樫山金型工業株式会社様は、長野県の佐久平に拠点を置き、国内のみならず、海外事業も展開されているエムケー樫山グループの会社です。
早くからRP(Rapid Prototyping)に目を向けられ、長い間培ってきた独自のノウハウを元に造形機をフルに活用され、広い分野で高い評価を受けられています。
今回は、EOSINT-Mの導入をされた背景と運用などについて、取締役 樫山剛士様、技術部 部長 丸山和生様、RP係 佐野浩二様にお話をお伺いしました。
事業概要
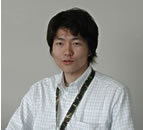
樫山 剛士 様
当社は、プラスチック用金型・プレス金型用の量産型製作を主とした金型メーカです。
最近では主に携帯電話などの情報通信機器、AV関連用の金型製作を行っております。
導入の背景
以前から試作の要望もありましたし、業務の幅を広げるために試作に着手することを検討するようになりました。
当時、光造形機はいくつかありましたが、すで出回っている機械を導入しても後発になりますし、まだ技術的にも未完成で業務として成り立たせることが難しいであろうと考えていました。
その後、継続して造形機関連の動向をチェックしている中で、ドイツでメタルを焼結するタイプの造形機(EOSINT-M)が開発されているという情報を耳にしまして、社長自ら視察に赴き、実際に目で確かめてきました。
「金型を直接造形可能」
「金型メーカの技量がないと立ち上げ困難」
この2点で他社との差別化が図れるであろうということで1998年5月にEOSINT-M250を導入しました。
RPという未知の分野でしたし、当時EOSINT-Mの機械自体も少なかったので、立ち上げに時間がかかることは承知の上でした。
導入から立ち上げ
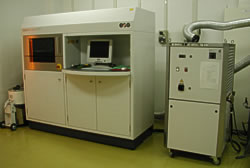
導入から半年はほとんど実験やサンプル製作を繰り返していましたが、それ以降は徐々に仕事が入ってくるようになりました。
導入当初は造形が安定せず、パウダーが上手く撒けていなかったり、造形後にプレートとの剥がれが生じたりしていました。
様々な問題があり、レーザパラメータの変更など試行錯誤を繰り返していく中でコツが掴めるようになり、運用に繋げていけるようになりました。
その後マシンのバージョンアップやパウダーの改良などもあり、2001年11月にはDirectSteel20(スチール20μ)の造形ができる最新のEOSINT M250 Xtendedに入れ替えることにより、仕事量も増えて成果も上がっています。
最近では仕事の幅も広がりつつあり、お客様にも評価して頂いていますので、長い間続けてきて良かったと実感しています。
導入の効果
【営業ツールとして】
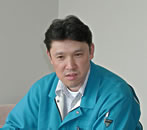
部長 丸山 和生 様
EOSINTを導入後は今までにはなかった自動車関連の試作の受注が増えています。
試作のお付き合いから量産金型に繋がり、現在もお付き合いが続いてるお客様もあります。
EOSINT-Mは分野を選びませんし、まだ珍しい機械ですので、人の目を引きます。
そういった意味では単に造形機としてだけではなく、「新規分野の顧客を開拓する良い営業ツール」にもなっていると思います。
【サイクルタイムの短縮】
EOSINT-Mでは形状の自由度が非常に高いので、水穴を楕円形状にしたり、リブの深い形状部分に螺旋状の冷却回路を入れ込むことが可能で、従来よりも冷却効率を高めた金型の製作が可能です。
従来工法の金型では冷却タイムが50秒かかっていたものを、螺旋状の冷却回路を組み込んだ造形型では半分以下の冷却タイムに縮めても、以前より製品精度が上がったという実績もあります。
サイクルタイムの短縮はEOSINTを使った型のメリットのひとつであると言えます。
【付加価値をつける】
現在、試作メーカであれば1週間程度で試作型を製作しますし、スピードの面では大差はなくなってきています。
一般の試作型に比べてEOSINTで製作する金型は試作型といっても「限りなく量産型に近い」という違いがあります。
しかし、お客様からすれば、従来工法であってもRPを使用していても関係ありませんし、今までのように「納期が早い・精度が良い」だけでは評価されにくくなってきています。
コスト面でも競争が厳しくなっていく中で、付加価値をつけることで差別化を図り、競争力を保てるのではと考えています。
お客様にとってEOSINT-Mはまだまだメリットの出せるポテンシャルを持っていると思います。
運用について
【パウダー】
当初50μずつ積層していたものが20μになったので、造形時間は長くなりますが、精度は飛躍的に向上し、仕上がりも非常に綺麗になりました。
また、DirectSteelはDirectMetalに比べ焼結時に熱量を必要とするので造形時間が長くなりますが、密度が高くなるという利点があります。
表面は磨きを行うと差がはっきり出ますし、成形品にも大きく影響します。
試作品でも品質が要求されますので、少しでも量産品質に近づけるためにはDirectSteel20の表面粗度が必要になります。
機構部品にはガラス入り樹脂の使用も多く、射出成形時の摩耗を抑えるには硬度が必要になります。
硬度の面でもDirectSteelが有利ですし、お客様から「鉄の粉末」とのご要望がある場合もあります。
特にベンチマークの場合はDirectSteel20を使う場合が多いです。
現在はDirectMetal50・DirectMetal20・DirectSteel20の3種類のパウダーを使い分けていますが、DirectSteel20を使用する割合が多いです。
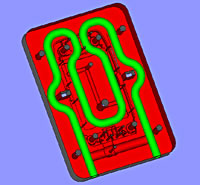
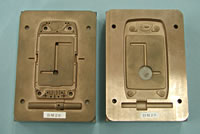
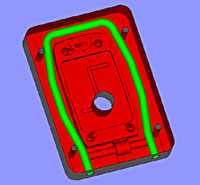
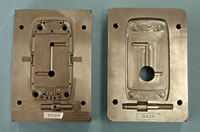
【独自のノウハウ】
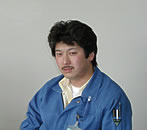
佐野 浩二 様
最近は金属部品造形の依頼が多くなってきていますので、サポートのつけ方などを研究しています。
ブロンズの場合はサポートを手で簡単に除去できました。
しかし、鉄の場合は若干ストレスも大きくなっているので、サポートの配置や形状・強度に気を配っています。
サポートは基本的に網目形状ですが、製品に接する部分は先の細い歯形形状にするなどして除去しやすいように工夫しています。
造形物の形状が違うとサポートも変わってきますので単純に流用することはできません。
また、サポートは製品に食い込ませて付けますが、食い込み量を間違うと除去する時に製品部分が取れてしまう場合もあります。
精密な物では、造形時の製品の向きやリコーティングの速度を変更して対応しています。
数をこなして経験を積んでいく中で「造形の勘どころ」のようなものを掴めるようになりました。
その中で当社独自のノウハウも構築していくことができたと思っています。
今では形状や大きさに関係なく、失敗することはほとんどなくなり、肉厚の非常に薄い部品でも造形可能になりました。
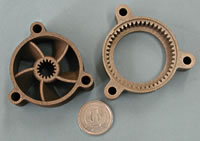
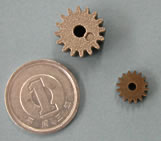
【後処理】
DirectMetal50のパウダーを使用していた頃にネックになっていたのはエポキシの含浸でした。
造形後のポーラスが多かったので、隙間を埋めて表面を綺麗に仕上げるためには必要な作業でした。
しかし、含浸量が少ないと効果が出ませんし、多すぎると仕上げの工程で苦労するので、ちょうど良い量を見極めるのに苦労しました。
試験を繰り返して含浸量を割り出す計算式を作成したり、含浸前に造形物を充分暖めた方が良いなどの解決策も見つけることができました。
また、DirectSteelでは含浸処理がありませんので、そのような問題は無くなりました。
今後の課題
これからは切削加工や従来工法では実現できない「RP造形機特有の強み」を上手く利用することに力を注いでいきたいと考えています。
また、EOSINTは様々な分野に応用可能ですので、隠れているニーズを掘り起こして新規分野を開拓していくことも今後の目標です。
スピード面でも今以上に向上していけば、量産金型へも繋がっていくと思います。
当社では焼き入れの金型が中心になっていますので、すぐには量産に応用できないと思いますが、当社はこのシステムだけで試作型を製作しようとは考えていませんし、量産工程だけで金型を作り上げようとも考えていません。
現在の設備をフル活用して、思いもよらないような提案をしていくことが必要なのではと考えています。
HZSについて
HZSには様々なベンチマークの仕事を紹介して頂いていますので感謝しています。
海外に比べ、日本のEOSINTユーザが一番クオリティを求めていると思いますし、要望も多いと思います。
そのあたりをHZSで考慮してEOS社へ届けて頂ければと思います。
金型としての競争力を上げるためにも、造形時間の半減を目標にして頂きたいです。
また、EOS社とのコミュニケーションをこまめに取って頂き、情報交換の窓口機能を今以上に強めて頂きたいと思います。
当社だけではなく、他のEOSINTユーザの意向を反映した日本仕様のEOSINT開発もできればお願いしたいと思います。
おわりに
お話を伺っている中で、普段何気なく使用している携帯電話などの金型にRPという技術が使われていることが分かり、大変勉強になりました。
大変お忙しいところ、貴重な時間をさいてお話を聞かせていただき、ありがとうございました。この場を借りてお礼申し上げます。
会社プロフィール
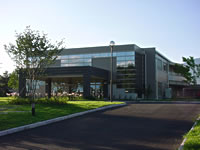
樫山金型工業株式会社
本社 | 長野県佐久市大字小田井1119 |
---|---|
創立 | 昭和53年1月 |
資本金 | 7,305万円 |
従業者 | 97名 |
売上高 | 20億円(平成15年度見込) |
事業内容 | プラスチック成形品、プレス加工品並びに精密金型 自動・省力機器の設計、製作販売 |
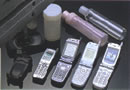
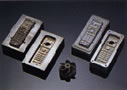
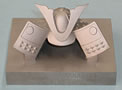
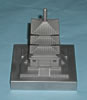