昭和精工株式会社様は、創業以来一貫して塑性加工に必要なフォーミングツールを開発、設計、販売されているメーカです。生産性向上を目的とした高いニーズが求められるなか、成形加工、成形機器はもとより、生産システムの構築など幅広い分野でご活躍されています。
今回は、GRADE/CUBE-NC導入の背景、自動プロからGRADEへの移行について、今後の課題などを中心に、代表取締役 木田 様、生産部 部長 横山様、システム課 主任 太田様にお話をお伺いしました。
事業内容について
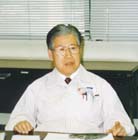
木田 様
当社は、1954年に塑性加工のツールを製造する会社としてスタートしました。創業から10年間は耐磨・耐衝撃工具の開発をしました。
20年目には、より高レベルな技術力を必要とする金型に着手し、30年目以降は金型加工法の見直しを行い、さらに、他社に負けない高度な開発をしなければいけないということで、金型加工法ツーリングを開発してきました。
現在はというと、研究開発創造の時代と位置付けまして、容器成形プレスライン開発、マイクロ複製技術開発、フィルムシート積層ライン開発などに着手しています。
当社の製品の割合ですが、食品容器としての缶(食缶)の金型が3割です。代表的なものはビールの缶などです。それから自動車の機能部品の金型が3割、電気、電子の機能部品の金型が3割、残りの1割は金型をベースにして周辺機器を揃えてもの作りするためのシステムで、自動機、専用機を作成しています。
その他に、2年半前に新しい取り組みとして、プリント基板の積層に用いるフィルムを作るために成形部を作りました。
GRADE導入の背景について
◆企業の責任と設備投資
常々、企業というのは永続発展するという責任があると考えています。
これからの企業の力というのは、知的財産、特許やノウハウをどれだけ持っているか、アイデアがどれだけあるか、そして当社でいうと電気業界、自動車業界、食品業界などあらゆる業界にユーザをどれだけ持っているかというブランドの力が基準になります。
そうすると、他社に真似できない技術・研究開発力を持ち、優秀な人材を確保、育成できる会社作りのほうが大事なわけです。未来に利益を確保でき、発展できる会社作りのために設備投資をするという信念があります。それで6年前には、20億円を投資して工場の隣に研究開発棟を建設しました。
もちろん現在の経済状況は、お客様からは短納期、コストダウンの要請がたくさんあります。しかし、このことは企業が生きていく上では当たり前のことで、絶えず技術を開発し、それを身に付ける努力をしています。
◆プロジェクトの発足と導入の決め手
このような状況の中、1997年4月に設計技術のレベルアップと加工技術の向上を目指してプロジェクトを発足させました。メンバーはCAD/CAM部門2名、製造部門2名、生産管理2名、チームリーダ1名、高速加工技術のコンサルタント1名でスタートしました。半年間いろいろと検討して、当社にとってHZSのGRADE/CUBE-NCが機能的にも、新しくこれからの企業の方向性を決めるのに大事なツールになると判断し、1997年10月にGRADE/CUBE-NCを3台導入しました。
GRADE導入前は、2.5次元の能力があるCADとCAMであれば、仕事に支障はありませんでしたが、常に現状よりも技術を向上させるものを企業内に取り込んでいかなければという危機感を持っています。
GRADEを導入すれば、皆が勉強するようになるだろうし、他社より遅れているのであれば、技術レベルを上げてそれを超えようと努力するでしょう。そうすることで、結果としてお客様が増えることにつながります。
当社は2.5次元形状の製品しか対応できないという体質でしたので、営業活動も非常に狭い範囲に限られていました。ですが、GRADE/CUBE-NCを検討している段階で、3次元形状がそんなに難しいものではなく、やればできるという自信がでてきたということも導入につながりました。
GRADE/CUBE-NCの機能での導入の決め手は、まずCAD/CAMの面からいうと3次元だけではなくて2次元と合流できるシステムであるということ、またモデリングにかなり定評があるということでした。一番のポイントになったのは複刃加工機能です。複刃加工の機能だけでしたら他にもありますが、3次元の機能も装備してあるということが決め手でした。
当初はGRADEだけを導入する予定でしたが、高速加工することになれば、従来のデータ供給方法ではとても工作機に追随できないため、CAD/CAMをDNCで工作機まで接続することにしました。
さらにGRADEの導入がきっかけになり、この機会にCAD/CAM、DNCの効果を側面的にも高めようということで、1998年9月にLANを構築して、生産情報をネットワーク化して生産管理まで行うことにしました。
現在は、うまく連携していましてこれからの効果を非常に期待しています。
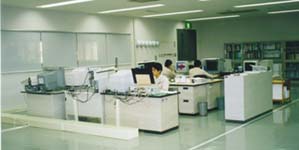
GRADEへの移行について
複刃加工の機能が重宝しています。
当社が、2次元から3次元へ移行していく段階で、複刃の機能があるほうがスムーズに移行できます。
2次元加工でも段差や加工する場所が増えてきたり、広い部分や狭い部分などいろいろ加工する部分があれば、自動プロではかなり大変ですが、GRADEでは複刃加工で経路を作成できます。また自動プロではできない傾斜で切り込んでいく加工などもGRADEで作成できます。
当社の場合、2次元の部分が多く一部分だけ3次元の曲面があるという形状なので、それをGRADEでうまく組み合わせられるのも便利です。経路においても編集して接続することができます。
自動プロも使っていますが、一部に3次元の曲面があるものはもとより、自動プロでもできる2次元もGRADEにどんどん移行しています。穴加工が当社の仕様通りのパスが作成できれば、全部GRADEに移行できます。
今の使用頻度はGRADEが6割で自動プロが4割です。リピート品として既存データがある場合は自動プロで、新規の場合はGRADEで作成しています。自動プロに慣れていますので、少しの修正であれば、言語を修正するほうが速い場合もあります。
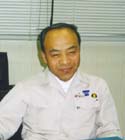
部長 横山 様
最近は、生産性を高めるために、たくさんの部品から構成される金型が一体化する方向になってきています。従来は2個だったものが一体化されて削り出しをする場合、部分的には複雑になるため、やはり自動プロよりもGRADEでモデリングする方が速く作成できます。
自動プロでは、2次元形状のRの彫り込みなどは成形刃物で切削できますが、成形刃物を作る時間と費用がかかります。GRADEでは、等高線加工で市販のボールエンドミルでデータを作成できるのでボールエンドミル1本で全部仕上げられるというメリットがあるために自動プロからGRADEに置き換えています。
曲面を削る場合はボールエンドミルでいいのですが、機能部品になると平坦な面がでてきますので、3次元のCAD/CAMだけでは難しいです。平坦な面は2次元の作業が入ってきます。
講習会に参加して1998年12月から実務に入りました。当初は3次元の形状を作成するのが初めてでしたので、2次元と感覚が違い、非常にギャップがありました。
最初の実務が2次元形状の中に3次元の部分が含まれるという一番難しい形状を作成することになり、3~4ヶ月かかりました。おかげで、そのときいろいろな経験ができ、かなり身につきました。
GRADE導入の効果について
◆高速加工の実現
GRADEを導入して、非常に複雑な金型の加工が容易になったということがあげられますが、もっとも大きい効果は、高速加工が実現できたということです。
検討プロジェクトのコンサルタントの方に、他社と比べて加工データの作成、切削スピードが遅いと指摘されました。ですから、高速加工を行うことで製品によっては放電レス、仕上げレスにもつながり、コストの低減が可能になるということでした。従来と比べると、複刃、高速加工も含めて効率が50%アップしています。
◆波及効果
それから、GRADEの直接効果だけではなく、波及効果がありました。高速加工をしている部署以外の部署もそれに刺激されて、高速加工の効果が浸透し、確立されつつあります。
これは、切削に限らず研削加工の部署においてもそうですし、現場全体が生産性を高めるための効率への意識が植え付けられました。また現場だけではなく、生産技術の部署でも実際肌で感じています。このように、GRADEを導入したことによって現場、生産技術、生産性に対する意識が向上したことが効果です。
◆成形刃物の減少
次に刃物に関してですが、成形刃物から市販の刃物に置き換えているので、成形刃物を作成する費用を削減できました。市販のボールエンドミルによる等高線加工で3次元的に削れるというのはGRADEの効果です。現在、市販の刃物で大物部品は効果がありましたが、小物部品はいろいろ問題がありまして完全にはGRADEに移行していません。
焼き入れした部品の切削ですが、成形刃物だと硬くて削れませんでした。市販のものでコーティング(Cコート)された刃物はボールエンドミルしかなく、成形刃物をコーティングするには大変な費用がかかります。GRADEで等高線加工の経路を作成することで、市販のボールエンドミルを使って焼き入れした部品の仕上げ切削が可能になりました。これにより、ある金型の部品に関して放電レスが実現できました。
◆図面作成の向上
焼き入れした部品をどうしても切削できない場合は、電極を作成します。2次元CADであれば、反転して電極の設計をしなければいけないのですが、GRADEでモデリングすると簡単に反転できますし、形状も頭に入りやすいので電極の設計自体が簡単にできます。それからパスを作成すると電極が削れてしまいますから便利です。図形を作成する場合もGRADEのCAD機能が使いやすいです。
◆加工時間の短縮
GRADEのCAM機能を使うことで、加工方法を意識するようになりました。自動プロですと2~3パターンしかありませんから加工方法が決まってきてしまいますが、3次元ですと等高線加工、走査線加工、倣い加工など、いろいろなパスを作成して効果的なものを探すということができます。また、加工時間が表示されるので、速い加工方法に変えたり、切り込み量を変えることで、加工時間を短縮することができます。
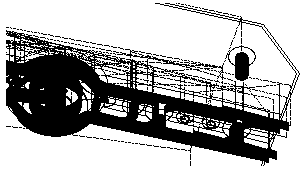
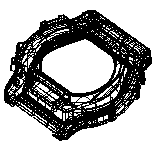
今後の課題について
小物部品での成形刃物レス加工に取り組みたいです。大物部品は効果がでているのですが、小物部品は逆に加工時間がかかってしまいます。
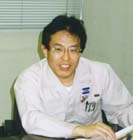
主任 太田 様
また、物によっては多数個取りで10~20個削る場合、市販のボールエンドミルでは、マシンのZ軸と形状の面精度に狂いが生じることがあるので、成形刃物で切削しています。成形刃物ではなくて市販のボールエンドミルでいかに面精度を上げるかが今後の課題です。
今後、曲面だけのものはなくなってくるのではないかと思います。自動車メーカ様でも曲面の中に機能部品が入ってくるのではないでしょうか。
ソリッドから3面図ができて、設計までできるというスタイルに大手メーカもなるでしょうから、設計から下りてきたデータでパスを作成するという本当の意味でのCAD/CAMになっていくでしょう。今後当社もソリッドには取り組んでいきたいと考えています。
HZSへの要望について
GRADEの機能的には、穴加工を充実させてほしいです。GRADEの穴あけ加工は自由度が少ないので、手間はかかってもいいですから自由度があることを希望します。
マニュアルについてですが、講習会を終えて習得したコマンド以外をマニュアルの中から探すのは非常に大変です。できればQ&A集として、雑誌またはホームページで公開してもらえると助かります。また、講習のテキストとは別に入門編、応用編などあればいいと思います。
おわりに
昭和精工株式会社 様にお伺いし、非常に奇麗で明るい社屋を拝見させていただきました。研修室などは設備を整えられて、お話にもありましたが、人材育成に力を入れられていることがよく分かりました。
常に開発、研究を続けていく姿勢や2次元加工にはない3次元加工のノウハウを経験と努力で模索しながら修得されようとしているお話は大変勉強になりました。
お忙しいところ、貴重な時間をさいてお話を聞かせていただき、ありがとうございました。この場を借りてお礼申し上げます。
会社プロフィール
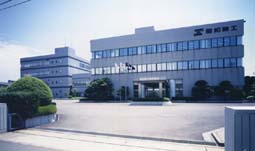
昭和精工株式会社
本社 | 横浜市金沢区福浦1-4-2 |
---|---|
創業 | 1954年 |
従業員 | 99名(含派遣社員19名) |
売上高 | 13億4千4百万円(平成10年9月末現在) |
資本金 | 資本金 :8,000万円 |
営業品目 | 食品容器の缶、自動車、情報、通信、電子、精密機器、医療、機能部品などの金型製品、フォーミングツール製品 |
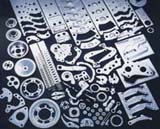
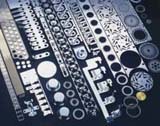
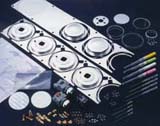
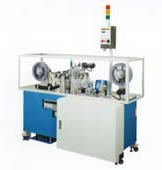