MPM(生産プロセスマネージメント)の考え方と活用事例
システムソリューション統括部 ROBCAD営業グループ グループマネージャー 櫻田 祐二 |
デジタルプロセス変革の課題
大競争時代の車づくりでは、世界最適調達やモジュール化、プラットホーム共有化など、系列や国境を越えたコラボレーションによるアジャイル(俊敏な)マニファクチャリングへと変化しています。こうした変化に対応するには、開発から生産まで世界的な分散、協調体制の中で、製品情報および生産工程情報を一元管理・共有できる環境を実現することが第一の課題です。
表1に、生産技術のデジタルプロセス変革の今日的な課題をまとめました。これらの課題解決のためには、3次元化だけに留まらないデジタルプロセスの更なる進化が必要です。
生産業技術のデジタルプロセス変革のカギを握るMPM
【製品ライフサイクルマネジメントに必要不可欠なMPM】
これまでのデジタルプロセス進展の潮流には、大きく二つの体系がありました。一つは、製品開発・生産準備のエンジニアリング支援を目的としたC4P(CAD/CAM/CAE/CATおよびPDM)、もう一つは、受発注、資材調達、生産計画など生販管理のルーチンワーク支援を目的としたSCMやERPです。
これらを統合・連携して企画から、設計、生産、販売、保守まで製品のライフサイクルにわたりコラボレーティブな企業活動を支援・管理しようとするのが、最近よく耳にするPLM(製品ライフサイクルマネジメント)です。しかし、従来の二つのフレームワークを単に統合するだけでは、基幹業務としての開発・生産プロセスはクローズできません。なぜならC4PやERPの延長では、生産工程をモデル化して生産前に最適に制御する仕組みが欠落していることが最大の理由です。
つまり、設計と生産の間を繋ぐ生産技術のプロセス、言い換えれば、生産設計や生産工程設計を、開発や生産とコラボレーティブに実行できるフレームワークとして組み込む必要があります。
その切り札が、MPMです。MPMは、生産工程を計画、設計、検証、管理、活用する概念です。製造業の開発・生産プロセスにおけるMPMの位置付けは、図1のとおりです。PDMはWhat?「どんな製品か」を管理するものであり、MPMは、How?「いかに安く早く品質良く生産するか」を管理します。SCMやERPはWhen/Where?「いつ、どの工場(工程)か」を管理します。このようにMPMは、生産技術のデジタルプロセスの中核であり、かつPLMのサブセットとして必要不可欠なフレームワークです。
【生産工程モデルの構築】
生産工程モデルとは、生産工程をコンピュータ上に表現するデータモデルのことです。生産技術の一貫したデジタルプロセスを実現するため、あるいは、バーチャルマニファクチャリングを実現するためには、まず、生産工程をコンピュータで扱えるようモデル化("e-BOP:electronic bill of processes"を構築)する必要があります。
この生産工程モデルe-BOPは、図2に示すように生産に必要な3つの基本オブジェクトである、オペレーション(工程、作業)、プロダクト(製品、部品)、リソース(設備、治工具、作業者)を互いに関連付けて、生産工程としてモデル化します。これらのオブジェクトは互いに連想性を持ち、それぞれ生産工程の論理的な階層関係を持ちます。例えばリソースには、ライン-サブライン-作業ステーションなどの各階層があり、それに対してプロダクトには、完成製品-サブアセンブリ(半完成品)-部品という階層を関連づけることができます。
このように、e-BOPではプロダクトのツリーとして、組立て順ツリーや中間加工製品ツリーを併せ持つことができます。製品構成を管理するPDMでは、一般に部品間の親子関係は持っているが、組立て順や加工順を伴う中間製品状態を表現していないため、生産工程としての扱いには無理があります。製品設計は完成品がアウトプットであるのに対し、生産技術は粗材から完成品に至る過程(プロセス)がアウトプットであるためです。
e-BOPで一元管理された生産工程情報は、図3に示すように、階層ツリー、3次元、属性テーブル、PERT図など多様な方法でアクセスできます。
【MPMソリューションの構成】
MPMソリューションは、生産工程モデルであるe-BOPを中核として、工程計画ツール、ロボットや人間の作業を詳細に検討する各種エンジニアリングツール、およびWebベースのコラボレーションツールなど、現在20種類以上のアプリケーションから構成されています。さらに、カスタマイズや既存システムとの連携を容易にするオープンなAPI(アプリケーションプログラムインタフェース)が用意されており、これらを、対象とする領域や目的に応じて最適な組み合わせで導入することができます。
これらのアプリケーションでは、e-BOPで管理される生産工程情報を共有してシームレスな情報連携が可能となります。また、コラボレーションツールによって、地理的に離れた部門間でもe-BOPの内容をWeb上で閲覧したり、データを取り出したりすることが可能となります。こうして、社内外を問わず情報の再入力や重複を減らし効率の良いコラボレーションが可能となります。
MPMは、加工、組立て、検査、物流など、多様な生産プロセスに適用することが可能です。
車体組立て工程計画へのMPM活用例
図4に、MPMを活用した車体組立て工程設計業務の一例を示します。
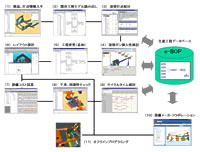
(上図をクリックすると拡大図が表示されます)
この例では、製品の仕様変更を受けて既存ラインを改造して設備対応する場合を想定しています。次のような手順でMPMを活用することができます。
(1) 製品、打点情報入手
製品設計CADまたはPDMなどから製品情報を入手します。打点情報や部品の材質、板厚などの属性情報は、XMLやCSV形式で取り込みます。製品情報を取り込むと、e-BOP内にプロダクトツリーと打点データベースが自動作成されます。
(2) 既存工程モデルの読み出し
仕様変更された部品が影響する工程を、変更管理機能によって簡単に検索できます。改造が必要な既存工程の情報をe-BOPから取り出し、3次元ワークセルモデル(ロボット、ガン、設備、打点情報)とその属性情報を流用します。プロダクトツリーから、組み付ける部品を指示して、改造する工程に割り付けます。
(3) 溶接打点配分
工程に割り付けられた部品に従い、その工程で溶接可能な打点が自動配分されます。図5に示すように打点毎の溶接条件属性値により、その工程での全打点時間がタクト内に収まるか否かを概算できます。また、既存のガンが使えない場合は、ライブラリから別のガンを検索して割り付けることが可能です。一車種数千点になる打点を一元管理できるため、各打点の溶接工程や配分モレの有無を、全工程を通して素早く確認できます。

(上図をクリックすると拡大図が表示されます)
(4) 溶接ガン挿入性検討
打点位置での断面を自動作成して、選択したガンと部品が溶接時に干渉しないかチェックできます。
(5) 工程変更(追加)
部品の設計変更により、既存工程では溶接作業時間がタクトオーバーする場合、工程を追加します。PERT図やツリー上で、新たな作業工程を簡単に追加できます。(3)項の作業によって打点移管を行うと、変更した打点や使用するガン、打点時間などの情報が更新されます。
(6) レイアウト設計
標準ライブラリからロボットや架台を選択して、2次元スケッチでラフレイアウトを作成できます。設備配置情報をもとに、3次元のワークセルモデルが自動作成されます。治具など外部から取り込んだ専用設備のモデルは、ワークセルモデルに直接配置します。
(7) 設備コスト試算
追加した工程の設備情報が自動的にe-BOPに反映され、コスト属性情報から設備投資額を自動的に積算できます。目標投資額を初期設定しておけば、目標に対する達成度を随時確認できます。
(8) 干渉チェック、ロボット到達性チェック
ロボットの到達性やガン、治具、部品との動的な干渉チェックを行いながら、最適なロボットの配置、詳細なサイクルタイムの算出を行います。従来のロボットシミュレーションと同様の作業ですが、MPMではe-BOPで一元管理された打点情報およびワークセルモデルを直接利用できるため、対象工程毎のデータ収集の手間が削減されます。
最適化されたロボットの配置やサイクルタイム情報がe-BOPに格納されます。
(9) サイクルタイム検討
個々の工程のサイクルタイムからガントチャートを自動作成して、工程間の負荷の平準化検討ができます。
(10) 設備メーカによる設備設計(企業間コラボレーション)
図6に示すように、コラボレーションツールによって、遠隔地にある設備メーカへe-BOPの中から設備発注範囲の工程情報を開示して、同時に同じ画面を見ながら技術検討を行ったり、任意に閲覧を行ったりすることができます。こうして、工程設計と設備手配を同時並行して効率良く進めることができます。
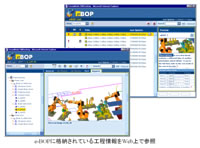
(上図をクリックすると拡大図が表示されます)
(11) オフラインプログラミング
詳細検討完了後、最終的なロボットプログラムを実機にダウンロードして、オフラインプログラミングを実施します。
実際の工程設計では、例えば新製品に対してライン新設、海外へ既存のラインを流用移転などさまざまなケースがありますが、常にe-BOPに工程全体の情報が一元管理されており、目的に応じて必要な業務を柔軟に遂行することが可能です。
まとめ
MPMによって、従来の枠組みだけでは不十分であった生産工程情報の一元管理と共有化が可能になり、コラボレーションによる俊敏で柔軟な生産対応が促進されます。さらに、顧客の求める製品の機能性、品質を向上させ、製造原価を低減させ、短納期化できるモノづくりの実力である「生産技術ノウハウ」の蓄積、共有、再利用という知的創造プロセスによって、競争力向上がもたらされます。
MPMは、これからの製品ライフサイクルマネジメントに必要不可欠なフレームワークです。