「ツーリングシステム」「メインジェネレーター」について
株式会社タカギセイコー 金型事業部 工機課 技士 中谷 明広 様 |
事業概要について
当社は、プラスチック工業部品の専門メーカーで、今年創業60年を迎える歴史ある会社です。本社は、富山県高岡市にあり、工場は富山県新湊市、氷見市や静岡県 浜松市など全国に8ヶ所あります。
金型設計・製造ネットワークのハブといえる金型事業部は、新湊の金型・技術センター内にあり、従業員は126名で、当社の売上高に占める金型事業全体の比率は、約13%を占めています。
当社が扱っている商品は、2輪・4輪等の車両機器分野が約45%、通信機器分野、OA機器分野がそれぞれ約20%、その他農業機械、建設機械等といった構成となっています。特に近年、携帯電話の伸びは顕著なものがあり、当社で製造した携帯電話の外装筐体は、日本で販売されている携帯電話の1/3強を占めています。
当社は、社内においてプラスチック工業部品の研究開発/技術開発、金型設計・製作、成形、塗装、組立てまでを一貫生産ラインで行える体制があります。成形は射出成形が主体で、AGI成形、DSI成形などの特殊射出成形や、その他DCPD-RIM成形、ブロー成形、回転成形、押出成形、超大型のFRP成形などを行っています。
プラスチック工業部品のあらゆる分野に対応でき、さらに各々の工程について独自のノウハウを持っていることが当社の特長です。
製品の品質については、開発段階では設計評価、製品化にいたる工程では製品評価といった、デザイン段階から組み立てまで、ISO9000に準拠した品質評価体制を導入しています。以上のことからプラスチック成形品において、お客様が求めている機能、価格、品質に対して、当社は、最も適している成形法を検討し提案することができるのです。
金型事業部では、金型製作だけではなく、デザイン段階から量産工場での立ち上げまでを、一貫した技術で対応しています。
製品の開発、設計では、サーフェイス設計グループとソリッド設計グループにわかれています。サーフェイス製品設計チームにおいては、サーフェイスモデラーのデザイン・イン体制をとり、機構部設計・3Dデータ化をお客様と一緒に行っています。なお、サーフェイス金型設計チームでは、㈱日立造船情報システム(以下、HZS)が開発している3次元金型設計システムに、協力会社の一員として型設計の経験とノウハウを提供しています。
ソリッド設計グループにおいても、コンカレントエンジニアリング体制をとり、お客様の設計に協力して製品設計と金型設計を同時に進めています。ソリッド金型設計チームでは、金型設計システム"Rapid Mold Design Tool"を完成させました。このシステムは新しく設立した㈱アイティー金型エンジニアリングで販売する計画です。
CAM部門では、NCデータを大量に作ることが急務になってきています。この対応として、データ生産合弁会社㈱ディスモを設立、又上海にもNCデータ生産を委託し、更に中国にも合弁で南海華達高木模具有限公司を設立し金型製作の事業展開をしています。
HZSとの取り組みについて
HZSと当社は、96年度に「金型生産性を高めるCAM機能を検討しGRADEシステムでの実用性をはかる」ことを目的として、共同プロジェクトを発足させました。この目標を推進するために、定期的にミーティングを行い、その成果を確認するために半期毎に発表会も実施しています。現在は、これを発展させ「CAM作業の自動化」をテーマとし、開発を進めているところです。
この共同プロジェクトから当社CADでは、GRADEベースの2次元設計システム、CAMでは、上記システムからの穴情報をもとに穴加工データを半自動作成する2次元穴加工システムを開発することができました。
今回紹介するCAM支援システムである「ツーリングシステム」と「メインジェネレーター」も、この共同プロジェクトにて発案され作成されたシステムです。(図1にHZSとの共同プロジェクトの歩みを示す)
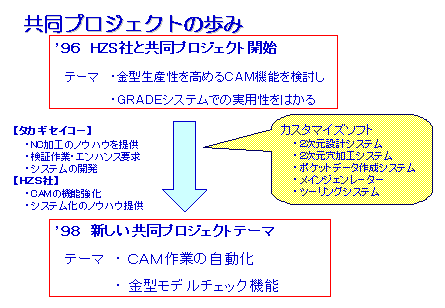
開発背景について
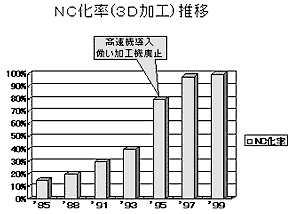
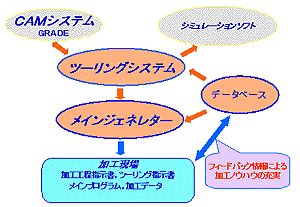
当社は10数年前からCAD/CAM、NC化の取り組みを始めました。その頃の三次元形状の型づくりはモックアップ・モデルを製作し、客先で承認をもらい、倣い加工といった具合に、汎用加工機が中心でした。その後、CAD、CAMのハード・ソフトの進歩と価格低減という時代の流れもあり、CAD/CAMに人、ハード、ソフトを、増強してきました。
完全NC加工による倣い加工からの脱却(図2に3D加工のNC化率を示す)や工作機のATC利用による自動化の推進をはかり、無人自動運転による金型製造を目指しました。
この目的を達成するために、まず行ったことが技術情報のデータベース化、技術情報の一元管理です。このデータベースを利用し、切削条件等(回転数・送り速度)が付加された様々なMC用メインプログラムを自動作成できるシステムを作成しました。
また、更なる3D時代になりCAM工程より出力するデータの質の向上、量の増加が求められ、機械・工具・付属部品(ツーリング)等の知識も必要になり、作業スピードも要求されてきました。そこで、CAM工程が現在行っている「ツーリング選択」「加工方案検討」「シミュレーションソフトへのデータ入力」「ツーリング指示書作成」といった作業を効率よく行い、かつCAM工程の自動化を推進するためにも開発に取り組む必要があったのです。(図3にシステム構成図を示す)
「天成」の標準機能内でのカスタマイズや取引先とのEDI処理等のアドオン開発をお願いして、機能的には、旧システムの仕様を網羅しました。その後、当社でVisualBasic、Access等を利用して各部門の細かな要求に応えるシステムを構築しています。
「天成」はまだまだ新しいパッケージソフトなので、現業部門からはデータの連携・検索、システム操作の快適性などの面で一部不満はでていますが、パッケージソフトということで割り切ってもらっています。
但し、このあたりはバージョンアップ等を経てより使い易いものになっていくものと期待しています。将来性を見込んでの導入なので、じっくりとつき合っていきたいですね。
■利用効果
旧システムにおいては受注明細や売上月報などの帳票は、電算室でプリントアウトし、紙ベースで各部署に配っていました。「天成」を導入して全ての情報がデータベースとして蓄積されていますので、基幹業務システムからの情報を簡単にデータとして、各部門に提供できるようになりました。
Access等から直接参照したり、ExcelやPDF、MAILを活用して社内外への配信に利用し、ペーパレス化を狙っています。従来の機能を移行しただけでも大きなメリットがでていると思います。
以前は、月報・日報を紙ベースで解析し、Excel等で会議資料をまとめたりしていました。マスタやジャーナルが全てデータベース化されていますのでAccess等のツールを用いて「このリムをある期間で売上集計したい」、「得意先別にサイズ別に集計して受注傾向を把握したい」等の要望をクエリにして瞬時に引き出し、Excelに保存するというようなことが可能になり、非常に効率が良くなりました。
データの入力については「天成」クライアントを使用し標準機能で使っていますが、データの閲覧・検索については、社内ネットワークのどのパソコンからでも使用することができます。リモートアクセスで自宅から、モバイルで出張先からでも可能です。
さらに、輸出市販のアルミリムなどは仕様があまりにも多く、旧システムのコード体系では管理できなかったものについても、「天成」に移行することによってコード体系を拡張でき、全ての仕様をコンピュータ管理できるよう改善している途中です。また旧システムの場合は、単価マスタの修正などは1機種づつ入力画面から手入力するしかなく、手間がかかっていました。
この点も「天成」を導入してから、営業部門からExcelでデータとして受け取り、直接データベースにアップデートを掛けることができ、入力ミスも防げるので、マスタメンテナンスの作業効率も上がりました。
■拡張性
蓄積されたデータをいろいろな角度から有効利用することを考えると、「天成」の標準機能だけでカバーできない箇所があります。しかし、Windows上のRDBMSなので、ODBCデータソースとしてあらゆる市販ツールから使用できます。そのためOUTPUTの変更・追加が比較的容易にできます。INPUT・更新系については今のところ「天成」の標準機能を使うしかなく、今後に期待するところです。システムとしていろいろなデータを取り込めるようになってくれれば、拡張性はさらに広がるでしょうね。
システムの概要
■ツーリングシステム
ツーリングシステムは、CAM作業者がNC加工データ作成時に決定していた工具、ホルダー等の組み合わせをデータベースに蓄えられた情報とCAMシステムから出力される3D形状の情報(又は、仮形状機能に数値入力)により、最適なものを選択し、その情報をシミュレーションソフトやアウトプット情報として出力することが可能なCAM支援システムです。
このシステムは、NCデータ作成前のツーリング決定により後戻りのない作業や情報の相互利用による人的ミスが排除できるのが特長です。
■メインジェネレーター
メインジェネレーターは、個々のNCデータを工程順に並べることで"データベース"情報より、様々な工作機にマッチしたデータ形式にし、加工条件等も自動算出したメインプログラムを作成することが可能なCAM支援システムです。このシステムは、加工条件を大きく左右する要因(ツーリング・工具突出し・加工方法・被削材)に応じて、きめ細かい加工条件が自動計算できるのが特長です。
システムの機能
以下に機能の概略を説明します。
■ツーリング候補表示機能
CAM作業者は、モデル形状より加工部壁面高さ抜き勾配・最小R・最大加工高さ・最小加工高さ等を求め、NCデータを作成する前にMC機にて使用するツーリングを仮決定し、NCデータを作成します。この求めた情報と刃先具名・NC機名等を入力することにより、使用可能なツーリング候補を表示することができます。(GRADEの加工評価機能及びその他チェック機能にリンクする予定)(図4に個々の情報を入力する画面を示す)(図5に候補表示した画面を示す)表示順は、以下の情報により決定します。
(1) 刃先具突出長の短い順
(2) 総係数の高い順(条件の高い順)
(3) 部品数の少ない順
(4) 全長の短い順
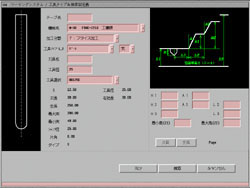
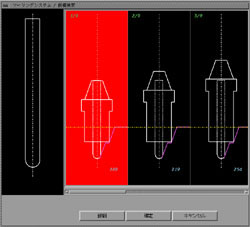
■詳細情報定義パネル
ホルダー名・工具名及び各突出長・ホルダ径・NC機名称等の情報を、このパネルにて表示します。(図6に詳細情報定義パネルの画面を示す。)このパネルでは、可変式ホルダー・刃具突出等の長さを変更可能範囲内(データベースより)で修正することができ、更にNC機によって異なるATC制限に関するチェック等も自動的に行います。
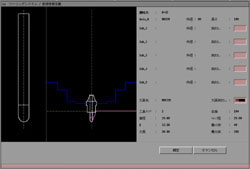
■シミュレーションソフトへのファイル出力
シミュレーションソフトを使用して、干渉チェックする為に必要なファイル等を自動作成します。図7に出力するソフトの選択とワーク形状寸法定義を(ワーク寸法,ワーク位置)行う画面を示す。自動作成するファイルは、工具定義ファイル・設定ファイル・バッチファイルなどで、これにより、面倒だった入力作業をしなくても、シミュレーションソフトを起動し、干渉チェックすることができます。CAM作業者の確認用にツーリング図も出力できます。
![]() |
![]() |
![]() |
■加工機変更機能
変更NC機を選択するだけで変更する前のツーリングを参照しながら、工作機ヘッドに干渉しないツーリングに自動変更します。これにより、加工予定を変更することによって発生する作業時間を短縮することができます。
■切削条件自動計算機能
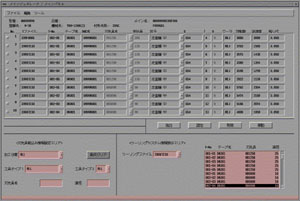
メインジェネレーターにて加工工程順に加工データを入力し、そのデータに使用するツーリング情報や加工区分(等高線荒加工など)等を選択することにより、設定内容を考慮した回転数・送り速度などを自動決定します。(図8に工程入力した状態を示す)
■加工指示書の作成
メインジェネレーターにてCAM工程からMC作業者に加工指示書やツーリング指示書等を出力することが可能です。(図9に加工指示書とツーリング指示書を示す)
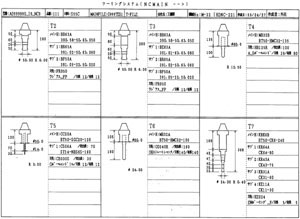
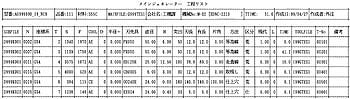
■MC機用メインプログラム自動作成機能
メインジェネレーターにて加工工程順に加工データを入力することにより、T・Dコード、クーラント等を半自動決定し使用するMC機にマッチしたデータ形式のメインプログラムを自動作成することが可能です。作成されたメインプログラムやチェックプログラム・加工データ等は、DNC装置(PC)に自動送信されます。
効果
当社において両システムを作成したことにより、以下の効果がありました。
- MC機の無人加工時間が増加した。作業人員体制は、MC機一台一人体制から多台持ち体制に移行することができた。
- 作業者によって違っていた、切削条件(送り速度・回転数)等の設定も標準化され、経験に左右されなくなった。(中国にあるNCデータ作成会社に両システムを導入し、社内と同様のデータ供給を実現)
- CAM作業者のツーリング選定に関する時間が削減された。
- 情報伝達もれによるポカミスが減少した。
- データベースによる「技術情報」の一元管理が実現できた。(都度のメンテナンス実施中)
今後の取り組みについて
両システムを使用し一年余りになりました。この間、各工程よりいろいろな要望(自社開発のため、どこに出すエンハンスよりも細かい内容)が出され、この要求を実現するため、機能のバージョンアップをはかり、更に使い易いシステムに育てて行こうと考えています。尚、両システムは、外販することを視野に入れて開発を行っており、今後PC版へ移行も検討しています。また、HZSと進めている共同プロジェクト項目にも、ツーリングシステムとGRADEとのリンクに関する項目があり、この開発項目が完全に実現すれば、後戻りのないツーリング選定、指定したツーリングによる加工不可範囲抽出などが可能になり、ツーリング選定時間が、更に短縮される予定です。
「ツーリングシステム」「メインジェネレーター」以外にも3次元設計システムから各プレートの穴情報を出力して貰い、その情報からプレート別の穴加工データを作成する「3次元穴加工システム」や「輪郭加工システム」の開発に取り組んでいます。またツールプリセッターへのデータ出力も含む「工具管理システム」の作成も予定しています。
現在データ作成手順などCAM工程に関する作業をマニュアル化し、使用工具・加工パターンも標準化してありすでに他のCAMシステムを使用して、マニュアルに基づいた加工データを作成しています。今後、GRADEの削り残し機能などが充実すれば、加工工程設計機能を利用しGRADEのみでデータ作成をしたいと考えています。
我々の目標は、MCの無人自動時間の増加・多台持ちの推進とCAM手動時間の低減です。(図10参照)目標に向け、今後も努力を続けていきたいと思っています。
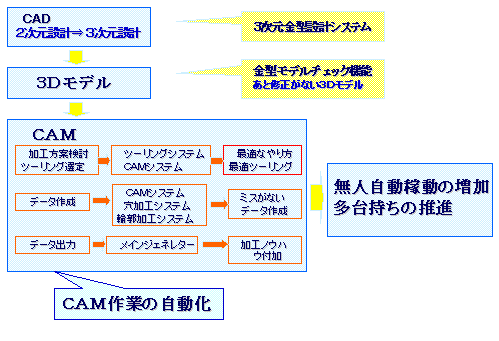
HZSについて
いろいろなことが気楽に相談できるところが、HZSのいいところです。ソフトのことだけでなく、サーバーシステム、DNC送信やパソコンとUNIXを混合して使用するための環境などいろいろなことを相談しています。また、HZSの自社商品だけではなく、トータル的にシステムインテグレートし、ICEMSurf、VERICUTなどいろいろな商品を提案してくれるところも助かっています。
その他、金型業界のことや、技術情報に関わる、セミナー、発表会(某営業所長さんの講演会、いつも楽しみにしています)を適宜に実施していただき、非常に参考になります。尚、今回紹介したシステムが完成したのは、SEの方々の全面的なサポートがあったからだと思っています。今後もHZSの協力を大いに期待しています。
会社プロフィール
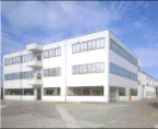
株式会社タカギセイコー
本社 | 富山県高岡市二塚322-3 |
---|---|
資本金 | 15億3,785万4,500円 |
創立 | 昭和15年3月 |
従業員 | 1,467人 |
主な営業品目 | ブラスチック工業部品(2輪車、自動車、OA機器、精密部品、携帯電話) |
金型/ 技術センター |
富山県新湊市川口800 |
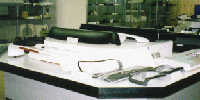
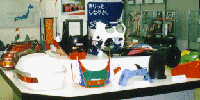