新素材の研究・開発に積極的に取り組むことができるようになります。
クラウン
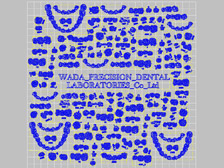
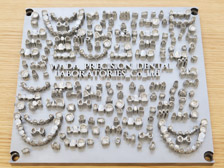
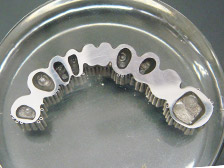
今後の展開について
金属床の造形に取り組む
EOSINTは、大阪と福島県に開設した東日本加工センターに導入しています。万一のトラブル時に造形が停止してしまうリスクを考えると、バックアップ対策として2台のEOSINTが必要でした。
これまでは、主に差し歯をEOSINTで造形していましたが、これから高齢社会の進展とともに、入れ歯の需要が増えると予想されます。入れ歯と差し歯では造形の技術が異なりますので、入れ歯を専門にしたスタッフが多く在籍する東日本加工センターで、入れ歯の土台となる金属床の造形にEOSINTを使えるよう、これから検証を実施する計画です。
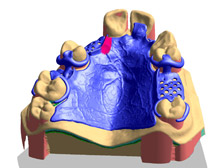
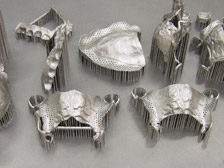
(サポート付)
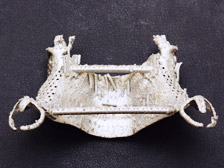
広がる3Dプリンターの活用範囲
EOSINTの活用範囲を広げて、矯正治療後に歯並びを安定させる保定装置も造形しています。一般的な保定装置は分厚い樹脂製になり、使用期間が1~2年と長期にわたるため、汚れやにおいが付きやすくなっていましたが、EOSINTで造形すると0.5ミリの薄く清潔な保定装置が作れるため、患者さまに喜ばれています。その他にもEOSINTの活用を検討しています。
矯正保定装置
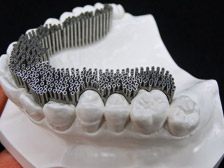
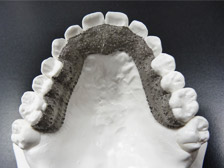
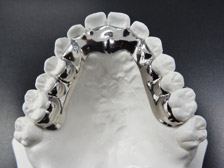
より良い労働環境を目指す
歯科技工業界の問題なのですが、この数年で歯科技工士の労働環境が良くないというイメージが定着して歯科技工士学校に入学する学生が減少しています。
当社は、この業界の中でも入社後の定着率は高い方ですが、より良い労働環境を目指し、さまざまな改善に取り組んでいます。まず、各地のラボで建屋が古い所は、移転や改装によりきれいなオフィス環境を整えています。その一番新しい建屋が東日本加工センターになります。さらに、労働時間についても終了時間を19時または18時半にする活動をしています。帰宅後に有意義な時間を過ごすことができれば、日々の仕事の励みにつながります。
NDESへの期待
今後、入れ歯への保険の適応範囲が広がれば、大阪、福島の2カ所のEOSINTでは製造が追い付かなくなります。その結果、各地区にレーザーシンタリングが必要になったとき、現在の高価格なEOSINTではなく、価格的にリーズナブルな装置を期待しています。
NDESは、EOSINTに熟知しているのでメンテナンスやサポートについても信頼しています。我々、歯科技工の仕事は、歯科医院や患者さまへの影響が大きいことから、トラブルは早々に解決したいという思いがあり、それにNDESは迅速に対応してくれています。
これからも、きめ細かなサポートや情報提供に期待しています。
おわりに
歯科技工の現場を訪問させていただいたのは、初めての経験でした。最先端システムを駆使して義歯のデザインや造形をされており、技工士の技能とテクノロジーが融合するこれからの歯科技工の姿を垣間見る思いがしました。
お忙しいところ、貴重なお話を聞かせていただき、ありがとうございました。
会社プロフィール
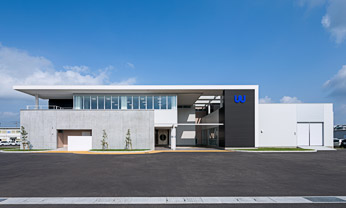
福島県岩瀬郡(竣工2015年6月)
和田精密歯研株式会社
URL http://www.labowada.co.jp(外部サイトへ移動します)
本社 | 〒532-0002 大阪市淀川区東三国1-12-15 辻本ビル6階 |
---|---|
総合企画・生産 | 〒533-0031 大阪市東淀川区西淡路5-7-16 国次ビル |
設立 | 1966年9月21日(創業1958年1月) |
資本金 | 9,950万円 |
従業員 | 1,012名(2015年4月現在) |
事業内容 | 歯科技工製品の製作・販売(インプラント、口腔外科関連、矯正装置、テレスコープアタッチメント、金属床などのデンチャー全般、クラウンブリッジなど)。全国42カ所以上に拠点を展開。 |