沖電気工業株式会社 エンジニアリングセンタ 実装技術開発部 生産技術開発チーム 係長 深井 雅克 様 堀川 俊昭 様 西山 和也 様 |
EOSINT-M導入経緯
情報機器の小型・高機能化、低コスト化要求に伴い増加する成形部品の製造期間短縮と、増大する金型費用の削減を図るために、EOSINT-Mを導入し運用を開始したので紹介する。
導入に当たり、量産型に適用するための技術評価を行い、十分に実用可能であることを確認した。平成10年9月に導入後、すぐに運用に入り、運用と並行して技術確立を行った。
EOSINT-Mによる造形法は、レーザ焼結法とよばれ、三次元形状をスライスしたデータを基に、ブロンズ-ニッケルの合金粉末を炭酸ガスレーザで焼結し、積層造形することで直接金型を製作することができる。金属粒子を融着するために、従来から試行されている樹脂型に比べ十分な強度をもつ。
三次元データによる一貫製造体制について
高崎地区での三次元設計の適用率を、新規成形部品 の割合でみると、1997年度46%に対し、1998年度は80%に拡大している。三次元設計の適用により、三次元モデルでの干渉チェックや、強度解析等が容易になったこと、また二次元設計で発生する単純ミスを防止できることから設計品質の向上に大きな効果を上げている。
三次元による効果を更に拡大するためには、下流工程での三次元データの活用が必要であり、そのための三次元データの一貫利用体制の構築と、コンカレント設計製造を推進している。(図1)
設計段階で、光造形を適用し、形状確認や機能確認を行ったり、成形品の抜き方向や肉盗みなどの成形性についてのチェックをコンカレントに行うことで、後戻りによるロスを最小限にしている。樹脂の流れ、ウェルド位置やゲ-ト位置の確認には流動解析を利用している。
三次元での金型設計はEOSINT-Mの導入と同時に本格的に開始した。三次元の金型データを利用して、造形で金型を製作し、更に三次元でのマシニングによる追加工を行うなど、現状では、金型製造工程までの三次元データ利用体制を確立できた。最終的には、三次元のデータを使った自動測定から測 定結果の検証を可能とすることで、評価認定の工数削減を図っていきたい。
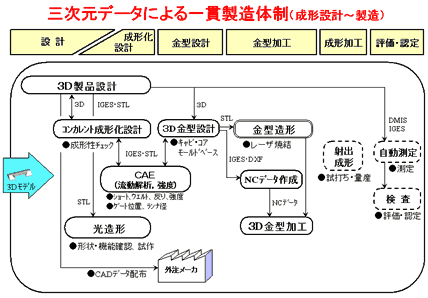
EOSINT-Mによる金型製造プロセス
EOSINT-Mによる金型製造プロセスを図2に示す。まず三次元で設計した製品形状にパーティング面を設定しキャビ・コア分割を行う。モールドベースにキャビ・コア及びイジェクタピンなどの各部品配置、ゲート設定などを行い金型設計モデルを作成する。
作成したキャビ・コアデータをSTLデータに変換し、造形用データ作成ソフトウエアにインターフェースする。そのモデルに対し、造形のためのモデル編集を行い、積層厚0.05mmに分割したスライスデータを作成する。
スライスデータにレーザの照射条件を割り付け、造形用プラットフォームと造形位置のセッティングを行い、造形を開始する。造形物はポーラス状になっているため、内部空孔を埋めるためのエポキシ樹脂による含浸操作を行い、強度アップと表面粗度の向上を図る。
含浸するエポキシ樹脂の量が、後加工や金型品質に影響を及ぼすため適量になるよう管理している。造形、含浸後のキャビ・コアを直接モールドベースに組み込むには寸法精度が不十分であるので、入れ子の側面やパーティング面の追加工、穴さらいを行う。離型性を良くするのと成形品表面の品質確保のために、仕上げ加工または磨きを行う。
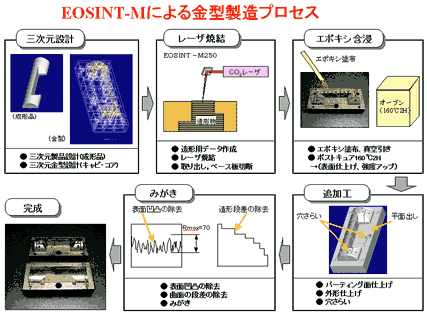
造形データ作成手順
造形データの作成手順を図3に示す。キャビ・コア設計完了後、STLデータをRAPID TOOLSに送り、モデルの移動、切断やSTLデータの不具合修正等を行い、造形のためのモデルを作成する。
作成した造形モデルに対してスライスデータを作成し、RPT TOOLSでスキン/コアデータを作成する。EOSINT-Mは、金型の表面(スキン層)と内部(コア層) で造形条件を変えている。スライスデータをEOSINT-Mのプロセス・ソフトウェアに送信し、照射パターンやレーザ速度などの造形条件の割り付けを行う。
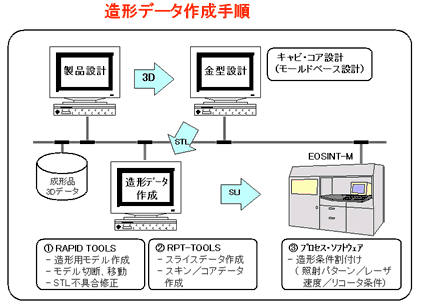
EOSINT-M評価事例
導入に当たり寸法精度、耐久性、耐食性、加工性や 表面粗度・改質性についての評価を行った。
■寸法精度の評価
造形後のキャビ・コアの出来寸法は0.2~0.3%程度 収縮ぎみになった。寸法公差の厳しい箇所は仕上げのための追加工が必要となる。
■試打ち成形品の寸法
EOSINT-Mでの造形金型の寸法とトライ寸法を比較し、寸法精度を評価した。収縮率、反り共に従来型と比べて小く、安定している。
■成形性&耐久性の評価
成形条件は、従来型とほぼ同等の設定が可能である。表面の仕上げ状態によっては離型性に問題が発生する。ABS樹脂で6000ショットまで成形して、問題ないことを確認した。
■耐食性評価
耐食性について、酸化率と表面粗さをNAK材と比較し評価した。200時間経過後の酸化率、表面粗さ共にNAK材よりも優れることが判った。表面の腐食状態もNAK材で発生した孔食や応力腐食割れなどの局部腐食はみられなかった。(図4)
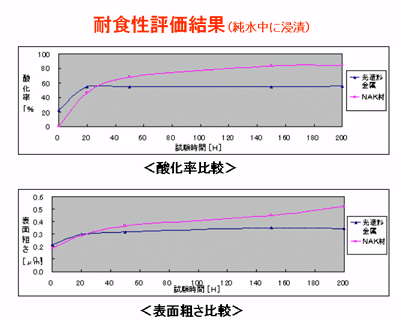
■加工性評価
切削加工性は良好で、加工後は光沢がでるが空孔部は残る。放電加工面はNAK材に比べ悪く、ワイヤカットに関してはワイヤ切れが多発する。溶接や肉盛りは難しいため、改修性は劣る。仕上げは、材料が柔らかいためみがき易いが、いくらみがいても空孔部は残る。
■表面粗度評価
造形物に対し、表面改質処理を行ったが、それぞれ表面粗さに関しての効果はあまりみられなかった。(図5) 現状は、特別な処理は行わず、造形後、エポキシによる含浸のみで仕上げを行っている。
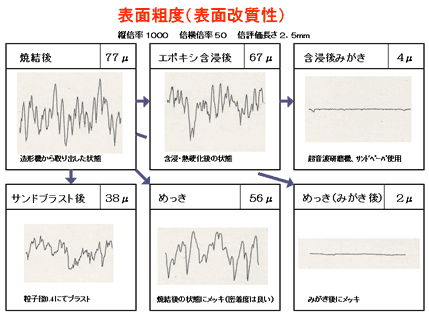
EOSINT-M運用に向けて
導入後は、安定して運用するための技術確立を行った。金型設計に関しては、離型性が悪いため、抜き勾配を通常よりも大きめに設定したり、イジェクタピンの数や配置を慎重に行うようにしている。
また、強度的にも従来型に比べ弱いので、強度を考慮したパーティング設定や押し切り形状にすることと、鋭いエッジ形状や細い形状は避けるようにしている。造形時、ベースプレートと造形物が剥離する場合があるので、境界部に剥離防止のためのサポートを付加するようにした。
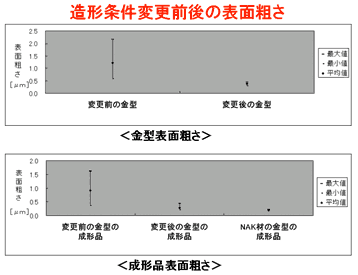
これにより、造形端部の剥離荷重を緩和することができ、剥離はほとんど無くなった。表面粗度を改善するために、造形条件の見直しを行った。今回はレーザの照射速度と表面粗さ、表面空孔部面積の関係についての評価を行った。最終的にレーザの照射速度を変えることで表面粗さ、表面空孔部面積を図6と図7のように改善することができた。
表面粗さはRa1.2から0.4に、また空孔部面積率については、変更前約50%に対し変更後は約25%まで小さくできた。
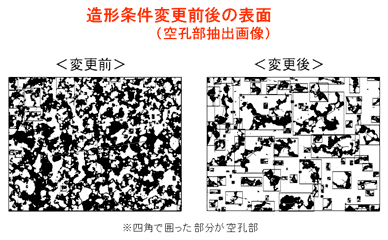
適用事例
EOSINT-Mで製作した金型と成形品の例を示す。(図8,図9)

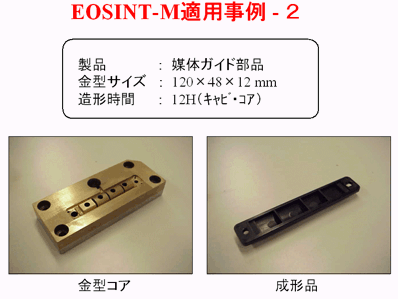
適用効果
キャビ・コアの製造工程の比較を図10に示す。従来工程では金型の設計を行ない、図面完了後に製造に入るが、造形を適用する場合は、キャビ・コアのデータができると造形に進むことができるため、その分、製造開始時期も従来に比べて前倒しが可能となった。
また、造形によりほとんどの形状ができてしまうため、金型図面の簡略化も可能となった。形状による差異はあるものの、本工法では、従来工法に比べ、放電加工のための電極製作や放電加工の工程を省略できるため、大幅な工期短縮とコスト削減が可能である。
キャビ・コアの製作時間を従来工法と比較すると、従来型で放電加工がある場合134Hに対し、EOSINT-Mではデータ作成、造形、追加工で60Hと約半分以下の時間に短縮できた例もある。平均的には30~40%の短縮が可能と考える。
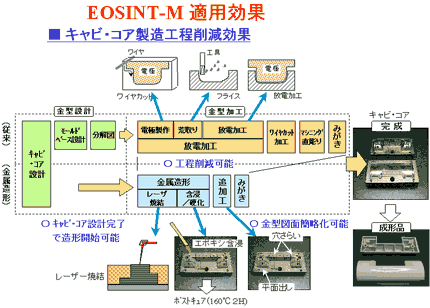
課題
現状の表面粗度では適用部品が限定されるので、表面粗度を改善するための造形条件の改良や、仕上げ処理が必要となる。EOS社ではショットピーニングによる処理を検討しているようなので結果を期待したい。
造形データ作成に関しては、データ作成手順の中で説明したように、色々なソフトを使わなくてはならないため、追加工代の付加や、製品面や指定した部分だけに特定の造形条件割り付けが簡単にできる統合的なソフトの開発を望む。
今後の展開
EOSINT-M適用の効果を更に上げるためには、造形時間の短縮や適用範囲の拡大が必要となる。今後は、造形時間を短縮するための金型モデリングや中サイズの金型へ適用するための検討と技術開発を行っていくと共に、造形条件に関しても当社独自の条件として更に最適化を図っていきたい。
また、鉄系材料のリリースが9月ということでアナウンスされているが、その技術調査と適用効果性につ いての調査も実施予定である。
会社プロフィール
沖電気工業株式会社
創業 | 明治14年(1881年) |
---|---|
資本金 | 678億円 (1998年9月現在) |
従業員 | 10,185名 (1998年9月現在) |
従業員数 | 10,185名 (1998年9月現在) |
売上高 | 540,641百万円(H8年度決算) |
高崎地区製品 | コンピュータ&マルチメディアシステム、金融システム、旅客交通システム |