![]() |
東京大学 大学院 工学系研究科 精密機械工学専攻 教授 木村 文彦様 |
---|
東京大学 木村教授は、マン・マシン・システム、コンピュータ・グラフィックス、形状モデリング、CAD/CAMなどをテーマに研究され、製造業の発展にご尽力されています。
また、精密工学会「設計論とCAD」専門委員会委員長、ISO TC184/SC4(STEP)国内対策委員会委員長など、世界を舞台にご活躍されています。
木村教授と懇談会の場を設けさせていただく機会があり、その中で「近未来の製造業のあり方」について大変興味深いお話しを伺いましたので、ご紹介させていただきます。
製造業と情報化
木村 製造業の物造りのあたりからはじめましょうか。製造業では情報化はものすごい勢いで進んでいます。
情報化は非常に重要だというのはみんなが認識していますし、現実にも効果がある。ただ、それが物 造りの中でどのような意味づけを持つかということは別だと思います。
情報化は道具です。レベルが違いますが、かなづちや、のこぎりと同じような道具なので、かなづちや、のこぎりがどんなによくても、それを使う人の技量がないと使えないですよね。今どちらかというと、情報技術というのはそれ独自の技術がありますから、それを使う人を越えてどんどん進みつつあります。特に情報システムにとってのユーザは、設計技術者・生産技術者ですが、情報技術の専門家ではなく、情報技術のレベルはあまり高くありません。
しかし、彼らは設計・製造をするという、非常に専門性の高い技術を持っているんですよね。逆にみると、情報技術者で情報システムを造っている人間は、製造のことを知らないから、物造りに適切なシステムなんかできっこないという話があります。
それで今我々も研究している、製品開発力といいますか、製品開発方法論が重要になります。
物を設計し、製造していくような過程をどういう形で知識化するかが問題です。体系化し、可視化して見えるようにし、記述する。そうすると、それを他の人に伝承することができます。蓄積ができますから、それをベースに次の人は足せますよね。足せると、今よりも増えていく。また増えていく、というようにポジティブな再生産をして知識を増やしていく。このようなベースがあれば情報技術者もある程度までわかる。前の世代で最新だった物が、次の世代になると当たり前になり、誰でもわかるようになります。
製造する技術を知識化する再生産メカニズムというのを作らなければいけません。製造業ではこれが非常に重要なところです。そのような方法論を現実のものとするための道具として情報技術が非常に役に立ちます。
インターネットとか情報ネットワークとか計算機とかの効果を考えたときに、我々が日常やっている専門性のいらないアミューズメントとか日常のショッピングなどは、あっという間にすごい勢いで広がりますよね。情報技術者も日常の活動のユーザですから、こういうところはリーダシップをとってシステムを構築し進めることができます。
ところが、設計とか生産は違いますから、情報技術者が前へ出てそれを進めることはできない側面があります。
情報化が非常に大切だといわれながら、このことがクリティカルな問題としてでてきています。お互いに言葉が通じなくなって、この2つの技術の流れが離れてきてしまっている。
HZS 我々のような会社は物造りの技術と、情報化の技術の間を埋めるということを目指していろいろな活動をしているわけですが、造った物をお客様に持っていっていろいろ使っていただき、ご意見を承ってまた作ってというキャッチボールをしながらシステムを向上させています。
木村 やっていることをはっきりつかむ一番いい手というのは、その人にその道具を使わせることですね。
道具を使ったやりかたをみると、その人が何をやっているかわかる。一回でもいいから使ってもらう。
使うと文句を言う。文句を言えばしめたもので後は直せばいいということです。
HZS 先ほどの知識の蓄積、成長させるメカニズムですね。
リエンジニアリング
木村 製造業で一所懸命やっているのは物を造る技術とかプロセスの文書化です。ISO9000、これから14000もでますが、プロセスを記述する、オペレーションを可視化するということが、今規制からも要求されてきています。
まず、自分たちの言葉で書く。それがある程度までくると、今度はそれを情報処理技術者が見ればある程度わかるようになる。物造りでは今ボトムアップでどんどん情報がたまりつつあります。これは非常にいい方向ですね。
ISO9000でよく言われるのは、やるのは大変だけど効果は即ある。やってみると何でこんなことをやるのかとか、重複しているとか、命令系統が曖昧とか、報告ルートがはっきりしていないとか、問題点がどんどん出てきます。それを再構成すると、まさにリエンジニアリングになります。
人が頭を使って物を造っているところは、なかなか簡単に文書化できないですね。文書化できないところがブラックボックスとして、はっきりするわけです。そうすると次は、そのブラックボックスの中をどうするかということになります。今はそのブラックボックスすらはっきりしていないわけですね。
問題は、製造技術のノウハウが個人の技術とか、これは我が社の財産です、という形で隠れていて、整理できていないことです。だから、その人がやめてしまうとその仕事ができなくなるということになりますね。
頭の中でやっていることを吐き出さざるを得なくなります。それは非常に大変ですが必要なプロセスです。そういうところまで製造技術者が歩み寄れば、情報処理技術者も、そこで話ができてくるわけです。
知識の共有化
木村 中小企業も含めて日本の製造業の強みは随所にあるノウハウだということですが、それで満足していると死んでしまうと思います。いい会社というのはそういいながらもノウハウを次から次へと生み出しているわけです。生み出すということは、前にあったノウハウは既成の技術として当たり前となる。
こういう風にしないと成長しない。
我々が今研究しているものにオントロジーライブラリーがあります。知識の共有化の基礎として、オントロジーデータベースをしっかり作るということで、これは非常に息の長い仕事になりますが、やはりそういうことも含めてやっていくしかないんでしょうね。
基礎的に我々が確実にわかったことは何かということを、計算機の可読なデータにしていく。例えばネットワークを通じて誰もがすぐ使えるようにしておくと確実に再利用できる。
誰もが使える形でデータベース化しておくということに付加価値があるのです。
同じようなことを再生産する必要はありませんし、世界全体の競争を避けるわけです。
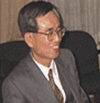
取締役社長 桑木 光信
HZS 私どものCUBEIIのカーネルにACISを使っていますが、ACISのコンセプトは上流のお客様を対象としていますから、我々からすると下流のお客様向けの機能が足らないところがたくさんあり、STIと共同開発しました。この共同開発についてSTIは、「他社と開発した基礎技術がベースとなっており、HZSと共同開発したこの技術もオープンにする。利用できる範囲を地球規模にすると、全体の技術が向上する。」と考えています。
我々もお客様とキャッチボールをしてシステムを向上させています。どういうことに着目して、どのようにブラッシュアップしていけばいいかということは、お客様に教えていただきます。基本的には同じことですね。
木村 製造技術としての知識を体系化する方法論があって、それを実際に使えるようなシステムに転化していくところに情報技術があるわけで、そのあたりに日本の付加価値、日本でなければできないことがあると思います。それが日本の生きる道ではないでしょうか。そういうところをうまく方向づけしていくのが大切ですね。
効率化
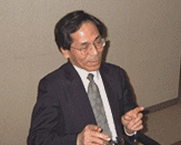
木村 何をやるにしても人が大事ということを言い出したのは、ヨーロッパです。アメリカもちょっと前から言い出しています。物を造るときは特にそうですが、付加価値をつけるということは、人の動機づけ、人が一所懸命考えて知恵を出すことしかないんですね。
一定の手順で仕事をすることは誰でもできる。誰でもできるということは付加価値がつきませんからね。誰もができても儲かるというのは関係するコストの差で儲けるだけです。
日本かヨーロッパみたいなところで何か生き延びていくことをやろうと思うと、非常に単純化した概念ですが頭を使うことしかないですね。
頭を使うための仕組みをどれだけ効率化できるかが、あと我々ができることですね。
製造業も単に空洞化するとか、物を造っても儲からないなどではなくて、製造をするというプロセスの中で、頭を使うことをいかに効率化するかということで、非常に効果が出ます。頭を使うプロセスをどれだけ効率化できるか、そういうツールをどう提供できるかというのが今の勝負ですね。
CAD/CAMがまさにそのようなツールの一つです。情報システムそのものを作る技術は、どう考えてもしばらくはアメリカにはかなわない。ですから、例えばアメリカなどからCAD/CAMの先端技術を持ってきて、膨大な製造知識を背景にして、自ら持っている膨大な製造技術と融合させる。もともと日本の技術者は大変有能ですから、そのようなCAD/CAMを使うとものすごく技術者の知的生産性が上がり、圧倒 的に儲かります。製造業の方向はそれしかないわけですね。
教育
木村 ソフト技術は、アメリカなどに比べて随分遅れており、この差を埋めるのは大変ですね。
これは、政策、教育の問題です。
日本では初等教育がよくありません。日本の初等教育では、クラス単位で整然と物事を進行させるために、人間を集団という枠の中で行動させます。できる子はあまりできない子の面倒を見ることが美徳として教えられる。
この子供の頃からのすり込みがよくありません。
ある一律のメジャーで測ると、できる子できない子がでてきますが、人に合ったメジャーで育てると、どの子も必ずいい面があります。
個人の生産性を上げるためには、得意なことをさせるべきです。
今の教育はゼロサムゲームで、できる子とできない子がいるということは良くないことで、平等化します。
教育は、ウィン・ウィン・シチュエーション(win win situation)であるべきで、この人はこれがいい、あの人はあれがいい、というのが理想の教育です。教育で大事なことは相手がどう考えているかということがわかることです。そうすると、いい教育ができる。
こういうところから改善しないと無理ですね。
日本の教育は社会の摩擦を回避していますが、このようなやりかたは、これからのシステム型の社会の生産率を下げていきます。
Life Cycle Industry
木村 物を造る、活用することを、Life Cycle Industryといっていますが、極端にいうと農業もそうです。
何らかの形で物を変化させていく、それに人工的な付加価値をつけていくというのはみんな製造業と絡んでくると思いますね。物を買ってきてちょっと付加価値を付けて売るというのは、ロジスティックスですから、運搬活動しかなく、これ以上の付加価値を付けるのは非常に難しいですね。
製造業というのはそうではなくて、入ってきたものが変わって出ていきます。変わり方にいくらでも可能性があるわけですから、そこをいくらでも効率化できます。
物を変えていくのは今までのような狭い意味での製造業ではないことは明らかでしょう。
資源浪費型の工業生産をやめてサスティナビリティ -地球持続可能性- といいますが、我々にはこの地球の環境が我々の子供から孫からその先まで、何百年も何万年も持つような形で今の地球のリソースを使っていく責任があります。そういう形にしていくことを考えたときに、今の製造業だけで体系化していくのは非常に難しいわけです。
物 -地球からとってくる資源- をできるだけ無駄に使わないように使い回していく。物を作ったら、リサイクルして使い直す。
今は製造業があって、販売屋さんがあって、修理屋さんがあって、廃品回収屋さんがあってと、別々で能率が悪く全体が最適化されていません。
別のインダストリーとしてやるのではなく、流れ全体を最適化するようなことをはじめから考えて産業構造を設計していくのが、Life Cycle Industryで、我々の研究のひとつです。わかりやすく言い換えると、物は地球にあって有限です。この有限なものを変な形で外に出すと廃棄物になったり、毒性を持ったり、エネルギーとして地球にたまり温暖化したりと、いろいろ悪影響があります。できるだけ物はとらない、とったからには変な形で外に出さないで使いきる。物は循環させる。そこで人間が知恵を加えると、古い材料がいくらでも新しい製品となって出てくる。同じことをやっているように見えますが、物が回りますからふんだんに人間の知恵が入れられて新しいプランとして出てくる。知恵はいくら使っても減らない。無限にある資源というのは知恵なんですね。これから人間が持続可能に生きていくためには、知恵を絞る以外にないですね。石油を取るだけ取って売りきってしまう。木をあるだけ切り取る。ということはだめなわけです。
STEP
木村 STEPも製品データを可視化するということで、我々大学の立場ではSTEPに統一するのはあたりまえだというわけですが、現実には10年かかってもなかなか進みません。今のSTEPのレベルでは情報が細かすぎます。将来的には、これはうんと将来ですが、もう一段高いレベルで標準化を考え直す波がくるでしょうね。来世紀にはそういうふうにならないと、統一インターフェイスというのは難しいと思います。

顧問 山元 洋治郎
HZS STEPのデータが細かすぎるというのは具体的にはどういうことでしょうか。
木村 形状データはNURBSに展開された係数のデータを渡します。曲面データはベジェー、NURBSなどいろいろなものがあり、その数値誤差の整合性を保ちながらデータ支給・変換し、形状の精度を保ちながら加工する。
これでは数値誤差など苦労が多く、しょせん無理ですね。簡単なことはできますが、いろんなことをやろうとすると相互にチューニングする人が必要ですし、N個あればN個のチューニングでいいかというとそうもいかなくて、組み合わせのチューニングが難しい。その問題はなかなか解決できないでしょうね。
しかし、曲面には形状を作ったもともとの条件があります。この条件を渡してやって、同じプロセスを起動して再生する。この方がずっとまともなはずです。
その方がデータ量も少ないですし、デザイナーにとっても曲面を作った意図がはっきりわかりますから間違いないんですね。そういう形にだんだん変わっていく。フィーチャーとかパラメトリック機能は、まさにそれを意図しています。
強力なパラメトリックは単なるバリエーショナルということではなく、パラメータとそれにかかる拘束条件をどういうところまで許すかによって、そのものが持っている機能要求だとか制約条件とかみんなあらわせるわけです。それを両方同じに持っていればデータを再生できますから、その方がずっと安全でローコストですよね。
STEPもパラメトリックインターフェイスなどいろんな角度で発展していくでしょう。
まだ5年、10年ぐらいは、ベンダーが苦労することになるでしょうね。
HZSへの期待
木村 知識の共有化という方向で話が進みましたが、どんな会社でもその会社が持っている一つのバックボーン、この分野では誰にも負けないという、知識の集積をいろんなことをやりながらも作っていくことが大事なのではないでしょうか。それを誰でも使えるような形で素早く提供すれば、非常にいいビジネスとなります。
そういう普及化する共有ベースというのがあって、たたきこむべき付加価値があることです。付加価値のある確立した競争技術は、普通はすぐできないんですね。研究でもよくいいますが、10年、どんなものでも10年我慢してやるとオーソリティーになれるかどうかわかりませんが、コソリティーぐらいにはなれます。
10年集積したことを他人は簡単には追いつけない。
技術開発もいろんなことをやっていくことは大事でしょうけれども、何かこれこれだっていうことを見いだすには、10年やるということでしょうね。そうすると10年やったことは必ず付加価値になります。技術を右から左へと作ることを日々やっていると、結局最後には会社に何も残らなかったということになってしまいます。
HZS CUBEIIは日本で初めてACISを実務レベルの製品にしました。世界でも超有数ではないでしょうか。
さきほど先生が10年とおっしゃいましたが、我々は比較的量産型の部品を作る金型を作るという世界でこういう道具を使っていただいて、約10年経ちました。
製造の金型を作るための道具を作るということに挑戦している会社は比較的少ないと思います。
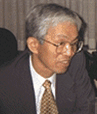
専務 植田 俊
木村 上流は多いですが下流は少ないですね。
HZS 工作機械を使って金型を作る技術は日本が相当優勢ですし、環境の中でシステムを作っていますので、CAMの分野では世界に一番近いところにいると思っております。その利点も活かして、今までの10年の集積をベースに、グローバルに通用するものをお客様にご提供できるよう頑張りたいと考えております。
今日は、大変有益なお話をどうもありがとうございました。