横浜ゴム株式会社様は、ゴム高分子技術の可能性を常に追求され、タイヤを核とする自動車分野、航空・宇宙、土木・建築、海洋、橋梁、鉱工業、スポーツ・レジャーなどの幅広い分野において、グローバルな事業を展開されています。平塚製造所は、全工場の総合生産拠点であると同時に、最先端の技術戦略拠点でもあり、総合的な開発研究を推進されています。
今回は、解析ソフトMSC.Dytran、MSC.Nastran、MSC.Patranの導入の効果、今後の課題などを中心に、タイヤ技術管理部 技術企画グループ主幹 田島様にお話をお伺いしました。
事業内容、タイヤ技術本部について
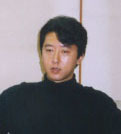
技術企画グループ
主幹 田島 様
横浜ゴムは、タイヤをメインとする自動車部品から、航空・宇宙関連、マルチビジネス部門では、ベルトホース、防舷材、ゴルフなどのスポーツ用品、その他各種工業品などを製造しています。
タイヤ技術本部では、乗用車、トラック、バスなどのタイヤから、航空機、特殊タイヤ、ゴムチェーンなどを開発しております。
私は、タイヤ技術管理部に所属しておりまして、データベースからネットワーク、スーパーコンピュータからパソコン、ソフトからハードまでコンピュータ関係全般を管理運営し、また、タイヤ開発に必要なソフトウェアの開発などを行っております。
本年7月までは、ビジネスプロセス(BP)革新推進部という部門に所属し、開発リードタイムを半分以下にするというプロジェクトに入っていました。
3次元設計への取り組み
◆ 導入の背景
改善のための取り組みは、まず最初に3次元設計への移行でした。
タイヤは幅方向の曲率と周方向の曲率と2重に曲率を持っています。今までは、2次元のタイヤの断面を絵に描いて、それぞれの曲率にタイヤの溝の絵を投影してパターンを作っていました。断面形状も2次元、溝も2次元となると、3次元形状にしたときに、さまざまな問題が発生するので、2次元での設計には限界がありました。そのため、最初から3次元CADを使ってのタイヤ設計に取り組みました。
また、タイヤには軽自動車から大型の乗用車までさまざまな大きさがあります。あるシリーズのタイヤでは、デザインは同じでもサイズが変わってきます。ある一つのデザインから、複数の大きさのデザインを作り出そうとすると、パラメトリックで設計できる機能がどうしても必要だということも、3次元CADの導入の背景にありました。
1997年末に3次元CADを導入し、3次元設計に取り組んでいます。
◆ 移行期
今も3次元設計の移行期です。新規開発するものは3次元で設計していますが、既存の製品を改良しなければいけないとき、以前に設計された金型を新規に製作しなければいけないときは、2次元データで作業します。まだ、混在しているのが実状です。
3次元CADデータは、社内の製作部門やモールドメーカさんにお渡して、カッターパス生成に利用されております。
3次元CADデータがあれば基本的には金型製作のためのカッターパスが出せるのですが、3次元データがあれば図面レスになるかというと、金型仕上げの段階等で現場の方が作業されるときに図面を見ますので、図面はまだ必要です。
◆ モデリング
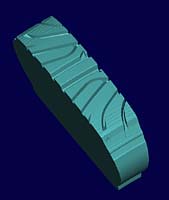
(1ブロック)
我々がモデリングするのは、1つの溝パターンを含む1ブロックだけです。ひとつのタイヤは異なる大きさの複数のブロックから構成されておりますが、1ブロックを作るとパラメータを変えるだけでいろいろな大きさの他のブロックを生成することができます。また、パラメータを変えることで異なるサイズのタイヤを生成することもできます。
また、このとき同時に図面も作成しますが、図面自体もモデルと連動しているので、モデルを変更すれば図面も変わります。今までの変更作業がモデルを通して一元的に実施することができるため、モデルと図面との不整合や修正ミスなどがほとんどなくなります。
当社で、パラメトリックに変更されたモデルも含め、すべてのモデルの検証を行った後、モールドメーカさんへ3次元モデルデータをお渡ししております。
1つのブロックのカッターパスを設定しておけば異なるブロックのカッターパスはパラメータの変更に追従して変化するので、すべてのブロックについてカッターパスを生成する必要はなくなるので、以前の2次元データで、それぞれのブロックのカッターパスを個別に作成していたのと比べると、金型製作はかなり効率化されたと思います。
バーチャルな試作
◆ 試作機の削減
タイヤを開発するためには試作をします。いろいろな試験をして、それを評価していますので、試作用としてタイヤを何十本も作る場合もあり、かなりの費用と時間がかかります。
また、試験を行う試験機も極めて高価で、さらにそれを運用していくにも年間でかなりのコストになります。
そこで、解析ソフトを使って、バーチャルな試験をすることで、まずは試験のための試作を減らそうと考えています。
現在では、解析を行うツールがそろってきていますので、以前までは、実際に試作タイヤを作らなければ評価できなかった場合でも、シミュレーションを行うことにより、試作タイヤを作らずに評価できる部分も出てきました。
最後はどうしても試験機を使ったテストをしますが、闇雲に全部作ってテストするのではなく、解析ソフトを駆使してある程度絞り込んだものに関してのみテストするということです。
◆ 人間の感覚によるテスト
人間の感覚でしかわからないテストもありますので、最終的には、人によりテストが行われます。
この人間での感覚でのテストですが、それも数値化しようと研究しています。車の挙動でのドライバーの心拍数や心電図での波形を周波数分析して、従来からのドライバーのフィーリングという尺度を、心拍、脳波という定量的な尺度へ置き換えるという研究なども行っております。
電子図書館
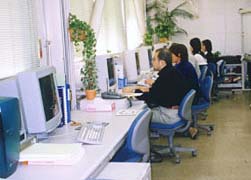
試験をした結果ですが、良かった悪かったの判定だけでなく、なぜ良かったのか、なぜ悪かったのかを、技術資料/要素技術として電子図書館というWeb技術を使ったシステムに蓄積しています。
電子図書館には、様々な文書フォーマットで作成された技術文書、報告書、図面やデータから日本の特許にわたる、様々なデータが約300GBのディスクに保管しています。それらのデータは、当社のイントラネット上から、セキュリティを確保しながらも、誰もが閲覧することができるファイリング・システムとなっています。電子図書館は、Webのサーチャーのような全文検索から、個別の項目(例えば作成者とか)を詳細に設定して検索する仕組みなどを利用者に提供しています。
MSC.Dytran, MSC.Nastran, MSC.Patran導入
1997年にHZSを通じて、MSC.Dytran、MSC.Nastran、MSC.Patranの解析ソフトを導入しました。陽解法のソフトはMSC.Dytran以外にも利用していますが、流体/構造連成問題への初めての取組みということも有り、MSC.Dytranを使いこなすまでにはいろいろ苦労しました。最近の商用FEMソフトは従来のものとは比べ物にならないくらい高機能なものが増え、最も複雑な構造物の一つとされるタイヤのシミュレーションも大きく前進してきました。しかし、逆にそれらのソフトを使いこなし複雑な現象を解明していくには、ユーザーサイドにも高度なさまざまなスキルが要求されます。そこで、弊社では事業本部の枠を超えてさまざまなバックグラウンドを有する人材を集めたプロジェクトを発足し、FEMシミュレーションに関する技術開発はそちらで対応しています。
タイヤのFEM解析
◆ タイヤFEM解析の特徴
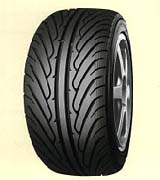
グランプリ (DNA GP)
弊社でのタイヤのFEM解析は本当に歴史が長く、今から約25年前に軸対称問題を解くための非線形FEMソフトを内作するところから始まっています。タイヤは、ゴム材料と有機繊維やスチールコードの補強材で構成された複合構造物です。ゴムは金属材料とは異なり、引張った時の伸びと力の関係が逆S字の非線形弾性を示します。さらに時間依存の粘弾性特性を有していますので、タイヤのFEM解析ではこれらの材料特性の評価が非常に重要となります。
また、自動車に装着されたタイヤは路面に接地した状態で大きく撓みますので、路面との接触と大変形を考慮しなければなりません。さらにタイヤの運動特性を予測するには動的な回転接触の効果も考慮しなければならなくなり、問題はますます複雑化していきます。このことが、タイヤは最も複雑な構造物の一つであると良く言われる所以です。
◆ ハイドロプレーニング・シミュレーション
ハイドロプレーニングとは、雨の日などに水膜で覆われた路面を自動車が走行した時、タイヤと路面の間に水膜が侵入してタイヤの摩擦力が失われる現象です。原因としては、水膜から受ける流体圧力がタイヤの接地圧力よりも高くなるためであると考えられていますが、タイヤのハイドロプレーニング性能の良し悪しはトレッドパターンの排水能力に大きく依存します。
従いまして、ハイドロプレーニング現象を数値シミュレーションで予測するには、トレッドパターンの影響を考慮しなければ全く意味がありません。しかも、タイヤという変形し易い構造物と水膜という流体が連成する複雑な現象ですので、非常に難易度の高いシミュレーション技術が要求されます。
これをいまMSC.Dytranを使って解析していますが、MSC.Dytranで提供されているオイラー/ラグランジュのジェネラルカップリング機能をもってして初めて解析可能となった事例です。どのようなトレッドパターンであれば最も排水性が高くなるのかなどといった、ハイドロプレーニング現象が発生するときのタイヤと路面間の状態を多角的に解析しています。
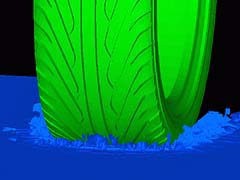

◆ その他の解析
ハイドロプレーニング現象のシミュレーションの他にも、乗用車用タイヤ開発のために運動性能シミュレーションとしてコーナーリング・シミュレーション、NVH性能シミュレーションとして振動固有値解析、そして、環境性能シミュレーションとして転がり抵抗シミュレーションなどを実施しています。MSC.Nastranを導入しましたきっかけもNVH性能シミュレーションへの対応の一環です。その他にも、さまざまなシミュレーションを駆使して蓄積したノウハウを、乗用車用タイヤばかりではなく各種タイヤ開発へ活かしています。
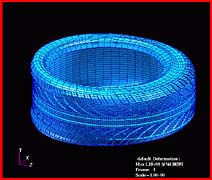
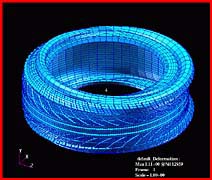
◆ コンピュータの性能
先ほどもお話しましたが、最近は市販のFEM解析ソフトの能力が格段に向上しています。そのこととあいまって、コンピュータの計算速度が格段に速くなっていますので、従来では到底思いも及ばなかったシミュレーションが加速度的に可能になってきました。ここでご紹介していますハイドロプレーニング現象のシミュレーションもその一例ですが、2000年を待たずに解析できるとは考えられませんでした。
現在、 弊社ではFEM解析のためにさまざまなカテゴリーのコンピュータと解析ソフトを導入していますが、ハードとソフトのマッチングを考慮した組み合わせで効率的に活用しています。しかしながら、コンピュータの処理速度は現状で十分であるとは言えません。今後、さらに高速化されることを望んでいます。
今日では、スーパーコンピュータと呼ばれるコンピュータは超並列マシンを指しますが、商用のFEMソフトも今後更に並列処理に対応していくのではないでしょうか。或る会社では1CPUで9ヶ月を要していた計算を256CPUで並列処理することにより計算時間を1日に短縮できた事例が有るそうですが、設計最適化をも包含した予測設計を実現するためには我々も今後はそちらの方向を模索しなければならないだろうと考えています。
タイヤの開発
デザイナーの感性でタイヤの溝をデザインして、次に、設計者が性能とデザインを照らし合わせて解析しながら設計していきます。ただし、特殊な3次元の解析になると解析専門の部隊で行います。
ひとつのタイヤを開発するのに、設計者は1~2名ですが、その他に、モデリングを実施する者、解析を行う者などがおります。
現在、開発期間は乗用車でいえば1つのタイヤで7~8ヶ月だったのが3.5~4ヶ月になってきています。開発期間を短縮して、常に新しい・いいものをできるだけ安価で市場に送り込み、お客様に満足していただくことが、私どもの使命だと考えております。
◆ OEM
自動車メーカさんからは、時期販売する自動車で車種を指定され、その自動車の専用タイヤを各タイヤメーカに依頼されます。ある程度の車のコンセプトやタイヤへの要求性能をいただいて、それに基づいてタイヤの開発を実施します。その開発したタイヤを自動車メーカさんで評価していただいて、どのタイヤメーカのタイヤを使うかが決まります。常にタイヤメーカの競争です。
新車についているタイヤは、自動車メーカさんがあらゆる面からチェックされたタイヤですから、トータルバランスに優れていて、その車に最もマッチングするタイヤになります。
◆ リプレース用
一般にカーショップの店頭に並んでいるのがリプレース用のタイヤです。リプレース用のタイヤは、お客様の嗜好を取りいれた、乗り心地、快適性、操縦安定性などに関する性能をふったものをシリーズとしてラインナップしております。
◆ CO2カット
「ころがり抵抗」を小さくして、CO2をカットするというコンセプトで開発した新素材をDNAというシリーズのタイヤに採用しています。
このタイヤは、タイヤ自体の発熱を押さえ、路面とのグリップを確保しながらも滑らかに転動していき、車のエンジンの効率を引き上げます。
テレビ会議
総合タイヤテストコースであるD-PARC(ディー・パーク)であらゆる角度から実車テストを行っています。ここにマルチメディア会議システムPictureTelを導入しています。
テストセンターと周回路4箇所の上にカメラを設置していますので、走行の様子を見ることができますし、そのカメラは遠隔操作をすることもできます。富士スピードウェイ、鈴鹿のコースなどの現地とテレビ会議をしたこともありました。リアルタイムで状況が確認できるので非常に便利です。
冬季用タイヤ専用テストコースT*MARY(ティー・マリー)もあります。このテストコースは、圧雪路、氷結路を再現しています。そこにもPictureTelが入っておりまして、工場や販売会社を含めて、現在、15台のPictureTelを導入しています。
今後の課題
まず1点目は、ビジネス・プロセスによる3次元の取り組みで、開発リードタイムを7~8ヶ月から、3.5~4ヶ月に達成できましたが、これまたさらに、短縮したいと考えています。
これには、「タイヤ開発」のあらゆるプロセスがコンカレントに流れていないと具現化できません。業務自体を全部見直して、コンピュータ化できる部分はすべて取り組み、本当に設計者が持っている感性を生かせるという環境に持っていきたいです。
◆ バーチャルな試験
解析ソフトが充実してきているので、これからは、コンピュータを使ったバーチャルな試験が本当に実現できるようになってきます。バーチャルな試験を充実させて、最終的な試験は本当に必要なものだけにするように取り組んでいきます。さらに、コンピュータ上で、バーチャルな試験で得られた結果を電子図書館に蓄積していくことで、バーチャルな試験自体もいらなくなるという環境を目指しております。
HZSについて
HZSへは、いろいろな要望を出しますが、それに対して応対も速いし、きちっり対応してくれます。他のメーカさんと比べて、HZSの対応が本来の対応ではないかと思います。
おわりに
平塚製造所内には、日英同盟に基づき明治39年に建設された「平塚ゴム記念館」があり、重要文化材に指定されているそうです。また、待合コーナの一角にはF3000が展示されてあり、モータスポーツ活動にも積極的に参戦されています。
タイヤというと誰もが身近に感じるものですが、安全、快適、活力を備えるために、技術はもとよりさまざまな開発課程を経て製造されていることがわかり大変勉強になりました。
大変お忙しいところ、貴重な時間をさいてお話を聞かせていただき、ありがとうございました。この場を借りてお礼申し上げます。
会社プロフィール
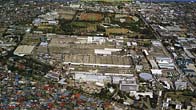
横浜ゴム株式会社
本社 | 東京都港区新橋5丁目36番11号 |
---|---|
創立 | 大正6年(1917年)10月13日 |
従業員 | 5,622名(1999年3月末現在) |
資本金 | 389億900万円(1999年3月末) |
売上げ高 | 2,402億900万円(1999年3月期) |
営業品目 | 自動車用、トラック・バス用、航空機用タイヤ、ベルト、防舷材、その他各種工業品、航空機用各種部品、スポーツ用品 |
平塚製造所 | 神奈川県平塚市追分2番1号 |
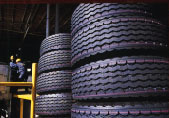
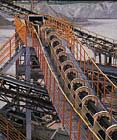
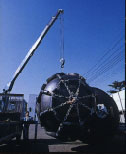
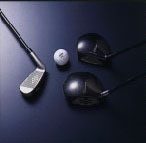