未来精工株式会社 金型事業部 金型課 山田 啓 様 石崎 敦也 様 山本 一 様 |
はじめに
ごく一般的な金型を作っている、20数名程の小さな金型製造部門が、今から1年半前、I-DEASを2台導入し、2次元CADから3次元CADに変わっていった過程と、現在、ようやくスムーズに流れるようになってきた、I-DEASによる「3次元金型設計」の事例を、実際に設計・製作したものをもとに、ご紹介させていただきます。決して新しいことをやっているわけではありませんが、「一金型屋」の3次元CADを使った現状の姿を見ていただき、少しでも多くの金型関係者の皆様の参考になればと思っております。
私ども未来精工株式会社は、岐阜県大垣市に位置しまして、電設資材メーカである未来工業株式会社より、平成6年4月、金型と自動機を作っていた技術部門が独立し、現在は社員数70名の規模です。
私どもの独立元であります未来工業株式会社は、昭和40年に設立した電設資材の製造メーカで、全国で9割ほどのシェアを持つスライドボックス(コンセント内部の樹脂製のボックス)や、電線を通す波付きチューブ、それらをつなぐコネクタ類、屋外の電気仮設ボックスや分電板、電気工事に使う様々なものに、アイデアを盛り込んで製品化し、プラスチック・プレス製品を中心に、全国で5ヶ所の工場で生産し、販売しております。(図1)
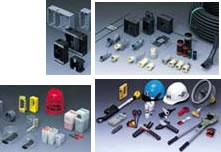
当社の業務内容は、私どもの金型製作部門のほか、自動機器部門では、各種自動機の設計・製作、特にプラスチックチューブの押出しラインと巻取り機(図2)関係を得意としております。
また、開発部門では、自社製品の開発、推進部門では、開発物件を製品化し、野菜や卵などの無人販売をするソーラーバッテリを電源とした「多目的省エネ型自動販売機」を製造・販売しております。また、インターネットプロバイダ業務部門の「ミライネット」と、異種5部門が集まった技術開発会社です。
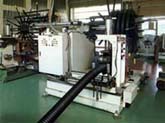
私どもの金型部門は、未来工業時代からこれらプラスチック金型を中心に、修理・メンテから始まり、設計から加工、トライ、生産ラインに立ち上がるまでの仕事を手がけてきました。別会社になってからは作る方の専門となり、プラスチックのインジェクション金型を主体に、押出し・ブロー・プレス金型から、モデル製作、治工具なども手がけております。現在金型部門は、営業3名、製造22名、計25名となっており、まだまだ9割が未来工業株式会社からの仕事ですが、家電・航空機モデル関係の仕事など、他のお客様からの受注も、徐々に増やしております。(図3)
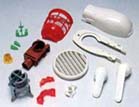
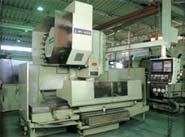
2次元CADでの設計業務
I-DEAS導入前の2次元CADで設計していた頃の受注から設計、NCプログラムまでの流れです。(図4)
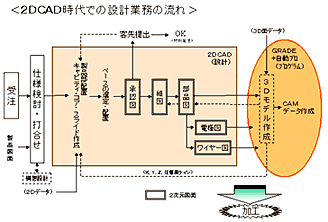
当初、設計3名、プログラム3名で、プログラム側は、自動プロが2台と、3次元CAD/CAMシステムGRADE/CUBE-NCが1台でした。
製品図面・2次元CADデータを元に製品部を設計してから、ベースに配置し、材料発注用の承認図を客先に提出します。その間、組図・部品図と仕上げ、完成した部品図を元に電極図・ワイヤー図まで作っていきます。3次元形状のものは、製品図面より2次元CADで設計し、それを元にCAM側で3次元モデルを起こし、客先承認後、プログラムを作るのですが、3次元データがある場合は、先にCAM側でX・Y・Z方向や任意の断面ラインを取り出してからしかPL面や割面を作れず、設計が進めないものもありました。そのような問題点から、「3次元CADでの型設計」の必要性が出てきました。
3次元CADによる型設計の必要性
◆3次元形状製品への型設計対応
受注の傾向として3次元形状の製品が増え、CAM側のGRADE 1台だけでは、追い付かなくなってきました。また、2次元図面では表現できないものも増え、「3次元形状製品への型設計の対応」に迫られてきました。
◆NCプログラマのモデリング作業負担の軽減
3次元形状製品が増えると、GRADEを使う一人にモデル作成とプログラムの仕事が集中し、NC加工や型納期が遅れることもしばしばでした。このような理由から「NCプログラマのモデリング作業負担の軽減」も、考えなければなりませんでした。
◆設計段階での形状認識と加工方法決定
2次元設計では、図面が完成し、CAM側に渡った後、「部分的に切削加工ができない」などの理由で、ワイヤー入子や電極が増えたりして変更が相次ぎ、その度、設計は作業を中断し、前の図面修正に時間を割きました。このようなことから「設計段階での形状認識と加工方法決定」の要望も出てきました。
◆設計ミスの削減
2次元設計では、部品図展開後、一部修正があるたびに関連図面全て修正しなければなりません。図面段階では、これらの修正・干渉確認忘れに気づかず、加工終了後に初めてミスに気づくこともありました。そのため、「設計ミスの削減」ができるCADシステムも検討していました。
このような問題点より、3次元CAD/CAMでの型設計とプログラムの必要性から、3次元CAD「I-DEAS」を導入、3次元CAM「GRADE」を増設し、設計側はI-DEAS 2台、既存の2次元CAD 2台、計4名で、プログラム側は、GRADE 3台で3名の体制で、平成9年4月にスタートしました。3次元CADでは、設計の流れも随分変わりました。(図5)
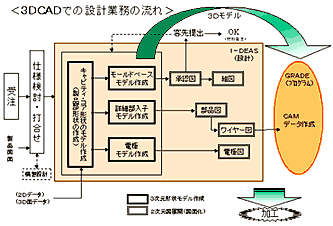
2次元設計のような直列の流れではなく、製品図面・2次元データ・3次元面データを元に、金型用製品部モデルを作成し、これを元にモールドベース・各入子・電極モデルの作成を、並列に行っていきます。電極に関しては、キャビティ・コア形状を作る時に使う「金型用製品部モデル」をそのまま電極モデルへと流用していきます。各モデルができると図面に展開し、承認図を提出、組図・部品図・電極図と展開していきます。このような設計の流れに変わり、さまざまな効果が出てきました。
I-DEAS導入の効果
◆3次元の形状認識による加工者の理解度UP
2次元図面では、加工者が図面を見て形状を理解するまでに時間が掛かったり、間違って認識することが多々ありましたが、I-DEAS導入後、NCプログラマには3次元モデルデータで、加工者には図面上に斜視図をのせるなどで、理解度が向上しました。
◆「作れる金型」(加工方法)の幅の拡がり
I-DEASでは、設計者が頭の中で描いていた形状をそのまま目視できるので、変則PLや変則割りも容易に設計でき、今までにない型構造や入子割り方法にも着想できるようになりました。また、設計段階でも各加工者に画面を見てもらい、確認・相談することが容易にでき、今まで設計者では解らなかった「加工方法」の幅が拡がり、「作れる金型」が増えてきました。
◆電極設計の短縮化
金型用製品部モデル形状が電極モデルとして流用でき、2次元設計では部品図が完成してから考えていた電極図面が容易に作成できるようになり、「電極設計の短縮化」につながりました。また、干渉チェックができるようになったため、以前では単品で幾つかに別れていた電極も、1つの複合電極にすることができ、電極加工と放電セットの効率が上がりました。
◆NCプログラムとNC加工の迅速化
NCプログラム時間が短くなり、以前なかなか進まなかったNC加工がスムーズに流れ、「NCプログラムと加工の迅速化」の効果が出てきました。
図6は、2次元CADから3次元CAD「I-DEAS」に変わった現在までに設計した金型-60型(30t~400tクラスまでの様々なもの)について、全作業時間を4つの期間に分けて「1型あたりの平均作業時間」をグラフ化したものです。(図6)
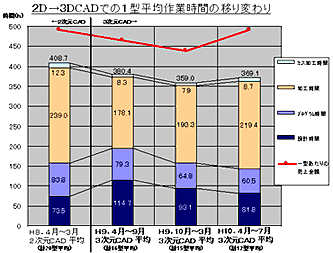
一番左の棒グラフが2次元CAD時代に1年間に設計した金型の平均時間で、太線より右はI-DEASを導入してから半年ごと、現在までの平均時間です。上の折れ線グラフは、1型平均の売上げ金額です。
導入当初は、製品部となるキャビティ・コアのモデル作成にかなりの時間を取られ、「モデル作成手法の確立」に悪戦苦闘し、トライ&エラーの繰り返しで、最初の半年は、設計については、2次元CADの約1.5倍の時間が掛かりました。
しかし、この「モデル作成手法の確立」と、バージョンアップにおける機能強化により、設計時間も少しづつ速くなってきました。プログラム時間は確実に減り、3人から現在約2.5人でまわるようになりました。
最近のデータでは、設計・プログラム時間は減っていますが、加工者の作業時間が逆に増えています。
その理由として、1型平均の売り上げ金額も上がってきたことなどから、複雑な型や特殊構造の型など、付加価値の高いものにも社内で取り組めるようになってきたからだと思われます。
言うまでもありませんが、全体の作業時間も2次元CAD時代と比べ、減ってきています。
Fコロエンドによる事例
2次元CADの作業から、3次元設計における手法の転換を事前に検討する間もなく、基本操作の講習終了後、実務の中で模索することとなりました。操作になれる間の加工型数を確保する人員の補充もなされなかったため、当初の目的である2次元CAD使用時と同等の型数の確保には、連日深夜までの作業となりました。それでも一時は型数が確保できずに、3次元設計中止という危機的状況にもなりました。
当初は製品モデルを作成し、そのモデルに抜き勾配、収縮率を付加すれば、設計から加工まで、スムーズに作業が進むと考えていましたが、この手法は確立できませんでした。面や形状の一致による演算エラー多発、設計変更に対応するための各パーツ間の関連性維持が困難であったためです。
そこで金型用のモデルを作成する手法をとり、設計変更の場合は基本形状を修正し、履歴操作で入子形状を置き換えることで、柔軟な対応がとれます。
未来工業株式会社のFコロエンド(建造物の壁より天井などに配線を引き込む際に使用される製品:図7)の事例を紹介します。
製品モデルではなく、金型用のモデル(図8)を作成します。すなわち、収縮率、抜き勾配を加味し、入子割りを意識した部分モデリングを行います。
この方法の利点は、作成したパーツの結合部の形状作成が容易で、パーツを電極モデルなどに利用可能なことです。さらにモデルをカット、結合すると、履歴が各パーツごとに分れる「ブッシュ型」になり、形状修正が容易になります。各パーツを結合したこのモデルが、キャビティ入子をカットする金型用モデルになり、結合部のフィレットを追加して、形状の確認をします。このモデルをVRMLファイルに変換し、Webブラウザでお客様にも形状を確認していただいています。このモデルを元に入子分割、スライド勘合部を考慮し、キャビティ入子を作成します。同様にコア側も作成し、コアピン形状はそのままパーツとして利用します。
入子製品部形状の作成が終了すると、入子設計と同時にモールドベースの設計を行います。(図9)
ライブラリに登録してある標準モールドベースを取り出し、パラメトリック機能を利用して、各プレート寸法を製品にあわせて変更します。当初は基準寸法を変更すると、全ての寸法が変更されるようなアセンブリ拘束を考えていましたが、すべてにアセンブリ拘束をつけるとレスポンスが落ちることや、あらゆる設計変更に耐えられる拘束を定義することが困難だったため、断念しました。
入子をベースに配置し、ポケット穴、標準部品用穴などをライブラリから取り出し、カットします。このライブラリパーツも作業中に作成したものを順次登録していきました。
可動側パーツをアセンブリに構成し、2次元CADでは確認しにくかった部品間の干渉、距離等を目視、測定で確認します。これにより部品間の干渉ミスが激減しました。
同様にして固定側パーツもアセンブリで構成を確認します。固定側と可動側のアセンブリ全体を合せ、干渉チェックを行います。(図10)
こうしたモデルデータから製品モデル(図11)を作成し再度形状確認を行います。
ドラフティングセットアップを介して、アセンブリを図面化し、組図を作成します。ドラフティングで、寸法記入を行う前の組図を承認図として提出し、承認待ちの間に組図に寸法、注釈を記入し、図面化を先行します。(図12)
次に部品図の作成を行います。(図13)
設計変更があった場合、2次元CADでは、変更に関わるすべての図面を修正していましたが、これらの図面は、アセンブリ、パーツモデルを参照していますので、修正もれ、記入ミスがなくなりました。また作成の難しかった斜視図が簡単に表示できるようになり、加工者の理解度向上に貢献しています。
3次元CADの特徴として、寸法線が自動で出力されますが、それらはあくまでも、モデリング用の寸法であって、設計者の意図する図面寸法が、出力されるわけではありません。図面寸法の出力を意識してモデリングしますと、相当な労力と時間が費やされますので、モデリング時に入力する寸法は、あくまでモデル作成用と考え、二度手間になりますが、図面寸法はドラフティングで記入するほうが時間的に速いと思われます。
現在のところ図面化に比重をおき、「図面化が速い」という前提で、機能を選択しております。
演算やサーフェースモデリングの機能は強化され、モデリングに幅ができた反面、関連性をもたせたモデリング、アセンブリ機能など、有効と感じながら活用できていない機能もまだまだあります。また加工現場では、図面がメインになっているため、図面化が必須で図面化に要する時間は設計時間の約半分を占めており、今後時間短縮を進める上で、それらの機能の活用、図面の作成方法は重要な課題になります。
承認が得られましたら、形状データをCAM側へ出力します。(図14)
導入の選定理由にもありました、CAM側での作業軽減の他に、生データでのデータ交換可能という、条件がありましたが、現在対応が遅れており、IGESデータに変換しての出力になっております。
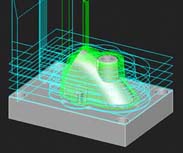
次に電極の設計を行います。電極の形状も設計者が検討しており、金型用モデルを利用して作成します。部分モデリングした形状に手を加え、キャビティ用の電極形状を作成し、同時に加工できる箇所をなるべく一体で製作します。多数の電極を使用しますので、電極同志の干渉、加工残りが容易に確認でき、複雑な形状を一体で製作することにより、作業時間を短縮し、自動加工化することができます。
各電極の加工位置を確認し、干渉をチェックします。(図15)
コア側も同様に設計します。形状を目視で確認できますので、加工R残りの認識も容易です。組図、部品図と同様に、電極図を作成します。(図16)
加工ポイント、深さが一目でわかり、プログラム作成の時間短縮になっています。(図17)
電極加工もNC工作機械が主流になっており、作業者の手仕上げを極力減らしています。
完成した金型はトライも1回で合格し、入子材の焼入、後処理を経て、完了となりました。(図18)
今後の課題
◆オペレーションの向上
- 3次元モデル作成のレベルUP
- 3次元モデルから2次元図面完成までの時間短縮
- 2次元設計機能(Drafting)での時間短縮
3次元側のDraftingSetupから2次元加工用図面にするにはかなり時間がかかるというのが現状です。図面レスが理想ですが、汎用加工も多々ありますから図面化しないわけにはいきません。ルール付けを行い、図面作成の最速化へ工夫をしていく必要があります。どんなに簡単な形状に対しても3次元から2次元へという手順をを取っています。今後、場合によっては、Draftingのみで進めていきたいと思っています。
◆I-DEASへの統一化
この先、現在使用中の2次元CADをI-DEASにリプレースし、チーム設計環境を確立していきたいと思っています。そうすることによって、金型部品などの標準データを共有したり、参照したりして、更なる金型設計効率を上げられると考えております。
今後、我々も3次元による金型設計を高めるために一層努力をしていきたいと思っています。