ボデー建付品質向上への取り組み
ダイハツ工業株式会社様は、「We do COMPACT」を企業スローガンに掲げ、コンパクトというメリットを最大限に活かし、21世紀に向けて社会や地球にとって「重荷」にならないクルマを、それでいてさまざまな個性を持ち、夢や満足をたっぷり乗せたスモールカーづくりをめざし、世界140カ国を超える国々に販売・サービス活動のネットワークを広げられています。今回は、公差解析における自動車部品の特徴、VALISYS/Assembly導入の背景、活用事例、効果、今後の課題などを中心に、生技開発部 生技開発室 倉橋務様にお話をお伺いしました。
はじめに
■ボデー建付品質とは
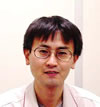
倉橋 務 様
自動車産業も成熟期を迎え、従来の機能中心のモノづくりの考えから、デザイン、ボデー建付といった外観の品質にも重点が置かれるようになってきました。ここでいうボデー建付とは、ドア、ランプなどを見栄え良く組み付けることです。この建付を良くするためには、例えばドアとドアとの隙間寸法、段差寸法の設計を開発初期から精度良く行う必要があります。
現在の課題は、ボデー建付品質の良い車を短期開発するために、設計段階の図面レベル向上を図るということがあります。つまり、開発初期段階でいかに早く、正確に問題解決するかということが重要になってきています。
■公差解析とは
現在のようにユーザの要求レベルが向上してきている一方で、部品には製造上の理由から公差があり、部品を作ると必ずバラツキが発生します。その公差(バラツキ)を持った部品を組み合わせて製品を作ったとき、その完成品が設計目標の品質に達しているかどうかを判断することを公差解析といいます。
簡単な公差解析の例として、次の図のように部品の公差がそれぞれ±1.0mmの場合、2つの部品を組み合わせるとどうなるでしょうか?
この計算方法は『バラツキの統計法則』がベースであり、この場合の寸法バラツキ量は、(±1.0mm)+(±1.0mm)⇒ ±1.4mmとなります。
しかし、これは各部品を平面的に見た場合の計算であって、部品の立体的な傾きを考えた計算ではないという大きな問題があります。
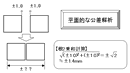
導入の背景
■背景(現状の問題点)
車の部品は、主要部品だけで300~500、細かい部品まで数えると、数千、数万となります。
ここで自動車部品の特徴をまとめると、
- 構成される部品が非常に多い
- デザインなど形状が複雑
- 部品が多く部品の構成が複雑 などです。
従来では簡易的な手計算や従来車種を参考にして公差決定してきましたが、
- 複雑な計算に時間がかかる
- 立体的な計算ができない
- 実車と計算値が合わない
などの理由があり、特に計算精度、時間面では大きな問題を抱えています。
その結果として、現物ができてからのトライ&エラーでの確認が必要となり、開発期間を圧迫することにつながります。
今後は公差解析の高精度化により、これらの問題を解決していく必要があります。
■システム導入の検討
公差解析の高精度化のためには、設計の初期段階より部品の3次元CADデータを活用したコンピュータによる公差解析が有効です。
ただし、この取り組みは弊社で初めての試みのため確認項目を洗い出して事前検証を行いました。
公差解析ソフトは数社ありましたが、実績、将来性、サポートなどを考えてVALISYS/Assembly(バリシス)を候補としました。
導入に先立ち、事前確認として、
- CADデータの互換性に問題はないか?
- 高精度な計算理論を備えているか?
- 実用的にソフトが活用できるか?
などの確認検証を行いました。
ここでは、確認検証により把握できた『高精度な計算理論』と『ソフト活用の流れ』を簡単に紹介します。
■確認項目①(高精度な計算理論)
単純形状、複雑な車両のデータでのトライを通じて、VALISYS/Assemblyには複雑な3次元形状を解析できる高精度な計算理論を備えており、実際の検討に十分適用できると判断しました。
下図は立体的な公差解析のイメージ図です。
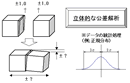
■確認項目②(ソフト活用の流れ)
ソフトを使った公差解析は3段階で行います。
- 条件入力;CADデータに公差~組付方法の設定
- 計算実行;部品の仮想組合せ~統計処理
- 結果表示;バラツキ(OK、NG)、寄与度の判定
計算結果は下図のように判定して対策を行います。
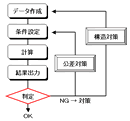
判定結果がNGの場合は、結果をもとに『最も影響がある部位』を特定して、重点的に対策を検討します。
この流れは、実際の検討で対策立案~確認できるサイクルであるため実用的に活用できると判断しました。
■導入への結論
確認検証の結果から、VALISYS/Assemblyは従来の問題を解決できる高精度な理論を備えており、また実際の業務で実用的に活用できると判断して99年3月に1システムを導入しました。
以下では、VALISYS/Assembly導入後、初めての本格適用となった新型車『MAX』の適用事例について紹介します。
ここでは従来から品質要求レベルが厳しい『ヘッドランプ取付け構造』と『新機構インパネシフト』の2つを検討しました。
VALISYS/Assemblyの活用事例
■取り付け構造の対策(ヘッドランプ)
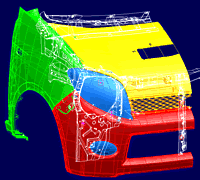
ヘッドランプは、フェンダ、フード、バンパーなどに囲まれた複雑な部位です。特に、MAXのランプはシャープなデザインのため、従来車よりも建付の品質確保が困難であることが懸念されました。
このヘッドランプの取付け構造を決めるにあたり、従来車から何種類かの構造を検討しました。
ここでは2種類の取付け構造の検討を紹介します。
MAXのランプ形状とボデーの基本構造をベースに、それぞれの取付け構造モデルを作成して評価しました。下図はその2種類の構造モデルの模式図です。
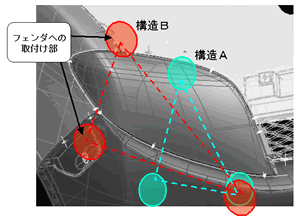
従来から経験的には構造Bの取付け位置バランスが有利とされていました。その理由としては、
- 取付け点のバランス(三角形)が良く、ランプ全体をカバーしている
- ランプ取付け位置がフェンダの近くにある
- フェンダに取付け部があると、ランプはフェンダとの位置関係を保てる
などと考えられていましたが、従来では実際に構造を変更した場合の予測はできませんでした。
今回、VALISYS/Assemblyを使うことで誰でも明確に、定量的に判断できるようになりました。
下のグラフは、最も品質要求が厳しいフェンダとの建付隙(コーナ部)のバラツキ計算結果です。
計算結果より、構造Bを採用すれば、構造Aに対し、約30%のバラツキ低減ができると確認できたので、MAXには品質向上が図れる構造Bを採用しました。
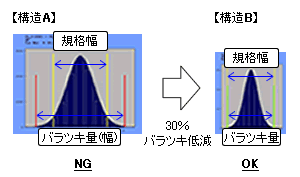
■取り付け構造の対策(新機構インパネシフト)
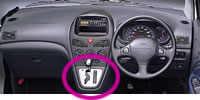
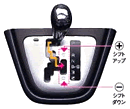
MAXには、新機構として内装のインパネ中央部にマウントされる『内装インパネシフト』を当社で初めて採用しました。
これは新機構であり、複雑な部品構成となるため、開発初期からインパネクラスタとシフトプレートとの建付、干渉不具合の危険性が懸念されていました。
下図は、内装インパネ周辺の部品の構成図です。
- 内装部品の多数のインパネを構成する部品・・①
- 機能部品のシフトプレート部品・・・・・・・②
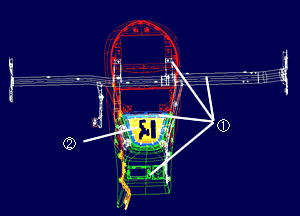
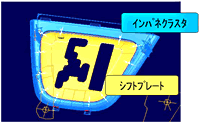
従来の経験にもとづく簡易計算でも、問題の発生が予測できましたが、問題のレベルを定量的に判断することができませんでした。
今回、VALISYS/Assemblyを使って検討した結果、下図のように当初の設計構造ではコーナ部の干渉不具合が発生することが判明しました。これは最悪の場合、干渉して取り付けできないこともあり得る重大不具合です。
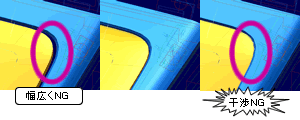
対策として、部品バラツキが発生しても建付見栄えが悪くならないような変更(デザインの一部見直し)を行い、狙いどおり問題解決しました。
このように、問題点の早期発見、早期解決をすることにより、実際に現物ができてからのやり直しロスの低減に結びつけることができました。
効果
- VALISYS/Assemblyを活用することで、従来から課題であった公差解析の高精度化への実用化の目処付けができました。特に、過去に経験がない新機構では不具合の未然防止と対策ができて、大変有効でした。
- 従来の経験に頼った検討に対して、評価の結果を定量的に判断できるようになり公差解析の信頼性が向上しました。
この高精度な公差解析システム(VALISYS/Assembly)を活用することで、ボデー建付品質の良い車を早く開発するための図面レベルの向上に大きく貢献できました。
今後の課題、展開
■適用部位の拡大
従来のランプ、ドアに加え、新機構を中心に適用部位の拡大を現在進めています。更に部品モジュール化等、過去に経験したことのない新構造に適用拡大して成果をあげていきたいと考えています。
■解析精度の向上
今後の課題としては、更なる解析精度の向上です。
これだけ綿密に検討しても、最後は現物にて確認しなければならない部分が残ります。VALISYS/Assemblyによる剛体シミュレーションでは精度良く検討できないケース、例えばバンパーのような軟らかモノのたわみ、なじみによる精度変化の予測はできません。これは難しい課題ですが、部品の変形を考慮したバラツキ解析に挑戦し、更にレベルアップしていきたいと考えています。
HZSについて
今回、VALISYS/Assemblyを使いこなすためにHZSのエンジニアの方にアドバイスをいただきながら実用化にたどり着くことができました。今後の新しい取り組みに向けても、より一層、強力なサポートをお願いしたいと思います。
おわりに
公差解析への情熱、技術力や製品に対する自信をとても強く感じました。普段何気なく見ている『ドア建付の隙間』という部分に、これほど深い意味があるというお話は大変勉強になりました。
大変お忙しいところ、貴重な時間をさいてお話を聞かせていただき、ありがとうございました。この場を借りてお礼申し上げます。
会社プロフィール
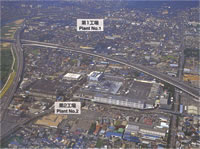
・本社(池田工場)
ダイハツ工業株式会社
本社 | 大阪府池田市ダイハツ町1-1 |
---|---|
創業 | 明治40年(1907年)3月1日 |
資本金 | 284億円(2001年3月31日現在) |
従業員 | 11,427名(2001年4月1日現在) |
売上げ高 | 8,695億円(2001年3月期 単独) |
事業内容 | 軽自動車、小型自動車の開発、製造、販売 |
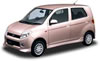
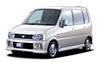
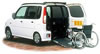
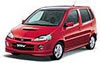