取締役 製造部長 新名 俊一 様 管理課 係長 弓部 伸一 様 技術課 係長代行 千沢 幸二 様 |
はじめに
金型メーカーを取り巻く環境
バブル崩壊後、各自動車メーカー間では生き残りをかけた競争が激化の一途をたどっている。そのような状況下、自動車メーカーは、市場ニーズに合った新型車を短期間で開発して市場に投入することが、ライバルに打ち勝つための大きな戦略となってきている。
当社の得意先であるトヨタ自動車さんでも、'96年初に、新車の開発期間を25ヶ月程から15ヶ月に短縮することを発表された。現在では、さらに短く目標12ヶ月という状況である。
当然のことながら、当社も規模は零細で末端の企業であっても、自動車の開発期間(生産準備)に関わっている以上、受注した金型の製作工期も必然的に短縮へのニーズが強くなる。少し大げさに表現すれば、短工期を実現することが、金型メーカーとして生き残るための必須条件でもあることは間違いない。
金型製作工期短縮への取組み
当社も、'96年6月より対前年比40%短縮の目標を揚げ、全社を挙げて活動を推進してきた。当時、目標40%短縮というのはとてつもなく高い目標であったが、結果、総改善件数132件にも上る取組みによって、約1年で目標を達成することができた。
まず第一ステップとして、源流(仕様打合せ)から下流(納入)までの徹底的な工程改善を行った。
従来の生産システムは、仕様の決まった金型をどんどん仕掛かり、現場では監督者が機械をやりくりし、日々工夫しながら製作していく方法をとっていた。これでは、工程間の停滞、加工の無駄が多く、かなり工数(工期)もかかっていた。
そこで、お得意先との仕様打合せから金型の納入まで、帳票、図面、工法、工程順などについて、すべてを徹底的に見直した。
基本的な取組み方としては、まず今までのやり方をすべて否定し、目標工数(日数)の中でやり終えるため、最小限必要なものは何か、もう一度ゼロから構築していく方法をとった。改善といった程度のものではなく、むしろ当社にとっては改革といっても過言ではないと思う。
第二ステップとしては、生産をシステム化し、「守れる」日程管理の仕組み作りに取組んだ。
金型は、いわば一品料理であり、小さな型(250TONクラス)から大きな型(1650TONクラス)、また、比較的単純な構造の型から複雑な型までが、こちらの都合に関係なく、得意先との約束納期に向けて多くの金型が流れる。
どこの金型メーカーでも同じであろうと思われるが、日程計画の作成には、業務に精通したベテラン社員が不可欠なのである。それでも、各種のトラブルが頻発し、遅れが日常化するといった事態に陥りやすい。
そこで当社では、金型を類似品・難易度別にグループ分けし、そのグループごとに基本となる目標日程表を作成した。新しい仕事を受注すると、当てはまるグループの標準日程表に基づいて、日程計画を作成するのである。その日程計画を作成する上での重要なポイントは、下記の2点である。
1) 停滞なく作る。
2) 必要なものを必要なときに作る。
当社の推進している「集中同期化生産システム」の基本的な考え方である。
そして、一連の活動を推進していく上でのキーワードは、「標準化」、「システム化」、「シンプル化」、「スピード」であった。このような改善の中で、CAD/CAMについても、従来の工程は、CADからCAM、つまり設計をしてから、モデリング、加工プログラム、加工するという流れであった。が、発想を逆転して、CAMからCAD、つまり、始めにCAMのモデリングをし、そのモデルデータを利用して加工データの作成、設計を行う。
このような工程の見直しによって、大幅な工期短縮を実現し、成果を上げましたので、CAD/CAMの工程短縮の事例について稚拙ながら紹介いたします。
その概要は、GRADE/CUBE-NCを3次元的設計に活用して、工数(工期)の短縮を実現したものである。
三次元CADに対する考え方
巷間では、金型メーカーの中でも、3次元CADでの型作りがトレンドの如く言われている。事実、自動車メーカーや部品メーカーは、積極的に3次元CADに取り組みつつある。
しかし、私どもが考えるところでは、例えば自動車の全部品まで3次元CADで作られ、当社のような小さな金型メーカーまで3次元CADのデータが供給されるには、まだ多少の時間がかかると推察される。
そのため、当社では、現有の設備の中で3次元CAD的な活用ができないだろうかという視点で取り組んできた。
金型を製作する上で、CAD作業は必要だと認識しているが、できれば最小限に止めたい。そして、極論になるが、図面は無い方が良いと考えている。モデリングをして加工データを作ることで金型を製作することができれば最良だと考えている。
すなわち、CAMが主体で、CADでの無駄な設計作業を限りなくゼロに近づける金型製作を理想と考えており、「図面を必要としない型づくり」を目指している。
そこで、今までの発想を逆転させて、現有の3次元CAM「GRADE/CUBE-NC」を使って、3次元モデリングをするとともに、同一画面上で2次元設計までも行えば効率が良いと考えた。しかも、それを一人の作業者が行えば、さらに効率が良くなるはずである。
つまり、現有のGRADE/CUBE-NCを活用した、いうなれば当社流の3次元疑似CADへの取組みに至る原点ともいえる考え方である。
従来の工程
従来の設計プログラム作業の流れ
お得意先からいただくのは、製品形状の図面である。現状は、コピー図支給とCADデータ支給が半々程度である。そして、大半のお得意先が構想図も設計して欲しいという要望がある。
従来は、お得意先と仕様打合わせをし、2次元CADで設計をして図面を作成する。
その後、モデリングをし、NC加工データを作って、加工に入るというように、作業が時系列的に直線に並んでいた。
別々の人間が、設計作業とモデリング作業を行うので、この作業間の情報を伝達するために、たくさんの帳票類を作成したり、図面にもすべて寸法を記入する必要があった。
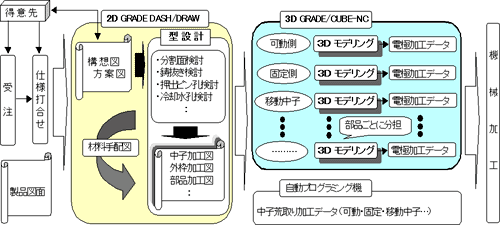
CAD上で設計作業をしていても、すべての寸法表記を必要とし、その図面を見て作業を行う後工程が読取りミスをすることも少なからずあった。
また、途中で設計変更があったりすると、せっかくCADでデータを作成しているのに、別のところでは手で修正を加えるといった、データ入力の二度手間もかなり発生していた。
また、金型によっては複雑な分割などがあるため、支給された図面をベースに2次元で設計をしていたときは大変難しく、かなりの熟練者であっても、途中でトラブルが発生することもあった。
改善の方法
目標 工期短縮40%のために
新型車の開発期間が25ヶ月程から15ヶ月に短縮されるのに合わせて、工期短縮40%を目標とした。
当然、設計・プログラム工期もその目標期間で終えるために、工程を全面的に再構築することにした。
作業にかかる日数そのものを短くしていくためには、同一システム上ですべての作業を行い、一度作成したデータをそれぞれの作業で有効利用(データの一元化)し、それらの作業をパラレルに進めることである。
いわば、金型メーカー社内でのミニチュアコンカレント化への取組みである。
改善後の工程
新しい設計、プログラム作業の流れ
かなり多くの工数がかかる3次元モデリングを先行し、そのモデルデータを使って同一システム上でCAD作業をすることにした。
2次元設計から作業をスタートした場合、金型が単純なタイヤキ式の分割であれば大きな問題はないが、非常に複雑な分割面を持つ金型になると、かなり熟練していないと、図面から立体をイメージし、正確な分割面を決めることは難しい。
現在は、最初に3次元でモデリングをすることによって形状がわかるので、複雑な分割面でも容易に決められるようになり、型構想の設計も早く楽にできるようになってきた。
大型の金型の場合、モデルデータをもとに設計作業を進めている間に、別の担当者が、電極やキャビティ中子のNC加工データ作成をパラレルに進めることになる。3次元モデリングと型設計は、必ず1人で担当することになっており、他の作業はそのボリューム、負荷状況によって分散処理をする。
当然ながら、簡単な型であれば、モデリングからNC加工データ作成まで1人で行う場合もある。
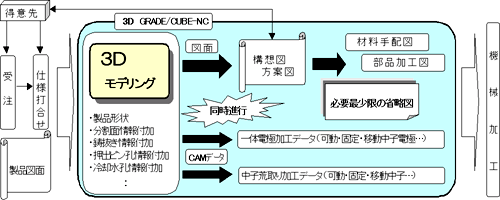
モデリングと設計作業を同一システムで1人で行う大きなメリットは、情報伝達のための無駄がなくなることである。別の担当者や後工程に情報を伝えるための帳票類も最小限に止めることができ、図面も寸法表記を省略したコンパクトな図面だけでよくなる。
従来、A0, A1サイズで出していた図面も、今では最大A2サイズまで縮小化している(大半はA3サイズである)。
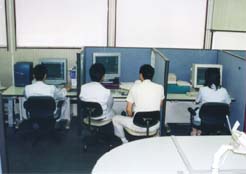
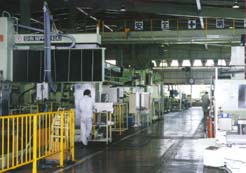
具体例
800TONクラスのトルクコンバータを例に、新しい設計プログラムの流れを紹介いたします。
◆お得意先からの製品形状のCADデータをもとに、
GRADE/CUBE-NCでモデリングをしたトルクコンバータの製品モデル
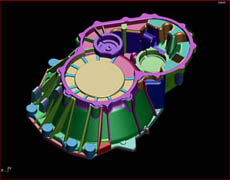
◆製品モデルデータをもとに構想図、方案図を作成。
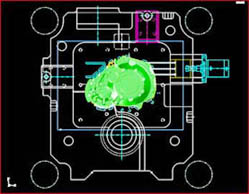
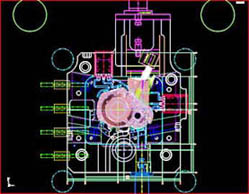
作成した構想図、方案図でお得意先に承認を得る。
◆金型の断面図
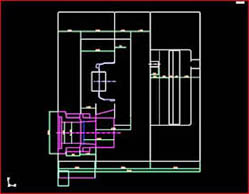
◆固定型 中子の加工図
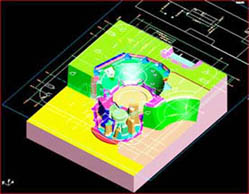
◆加工部品の詳細設計図
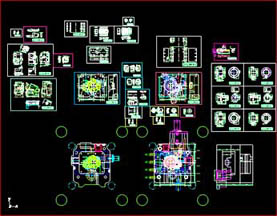
◆電極モデルでのパス計算
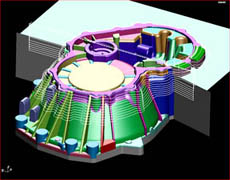
◆固定型 おも型(外枠)
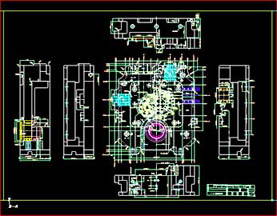
◆金型
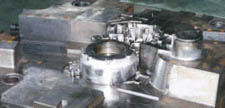
◆製品
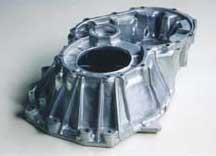
活動の成果
この活動を始めたときは、GRADE 3台を使っての試行錯誤であったが、全員が英知を出し合い、果敢に挑戦した結果、高い目標を達成した。
その後、GRADEを順次4台導入し、現在ではすべての受注金型の生産システムに展開している。
金型の形状が複雑で難しいものほど効果が大きく、従来、当社で90日~100日ほど掛かっていた金型を、現在では45日~50日間で製作できるようになった。
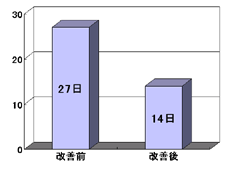
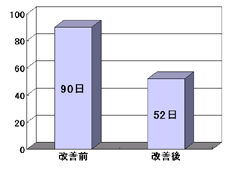
この3年間で、金型の平均工期を42%短縮し、生産性を45%上げることができた。売り上げは、約5割増え、4億2000万円から6億4000万円を達成した。いずれも、当社にとって設立以来のことである。
また、この金型不況の中でもフル稼動の状態であり、お得意先様には感謝の気持ちで一杯である。
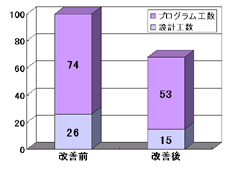
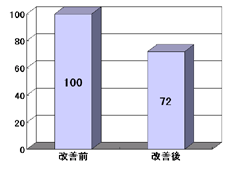
今後の課題と取り組み
今は、GRADEを使ったサーフェイスモデリングでやっており、ソリッドモデリングについてはほとんど手付かずの状況である。
将来のCAE等への展開を考慮してもソリッド化は時代の流れであり、今後、主流になっていくことは疑いのないところである。
しかし、サーフェイスモデルが優れている点も多いことと、全面的なソリッド化には設備投資にかかる費用の大きさ等も考慮に入れると、もう少し慎重な見極めが必要かと思われる。
現状では、サーフェイスとソリッドが融合した使い勝手の良い次世代のCAD/CAMシステムを期待している。
当社にとっても、現有システムと次世代システムとの切替えのタイミングは最重要課題であり、判断を誤ることのないよう、慎重を期したいと思っている。
金型メーカーの現状は、業態は製造業であるが、その中身は3次元の情報処理産業と言えなくもない。情報処理をいかに正確に早くできるかが、コストも品質も工期をも決めてしまうと言っても過言ではない。
競合他社に打ち勝っていくには、情報処理の正確さとスピードが最も重要であると考えている。
当社も時代に遅れることのないよう、常に新しい型生産のあり方を研究・実践して、この厳しい競争に勝ち残っていきたいと願っている。
会社プロフィール
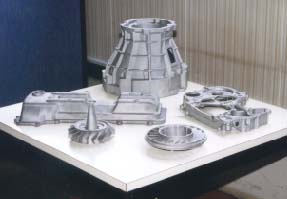
シンコー精機株式会社
創立 | 1979年11月に設立。1980年9月から本格的に創業。 |
---|---|
設立の目的 | アイシン軽金属株式会社で使用するAlダイカスト金型を、高品質、低コスト、短納期で供給することを目的として、アイシン軽金属の子会社として発足。 |
従業員数 | 29名(1999年6月現在) |
型の生産能力 | 250TONクラス~1650TONクラスまで、年間約70型を製作 |
特長 | CAD/CAMを基本とした独自の生産システムによる高品質、低価格、短工期の型製作 ・鋳造製品の内部品質を高めるための各種技術の提案 |
売上高 | 約6億4000万円(90%がアイシン軽金属向け) |
生産品目 | ダイカスト用金型およびトリミング型、金型鋳造用金型、冷間鍛造用金型、金型の修理・改造、その他金型部品の製作等 |