日立金属株式会社様は、高級金属製品、電子情報部品、自動車用高級鋳物部品、設備・建築部材などを主にビジネス展開されている総合材料・部品のトップメーカです。
今回お伺いした素材研究所では、材料開発・機能設計・CAEを核とした新製品/新技術の研究・開発活動を主に行われています。
今回は、砂型用レーザー焼結システム (EOSINT-S)を使った試作品製作を中心に、製品開発室 主任研究員 原雅徳様、研究員 吉沢亮様、松尾進一郎様にお話をお伺いしました。
事業概要
当社は、特殊鋼/ロール/情報部品/磁材/自動車機器/配管機器/環境システムの7つのカンパニーから構成されています。
ここ素材研究所は「自動車機器カンパニー」に所属し、自動車関連の鋳造部品の生産に伴う新素材や評価などの研究・開発を行っています。
また製品開発室では、車体軽量化などの環境対策に貢献する排気系部品や足回り・車体部品の研究・開発と、これら部品開発の短納期化のニーズに応えるための技術開発として、材料および製造技術、CAE、製品評価まで手がけています。
RP(Rapid Prototyping)もその一つです。
工場は、九州工場(鋳鉄・鋳鋼)、真岡工場(鋳鉄・アルミ)、熊谷軽合金工場(アルミ)の3つです。
主力製品はエギゾーストマニホールドやタービン用のハウジング、サスペンション部品、アルミホイールなどを手がけています。
導入の背景
当初、粉体を使用したバインダーで積層していく石膏を使ったRPシステムを導入していました。
造形物はそのまま模型になりますので、木型の代わりとして使用していました。
ですが、木型よりも強度に劣りますし、取り扱いやスピード面で問題がありました。
2000年頃からEOSINTの存在は知っていました。
展示会などで拝見していましたし、お話を伺い始めたのもその頃です。
導入を検討する際に価格や木型に比べて効率的かどうかなど検討を重ねました。
また、直接EOS社でお話を伺うために、ヨーロッパへ行き、欧州での活用状況について色々と調査を行いました。
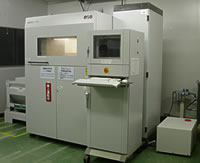
その結果、EOSINT-Sはエンジンのヘッドやブロックの開発を見込んで開発されていることもあり、エギゾーストマニホールドなどもほぼワークサイズ内に収まり、当社の要求を満たすものでした。
また、自動車開発期間の短縮化が進んでいく中で、スピードアップを図るためにも導入に踏み切りました。
2002年8月に導入し、9月から試験運用を行いました。
導入から立ち上げ
導入当初は実際にやってみないと分からない部分が色々とあり、苦労しました。
それから2ヶ月ぐらいはレーザの条件や、ポストキュアの条件、歪み量など色々と試行錯誤しながら解決していきました。
以前から石膏を使ったRPを使用し、「積層法」という手法に関しての経験があったことが活きていると思います。
寸法精度の問題は早めにクリアできましたが、細かいツメの部分で時間がかかりました。
HZSが国内ですでに数社の導入実績があったこともあり、立ち上げ作業も想像していたよりスムーズにいきました。
導入の効果
従来はデータを加工して鋳型を作るまでに2週間程度かかっていましたが、今では最短で1週間以内で対応できるようになりました。
スピードアップが一番体感できる効果です。
造形可能な数量に関しては限りがありますが、少ない個数でのオーダーも数多くあるので効果があります。
また、積層法ですので、アンダーカットや従来法では不可能な形状も造形できます。
従来は分割して組み立てていた中子形状もEOSINTでは一体で造形できることも非常に大きなメリットです。
また、設計変更時のデータ修正に関しても金型をおこす場合の工数と比較すると少なく、スピードアップにつながっています。
造形を夜間に無人で行うことができるので、昼間には別作業ができ、時間の節約につながっていると思います。
EOSINTは自動車開発において、最初のプロトタイプを作る部分に威力を発揮していると思います。
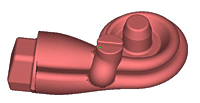
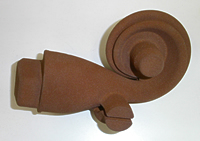
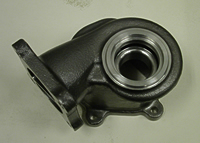
運用について
【設計から評価まで】
オーダーが入ってきた後にこちらで量産に適した形状に再設計しています。
タービンなどであれば耐熱性を考慮した材質・形状も提案します。
コストと納期に見合った手法(EOSINT/従来の工法)で試作品を製作し、この研究所で耐熱性の実験・評価を行います。
お客様からの図面どおりに製造していくだけではなく、要求された仕様に合わせて強度を出すような形状を設計し、試作・実験・評価しています。
形状を造るだけでなく評価まで行っていますので、「評価をするための試作品をいかに早く作るか」が鍵です。
我々は何処にでも作れる品物を追い求めているわけではなく、高級鋳物といった部分を狙っています。
そこまで追求するために研究所があり、各工場で設計・開発を行える体制を整えていることが、当社の特徴であると思います。
【運用時の配慮】
仕上げの工程でハンドリングするためにバーナーで焼き付けを行う工程が大変です。
どの状態が一番良いのかコツのようなものが完全には把握できていませんし、作業者の感性に頼っている部分が大きいです。
この工程は個人差が出る部分だと思います。
また、砂落としの工程では造形物の形状をイメージしながら作業しています。形状を認識して作業をしないと壊してしまう場合もあります。
形状の大まかな箇所は思い切って払いますし、複雑になっている部分では慎重にエアーを吹きかけながら除去しています。
ノウハウの構築
【設計】
どのような設計をすれば最終形状で寸法精度が良く、強度が保てるのかという「鋳型の設計」が最大のノウハウだと思っています。
従来工法と言われる木型や金型とはデータの取り扱いも違いますので、これまでとは違った技術が必要になります。
【造形】
これまでの鋳物生産の経験から、砂が鋳造品の品質に与える影響も大きいと考えていますので、鋳造品の形状、材質などを考えて、最適な砂を選定しています。
また、それに伴ってレーザのパラメータなども変わってきます。
教育段階で、「砂に適したレーザパラメータの考え方」についてのレクチャーがあり、それが役に立ちました。
砂を変更しても、適切なパラメータ値を見つけることができ、早く対応できました。
短納期試作開発システムの構築
IDIS(Integrated Design-In System)[統合デザイン・イン・システム]により開発期間の大幅な短縮化を図りました。
自動車メーカ採用の主要な3次元CADソフトを導入し、日米欧間のネットワークを構築しています。
これにより顧客とデータ通信をダイレクトにできますし、設計や型製作で活用できます。
また、RPを利用したデザインレビュー、CADデータを利用した強度設計、足廻り部品であれば構造解析、鋳物であれば湯流れ・凝固などの鋳造関連の解析を行い、RP造形モデルなどを活用し模型や鋳型を迅速に製作します。
今後の取り組み
導入から日が浅いこともあり、宣伝が行き渡っていない部分もありますので、上手く情報配信していくことも今後の課題です。
導入してまだ5ヶ月ですが、社内外からの鋳型製作の要求量も徐々に増えてきて、稼働率もかなり高くなってきました。しかし、まだまだ上げられると思っています。
今後も多様化し短納期化していくお客様のニーズに応えていきたいと思っています。
さらなるスピードアップと精度の向上、人の手で行う作業の改善・効率化が今後の課題です。
HZSについて
今後もさらにスピードアップにつながるようなバージョンアップ、ワークサイズの拡張を期待しています。
また、砂などの材料の価格面でもう少し努力してもらいたいと思います。
教育に際しても丁寧に指導して頂いていますし、問題がおきた際も対応が早く、技術的にもサポートしてもらっていますので満足しています。
おわりに
最近は、色々な自動車メーカが次々に新型車を発表しているのをよく目にします。お話を伺っている中で、そういった開発作業の中で様々な技術が使われ、あらゆる取り組みや努力があることが良く分かりました。
大変お忙しいところ、貴重な時間をさいてお話を聞かせていただき、ありがとうございました。この場を借りてお礼申し上げます。
会社プロフィール
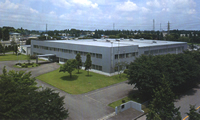
日立金属株式会社
住所 | 東京都港区芝浦一丁目2番1号(シーバンスN館) 東京都新宿区西新宿三丁目7番1号(新宿パークタワー) |
---|---|
設立 | 1956年(昭和31年)4月10日 |
資本金 | 262億8355万円(2002年3月末現在) |
従事者 | 6,144名(2002年3月末現在) |
売上高 | 2,367億円(2002年3月期) |
事業内容 | 高級金属製品、電子・情報部品、 自動車用高級鋳物部品、設備・建築部材の製造と販売、サービス他 |
素材研究所 | |
住所 | 栃木県真岡市鬼怒ヶ丘11番地 |
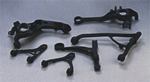
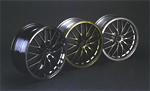
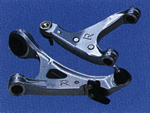
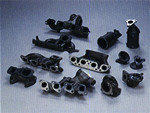