佐藤精密木型株式会社様は、4輪、2輪のインジェクション型などの木型メーカとして、短納期で高品質、高付加価値の製品造りを常に追求され、グラファイト及び銅電極制作をはじめ、家電製品のプラスチック部品用金型など幅広く製品開発をされています。
今回は、GRADE導入の背景、GRADE/CUBE-NCを用いた木型・金型造り、今後の課題などを中心に、工場長 鹿野様にお話をお伺いしました。
事業内容について
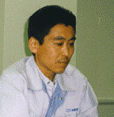
当社は、木型製造を営業品目として始まった会社で、1986年に初めてNC加工機を導入し、自動プロを利用してのNC加工をスタートさせました。
GRADEは、1989年より導入し、それ以来自動プロを止め、CAD/CAMによる木型製造に切り替え、現在では、グラファイト電極製作、各種治具製作、金型加工、NC放電加工なども行っています。
扱う製品の大半が4輪、2輪のインジェクション型に関係するもので、国内のさまざまな金型メーカからの仕事を請け負っています。主な営業品目として、バンパー、インパネ、フロントグリル、フェンダー、マッドガードなどがあげられます。他には、家電関係のプラスチック部品や椅子の背、座などの金型も依頼があれば何でもこなしています。社員の平均年齢が28.8歳ということもあって、若い力で新しい技術に常にチャレンジしています。
GRADE導入の背景について
国内では、高度成長に伴い大量生産のできるプラスチック製品が数多く作られるようになりました。プラスチックの成形品を作るには金型が必要となります。金型を作る上で簡単な2次元形状であれば木型マスターを必要としませんが、複雑な3次元形状になると倣い加工が必要となります。それらに必要なマスターモデルを我々木型メーカが図面から手作りで作ってきたわけです。
約20年ほど前から少しずつNC化が重要視されるようになり、当時はNC加工機もデータ作成する自動プログラミング装置もまだまだ模索の時代であったため、我々も手作りで木型をせっせと作っていました。
当時、我々の業界では一級技能士の手による作業が主流でした。
NCと比較しても、やはりまだ手には勝てないという感じだったのですが、当社の社長は意欲的にNC化に取り組んでいて、1985年に樹脂加工用NC機と自動プログラミング装置を導入しました。マイラーを計り、自動プロに数値を打ち込みながら作っていくもので、作業も大変でしたが、それ以上に自動プロのテクニックを上げていくことのほうが大変でした。
それから3年も経たないうちに、金型メーカからCADのデータが渡されるようになり、CADを持っていないと仕事が貰えなくなるというような噂が耳に入りました。その時には、正直言って我々はやっと自動プロに慣れ、自由に加工パスが作れると思った矢先だったのでショックでした。
CADの導入を検討し、どのメーカのものがよいかと迷っていたところ、丁度その頃お付き合いのあった2輪メーカのCADに詳しい方に何社ものCADを比較検討していただき、アドバイスを受けました。それらの結果、HZSのGRADEが当時一番でした。
このようないきさつで1989年初めにDS版のGRADE/CUBE-NCを導入することになりました。
導入当初は、CADそのものに抵抗がありましたし、使いこなすまでには時間がかかりました。
しかし、使い慣れてくると自動プロと比較して、性能が格段に良く、使いやすくなっていることもはっきりとわかりましたし、そうなってくるともう1台、さらにもう1台と必要になっていきました。それ以来、性能の良いマシンが出るたびにHZSに増設をお願いしています。
GRADE導入後も、他社のソフトもいろいろと検討して迷ったりもしたのですが、他社のCADと切削のスピードを比べてみてもGRADEのほうが速いようですし、バージョンアップ、サポート、品質を考慮した結果、GRADE1本で行こうと決心し、その考えをずっと貫いています。
設備構成について
1989年にGRADE/CUBE-NC導入以来、DS 2台、SUN 5台、Silicon(35TG) 1台、Silicon(Indigo II) 5台、Silicon(OCTANE) 2台、計15台になります。
時代と共にハードの能力もアップし続け、その都度確実で早くNCデータを作ることが可能な物を追い求めてきた結果、今の設備になってきたのだと思います。
取引先とのデータのやりとりに関しては、以前はオープンリール、CMT、DAT、FDなどのメディアによるデータの受け渡しで不便でしたが、現在はインターネットの他にルータを2台用意し、10社ほど通信によりデータの送受を行っています。お互いGRADEユーザということもあって、社外とのデータのやり取りもうまくいっています。
また、GRADEユーザ以外のところからのデータがきた場合にも、曲面のデータや構成点数などに多少問題がありますが、ほとんどのデータ変換は問題なく行えています。
先日、データ変換の精度チェックがありまして、メーカから面と点の離れ具合の精度チェックなどレポート用紙10枚分ほどのチェック項目を貰って確認したのですが、問題なく変換できていました。
設計変更などがあってもあまり苦にならず、本当に便利です。社内のNCデータの転送はNC機11台を光ケーブルでつなぎ、オンラインで行っています。
また今回の新工場におけるCAD室の広さは、将来CADの強化を図っていくために旧社屋の5倍相当の床面積を確保して、現在は余裕をもってやっていますが、いずれこの部屋にさらにGRADEが増えて狭く感じられるように頑張っていきたいと考えています。
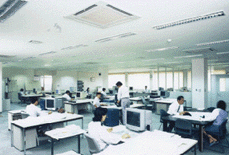
GRADE/CUBE-NCを用いた木型・電極・金型作りについて
GRADE/CUBE-NCを導入した当時は、今と比べてみると納期に余裕があったので、試行錯誤する時間がありました。インパネ、バンパーなどの大きなモデルになると、メーカから貰ったデータのIGES変換にかかる時間と、金型抜き方向へのローテーションなどにかかる時間は半日以上かかるのが当たり前でした。しかも、パスデータを作っても全てをチェックしないとパス落ちがあり、不安ですぐには、加工に入れませんでした。それが今では、HZSの努力とハードの進歩により、パス落ちもほとんどなくなり、短納期で高品質の製品を作り出すことが可能になり、今まで以上にお客様の信頼を得ることができました。
当社では、CADのオペレータは、CAD だけを扱うという業務形態ではなく、データを作った本人が、実際にそのデータを元に工具を取り付け、切削を行う工程を担当するようにしています。データを作った本人が一番良く分かっていますし、現場を経験することで加工のできるデータを作れるようになるからです。データ作成する側と現場で作業する側の考え方の違いによるトラブルを防ぐという意味でも分業化は行っていません。
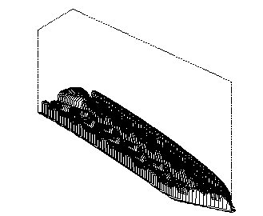
当社の社員の努力も実を結び、当初の営業品目の木型製作だけではなく、カーボンを使用したグラファイト電極、金型のNC加工、放電加工と品目を大幅に増やすとができました。当社の社長の「CADを利用して、あれもできないか、これもできないか」という前向きの姿勢に、これまで我々以下全員が一丸となって何にでも挑戦してきました。中でも、新しいマシンの導入に関しては苦労しました。新しいマシンを導入するたびにそれをうまく使いこなさなければいけませんし、それに伴って、データの効率のよい利用方法を考えてきました。特に、ひとつのデータを作ったらそれで終わりというものばかりでは効率が悪すぎるという点に目をつけ、そのデータを利用して、木型も作り、電極も作り、金型も削るというデータの利用方法を考えました。
マシンの導入に関しては、いろいろと苦労はありましたが、それにより、業務内容に幅ができました。
まず1つ目に木型加工用のマシンがあげられます。木型加工用マシンは3台ありますが、そのうち2台は、自動プロの時代からのもので、GRADE/CUBE-NCになってからは、稼動時間が大幅アップしました。もう1台のマシンは、大型で、5軸制御です。インパネ、バンパーなどのアンダーカット部も容易に加工することができます。
2つ目に、グラファイト専用加工機の導入です。これは、銅電極加工が主流だった頃に先立って導入しました。カーボンを加工する時に、粉塵が飛び散らないようにできる装置で、放電加工機の発達と共に金型を仕上げる工程で絶対必要な電極を作るというものです。付加価値を上げるため、CADデータで木型を作り、そのデータを利用し、グラファイト電極を作ります。グラファイトの放電性能が認められると受注も多くなりました。今では、面データの精度も良くなり木型を作らずに、いきなりグラファイトでマスターを作り、それらをデザイナーの方々に承認していただくというやり方もかなり増えてきました。そのためグラファイト専用加工機5台をフルに活用しているという状態です。
3つ目に、金型加工機です。バブルの後の不景気な時期に生き残りをかけ、金型を削るマシニングを導入しました。社長から機械を壊してもよいから金型を削ってみろと言われ、何も分らないまま、仕事を受けてしまいました。新品のカッターをいきなり折ってしまったり、金型材料の取り直しなど失敗に失敗を重ね、メーカにお叱りを受けながら、今では3台のマシニングを使いこなすところまで成長しました。
これからは、一部を除き、木型は必要とされなくなり、グラファイト電極に切り替わっていくと思います。CADの強化と、性能の良いマシンとのコンビネーションが要求されるでしょう。
問題点はまだあります。例えば、切削を行う際にはどうしても荒取り加工の工程は時間を多く必要としますし、刃物が折れてしまったり、無人で作業を行うというわけにはいかないなどの問題がありますが、それをクリアしていかに早く正確に仕上げることができるか、また刃物の選択、加工方法という点でも常に研究しています。
HZSのバージョンアップを期待しながら、ノウハウを蓄積し、どこよりも早く信頼のおける高精度の金型加工ができるように努力していきたいと思っています。
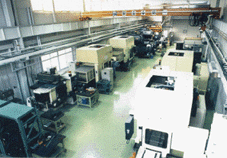
今後の課題、取り組みについて
我々は、4輪、2輪の金型に関係する事業を目的としている限り、メーカと共に今後の世の中の経済状況、ニーズによってすばやく反応できる態勢を整えておくことが大切ではないかと考えています。
また、自動車メーカも爆発的ヒットがない限り、多品種少量生産になっていくでしょうから、コスト、納期も益々厳しくなるのではと予想しています。こんな状況に対応していくには、性能の高いとNC機を設備してそれらを使いこなし、少しでも早く良質の型を削り上げることしかないと思っています。
試作の方面からみますと、今注目されているラピッド・プロトタイピング、ラピッド・ツーリングに大変興味がありまして、Techno Fusionでも見学させてもらいました。これから先、大型化、低コスト化が進めば、金型に対する考え方が大きく変えられるのではないかと思っています。将来は本型に使用されることになり得るかもしれません。当社においても、いずれこれらの装置を導入する時がくるかもしれません。
他には、IGES変換に変わるSTEPとか、サーフェイスに変わるソリッドとか、実際の世の中での動きに注目しつつ、取り入れるタイミングを検討している状態です。いずれにしても、CADの力を借りないと何もできない時代になりつつあるというのは確かです。HZSの方々に常に新しい情報を提供していただいて、我々は研究し、その時代に応じた的確な判断を下し、新しいものに積極的に取り組んでいこうと思っています。
HZSに期待するところ
当社のような小規模なところでも、HZSの方々が何にでも親切丁寧に応対していただけるので、本当にありがたく思っています。我々ユーザにおいてはどこも同じでしょうが、常に扱いやすく、スピーディなモデリングが可能で、安全かつ無駄のない加工データがより早く出せることを望んでいます。今後のバージョンアップに期待すると共に、バージョンアップの情報を早めに教えていただけるとありがたいと思います。
また、HZSの絶対パス落ちしない等高線加工という加工方法にも期待しています。そうなれば、経験の浅い人でもすぐに切削に入ることができるようになります。
これからは、CADの性能で、我々の業界で生き残っていけるかどうか左右されると言っても過言ではないと思います。常に我々は新しいものを取り入れ、研究し、使いこなす努力をしなければなりませんが、HZSも今まで以上に前進あるのみで開発を押し進めていってもらいたいと期待しています。その他、幅広くCADに関係する新しい情報を随時提供していただけるようなサービスもお願いしたいと思います。
当社に仕事をお手伝いさせてくださる会社がございましたら下記までご連絡下さい。
〒501-3217
岐阜県関市下有知5488-2
TEL(0575)24-1357
FAX(0575)24-2579
工場長 鹿野 敏夫
おわりに
新社屋を建てられたばかりということで、社内は本当に奇麗で、承認室などは、ゆったりとしたスペースを取られていました。また、お話を伺っていても新しいものに常に取り組んでいる前向きな姿勢、それを使いこなしている技術力、研究熱心なところには、感心させられました。
工場内もひとつひとつ説明しながら案内してしていただいて、大変勉強になりました。
たいへんお忙しいところ、貴重な時間をさいてお話を聞かせていただき、ありがとうございました。この場を借りてお礼申し上げます。
会社プロフィール
佐藤精密木型株式会社
本社 | 岐阜県関市下有知5488-2 |
---|---|
創業 | 昭和50年12月 |
資本金 | 1,000万円(平成9年8月末) |
従業員 | 25名(平成9年8月末) |
主な営業品目 | 各種木型製作、金型NC加工仕上、倣いモデル製作、各種検査治具設計製作、 グラファイト及び銅電極製作、NC放電加工仕上、NC加工データ製作、 GRADEによる金型CAV・CORモデリング |
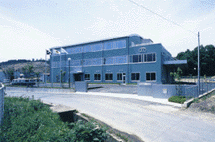
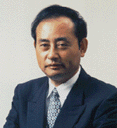
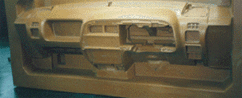
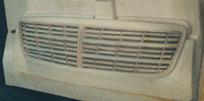
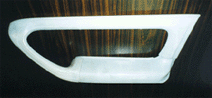
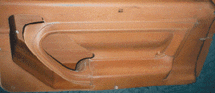