「設計モジュール化技法」で「P(新製品開発力)+QCDS(競争力強化)」を実現
![]() |
株式会社 経営システム研究所 代表取締役社長 冨田 茂 様 |
---|
株式会社経営システム研究所(以下、KSK)様は、設計業務改革指導に定評のある製造業向けコンサルティング集団です。業務改革とシステム導入を同時並行で進め、「設計モジュール化」や「座席予約生産化」といった手法を用いて、効率化やコスト削減、新製品創造などにつなげる提案を得意としています。今回は、代表取締役社長である冨田茂様に、日本の製造業の未来と同社のコンサルティング手法についての話をお聞きしました。
学生時代から目指したコンサルティングの道
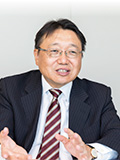
代表取締役社長
東 和久
東 冨田社長は、30年以上にわたり製造業に対してコンサルティングをされており、私たちのプライベートセミナーでも製造業の競争力強化についてのご講演をお願いしています。まずは、冨田様のご経歴を伺いたいのですが、どのようなきっかけで製造業のコンサルティングの道に進まれたのですか。
冨田 大学時代、担当教授に、「ハーバード・ビジネス・レビュー」という書籍の翻訳を頼まれ、その中で「コンサルタント」という仕事の存在を知り興味を持ったことがきっかけです。大学当時、家庭教師や塾講師のアルバイトをしていて、毎年、教える内容に変化がないことに飽きてきていたこともあり、世の中の変化に対応しながら、飽きがこない分野で人に教える仕事がしたいと考え、大学卒業後はコンサルティングの仕事に就こうと決めていました。しかし、大学でコンピューターを専攻していたことから、担当教授の勧めもあり、大手輸送機メーカーに就職することとなりました。その会社では、社内の電算化推進室を皮切りに、営業や技術など、いろいろな業務を経験し、その後、システム部門に戻り、技術情報システム構築と、既存のシステム再構築のプロジェクト設計や推進をさせていただきました。この時に実感したのが、「業務の改善・改革無くして、システムの成果無し!」ということでした。
東 この時のご経験が、後のコンサルティングにも生きてくるのですね。
冨田 そうです。実は入社する時から、10年で会社を辞めてコンサルタント会社を作りたいと、上司や周りの人には申し上げておりました。ちょうど入社後10年で、大きなプロジェクトが終わり、退職を申し出たところ、情報システム子会社をつくる話が動き出しており、上司から、お礼奉公としてこの会社の立ち上げを手伝ってほしいとの打診があり、その子会社に出向することとなりました。そこでは、関係会社や協力会社のシステムの導入、自社の生産・製造業務の改革などに3年間ほど従事したのですが、ここでの経験も大変勉強になりました。その後、ようやく独立のお許しをいただき、平成元年の3月にKSKをスタートさせました。
東 会社の設立当初は、仕事を取ることも大変だったと思うのですが、どのように会社を軌道に乗せていかれたのですか。
冨田 元々10年で会社を辞めると考えながら業務に取り組んできていたということもありますが、情報システム子会社時代に、ITメーカーとのお付き合いの中でシステム導入のユーザー事例やシステムの管理手法の講演などをやらせていただいていたことなど、それまでの経験が全て事業に展開できたので、会社を設立した時には、既に仕事がたくさんあったという状況でした。当時の事業内容としては、「業務改革を伴わないシステム導入は、失敗につながる」という自らの経験を基に、製造業を中心に流通業や食品加工業といった企業に対して、業務や組織の変革に関するコンサルティングやシステム構築のアドバイスを行っていました。
東 システムを導入すれば業務改革が図れるという考えも少なくなかった当時では、お客さまからすると新鮮だったのではないでしょうか。
冨田 情報システムはあくまでもツールですから、効果が出ないと意味がありません。前職での経験からシステム導入時のポイントが痛いほど身に染みてわかっていましたから、この経験がコンサルティングをするときに受け入れられたのではないでしょうか。例えば、データベースの整合性が悪く、人事・給与、会計、営業、生産などのシステムが全くつながらなかったことがありました。これは、データベースや統合システムについての知見がほとんどない担当者が、システムの全体像を把握せず個々のシステムを縦割りでバラバラに開発したために起きた現象だったのですが、このままでは使えないため、それぞれのデータベースの整理と、相互の連携や標準化を2、3年かけて行いました。
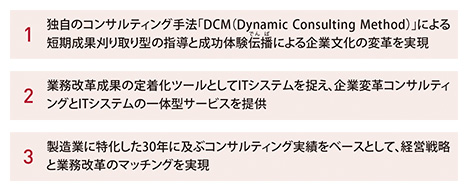
量産メーカーのコスト削減に
有効な「座席予約型同期生産」
東 現在、コンサルティングの対象としているのは、どのような分野の企業が多いのでしょうか。
冨田 個別受注型の組立製造業のお客さまが非常に多いですね。他に、量産メーカーの生産管理なども多く手掛けていますので、自動車の部品メーカーや家電メーカーなどからも相談を受けることがあります。
東 量産メーカーには、どのような提案をされますか。
冨田 量産メーカーからは、在庫と製造コストの削減に関する依頼が最も多くあります。そのため、「座席予約型同期生産」といわれる業務の仕組みとシステム構築をよく提案しています。これは、製品の組み立てと部品の製造や調達を同期させることにより、組立必要部材を使用するタイミングで納入させたり、さらに生産する製品ごとにあらかじめ「生産座席枠」と呼ばれる上限数量と出荷頻度に合わせた生産タイミングのサイクルを設定することにより、受注や出荷指示時に即その生産座席枠に生産から出荷を割り当てたりして、生産後の製品・仕掛り・部材在庫をゼロに近づけようとする手法です。生産計画の立案方法が列車の座席予約に似ているので、このような呼び方になっていますが、組み立てに合わせた「同期生産・同期納入」も考え方のベースになっています。座席予約型同期生産であれば、オーダーを生産枠に引き当てた段階で、その枠に見合った部材が納入されますので、飛び込みの短納期受注が頻発したり、受注数量が多少変動しても、納期遵守率や生産性を阻害することなく、効率的な生産ができるようになります。生産性が3割上がり、在庫が4分の1になり、低かった納期遵守率が100%近くまで上がったという成果が出ています。
日本の製造業を取り巻く環境変化
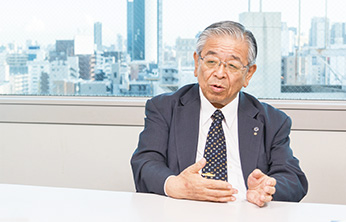
東 近年、日本の製造業を取り巻く環境が大きく変わってきていますが、冨田社長はどのようにお考えですか。
冨田 製造業は今、100年に一度の淘汰時期に入っています。かつて、家電メーカーに再編の波が起きたとき、徐々に衰退していった家電メーカーと新たな道を見つけた勝ち組の家電メーカーとに分かれました。これと同じことが、今、多くの業界で起き始めています。日本の製造業を取り巻く環境を見ると、コスト競争力の相対的低下により輸出が次第に難しくなり、国内マーケットも人口減少やデフレ経済で縮小し、厳しさが増しています。一方、中国や東南アジアなどで民族系企業が多く立ち上がり、第二次世界大戦後の高度経済成長期の日本のように一生懸命ものづくりに取り組んでいます。それはそれでいいことですが、主に生産規模によって、中国などのメーカーとの間にこれだけ大きくコスト競争力が開いてしまうと、市場での付加価値を失いコモディティ化(普及製品化)が進んだ製品を作り続けている企業は、生き残る道が無くなってしまう可能性があります。
東 日本の製造業にとって、非常に厳しいご指摘ですね。
冨田 技術革新の面では、エネルギー転換の遅れが影響しているとみています。エネルギーは、1800年代に水車から石炭への転換が起き、さらに1900年頃に石炭から石油へと変わりました。その後、また100年以上が経過した今日、本来ならば石油などの化石燃料から水素や風力発電などの再生可能エネルギーに切り替わらなければいけないのですが、それが日本ではうまく進んでおらず、技術革新が停滞していることが、製造業を厳しくしている一因だと思います。石炭から石油への切り替え時に、蒸気機関から内燃機関への技術革新が起きたように、製造業は、エネルギー転換期に大きな変革を迫られ、技術革新を繰り返しながら発展をしてきたのです。また、それを乗り越えた企業だけが、さらに発展を遂げられたのです。
東 では、日本の製造業は、今後、どうなっていくとお考えですか。
冨田 今のままではいられなくなると予想しています。例えば、自動車業界では10年後には国内の何社かは淘汰されている可能性があります。自動車の生産台数が中国やインドなどと比べて相対的に減少し価格競争力を落とすとともに、電気自動車(以下、EV)の普及などで部品点数が大幅に減少し、自動車メーカーはもとより、部品ベンダー、自動車業界に需要の多くを依存している工作機械やロボット、二次電池、電子部品、金型、製鉄など、多くの産業分野で淘汰が進んでいく可能性があります。現在、花形である業界が、今の家電業界が過去10年ほどの間にたどったのと同じ道をたどらなければいいと願っています。
淘汰の時代を生き抜くための
「設計のモジュール化」技法
東 コンサルタントの立場から、どのような解決策が提案できますか。
冨田 日本の製造業の未来をバラ色にできるかどうかは、今から日本企業が何をするかにかかっています。従来の製品分野で勝ち負けが決まりつつある今日、採算が取れなくなる事業からどう撤退して、新しい分野に事業をどうシフトさせていけるかが重要になってくるのです。その手段の一つとして、「設計モジュール化技法」を提案しています。一般的なモジュール化とは、システムや製品などを構成要素ごとに分割して機能単位でまとめ、規格化や標準化を行うものです。これを設計に応用し、既存図面をモジュール化して編集設計することで、最も少ない部組品や部品種数の組み合わせによって製品を表現しようとするものです。コストを決定する上で最も重要な単位当たりの部材の生産量を高めることはもちろんですが、モジュール化を実現すると、設計者が図面を引かなくても済む「設計不通過」と呼ばれる状況が生まれ、特に個別受注事後設計型組立製造業の設計部門の効率化には最適な技法であると言えます。設計のモジュール化を起爆点とする業務改革を行い、それをシステム化して取り込むことで永続的で大きな効果が得られます。
東 設計のモジュール化で、一番の難しさはどこにありますか。
冨田 モジュールの分割ですね。部品、ユニット、ブロック、製品という単位のどこで図面を分割してモジュールの単位とするのがベストなのかという判断が、一番の肝になります。ただ、当社では、モジュール分割のポイントを業界別にノウハウとして把握していますので、難しいことではありません。設計のモジュール化ができたら、次に顧客からの製品仕様と、それを実現するための部材や部組品などの機能との関係を、コンサルティングの中で定義していきます。それによって、設計者の介在無しに必要な図面がシステムで抽出できるようになります。例えば、耐食性を求められる製品では、素材を鉄からステンレスに変えるかチタンに変えるかなどを考えますよね。さらに、成形性やコストも加味して部材や部組品を選びます。その設計者の思考の流れを解析、標準化していけば、誰でも同じ結論にたどり着けるようになります。その後、コンサルティングした結果をAI型のコンフィグレーター(自動選定ツール)に取り込んで活用することにより、営業担当者が製品スペックを入力するだけで自動的に図面が抽出され、次の瞬間には部品表が生産部門に渡るといった仕組みが実現できます。当社は、このコンサルティングを主力サービスの一つとしてやってきたことになります。
東 冨田社長は20年以上も設計のモジュール化に取り組まれていますが、企業が設計の効率化を望むのはどのようなニーズからなのでしょうか。
冨田 それには2つのパターンがあります。1つ目は、図面を期日までに出せるようにして製品の納期遅れなどのトラブル解消を狙うものです。
2つ目が、人材を受注設計業務から別の業務にシフトさせたいという経営戦略上のニーズである「パワーシフト」になります。設計者を育てるには長い期間が必要であり、このパワーシフトの方が、今後の日本の製造業では重要になっていきます。当社のコンサルティングでは、一般的に受注オーダーや製造番号の7割程度を設計不通過とするように目標設定しています。実現すれば約3割の設計人材を、よりクリエイティブで成長の見込める新製品開発などに投入できるようになります。必要があれば、新製品創造のコンサルティングも行っています。
生き残りのカギとなるパワーシフト
東 設計の効率化によるパワーシフトという考え方は、時代の変革に対応するための大きな可能性を感じます。
冨田 世界的に自動車メーカーのグループ化が進んでいますが、そこにはEV、燃料電池車、従来のレシプロエンジン車の3本柱の開発を全て1社で対応していくことが不可能になりつつあるという背景があります。協業も含めて、既存の開発・営業・生産環境の効率をできるだけ高めることで、EV開発などの新分野に人材を投入しようと、各社が動き出しているのです。
東 製造業では、開発期間が非常にシビアになっていて、担当者一人に与えられる仕事量とクオリティーの要求がますます上がっていると感じます。担当者が粘り強く頑張るだけでなく、新たな人材を投入するなどの改革も必要だと感じますがいかがでしょうか。
冨田 おっしゃるとおりです。当社のコンセプトは、「企業変革とその結果の仕組み化」です。企業の組織や仕事の仕組みを変えることで効率化を実現し、さらにその仕組みをシステム化して設計や生産、営業といった業務に乗せていった結果、大きな効果が出てそれを持続させることができるようになります。そのための重要なキーワードの一つが、先ほども申し上げたパワーシフトなのです。100年先まで成長できる事業分野を見つけて、そこへどうパワーシフトさせていくかが生き残りのカギになります。今の事業を続けながら、パワーシフトしなければなりませんので、ITなどの最新技術がより重要になってくると思います。
東 既存の業務や組織を改革し、新規ビジネスにチャレンジする場合、変化を嫌う人たちも出てくるのではないでしょうか。
冨田 確かに、 企業が大規模であればあるほど、いろいろな問題が出てきます。今までのやり方を変えたくないというコーポレートカルチャーへの固執をどうやって越えていくかが重要になります。われわれは、成功体験を早く積んでもらうことが効果的だと考えています。これを「成功事例の拡大伝播」と呼んでいますが、最初の3~6カ月程度の期間で見える形の成功事例を作り、それを経営者の方に公式に褒めてもらいます。金一封で表彰してもらえればもっと良く、その後、全社的にそれに取り組むとアナウンスすることで、誰もが「よーし、自分も!」と、積極的になるのです。雪崩を打ったように組織が動き出すのが分かります。
技術力をベースにした
最新鋭の統合ソリューションを
東 私たちは、技術部門と製造部門にまたがる進捗管理やコスト情報を統合的に管理することを目的に、元々別のシステムとして構築されていた「会計・個別原価管理・資材・在庫管理ができるERP(Enterprise Resource Planning)」であるProject-Spaceと、「技術部門が使用するPLM(Product Life-cycle Management)」と「生産計画・工程管理」ができるBiz∫SCAW製番管理を一つにまとめた「統合ソリューション」として展開していきます。これにより、顧客要求への対応力向上と競争力のさらなる強化、生産業務の効率化を進めることができるようになると考えています。
冨田 NDESの強みは、第一に技術に強いことだと思います。それは、CADソフトのGRADEの時代から培ってこられた技術力がベースにあり、製造業に必要な技術的要素を兼ね備えているためです。さらに、そういう技術を核にしたERPも充実しているため、統合ソリューションとしての完成を楽しみにしています。
当社への依頼には、全社システム再構築の投資効果を十分満足させるマスタープランを作って欲しいという案件も増加しています。そういう場合には、営業・設計・生産・原価・品質・サービス・会計などを、企業横断的に網羅できる統合ソリューションが必要になります。しかし、営業や生産などの各領域での効率化は既にやり尽くした感があり、新たにシステムを導入してもなかなか投資対効果は現れてきません。一方で、技術部門における効率化はまだまだ大きな期待が持てる分野であり、技術部門の変革を起爆点として、営業・生産・原価・品質・サービス・会計などの部門を、新しい技術の仕組みとの連携によって効率化できる余地が大きいことに気付いています。また、お客さまからも技術的要素に強い統合ソリューションの要望が出てきており、それを全社的に適用することが求められてきています。
東 技術的要素をベースとした統合ソリューションということであれば、私たちが目指す方向性とも合致しますが、そのご提案ができるようになるまでには、もう一押しが必要だと考えています。
冨田 御社の統合ソリューションができれば、たくさんのニーズがあると思います。その点でも御社に期待されているお客さまが多いのではないかと考えています。技術から始まる統合ソリューションをさらに強化していかれることが、明日の日本のためにもなると思います。
日本の製造業の多くは、これからできるだけ早くコモディティ化していない製品事業分野にパワーシフトを実現しなければ生き残れません。そのためには、設計の効率化が不可欠です。次の次の世代にも日本のものづくりを残していけるように、われわれも微力ながらお手伝いをさせていただきますので、お互いに頑張ってまいりましょう。
東 ありがとうございます。標準化や設計のモジュール化などの業務改革は、システム導入と同時進行で推進 していかなければ、うまく機能しないと思います。そういう意味でも、私たちもソリューションのご提供という側面から、日本のものづくりを支えていければと思います。これからも引き続き、よろしくお願いいたします。
会社プロフィール
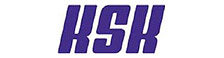
株式会社経営システム研究所
URL http://www.ksk-consulting.com/(外部サイトへ移動します)
住所 | 大阪府大阪市東淀川区東中島1-19-4 新大阪NLCビル12F |
---|---|
設立 | 1989年3月 |
資本金 | 2,500万円 |
事業内容 | 製造業向け各種コンサルティング |
関連するソリューション
関連するソリューションの記事
- 2022年01月15日
-
個別受注型製造業向け仕様選択コンフィグレータ
Delight-Space®のご紹介
- 2021年07月10日
-
4事業部のご紹介(4)
ビジネスインテグレーション事業部
- 2020年04月01日
- 「受注設計製造プロセス 統合ソリューション」のご紹介