はじめに
「人とシステム」9号(1998年4月発行)「これからの金型業界」の掲載から約2年が経過し、コスト・納期・品質どれひとつとっても、金型業界にとっては厳しい環境ばかりです。前回と同じ皆様に、この2年間の変化を振り返り、これからの業界の進む道をお話し頂きました。
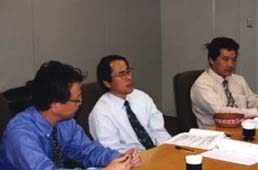
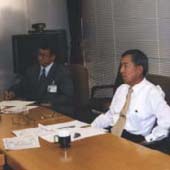
高野 2年前の97年は、金型産業にとって史上2番目に大きい生産高の良い年であったために、この2年間に激変しているということが話題になります。恐らく皆様が生産している金型の世界も同じだと思われます。
この2年間で、皆さんの会社の中での立場がどのように変わったかお話いただけますか。
白石 今まで技術を見ていましたが、全体のコストダウンをしなければいけないということで、99年の1月から、工場全体を見るようになり、生産管理を進めています。今まで、CAD/CAMに必要とされていたことも違う面から見ることができるのかなと思っています。
今は、生産管理をどのように進めていこうかということを一生懸命考えながら、クレーム処理と雑用に追われて、四苦八苦しているような現状です。
米谷 以前は、一技術者だったのが、課長になり、金型設計全体をまとめるという立場に変わりました。そこで、全体をみていかに効率よく仕事をまとめるかという点で、仕事の見方が変わってきました。
今は、金型設計をいかに効率化するかということをターゲットにしています。
堀川 メルコはプラスチック、ダイカスト金型の製作を行っており、以前は両方の金型の生産準備(構想設計からNC情報作成まで)を行う技術課を担当していましたが、昨今のお客様からのQ、C、Dの要求に対し、正確、かつ迅速に情報を提供する体制作りの一環として、プラスチック、ダイカストのグループに分け、特に売上げ、顧客の少ないダイキャストについては、受注活動から生産準備、NC加工、仕上げまでを一つのグループとし、仕事量、工程の進捗把握、顧客への対応、Q、C、Dの作り込みの責任者として、ダイカストグループを担当するようになりました。
金型の世界に何が起きているか
高野 最初はマクロ的に見て、今、金型の世界に何が起きているのかお話いただいて、それから細かい分野に入っていこうと思います。
米谷 この前は、品質が重要と言ったと思いますが、今は、コストが一番重要視されています。
品質を保ちつつ、いかにお客様のニーズに合ったコストで金型を作るか。コストを下げるということは、納期を短縮するということで、例えば、シリンダーヘッドの金型一式、今までは3~2.5ヶ月でしたが、最近は、3次元のデータまで支給するから、1.5ヶ月で加工組み付け仕上げまでしてほしい。納期が半分だからコストも半分だよと、そこまで要求されていますね。
我々もそのコストの中で利益が出る体制にしていかないといけない。金型自体の生産量も減っている中で、安定した受注をするために、デザインインという形が当面の作戦ですね。開発段階から仕事に携わって、お互いのメリットを確認しあいながら、提案をしていく。
環境を考慮したハイブリッドカーなどがでてくると、新型のエンジン、部品点数も増えます。そういう部品を開発段階から一緒にさせてもらって、お客様にも試作品を早く出すというメリットを提案しています。
堀川 我々のところでは、Q、Cは元より物を早く欲しいという要求が高いですね。金型を早く造れば当然コストは安くなる(時間を掛けずに)。
ヤマハ発動機のグループ会社ということもあり、デザイン段階から参画して製造要件の織り込みを行ってほしいとのデザインインの要求が高く、実際のプロジェクトでの展開実績も出てきています。
デザイン、設計段階での工数は増えますが、後工程での変更を最小限にすることができ、納期の短縮につながり、一次試作の本型物での評価が可能になります。
白石 最初から非常に難しい質問ですが、今後どのように金型業界で生き残っていくか。そのためには、当然コストダウンをしてないといけないのですが、その要求に追いつけていないですね。
金型業界が加工屋さんになりつつあるという中で、特化したものをどのように自社に作っていくかということを、今悩んでいるところです。
当社のお客様がアジアを回られて、そこでの価格を調査されましたが、韓国は3~4割安く、その価格がターゲットになっていると思います。当社の場合は、98年の10月ぐらいから、受注が減り引き合いが少なくなって、コストダウンを余儀なくされ、97年の春先の価格から3~4割下がっています。早急に、利益を出せる体制にしないといけない。どうやろうかというところを本当に悩んでいます。できたら教えていただきたいですね。
お客様が、ソリッドのミッドレンジCADで全部開発を進める方針で導入されるときに、当社に相談があり、金型メーカさんはずっと前から3次元CADを使っているからいろいろ教えてくださいと言われましたが、ソリッドの3次元設計と当社が使っている3次元のCADとは、基本的に違いますから、一緒に勉強していくような形で、開発段階から一緒に仕事をさせていただいております。抜き勾配や金型要件を織り込んでモデリングしてもらうために、当社の設計者が週に1~2度行きます。手配図面や3次元データが追いつかず、モデリングや、図面に寸法を入れる作業を手伝うこともあります。
お客様との取引の形態
高野 お客様との取引の形態、取引の内容、お客様の要求が変わってきているという部分はありますか。
米谷 メーカさんによって違います。寸法、寸法公差、仕上げ記号などの入った金型の3次元のソリッドデータを出すから、図面レスで加工してほしい、というところが増えつつありますね。この場合も当社で図面は書かなくていい。これからこういう形態が増えてくるでしょう。
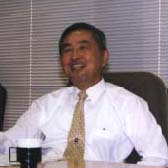
取締役副社長
高野 輝雄 様
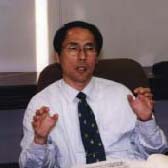
金型事業部D/Cグループ
グループ長
堀川 喜久雄 様
従来どおり、2次元図面、製品の3次元形状データ支給という形態はまだまだ残っています。この場合は、金型図面、部品の寸法公差まで入れて、補正、加工代などの金型要件などは図面に書いて返してくださいと言われます。
高野 3次元データ支給の場合は、米谷さんから見れば工数はずいぶん圧縮できるわけですね。
米谷 基本的には、3次元データがくるから工数が少なくなるということですが、実状はそうではないですね。そのまま加工して、ミスがあったらお客様の責任ですと言えばいいんでしょうが、我々としては、いい金型をお客様に納めたいので、どうしてもデータをチェックせざるを得ない。クリアランス、肉厚など確認をして、データとして大丈夫という裏を取ってから作業しているので、実際の工数はそんなに減っていません。
高野 以前に比べて作業内容が変わっていますね。
米谷 そうですね。今までは3次元形状を作るということが主体でしたが、モデリングからデータをチェックして、効率のいい加工のできるプログラムがいかに早く作れるかになります。
高野 金型の品質は当たり前、でも上流の製品データの品質がうんぬんというのは矛盾がありますね。
堀川 つじつまの合わないところは、型メーカが手直しをしてくれる。それが型メーカの技量になっていますね。
高野 その感覚はしばらくは変わらないでしょうね。金型の品質という点で、必要としない部分が過剰になっていたことがあったのではないでしょうか。
堀川 意匠側は当然、外観品質を要求されますが、裏面側については機能が優先されます。
客先からのコストダウン、短納期の要請もあり、傾斜やスライド部品については、客先指定の材質から機能、用途を満足すれば、切削性等を考慮し、材質の見直し、型構造についても、型強度等は技術的な裏付けをもとに、できるだけコンパクトな型製作を提案させていただいています。
今後も、製品形状でのVA/VE提案、解析、成形性も考慮した型製作への要求が高くなると思います。
白石 発注形態としましては、3次元データでいただくケースがかなり増え、6~7割ぐらいです。キャビティの意匠形状だけだったメーカが、コア側の面モデルをくれるようになってきています。2年前にデータがなかったメーカからデータが出てくるということはありませんが。
高野 データ精度という点ではどうですか。
白石 IGESで出てきますので、元の面が悪いのか、受け取るGRADE側が悪いのか、判断がつかないですが、新しい加工方法でどういう面でもある程度加工できるようになっています。
品質の要求については、寸法保証という面でだいぶ厳しくなってきています。昨年、成形機も入れましたので、成形品を納めるような形をとっています。初回に成形したときに成形品の製品寸法の測定データをお渡ししていたのが、試作での小ロット注文でも、ロットごとに寸法検査表をつけて出すという成形屋さん並の要求がきています。
試作の金型を量産に使おうという話もあります。試作だけの場合、短納期にあわせるために金型構造や量産を考えずに作ります。それで量産型がきた場合に、型構造上非常に難しくなりますので、形状変更の依頼を出すのです。そうすると、試作型はできたじゃないかという話になって、非常につらい思いをしているのが現状です。
高野 それは構造が全然違いますから、よく説明をしてわかっていただく必要がありますね。
データで受注する際、何が一番大きい問題でしょうか。
白石 面の整理は必要になってきます。IGESの設定の中で、面が重なっている、お客様のモデルできちっとソリッドがくっついていない、まったく同じ面が2つあったり、面数が相当増えている場合もあります。非常に少ない構成点のサーフェイスになっている場合など、面のはりかえになります。構成点が多いデータをいただいた場合は、今の性能では動かない状態になってしまいます。お客様によっては、ボスやリブなど全データを出してくださいますが、データが重たくなるばかりで、それを整理するのが大変な作業になります。
堀川 客先により違いますが、プラスチックの場合は支給される情報は基本的には、意匠面の面データ+機能形状はワイヤーフレームが多いですね。裏面側まで面データを支給されることは少ないですね。客先によってはやはりデータの整理は必要になります。
ダイカストでは、客先が少ないので他社は解りませんが、2次元の図面データがほとんどで、こちらで3次元データ化します。
高野 米谷さんのところは、客先が持っているシステムでデータを渡したいという要求はありますか。
米谷 そう言われれば、「はい、入れます」と言わざるを得ないでしょうが、CATIA、I-DEAS、CADCIAS、統合CAD、Pro/Eなど、お客様それぞれ使っているシステムが違います。データを受けることを主目的としPro/Eを入れましたが、メーカさんからPro/Eでデータが出ることが少なく、投資した効果があまり上がらなかったこともありましたので、闇雲に入れるわけにもいかないです。
そこで、IGES、STEP、ACISデータなど共通のデータでいただいております。強引にI-DEASを入れろ、Pro/Eを入れろという話は、今のところないですね。
NCテープまで出すから加工だけしてという場合もあります。エンジンのポートですと、削り方によって面粗度なり、形状の荒さが変わってきてエンジンの性能に影響がでます。テープを出してそのとおり加工すれば、世界のどこで作っても同じ物ができるのでテープを出す目的はわかるのですが、現実問題としては難しいでしょう。
高野 お客様の方は、そういう仕様まで持って初めて価格は3割安くなるということなんですが、体制を作る前に価格が先になってるという気がします。
米谷 データを出すから安くしろという話だけが先行しています。3次元化というのは、今は上流のところだけ動いていて、今まで図面で承認を得ていたのが今後3次元で承認をしますといったときに、鋳造現場の品質保証までそのデータがおりてくる体制ができていない。3次元化に対して明確な方向付けがされていないのが現状です。
この2年間の技術の進歩、変化
高野 この2年間、価格との戦い、納期との戦いの中で、技術的に進んだのはどういうところでしょうか。
白石 成形機を入れたということは大きかったと思います。それまでは、トライはすべてお客様でやってもらっていたので、お客様のところに金型をお持ちしてうまく流れない、成形できないというときなど、型を移動する時間がロスしていました。自社でトライをするようになって、それがなくなりました。
また、お客様が当社にきてくださって成形条件を詰めていただけるので、成形機を入れて間もない当社にとっては、大変いい勉強になっています。その結果、成形のことを考えた型設計、型作りができるようになってきました。特に、設計部隊には成形に立ち合わせて、成形条件、樹脂の流れを考えるようにさせています。そういう方向で進んでいるのは間違いないですね。
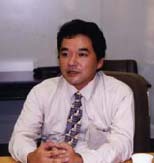
製造部 課長
白石 龍二 様
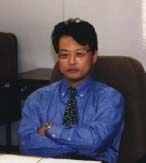
システム課 課長
米谷 強 様
成形機を入れて、納期的に少し余裕は出たかなと思いますが、それ以上に品質も高く要求されていますから、品質が上がって、期間的にはあまり変わっていないというのが現状だと思います。
高野 お客様の技術的な満足度はどうですか。
白石 上がっていると思います。しかも量産機を止めなくていいというのが大きいとおっしゃいますね。
米谷 ダイカスト、LPなどで鋳造したものを試作品として納めることもあります。設計者が造形の場面に立ち会って問題を見ることで、金型の品質自体も設計の品質自体も上がってきますし、お客様の造形機を止めないで、試作の仕事ももらえるということで非常にメリットがあります。
高野 シミュレーションについてはいかがですか。
米谷 ダイカスト、GDCLPの湯流れ、凝固に関してやっています。シェルモードの解析は難しいですね。素材のバリをなくすために、金型の熱変形によるバリの解析をしたいですね。
高野 シミュレーションとトライワンの結果との差はどの程度で、何点ぐらい取れますか。
米谷 解析はひとつの条件を与えて実行しますが、実際の鋳造現場ではその日の気温、湿度などによって1回ごとに変わってきますから、なかなかそれがぴったりくるわけでもない。でも、この辺に出そうだと傾向がわかるだけでも70点はあげたいですね。
解析により、トライの条件の決め込みがやりやすくなり、一発目で良品がとれるようになり、トライの回数は減りました。解析の方も実際にトライすることによって条件の品質も上がってきますし、実際の方も解析の条件によって良品が取れるようになる。お互いに補完し合っています。
堀川 この2年、取り組んできたことは、
①工程での不具合の削減。
②生産準備、加工工程の標準化です。
不具合を出せば、当然修正コストも発生すれば、部品遅延にもなり、遅れを取り戻そうと無理をし、新たな問題の発生引き起こす。
まず、品証グループを中心に生産準備と機械加工で起きた不具合の発生を作業者が申告することから始め、とにかく社内外で発生する不具合数を把握し顕在化させ、不具合に対する意識の高揚につとめてきました。要因を分析し、できるところから対策を始めました。
標準化では、生産準備グループの業務範囲は、客先での仕様打合わせから始まり、型、電極設計、モデリング、NC情報、測定情報作成、トライ立ち会いフォローまで広く、Q、C、Dの80%はこの工程の能力で決まってしまいます。
生産準備と加工のミーティングを定常化し、工場で起こっている問題点をフィードバックし対策を検討、設計標準、加工標準に織り込んできました。
高野 特徴的に現れた不具合の要素は何ですか。
堀川 加工では、切削時の負荷での刃具の振れ、抜けによるワークへの喰い込み。
生産準備では、NC情報チェックの見落とし、部品図の公差、寸法記入漏れ、間違いです。
特に1~2年生クラスの不具合が多いので、このクラスの教育をどうしていくか?リーダークラスの持つノウハウをどのようにして標準、手順書にしていくか、さらに進めていく必要があります。
納期短縮のキーは
高野 納期短縮のポイントには何かありますか。
米谷 加工においては、高速加工、複合加工機。旋盤ものに穴をあける場合、旋盤にのせてから、段取りがえして穴をあけるのではなく、複合機で、一つのマシンでできるようにする。生産準備は不具合を出さない。効率のいい加工ができるようにする。工程を分析して、各工程でどういうことをすれば一番早く設計ができるか、加工の速いテープができるか。細かく分析して、ひとつひとつやっていかないと、ドラスティックにつめることはできない状況です。
白石 前は技術にいましたので、3次元設計での設計ミスをなくし、設計とCAMをひとつにして、自社の中で一番賃率の高い部門のコストをいかに減らすか、ミスをいかに減らすかです。3次元設計により、単純なポカミスが削減できるのではないかと思っています。
今の立場では、工場全体を見ていますので、工程管理をする上でいかに流して工期を縮めるか。毎日4~5型、月に100型ぐらい出荷している。でも100型も生産できるわけはなく、結局は出戻りが多いわけです。出戻り、トライ回数を減らしていくかということです。そういう管理体制をとっていきたいと考えています。
高野 金型の工数の中で、設計からCAMにかけての部分が占める割合がものすごく大きいですね。これを徹底的に小さくしないと全体的に縮まらない。人の問題もありますし、難しい部分ですね。
白石 CAD/CAMは、一番陳腐化の早い部分で、人をかければかけるだけ、設備も入れなければいけない。工作機は動かしただけ賃率は下がる。設計は、残業すればするだけ悪くなるのですよね。CAD/CAMという部分をいかに効率化するか。できれば、半分ぐらいの時間で金型設計からCAMまでやってしまうというぐらいでないと、今後太刀打ちできないと感じています。そのための社員教育も重要なファクターになっています。
高野 NCマシンの無人稼働率はどれぐらいですか。
白石 リブ堀りをするようになったので、平均して1台あたり、30~50時間は増えてきたと思います。
高野 目標を持ってやっておられるなかで、ネックになっている部分はありますか。
白石 職人さんとコンピュータのつながり、そこが非常に難しいですね。職人さんの技術をいかに観察してマニュアル化していくか。技能をどうやってコンピュータに取り入れていくか。ベテランの職人さんにそこをどううまく理解してもらってやっていくかというところでしょうね。
堀川 生産準備では、設計の標準化、部品の標準部品化(設計の3次元化が早期にできる)。図面を減らせば不具合の削減につながる。
加工では、部品毎に最適な標準工程をきちっと決め、必要な機械に最適な部品をセットする。
仕上げでは、社内トライの位置づけを明確にする。どうしても客先のトライ要求に合わせて安易にイベントにしがちなので、このトライの目的、何を評価するのか明確にして、トライの回数の削減を心掛けていく。
目標はトライ一発。
海外の金型との戦い
高野 韓国とは、為替差を含めて労務費の違いが大きくある。2シフト体制で、納期が短い。その一方、技術レベルは上がってきている。これから我々はどうやって戦っていくのでしょうか。
白石 昨年から、韓国から材料を仕入れるようにしましたので、価格面では韓国は安いですね。当社が使っている材料屋さんは24時間体制ですので、納期的にも非常に早いです。
ソウルから仁川の型屋さんを見て回りましたが、韓国のほうが台湾より進んでいると思いました。細かいところを見ると、どうかなというところがありますが。今までは台湾に出していましたが、はじめて韓国にも金型を出しているところです。
台湾も、そこそこの精度で加工してきます。何が違うかというと、仕上げの合わせ技術が一番違います。仕上げの合わせは、日本人の感覚がベストかなという気がしています。台湾では納期、価格にみあった合わせしかしない。その金型を社内に持って帰ると、仕上げの者が合わせの途中で止めていると言います。韓国もまだ型ができていませんが、同じような感じかなという印象です。
そうなれば、当社からデータを支給して、材料も全部向こうで調達して加工だけやってもらい、こちらで組めばそこそこ安くできる。できるかどうかはわかりませんが、そういうやり方もあるのかなと思っています。
堀川 海外との競争については、相手国によって違ってくると思います。
ヨーロッパ、米国を考えれば、品質、コスト、納期において日本が劣るとは考えられない。コミュニケーションの問題があり直接取り引きがむづかしいがこれが解消できれば可能性が高い。
アジア諸国を見たとき、例えば、中国からの金型の受注を考えてみると、中国での要求品質(要求品質が上がらない限りは)、価格では、人件費が高い日本で金型を造って送ったのでは合わない。逆に中国の現在の型製作の品質レベルをみれば、日本に持ってくるのは難しい。
中国に日本から生産準備、管理の技術を持ち込んで、現地の人たちに対し教育し、金型製作を行う。人の定着、人、外注の管理には問題があると思いますが、むしろこの辺を拠点にして、アジア諸国に金型を輸出したら面白いかもしれない。
いずれにしても、まだ国内の金型の仕事がなくなってしまったわけではないので、さらにQ、C、D作り込みをしっかり行い、競争力をつけ、対応できるようにしていきたい。
米谷 国内で安定した受注量が確保できない以上、海外に目を向けないといけない。そういったときに、設計者、生産準備に関わる人たちが、外国語で対等にニュアンス的なものまで含めて打ち合わせができるようにならないと太刀打ちができない。品質は大丈夫。コストも何とか頑張れば大丈夫。ところが、実際に製品を立ち上げるわけですから、よりコミュニケーションしやすいほうに話がいくのは当然のことです。日本語だけで間に商社に取り持ってもらってると、マージンが入りますから、直接、海外のメーカと対等に打ち合わせのできる体制を取らないといけないでしょう。金型の品質、コストを含めて、ヨーロッパには負けていないと思います。あとは、語学力、インターネット、電子メールなどで自由に対等にやれるような体制にしないといけないということ、為替変動があってもそれを吸収できる体力が必要ですね。
高野 日本に残る部分は精密度の高いもの、設備投資が多額になる大型のもの。これらの中間的な要素のものが、海外競争には弱い部分が目立ってきているように感じます。
ひとつだけいえることは、金型の発展途上国では、今は金型の周辺のインフラが遅れていますが、これらが進んでくるとより競争力がつき、問題かなと思います。設備投資に関しては、高度な機械はまだまだ日本だろうと思いますが、韓国にしても台湾にしても工作機械メーカが育ってきていて、日本の工作機械に比べて値段が安い。CAD/CAMのシステムも、同じシステムでも彼らが買うほうが安いという問題がありますね。人件費安いよ、その他も安いよ。まず価格競争力に対しては大変弱いなという気がします。
中国も金型は伸びています。彼らが設備を買うときは新しい設備を買う。日本の金型屋さんは、多少疲れてきていて、設備投資ができない。このような差も目立ちます。上海の南に、金型屋さんが500社ぐらい集まっている市があります。一社でいろいろな設備を持つと大変なので、中核になる金型屋さんがCAD/CAM、マシニングセンターを持っていて、金型屋をまとめ上げている。周囲にはあらゆる賃加工メーカがあり、しのぎを削っている。この辺が力をつけてきています。
シンセンにある千人もいる金型屋さんは、プラスチックのPCの箱物を21日間の納期で1セット仕上げる力を持ち、アメリカのPCメーカがそこに仕事を持ち込んでいるそうです。千人の人たちが、最新の設備を持ち、2交代で働いているそうですが、脅威だなという気がします。
日本は、どういう特長を持てば勝ち残っていけるのかを考えてしまいます。
HZSへ
高野 今日本の型産業は、変革期に来ています。この座談会でも話題になっていることがそれぞれのキーポイントになっていて、いい形でより高度なCAD/CAMの武装をしていかないと、コストも下げられない、納期も縮められない、お客様のニーズも呼び込めないと思います。HZSに望むことをお話いただけますか。
白石 3次元金型設計支援システムがでてきていますが、それが完璧になればなるほど、どこでも型設計ができるようになって、加工屋さんになってしまうのではと懸念しています。
設計支援というところに重点をおいて、各社固有の技術を取り入れてカスタマイズできるシステムを作っていただきたい。金型分野のシステムメーカの中ではNo.1のHZSさんにしては、金型設計支援システムの開発は遅れていると思います。早くいいものを出していただきたいと思っています。
これからは、ミッドレンジのソリッドが中心になってくると思います。データを受けるときに、モデリングの履歴というのが非常に問題になってくるのではないかと思います。履歴をうまく使えるようにする場合と、まったく履歴を消してしまって自由に変更ができるようなシステムとを考えながら作っていかれたらいいのではないかなと思います。
堀川 システムを上手く使いこなし生産効率を上げることは、どれだけ作業が標準化できているかがポイントだと思います。
これからは、設計では標準化された部品、製品の3次元データを簡単に取り込んで、設計ができるようなパラメトリックな3次元金型設計システムの開発が必要です。型強度、歪みの解析。しかもデータは軽く!
加工側では、この3次元CADデータを受け取り、標準工程設計に基づきNC情報を自動出力するCAMシステムを開発してほしいと思います。
GRADEのように高いハードに依存するシステムは一番厳しいところに来たと思います。最低限、GRADE/CUBEのPC版への移行、他システムからの情報の授受のスピード、信頼性を高めることを早急に実現してほしい思います。
米谷 データ変換ですね。3次元のデータが取れることを前提に仕事を受けているわけですから、GRADEでデータを受けれないと、仕事ができないわけです。それをきっちり受けられるような形にしてほしい。
CATIA、Pro/E、I-DEASのダイレクトインターフェースを早急に整備してほしい。そうすれば無駄な投資をしなくてすみます。I-DEASが1台あっても、それだけでは仕事にならないのです。パラレルで作業するためには人を分けないといけない。台数があるGRADEをうまく使って、効率を上げるためには、データ変換を最重要項目として希望します。
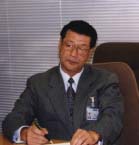
竹内 金型システム事業本部では、売る、サポートする、開発する、この3つを束ねています。お客様の要望ニーズを的確に収集してそれにあったシステムをご提供する。我々システムメーカも、製造業と同じです。よい製品を早く安く作る。
その中で皆さんが言われた3つの課題。型設計システム。データサーバ。CAMの全自動化。今年度、この3つは何が何でもやります。
型設計システムについては、金型メーカさん何社かと一緒にし、プロジェクトに金型設計の経験者を入れています。型設計のシステムがあるから、勝手にできるというものではなくて、過去のノウハウが蓄積された中でこのシステムを使って、いいものを早く作る。型設計プロジェクトチームを作って、十数名これにかけています。今年度末にVer.1を出します。単に図面を書くだけでは面白くないので、CAEを入れた型設計システムで、他社より一歩前に行きたいと考えています。
データサーバ。お客様が、大手メーカさんのCAD/CAMにあわせて導入することはできない。特に自動車関連では、トヨタの統合CAD、CATIA、I-DEASなどのデータをダイレクトに受けるためのデータサーバという形に取り組んでいる最中です。
CAMの自動化。バッチ的なシステムを使っていくためのデータベースをインテリジェントな形で用意して、それをお客様ごとに変換すれば使っていけるような形になると思っています。
この3点、一番必要なところからきちっとやります。
皆さん、今日はどうもありがとうございました。