西川ゴム工業株式会社様は、Seal and form engineering companyを企業コンセプトにされ、ゴムを中心とした高分子素材を扱った製品の開発、生産、販売という一貫した体制の研究開発型企業です。主力製品であるドアのシール材、ウェザーストリップは国内ではトップシェアを占めています。また、米国、ヨーロッパ、アジアなどに合弁会社を設立され、技術供与による活躍の場は全世界に広がっています。
今回は、HZSよりご導入いただきましたラピッド・プロトタイピング・システムの運用、そして今後の課題などを中心に、金型部 部長 佐々木様、課長 栗坂様にお話をお伺いしました。
事業内容について
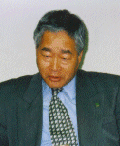
佐々木 様
西川ゴムの製品の内訳は、85%が自動車関連製品、残りの15%が建築・土木・産業資材関連製品、化粧品・医療・エコロジー関連製品です。
主力製品は、自動車関連のシーリング製品で、国内の全自動車メーカ様と取引があり、国内の自動車シーリング関係としてトップシェアの40%強を確保しています。
海外における活躍の場は全世界におよび、開発、生産、販売活動は高い評価を受けています。20年前には、米国のスタンダードプロダクツ社と初めて技術契約しました。そして昭和61年にスタンダードプロダクツ社と合弁で米国のインディアナ州にニシカワ・スタンダード社を設立して、現在ではアメリカに進出している日本の自動車メーカ全て及び、フォード社、ゼネラルモータース社に製品を供給するまでに成長し、工場も3工場、従業員1,600名の規模になっています。
さらに、ニシカワ・エンジニアリング・オブ・アメリカ社を設立し、西川ゴムの北米の拠点としています。また韓国、インドなどアジア地域は独自に事業展開しています。
スタンダードプロダクツ社は米国、カナダ、ブラジル、メキシコ、フランス、イギリス、ポーランド(計画中)に工場を持っている非常に大きな会社です。
西川ゴムは、スタンダードプロダクツ社と共同でグローバル化を展開し、「世界のシェア20%」を目指し、活動しています。西川ゴムは技術を提供し、スタンダードプロダクツ社が工場と人のマネージングをするという役割分担で進めています。
このように米国の企業と事業展開していますので、品質保証についても非常に重要だということで、ISO9001とQS9000*1を取得しています。
現在の西川ゴムは、8.5:1.5と自動車関係が多いのですが、6:4になるように自動車以外の分野にも力を入れています。エコロジー的視野から生分解性素材の研究開発に取り組み、そこから誕生したのがNATULOVEです。これは、西川ゴムの発泡技術によってコンニャク芋を原料に作った天然素材100%の生分解スポンジです。
その他に健康食品分野にも進出していまして、西川ゴムの100%出資の西川物産株式会社で取り扱っています。
環境保護にも積極的に取り組んでいます。ゴム製品からスクラップが出ますが、それを再度リサイクルして、炭にもどして有効活用しようということで、業界で初めて廃ゴムの連続炭化システムを導入して再利用しています。
その他にも、現在問題になっているペットボトルについても粉砕して、発泡化して、いろいろな容器にリサイクルして使う設備も近々建設する予定です。
*1 米国BIG 3(クライスラー、フォード、GM)およびトラック業界(5社)が自動車業界特有の要求事項を付加した共通品質システム規格です。
金型部と設備
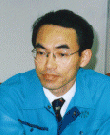
栗坂 様
西川ゴムの金型部の特長は、設計、CAD、購買、検収、拡販を一括して行う組織構成にしているということで金型部31名、西川物産60名、100%に近い取引をしている型メーカ80名を合わせて170名規模で全世界の金型に対応しています。西川ゴムの金型部および西川物産の中で設計に携わっているのは34名です。
金型部の売り上げは20億円で、半分の10億円は海外の金型の仕事になっています。
15年前からCAD/CAM化に注目しており、現在はグループ全体で60台の3次元CAD/CAMシステムを使っています。またマシニングセンター(M/C)は55台、放電加工機は24台あります。工場現場ではM/Cを主に夜間は無人運転で対応しています。
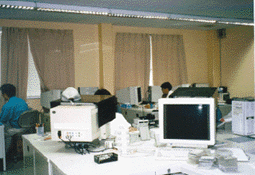
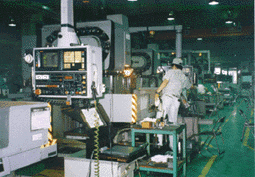
マシンオペレータは3年間ほど現場を経験させた後、CADの教育を半年間行います。そして技量テストをして、合格すると緊急時やCADが忙しいときは、現場のマシンオペレータがCADを操作して、2直体制に入って応援します。
どこの企業もCADのオペレータが足りないと聞きますが、西川ゴムの場合は、現場のマシンオペレータまで全員CADができるのが特長です。
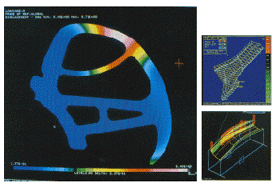
西川ゴムは全世界と取り引きしているので、いろいろなシステムが必要です。その中で、フォード社とマツダ社向けのシステムとしてI-DEASをHZSから導入することにしました。
ラピッド・プロトタイピング(RP)・システム導入の背景
15年前からいろいろなCAD/CAM化に取り組んできましたが、自動車メーカ様からはコストダウンという強い要求が常にあります。
その要求に対応するためには、2つ方法がありますが、まずひとつめに金型の加工法案を見直すことによってコストを下げるということです。正規に作るものを簡便に作るということで、例えば、プラスチックなどは試作型を鋳造で作るとか、onewayの金型を樹脂で安く作るということです。
もうひとつは、量産一発化を目指してツーリングのトータルコストを下げるということです。量産一発化をするということは、物ができてから判断するのではなく、設計段階で完成度をレビューしなくてはいけないということです。
ところが製品形状が非常に複雑なため、コンピュータによるシミュレーションだけでは評価しにくいところがあります。また、機能や性能を保証する以外に、社内でのコストを安くするための作りやすさを評価するためには、コンピュータ上だけでは不十分です。そういうものは、物を見て評価することが必要です。
そこで、ラピッド・プロトタイピング・システム(以下RPシステム)を使って形状を作成し、目で見て評価しようということでHZSから2年前に導入しました。
RPシステムを開発のひとつのステップとして導入し、これで開発全体の効率化を図っていきたいと考えました。
今では、海外や日本の自動車メーカ様に良い評価を受けていますので、その考えが正しかったということです。
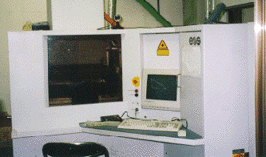
RPシステムの利用
RPシステムを導入しても、単なるワイヤフレームのデータがあるだけではRPシステムは動きません。ワイヤフレームのデータをトリミングし、SPLデータに変換して、RPシステムで見れるようにしなければいけません。西川ゴムは、RPシステム導入前から正確なデジタルデータを作り、100%データ化していましたので、RPシステムを導入してすぐに使える状態にありました。ですから導入して何の問題もなく形状を作ることができました。
RPシステムをどのように利用しているかというと、例えば、自動車ショーのように形状だけを要求されて機能を追求されない場合に使います。まず、RPシステムで形状を作成し、シリコンで反転して、その中に樹脂材を流し形状を作ります。ゴムではありませんが、代用品を作ります。
その他には、自動車メーカ様からの要望で企画段階で形状が少し見たいというときに、正規の金型を作成するには高いので、費用をかけたくない場合などに使います。
このように、お客様から特異要求があったときだけRPシステムを使って形状を作り、ゴムらしきサンプルを作ります。
それ以外にも、自動車のボディーでゴムが取り付く部分を検証する検具として作ります。自動車メーカ様からボディーのデータをいただいて、当社で作ったゴムを検証する検具をRPシステムで作成しています。この部分を鉄板で作っていたら、何百万~何千万円かかります。それに、木型メーカがハンドワークで作ったら精度が出ているかわりませんが、RPシステムではデータで形状を作りますので、精度良くできます。ただ、残念なことに強度が足りないので、壊れることがあります。
先ほどもお話ししましたが、金型部の仕事の半分は海外向けの金型を作っています。海外のデータは変換などで差異が生じるため、金型受注時にRPシステムで作って物の現物承認を得るためにも使っています。
今後の課題
今後の課題は、短期開発の中での量産一発化をするために技術確立をしていきたいということです。3ヶ年で取り組むテーマとして実際に大幅なコストの低減、納期の短縮をやりたいと考えています。その方策として、まずソフトでいえばCAMシステムの見直しです。すなわちNCデータの作りやすさで、等高線加工や自動化を含めた作りやすさです。もうひとつは、高速加工機械の有効活用、そして加工条件の標準化などがあげられます。
短期開発というのは初期開発の場合で、製品設計、金型、物作りのトータル4ヶ月半を3ヶ月にするということです。そうするためには、どうしてもデータベースを活用したデジタル化が必要です。
<短期開発(量産一発化)>
- 製品設計期間の短縮、内容充実
- 得意先とのCADネットワーク
- CADのモデルによる評価、RPシステムによる形状評価
- 成功例、失敗例のデータベース化
- 金型設計期間の短縮
- 得意先とのコミュニケーション、CADネットワーク
- 得意先評価の把握、反映結果のデータベース化
- CAD/CAM時間の短縮
- 等高線加工データの拡大と自動化に強いCAMシステムの採用
- 金型製作期間の短縮
- 高速加工機械の採用
- 仕上げ時間の短縮・精度向上
これらのことを実現することによって、短期開発の量産一発化を目指します。そして世界のシール関係の仕事をし、これまで以上に西川ゴムを世界のツーリングセンターにしていきたいと考えています。
海外との取引が多いので、海外とコミュニケーションができる国際人としての社内教育も必要です。
現在、海外との関連会社とオンライン化することは実施済みです。現在、テレビ会議の導入も検討していますが、そういうツールを使いながら、グローバル化を推進していきたいと考えています。
HZSに期待するところ
RPシステムに関しては、ゴムには柔らかいものや硬いものなどいろいろありますが、できるだけそれに類似するような素材の検討をしてほしいです。例えば、検証用検具に使うときは衝撃への強さなど材質の向上も望みます。
CAD/CAMの話ですが、設計からモノ作りに入るときに、どこのメーカのCAMシステムでもいろいろな小さな問題があります。現在使っているシステムにもCAMに問題はあります。
私が思うには、金型の技術は世界の中で日本が最高レベルです。将来、金型のCAMに関しては、日本が世界を制するでしょう。
しかし、CADに関しては世界的なメーカがあるので日本は非常に難しい立場です。
CADの面で米国、ヨーロッパには負けますが、それを応用し、使いこなしている現場実績データというのは日本が優っています。やはり、日本の金型メーカと協力し、使い方の改善をしていけば、最強のCAMになるはずです。だからCADに関しては大手のCADメーカと組んで、日本が一番強いCAMだけを保持していこうというのを望みたいわけです。5~10年したらその方向になると思っています。
その時に注意しないといけないことは、偏らないということです。例えば、データ交換です。限られたメーカのシステムによるデータしか取り込めないのはだめです。全世界で通用するCADメーカのデータが使えるようなデータ変換を考えてください。内蔵しても結構です。異なったシステムをそろえるには何千万もの投資が必要ですから、問題なくデータ変換ができなければ、これからの国際化には通用しません。
とにかくコンピュータは、異なったシステム間で互換性があるということ、バージョンが変わっても新旧の間に互換性があるということが不可欠です。新バージョンが2~3年前のものと全然違って互換性がないのは非常に困ります。
HZSには、CAD/CAMシステムのCAMだけを取り出して、経験の少ない女性でも、操作できるようなマニュアル化された安価で使いやすいCAMシステムの開発をお願います。
おわりに
西川ゴム工業株式会社様が、自社ブランドとして販売されていますNATULOVEは、天然素材ということと防腐剤、抗菌剤、漂白剤を一切使用していないということで、刺激に敏感なアトピーの方や赤ちゃんに非常に良いそうです。
コンニャクのスポンジは江戸時代からあり、高野豆腐と同じような作り方をしていますが、NATULOVEは、きめ細かい泡立ちを出すのに独自の発泡化技術を使って、均一なスポンジ目(気泡)を作るのに苦労されたそうです。
たいへんお忙しいところ、貴重な時間をさいてお話を聞かせ ていただき、ありがとうございました。この場を借りてお礼申し上げます。
今回の「人とシステム」にNATULOVEのカタログと申し込み用紙を同封しています。詳しくはカタログをご覧ください。
会社プロフィール
西川ゴム工業株式会社
本社 | 広島市西区三篠町2丁目2番8号 |
---|---|
設立 | 昭和24年4月 |
資本金 | 32億5,604万円(平成9年7月1日現在) |
従業員 | 1,646名(平成9年7月1日現在) |
売上高 | 439億6,415万1千円(平成8年度の実績) |
主な営業品目 | 自動車関連製品(ウェザーストリップ・ドアアウター、ウェザーストリップ・サンルーフ、フラッシュマウントモール、サイドモールなど)、建築・土木・産業資材関連製品、化粧品・医療・エコロジー関連製品 |
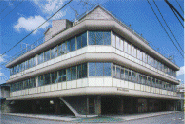
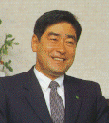
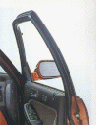
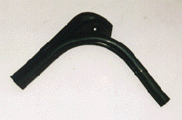
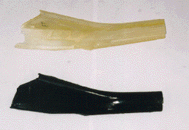
下:モデルから反転注形した発泡サンプル
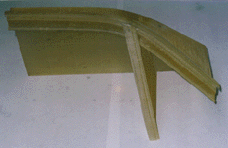