プロフィール
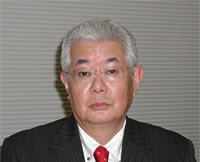
取締役会長
岡田 吉誼 様
岡田 吉誼 会長プロフィール
1942年 | 兵庫県生まれ |
---|---|
1964年 | 東洋工業株式会社(現マツダ)に入社 |
1990年 | 第1情報システム部部長として、R&Dのシステム化を推進 |
1994年 | 開発期間短縮プロジェクトに参画 |
1996年 | MDIプロジェクトに参画 |
2000年 | 経営革新プロジェクト室主席として、MDIプロジェクトを推進 |
2002年 | マツダ株式会社 定年退職 |
現在
日本テクノマティックス株式会社 取締役会長 | |
PLM コンサルタント | 技術士(情報工学 第12559 号) 日本機械学会フェロー |
株式会社東大総研 | 理事 |
日本電気株式会社 | 自動車業ソリューション事業部 PLM コンサルタント |
マツダを定年退職された後も、日本の自動車業界におけるデジタル化推進のエキスパートとして、PLMコンサルタント、講演など、ご活躍されています。
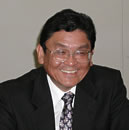
福武 映憲
福武 岡田会長は、MazdaのMDI(Mazda Digital Innovation)を推進してこられ、現在、テクノマティックスの会長をなさっています。今後、自動車を中心としたものづくりの中で、デジタルデータがどのように使われていくのか、ものづくりに携わる会社は何を考えなければいけないのかなどについてお伺いしたいと思います。
日本の自動車会社さんでデジタルデータを使ってものづくりを最初に実践されたのが、マツダさんのMDIだと思います。MDIを推進してこられた岡田会長に、まずは、MDIに至る経緯をお話いただけますか。
ITとの出会い
岡田 マツダに入社したのは1964年ですから、かれこれ40年になります。当初は、CADや金型に関わるつもりはなかったのです。たまたま、先輩から、ボーイングのファーガソンが書いた曲線・曲面の理論の論文をもらい、最初は興味がなかったのですが、論文を読んで、しなる定規のプログラムを作成しました。
当時、マツダには、呉造船出身の人がいて、しなる定規を使いながら、車の原寸の図面を書いていました。物好きな人が2人いて、新入社員の私が作ったコンピュータの定規を使いだしたのです。それが発端で、CADや今日いうところのPLMに関わる仕事に携わってきました。縁とは不思議なもので現図場にいた2人とは、それ以降も長い付き合いをすることになりました。
当時は、マサチューセッツ工科大学(MIT)で考案されたNC用言語のAPT(Automatically Programmed Tool)が流行しておりまして、先ずNCをやることになりました。先のファーガソンの曲面を応用して、車のオイル注入口の上部に開閉するフィラリッドの一部数cm四方を曲面加工しました。そうしたら、当時検査の神様のような人が来て、削った表面を触って、これはいけるかもしれないと。生産技術の専務に、社外に口外してはいけないと言われたことを覚えています。
数cm四方のパッチの切削からスタートして30年後には、車のサイドパネルを全部削って、しかも磨きレスで、即仕上がります。非常に懐かしいというか、隔世の感があります。
いずれにしても、ずっとやっていたのが、点列を取ったり、点列を通る線を作ったり、線と線をまたぐ曲面を作ったり、それに法線を立てたり、空間の点の制御を40年間、定年になってもまだやっています。
クリティカルパスの解決
岡田 自動車の各社がパネルの金型に取組んだのは、自動車の開発期間の中のクリティカルパスが、ボディーの設計と、ボディーのパネルの金型製作だったからです。これを解決すれば開発期間を短縮できます。これはITが直接的にものづくりに貢献した極めて典型的な例だと考えています。時代が進んで次のクリティカルパスは、安全やNVHに変わってゆきます。クリティカルパスを次から次に解決していくことによって、開発期間が更に短縮できます。そうすると、次にくるクリティカルパスは何かと予測することが、将来に向けてのひとつの手だと思います。車の中には、2桁のオーダー(70~100)のコンピュータが入っています。高度の機能の車を想定すると、コンピュータの組込み回路の設計が、将来クリティカルパスになる可能性があると思います。
MDI(Mazda Digital Innovation)
福武 40年の間に車のクリティカルパスを順次解決されながらやってこられたということですね。
【開発期間短縮プロジェクト】
岡田 大きな流れでいうとそういうことになると思います。クリティカルパス全体に関わるような改革を全社のプロジェクトでぜひやらせてくださいという試みも何度かありましたが、なかなか実現しませんでした。
ところがバブルがはじけた危機の中でマツダも真っ先に影響を受けて、当時の社長の下に全社改革の抜本策が検討されました。ほとんどのものは即実行に移されましたが、数件の部門横断的なテーマが取り残されておりました。正に残されたテーマの一つが商品開発の開発期間短縮だったわけですが、これに目をつけ、手を挙げ、自らリーダーとしてこのテーマに勇猛果敢に取り組んだのが新見光弘氏です。また、これがMDIスタートのそもそもです。このような経緯で、1994年の春に開発期間短縮プロジェクトとして発足しました。そのときは、10人足らずのコアーメンバーで2年間ほどトライをいたしました。
この2年の間に、フォードから3回見学に来ました。
彼らもデジタル化のプロジェクトを立ち上げているが、なかなか現場がついてこない。マツダを見たら、現場が動いている。すでに動いているところもあるのだということを見せるために、2回目は現場の人たちを連れてきました。
逆に1996年の3月に我々もフォードへ行き、C3PプロジェクトのリーダーであるDr.Riffと、両社の将来システムについて話してみると、大筋で似通った仮想開発の考え方、システムであることが分かり、すぐ連携してやろうということになりました。
【MDIのスタート】
岡田 フォードから帰って間もなく、フォード、マツダは車開発でかつてないようなコラボレーションを進めることになり、急遽8月の経営会議で予算をつけてもらって、MDIが正式にスタートしました。車の開発期間短縮では、デザインをフィックスしてから量産開始までを世界的にターゲットにしています。その期間を27ヶ月から15~18ヶ月に短縮し、普通に開発できるようにというのが目標でした。
新規投資をして、トレーニングをして、新しいビジネスプロセスで車を作って、6年目に最初の車デミオが世に出ました。フォードと共通の車体で作った車です。私がびっくりしたのは、同時期に、ルノーと日産のマーチがでましたよね。それから、三菱のコルトもそうです。相談してやったわけではないけれども、流れとしてほぼ同時期にグローバルに共同開発した商品が出てきましたね。
【MDIフェーズ1】
岡田 プロジェクトを進める上で、既に徹底したデジタル化を実践した企業があるということは、大きな支えでしたが、それがボーイングです。ボーイングには、1985年ごろから1992年まで4回訪問しています。
1回目に行ったときに、ボーイングにある7つのCADをやめてCATIAだけにする。1つにすることに意味がある。道具はずっとサポートしてくれないと困るから、IBMが提供しているという点で、安全や信頼を評価してCATIAにしたと言うのです。当時の日本だったら、機能を並べて○×をつけ、○が多いほうが優れたCADだと評価していましたが、このような考え方は、アメリカ人らしいですね。しかも教育をして、一点切り替えをすると。何でこんな壮大なことをするのかと聞くと、物理的に作った飛行機のモックアップを見せてくれましたが、壮大な大工仕事ですね。最低2機作るそうですが、これをゼロにするだけで、費用が出るということです。ボーイングも、1985年から1992年、やはり7~8年かかっていますね。
このようなわけで、1994年の開発期間短縮プロジェクトのキックオフに、ボーイングのデジタルイノベーションの部長に、基調講演をしてもらったのです。飛行機は100万部品あるけれども、自動車はせいぜい3万部品でしょう。それなら6ヶ月ぐらいで作れるのではないかと言っていました。でも、飛行機は、1箇所にみんなが集まって作りますね。NCにしても、量産で何回も使うNCではないですね。自動車の場合は、製造を始めてから4年間、同じ品質で何十万台も作り続けます。ここが違うと思いますね。
MDIが成功したのは、IT屋が仕掛けたのではなく、車を作っている人たちが母体になって、業務側を総動員したからです。それに道具をあてていった。結果的には、私が知っている人と知っている技術のほとんどをMDIにあてたことになります。
フェーズ1の目玉はデジタルモックアップによる検証です。部品をアセンブリしてデジタルモックアップを作成するわけですが、どこかの部署がやっていないと、歯抜けになります。使い物にならないわけです。相当な人数の設計者を集中的にトレーニングして、全部品頭ごなしにやらないとできないわけです。従来のように「物を作ってから考える」のではなく、「物を作る前に考える」のが、フロントローディングであり、デジタル革新のエッセンスですが、デジタルモックアップによる事前検証は正にその第一弾となるわけです。
【MDIフェーズ2】
福武 フェーズ1の次は何がくるのでしょうか。
岡田 デジタルモックアップの進化のような話ですが、デジタルモックアップも2通りあって、お互いの位置関係を見ているのは、スタティック、静的な関係ですね。試作品を作る前にアセンブリをして事前に確認できるだけでも確かに効果は大きい。しかし試作品の数は減るわけではありません。精度のいい試作品が早くできるだけで、試作車を使って実験をする仕事量は変わりません。
今度は、性能のチェックもできるようなデジタルモックアップになれば、試作車が減ります。形状をアセンブリして、車の形ができたというのではなく、タイヤやエンジンや足回りなどが、性能を伴うモデルとして構築され、机上実験ができないかというのがMDIの第2弾でした。試作がゼロにならないにしても、部分の試作で置き換えられないか、部分の試作ですんだ物はゼロにならないか、実験と解析シミュレーションの合わせ業により、試作レスに取り組もうという挑戦です。
最近の日経ものづくり誌によりますと、マツダの新型車ベリーサは、デミオのプラットフォームを使い、デミオの開発で行ったCAE、台上試験、実車試験の結果を活用し、ノウハウを活かして、試作型なしで12ヶ月の開発だったといっています。
このことは大きなヒントになると思いますが、開発のときにゼロから立ち上がるのではなく、知識・経験の獲得分だけ完成度が上がるとすると、今後大いに知識のフロントローディングが期待できるのではないかと思います。
CAD/CAMからPLM/MPMへ
福武 CAD、NCというキーワードから、それを含むPLM、MPM(Manufacturing Process Management)に変わってきましたね。テクノマティックスさんが取組んでおられるMPMは、PLMのどの領域をカバーされているのでしょうか。
【生産技術にIT】
岡田 東大の松島先生がよく言われていることですが、
これまでを振り返った時に、
工場にITを入れてFAという時代があり、
工作機械にITを入れてNC、
設計にITを入れてCAD、
生産にITを入れてCIM。
この伝でゆくと、テクノマティックスは、生産技術にITを入れたということになります。またPLMは、エンジニアリング・チェーンにITをいれたということになるのでしょうか。テクノマティックスの生産技術のITというのは、金型NC以外のあらゆる生産技術領域へのIT投入です。自動車のCAD/CAMでは上流のCAD機能と共に長年金型のNCが注力されてきました。しかし、テクノマティックスはその後に続いたロボット化に端を発しているため、このような展開になったのだと思われます。
【工程エンジニアリング】
岡田 テクノマティックスのオーナーと会ったときに、何でこの会社を作ったのかと聞いたら、イスラエルは兵役があり、兵隊に行って、そこで軍事用ロボットのプログラミングをした。兵役から帰ってきて、民生用のロボットに活かせないかと、会社を作ってロボットのオフラインティーチングを始めたそうです。彼らのやり方は欧米流で、買収してどんどん大きくしていきますね。ロボットも溶接から塗装、人間の動作のシミュレーション、公差解析、デジタルモックアップによる工学的検証、汎用的な物流シミュレーションと品揃えを進めるわけです。
そして日本ではシステム化が非常に困難だと言われていた工程設計領域でもシステムで支援できるようにしたのです。これが、eM-Plannerと称している製品です。
生産技術の多様な個々のタスクを支援していた時代をCAPEと言っておりましたが、工程設計を取り込みプロセスのデータベースを構築するに及んで、一般的にもMPMという用語で流通するようになりました。
東大の藤本先生によると、「製品とは情報の束であり、製品開発は頭の中にある製品情報が、スケッチ、設計図、金型、最終製品というようにさまざまな情報媒体にかたちを変えて転写されていくプロセス」である。この視点に従うと、工程エンジニアリングは、設計情報を受け取り、生産へ転写していく一大プロセスと言えますし、この工程エンジニアリングを総合的にサポートしているのが、正にMPMですね。
先に話をしたフォードのRiff博士ですが、今年の弊社のMPM Forumで基調講演をお願いしました。その折、PLMというのはいろいろなBillの統合なのだという指摘が印象的でした。BOMのBillを指して言っているわけですが、Bill of Specification、Bill of Design、Bill of Analysis、Bil lof Processと確かにいろいろなBillが想定できる。MPMではBOP(Bill of Process)*を作成し、工程を各種シミュレーションで検証するのですが、このBOPはものづくりの情報のエッセンスです。こういう商品を作りたいという商品仕様(Bill of Specification)に対して、こうすれば作れるとなるわけです。
統合の観点からすると、ひとつはM-BOMといわれる部品表です。部品の親子関係が全部書かれています。購買での購入部品や技術的なデータも書いてあります。BOPで部品表に連結したら、部品表のプロセスデータ、技術データをうめることができ、部品表とインテグレーションできるのではないか。製造では、どういう順番で車を作るか、作るオーダーのシーケンスを決めて、一つ一つのオーダーに対して、どの部品を供給するかという技術データが対になっています。その情報もBOPから持ってこられるはずです。そうすると、ここを充実すると、製造の現場や製造のための原単位の部品表にリンクできるようになるから、生産技術の次の突破口になるのではないか、これはこれからの課題です。
* eBOP(Electronic Bill of Process)は、テクノマティックスの製品で、すべての生産プロセス(加工、検査、組立てなど)をオペレーション、パーツ、リソースと関連付けて、デジタル表現させる手法です。
【2つのビジネスプロセス】
福武 テクノマティックスさんのソリューションは、ROBCADから、デジタルモックアップ、CAPE、MPMと名前を変えながら、柔軟な生産体制を実現するソリューションへと広がっていますね。ものづくりの一番近い領域については、ある程度カバーできるというところまできたのではないかと思います。
岡田 バーチャルに製造している状況で起きている振る舞いと、製造現場で起きている振る舞いと、限りなく近くなってきますね。実際に物を作らないだけで、ほとんど作るのと同じ状態を詳細に行っています。
ヨーロッパの自動車のユーザは、ROBCADでロボットの動きをシミュレーションしてOKなら、OKと同時に現場でロボットを動かすための命令も出してほしいと要望しています。即実行しようとすると、冶具が動いているシーケンス制御があり、ロボットを動かすロボット制御もあります。両方の制御命令がリンクして動いているので、実行できる命令を出すのは大変だと思いますが、ひとつはそういう方向ですね。
もうひとつは、シミュレーションで先を見ながら実行していこうということが起きるかもしれません。どこかで欠品がおきたときに、すぐに最適状態にディスパッチをする。日本人はディスパッチが一番うまいですね。でも、神様のような日本人がいなくなったときに、瞬時にディスパッチをしようとすると、シミュレーションをする必要があります。バーチャルとリアルが紙一重に向かう中で、シミュレーションをすることがどれだけ広がってゆくか、興味があります。
商品開発と受注・出荷処理の、製造業の2つの大きなビジネスプロセスの交差しているところが製造ですから、そこへ向かっていくということは、これから商品開発とは異なるビジネスプロセスの影響を受けていくということです。企業全体でのスループットを考える方向になりますね。
HZSさんだったら、技術系のシステムインテグレーションをやる部隊がいて、同時にビジネス系をやる部隊がいて、それが連携すれば全部カバーできるという話になるのでしょう。
福武 3次元の情報と経営管理なり、材料手配の仕組みをうまくドッキングさせるようなところで、力を発揮するのは当社の生きていく道だと思います。
【デジタル化の現状に思うこと】
岡田 今、世の中を見て思うことは、ベンダー1社でこれからのPLMを作るということは、絶対にできないということです。そうすると、ベンダーが複数いて自分自身のシステムも入れてインテグレーションをせざるを得なくなる。そういうときのインフラとして何を選択したらいいのかということは、これから解明していくことではないでしょうか。今はCADやデジタルモックアップを中心にDesign Process Managementが進行過程にある。
同時に設計と生産技術がパラに動いている。それをきちっと情報で全部つなぎますということも、そのレベルがまあまあ先端的な企業でできています。しかしよくみると、実験・解析の世界と設計の世界がきれいにリンクしているというのはこれからじゃないでしょうか。ましてや製造や部品表ともリンクするという話になるとまだまだでしょう。
少し話が変わって、デジタル化の効果の側面ですが、MDIもそうですが、デジタルな投資をして、開発期間が短縮したら、車のコストも下がっているはずです。ということは、車の月当たりの台数をかなりおとしても、やっていける時代になったということだと思うのです。1つの車を年間何十万台も作るという時代がありましたが、今も総台数はあまり変わらないとしても、内訳はものすごくバラエティに富んでいます。
福武 1車種あたりの生産数が減って、車種が増えているということは、逆に価格が上がってもしかたがないと思いますが、コストが下がっているのは、まさにこれらの道具のおかげですね。
日本と欧米の発想の違い
福武 今、ものづくりのキーワードは、早く、安く、高品質ですが、これからは、ユーザニーズ、ユーザが何を求めているかをいち早く察知して商品化するというのが、日本で生きていくには重要なキーワードだと思います。そうするると、3次元の蓄積されたデータをどううまく使って新しく製品作りに役立てるかということがポイントになってくると思います。
コンピュータの能力が進んでいるということがあって、ソフトが頑張っていけるという感じがしますね。
岡田 ソフトで頑張っていけるということには、まったく同感ですね。ただ日本はものづくりが得意だといいますが、ものづくりのソフトに関していうと、HZSさんが自前でGRADEを作られたように日本発のソフトを売っておられる例もありますが、テクノマティックスに関係していて言うのもおかしいですが、海外で作られたものづくりのソフトを仕入れてきて、それにサービスをつけて売ります、という形態があまりに多いですね。それはそれで、繁栄していますということになるかもしれませんが、質的に見るとすごいギャップがあるでしょ。物を作るのがうまいのに、ソフトの部分はほとんど輸入に頼る。なんでこういう極端なことが、おきるのだろうかという気がしますね。この日本の特異な現象をテーマにしてパネルディスカッションをしたことがあります。パネラーの一人であった米国Daratech社の社長の指摘ですが、日本人にはみんなが使うようなモノを工夫して作ろうという発想があまりないのではないかと言ったのです。自分だけのものすごいPowerのあるモノを作ろう、一点磨き上げるようなそういう発想はあっても、平均的にみんなが使えるモノを作って売ろうということに向いていないということです。外人から見ると、そのように見えるのかなあと思いますね。
それと日本では、まず日本で成功してから海外に出て行くという考えがありますね。それでは最初から勝負がついたような話で、プロトタイプを作っているときから、世界の主要なところに全部出してしまう。あたったところから行きますというのが欧米のやり方です。テクノマティックスも最初は、ヨーロッパの自動車メーカで、育ててもらっています。
日本発のソフト、日本のものづくりを反映したソフトをいかに提供できるか、課題ですが、同時にこれからの夢ですね。
HZSへ
福武 これから先、HZSはどういう方向で取組んでいけばいいか、アドバイスをいただけますか。
岡田 よく米国の製造業は歴史的に航空産業が先導したと言われました。その役割は日本では造船業であったような気がします。その流れを汲んでおられるだけに、HZSさんは、ほんとの仕事をしていてガッツがあるというイメージがあります。そういうことが薄れている時代ですから、自前のシステムを取り戻していくとか、ユーザの会社が付加価値をつけようとしていることに対して手助けを行うなど、高い付加価値をつけていかれることを望みます。お互いライセンスだけを販売する時代は終わろうとしています。
福武 日本の企業が生きていくのは、人のできないことをやるしかないですからね。当社は、いいモノを作って売るということと、いいモノを作って売る技術を活かすという、この2面で他社との差別化を図っていきたいと考えています。
デジタル化を推進してこられた岡田会長のますますのご活躍を祈念しています。本日は、いろいろなお話をどうもありがとうございました。