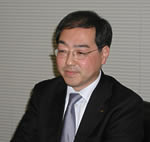
所長 小松 道男 様
小松 道男様プロフィール
1963年 | 福島県生まれ |
---|---|
1983年 | 国立福島工業高等専門学校 機械工学科卒業 アルプス電気株式会社入社 生産技術部で、電子部品、通信機器部品、自動車内装部品等のプラスチック射出成形金型の設計に従事 日本機械学会畠山賞受賞 |
1991年 | 史上最年少27歳で技術士資格を取得 |
1993年 | 小松技術士事務所設立 |
1999年 | 日本合成樹脂技術協会金型研究会委員長 |
現在 | プロフェッショナルエンジニア(技術コンサルタント)(独)福島高専電気工学科非常勤講師(生産工学講座、知的所有権講座)、すみだ中小企業センター技術相談員、(独)国際協力機構(JICA)金型プロジェクト国内支援委員、福島県ハイテクプラザ技術顧問、創成国際特許事務所顧問 |
主な著書 | プラスチック射出成形金型設計マニュアル、プラスチック射出成形金型設計マニュアル分割構造金型編、プラスチック射出成形金型ピンポイントゲート金型編(日刊工業新聞社) イラスト射出成形アイデア活用術、はじめての金型技術(松岡甫篁技術士と共著)(工業調査会)Amazon.co.jp金属・鉱学部門で売上第1位ランキング(2002年5月) 射出成形事典(部分執筆、産業調査会) |
専門事項 | プラスチック射出成形品の生産システム構築、プラスチック射出成形金型の開発・設計技術 新製品の生産技術開発と知的財産権利化支援 |
業務内容 | 1.プラスチック金型の設計、生産技術に関する技術指導・コンサルティング 2.射出成形加工技術のコンサルティング 3.CAD/CAM/CAE技術に関するコンサルティング 4.新製品開発のコンサルティング 5.知的財産権に関するコンサルティング 6.技術者育成に関するコンサルティング |
所属学会等 | 日本技術士会、日本合成樹脂技術協会、型技術協会 |
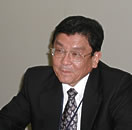
福武 映憲
福武 小松先生は、中小企業の振興を大きなテーマのひとつとされ、製造業の支援に真剣に取組まれていらっしゃいます。日本はもとより、アメリカ、ドイツ、フランス、香港、ベトナム、タイなど約12カ国で、コンサルタントとしてご活躍されていますね。中小の金型企業さんが日本で勝ち残るためには、何をしなければならないのか、世界の金型事情なども含めて教えていただければと思います。
ヨーロッパの技術
【金型は生産システムの一部】
小松 昨年の10月にK2004に行きました。これは3年に一度開催されるプラスチック関連の非常に大きな展示会です。当然、金型に関わるものも展示されています。日本の場合は、金型産業はひとつの独立したカテゴリーで、金型というジャンルが成立していますが、ヨーロッパやアメリカでは、プラスチック部品を生産する生産システムの一部という位置づけで金型技術が発展してきています。射出成形加工をしてプラスチック製品をいかに効率よく安定してたくさん供給するか、システム指向で全体を最適化する中で、金型がどうあるべきかという着想に基づいています。
福武 ヨーロッパもアメリカも、日本以外はそのような考え方ですか。
小松 アジア以外はと言ったほうがいいでしょうか。だから、金型単体で最適化していくと、どうしても早く安く作るということに目がいきがちになります。中国を始めとする近隣諸国と価格がコンピートするために、もっと安く、もっと早くということになります。
このような過当競争があったのが、今までの10年ではないかと思います。ところが、さらにエスカレートして、中国の値段で提示されるがとてもできない。そんな状況の中で廃業される金型屋さんも出てきて、このままでは金型産業は壊滅するのではないかという悲観的な論調もだいぶありました。
ヨーロッパなどでは、生産システムの一部と位置づけていますので、新たなプラスチックの素材、燃料電池の自動車、デジタル家電の普及など、今まで世の中になかったプラスチック部品を最適化で作るためには、金型はどうあるべきかということをまじめに考えて、非常に周到にやってきたというのは事実だと思います。
したがって、ヨーロッパでは、金型の値段は成形品で償却します。最終成形品を生産する数で、投資した金型費をどう回収するか。こういうのは、綿密に計算をされているというのが、日本とは違う特徴的な点です。
【生産性の高い金型】
小松 ヨーロッパの場合は、荒っぽく申し上げれば、金型の納期は、日本の2~3倍は許容されていますね。それは、モデルチェンジのサイクルや、耐久消費財を長く大事に使うという風潮もありますが、金型は長くかかっても、生産性が高く作成できればそれで認めましょうと、この辺は日本のマーケットと大きく違うところですね。
福武 最近は、ヨーロッパからも日本に短い納期で中国並みに安くできないかという話もくるとお伺いします。
小松 K2004へ行ったときにヨーロッパの企業さんを回ってみたら、ヨーロッパも中国は捨ておけないということで、中国での調達の可能性や、世界の約半分を作っている日本のマーケットにどうやって入っていったらいいかというご相談もありました。ヨーロッパも、東洋に拠点を持って展開をしたいという意思はお持ちです。ところが、日本の漢字という独特の文化、異なったビジネス習慣が非常に大きなハードルになって、日本になかなか入ってこれないというジレンマはお持ちのようです。
ヨーロッパ、アメリカの金型の大きな特長のひとつは、生産性が極めて高いということです。スクラップを出さないスクラップレス成形技術が重要視されています。ある統計によれば、金型の総生産数の40%程度は、何らかのスクラップレス技術を搭載しているということです。
福武 生産性が高いというのは、具体的にはどういうことでしょうか。
小松 プラスチック成形型の場合、日本では一般的にコールドランナーで、樹脂を流したところの枝の部分は廃棄しますから、原材料の10~60%は廃棄しています。ランナレスを使えば、材料の利用率が100%になります。廃棄物が出ないという点で非常に大きな差が出ます。
また、マルチキャビティで、取り個数を多くする。たとえば、64個取りや128個取り。64個取りをスタックモールドという技術で2面取りをすると128個ですね。それが、日本では16個取りで、コールドランナーで作っている。そういう中で、成形品の単価を本当にいくらで作っているのかという勝負をした場合には、金型代を償却したとしても、日本は勝てるような技術は無いと言っていいと思います。
今は、日本のマーケットは、地理的な事情や関税で保護されて守られている状態ですが、本当にそういうようなものがないところで、プラスチック成形品のコスト競争に入ったときには、勝つのは難しいと思います。
福武 なぜ日本は、ランナレスや多数個取りに取組んでおられないのでしょうか。
小松 短納期で対応するという場合に、ランナレスシステムで対応すると時間がかかるからです。ランナレスシステム、バルブゲートなどを使いますと、その仕組みの投資にイニシャルコストが結構かかります。金型の単体価格と同額程度のさらなる投資をしなければいけない。
大量に自社製品を作られている会社以外は、生産数の問題と、非常に短いライフサイクルで投資を回収しようという中で、ランナレス成形を積極的に取入れにくいという背景があると思います。
福武 日本では、短納期で多品種少量にどれだけうまく対応するかということで、小ロットの金型にお金をかけることができないとよく伺います。そういうところから、生産性のいい金型作りがなかなかできないのですね。
小松 自動車の部品では、大きなバンパーやインスツルメントパネルなどを成形する場合に、従来はコールドランナーで枝をいくつかに分けて分岐して充填するので、入り口がひとつで出口が6箇所ぐらいあります。1つの入り口で6箇所もの注入口を精密に制御しようとすること自体、不可能に近いのです。バルブゲーティングを使えば、6本の独立した開閉バルブを金型の中に搭載して、それぞれの開閉タイミングを制御することができ、まっすぐで美しいバンパーが成形できます。
ヨーロッパの今回のK2004でも自動車の大型部品の成形には、バルブゲートシステムがたくさん採用されてきているというのが印象的でした。
バルブゲートシステムは、日本の大手自動車メーカーさんはすでに導入されていて、国際的に常識化していますが、自動車メーカーさんがアウトソースされる中小の型屋さんでは、技術の習得も大変ですし、ついていくのも非常にきつく、バルブゲートは使いにくいという図式があると思います。
日本の強み
福武 日本の金型のここが一番だというところはどこでしょうか。
【3次元CAD/CAMを使った意匠面の作成】
小松 厳しい環境の中で、短納期でいいものを作り上げる。非常に激しい競争を繰り返してきた中では、意匠形状に特徴があるような金型を、3次元CAD/CAMを使って効率的にいいものを作るという技術は、日本が飛びぬけて強いところです。
しかし、金型にはいろいろな種類がありますので、すべてが世界一だと思ったときにつまずきが出ます。樹脂金型は40年強ぐらいの歴史しかないわけです。金型のピークを作ってこられた皆さんが引退される時期に入っており、過去のサクセスストーリをそのまま踏襲しても、過去は過去の栄光でしかありません。
人の動きやものの動きがこれだけボーダレスになってきますと、これからは考え方を切り替えて、国際競争という中で見据えていかないと、異文化との競合になった場合に、はたして日本のモデルが外国勢に受け入れられて、打ち負かすことができるのかよく考えないといけないですね。そういうステージに入ってきていると思います。
【マイクロ電子デバイスの金型技術】
小松 もうひとつは、分割金型という、コネクターあるいはマイクロ電子デバイスの金型技術も世界でトップであると思います。
超精密の分割金型で、マシニングセンターで削るというよりは、ワイヤーカット、精密研削です。小さな部品をたくさん集めて、寄木細工のようにして作る金型構造です。この辺は、非常に強いと思っていいと思います。
携帯電話の端子、移動体端末で多量の画像データを送るような場合には、たくさんの穴を設けなければいけません。0.15mmぐらいのピンを並べて折れないようにして、4個取りぐらいで作るのです。これは、日本でしかできないでしょうね。
この辺になると、HZSで開発されている3次元システムでモデリングをしてコンポーネントデザイン、コネクター単体をデザインして、3次元で組合わせの状態などをシミュレーションする。非常に強いジャンルですね。
金型積層造形
小松 今回のK2004で印象的だったのが、金属粉末造形技術です。これがきちんと認識された展示会であったと理解しています。
今までの金属粉末造形は、単に形が造形できるという印象でしたが、EOS等の展示の中心は、異形状のコアの中に冷却回路を任意で構成でき、早く冷やせることです。成形金型の冷却回路がつけにくいスライドコアなど、離れたパーツの中に任意自在に冷却回路を設けることができる。こういうことで、今まで冷やせなかった部分を適正に冷やすことができる。
金型を作るうえで、温度をきちんと制御することができるキャビティをHRC40程度の工具鋼で造形できるのです。こういう切り口で展示をしたということが、非常に重要なことだと思います。
今までの手法ではできなかったものができる。それを使うことで成形品が早くサイクルアップでき、外観もひけのない安定したきれいな美麗な曲面が得られる。今までなかった技術が実用化されようとしています。これを象徴的にあらわした印象深い出展だったと思います。
ドイツはレーザーに関しては、非常に特化しているとみていいと思います。
福武 EOSINTを使って、今までできなかったところに水管をはわせて、従来よりも2割短いサイクルタイムで成形できさえすれば、少々金型が高くてもいいんだとおしゃっていただいています。
とうもろこしからプラスチック
小松 私の研究テーマのひとつで、ここ最近お茶碗の研究をしておりまして、とうもろこしが原料です。耐熱ポリ乳酸というプラスチックで、使い終わったら土中に埋めると、バクテリアが食べてCO2とH2Oのみに分解されます。
【生分解性プラスチック】
福武 どのぐらいの期間で分解されるのですか。
小松 フィルム状ですと、1週間でなくなります。お茶碗では砕いて、堆肥などに入れて、6ヶ月ぐらいです。残っても、木が腐るような形でいずれはなくなります。
ある原材料メーカーさんでは、経済産業省と農林水産省の食堂で1年ぐらいベンチマークをしています。3月25日から開幕する愛知博で使う食器は、すべて植物由来の生分解ポリ乳酸を使います。これは小泉総理の肝煎りもありまして、2月の衆議院施政方針演説でも、環境にやさしいということのひとつとして、耐熱ポリ乳酸を積極的に使っていくと演説されています。
この素材は、耐熱性があり、120℃まで変形しません。つまり、食器洗い機に入れて洗っても大丈夫です。今までのポリ乳酸は70℃前後で、ぐにゃっとなってしまいましたので、10年間気の利いた実用化はほとんどできませんでした。これが、昨年、微量の粘土等をナノコンポジットの粉を分散させることで、結晶化を促進して、120℃まで持つ材料が出てきたのです。食品衛生法上もクリアーしていますから、人体にも無害です。この食器は、愛知博以降、大量にマーケットに出回ると思います。
【車の部品やパソコンにも】
小松 トヨタさんは、10年以内に樹脂部品の20%にこのプラスチックを使用していくと発表されています(http://www.toyota.co.jp/jp/environmental_rep/03/special02.html)。自社でも2001年にインドネシアにサツマイモを原料に家畜用資料と生分解性プラスチックを製造する新会社を設立されています。
パソコンメーカーのNECさん(http://www.nec.co.jp/press/ja/0401/2603.html)や、富士通さん(http://pr.fujitsu.com/jp/news/2002/06/5-1.html)もこれを筐体部品に使うというプレス発表が出てきています。
したがって、プラスチック部品は石油から作って使い終わったら燃焼処理、埋設処理をして永久に地球上に残ることが当たり前だった文化から、植物から得たもので素材を作り、使い終わった自動車部品や家電部品は土へ埋めて分解するという文化に変わっていきます。これは、日本から世界に発信するすばらしい技術だと思います。
ごみを大量に捨てているということは、今後は、分別ではなく回収して土中に埋めて土に返す。カーボン・ニュートラル・リサイクル*がきちんと動くようになってくるでしょう。プラスチックは石油から作るという常識が変わっていく年が、今年であると思います。
この耐熱生分解性プラスチック用の金型は、キャビティの温度管理が非常にセンシティブで、金型の温度を120~130℃に安定させて保持しなれば所望する耐熱性が得られません。そのためには、流路をどういうふうに形成して保温するか。暖めすぎてもだめですし、うまく冷やしながら暖める。そういうようなものを金型の中にうまく盛り込まないと成形できません。
今度は、筐体関係などに当てはめていくときに、金型の形だけ削るのではなく、水管の裏側のデザインをどうするか、そういう部分にノウハウを入れ込んでいく、新たな型技術が早急に必要になってくると思います。
金型の内部が非常に重要になってくると思います。それが実現できるようなものが、金属粉末造形だと思います。形を作るのではなく、キャビティの表面温度をいかに安定させるかという着眼点でいけば、削るだけではなく、金属積層が非常に重要なポイントになって、用途は非常にたくさんあるのではないかと想像しています。
* カーボンニュートラルとは、ライフサイクル全体でCO2の増減に影響を与えない性質のことです。土壌に埋めて分解された生分解性プラスチックから発生するCO2は、トウモロコシを栽培し光合成に使われるので、循環しCO2を増やしません。
マイクロモールド
小松 ドイツへ行ったもうひとつの目的が、マイクロモールドです。LIGAプロセスといわれる工法で、ニッケル系の合金をレーザーリソグラフィーで積層して、ナノオーダーのキャビティを作ります。部品の内側に非常に微細な溝があり、難聴などで耳の手術をしたときに人体の中に埋めて使うインプラント型のとても小さな成形品も実用化されています。
ドイツでは、医療系の研究をしていまして、耳の中に埋め込む補聴器、カテーテルで心臓手術をするときの先につけるカッターなどを熱心に研究しています。レーザー技術はドイツが群を抜いています。
日本では、オリンパスメディカルシステムズさんが、胃カメラではなく、薬の錠剤のように飲み込む、プラスチック製の使い捨てカプセル内視鏡で、2年後の実用化を目指されています。
東レさんは、がんなどの病気を遺伝子診断するDNAチップを開発されています。感度は、従来のものより100倍も高くなっています。これは、突起表面をナノレベルに加工します。
富山のリッチェルさんも直径10マイクロの穴や溝を開けた微細チップを開発しています。
そういう金型は、レーザーや、専用の成形機が必要になります。部品が5/10000g程度ですから、これを4個取りできちんと計って射出する。安定して打てないといけないので、そのような成形機は日本ではまだ量産されておらず、現時点では、ドイツの「Microsystem50」しかありません。一緒に共同研究しているチームが、ごく最近、日本での3号機を導入しました。あと数年間、この金型を研究していきます。
このような加工を応用して高級に精密に作る方法と、もっと安価にマシングセンターを使って作る方法といろいろありますから、その辺を確立すれば、安くていいものが完成すると思います。このようなメディカル系のマイクロ成形が出てくる可能性がありますね。
最新の技術にふれること
小松 夢のような非常に大きな話ですが、今までとは違ったこのような新しいマーケットが出てきているのは事実です。中小の金型屋さんの技術開発も、こういう部分を少しずつやっていこうという姿勢をオーナーやトップが持っていないと、まったく反応しないで終わってしまう。次の時代で活躍していくためには、こういう新しいジャンルで何とかやってみようという気概を経営トップが持つことが、非常に重要なことです。
福武 トップの方のそのような思いがあれば、一般的にはどのような行動をすればいいのでしょうか。先生のような方にうまくめぐり会って、お話をお伺いしないといけないですね。
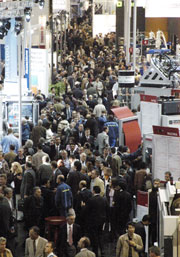
©Messe Dusseldorf GmbH
小松 そういうこともあるでしょうし、K2004という展示会や、アメリカの見本市もあります。そういうところへ思い切って飛び込んでみると、似たような思いをもった人たちが世界中から集まってきますから、そこでめぐり会った人たちと、意気投合してうまくいくこともあります。
私のこの5~6年は、欧米で出会った人たちと意気投合して研究してきたものがうまく事業に結びついてきています。先進国の会議や展示会に行ってみること。その旅費がもったいないなどと言うのではなく、ぜひ行ってほしいと思いますね。そうすると、日本の金型の作り方や発想の違いが身にしみてわかるのではないかと思います。情報は取りに行けば必ずそこの周辺にあります。
このように考えていけば、着想は後発であっても、生産技術は先行してやっていくことができます。発想は欧米に任せて、生産技術は日本で開発する。お互いにその技術を持ち合いながら、安定して社会をよくしていく。いい方向に導いて、皆が幸せになるようにやっていく。こういう理想を掲げることが、私は重要だと思います。
コストが安いから中国へ行くということだけではなく、どうすれば社会や環境をもっと良くしていけるか、格好つけた言いかたですが、高尚な考えを持ってやったときに初めて異文化とめぐりあって、お互いに分かり合えるものが出てくるのではないかと思います。
現地で出会う中小の金型メーカーのオーナーさんは、勉強されていますね。そういう会社は非常にアクティブですし、反応も早いし、クリエーションの大切さもきちんと認識をされています。
アジア
【中国】
福武 中国の金型の技術はこれから先は、日本と同じレベルに来るものでしょうか。
小松 私は、返還前と返還後に香港しか行ったことがありません。現代の中国にはあまりときめかないので、今のところ行ってみたいとはあまり思わないのです。
中国の国民一人当たりのプラスチックの年間消費量は、約10Kg、日本やアメリカは100Kg前後です。マーケットとして非常に大きいところですから、金型の需要というのは底知れぬ量があることは事実だと思います。
金型もピンからキリまでありますが、マイクロ成形や生分解樹脂というカテゴリーをはたして中国でやる意味があるのかと考えると、そういう類のものは、日本やドイツが中心になってやっていくもので、中国のマーケットの皆さんがほしがっているような製品の金型は中国でやると、大きく2種類に分かれていくと思います。
【フィリピン】
小松 フィリピンとは、日本はFTAの基本合意を出して、この10年以内に物流の相互関税は撤廃していこうという方針が出てきました。フィリピンは、今までは金型などは出遅れていましたが、英語圏で成田から4時間で行ける、名古屋からでしたらもっと早いですね。そういうポジションのところに、FTAの波にのって、金型や部品産業を立地していこうという動きが出てきています。
【タイ】
小松 タイと日本の間は、この4月ぐらいにFTAの基本合意の発表があるでしょう。そうすると、米と自動車のバーター取引という中で、日タイ間の関税も10年以内に撤廃しようとなりますから、タイへの金型や部品加工は、今非常にエネルギッシュなものがあります。タイの工場も、日本の金型工場、射出成形の工場がそのままリプレースしたような形で、日系が進出していますので、タイ工場のレベルは、日本とまったく遜色ありませんし、むしろタイのほうが進んでいるわけです。こういう現実をきちんと理解しないで、タイの金型はたいしたことないよと思っていると、捉え方を誤っていると思います。タイは、日本の生産拠点と同じかそれ以上のものを作り出すことができるようになっています。トヨタさん、ホンダさん、CANONさんもそうですね。
タイはむしろ中心的な存在で金型産業が伸びていくポテンシャルがたくさんあるのではないかと思います。
【インドネシア】
小松 インドネシアの金型とプラスチック産業の綿密な調査を10年ほど前に担当したことがあります。インドネシアの場合も金型は重要ですが、日本の支援は出遅れましたね。今回の選挙で大統領が変わったということで、日本もインドネシアを支援しようということにはなっていますが、むしろ、スイス、ドイツの支援のほうが先行しています。バンドン工科大学に、スイスが寄与した金型トレーニングセンターがありまして、非常に多くの人材輩出をしていますので、日本は出遅れている状態です。
【ベトナム】
小松 ベトナムは非常に重要なポジションだと思います。タイ~ホーチミンシティー~ハノイには、二輪車産業、家電産業がある、CANONさんなども出られています。コンポーネントの最終組み立てが出ることで、部品のサプライの需要が非常に大きいです。したがって、まずは金型の輸入が増えて、メンテナンスが増えて、ローカライズが増える。中国に対するリスクヘッジを考えますと、ベトナムのポジションは、非常に重要だと思います。
私がハノイとホーチミンを訪れたのが5年前ですが、そのとき中心になっている世代が30~40代ぐらいです。我々の国を我々の力で立て直すんだという強い国民の意思をお持ちになっています。国を今から立て直して伸びていくんだという国民の強い意識を感じました。社会主義から市場主義経済に変わるという中で、いろいろ困難はありますが、ベトナムは順調に伸びていくでしょうし、日本はベトナムとは仲良くしてパートナーとしてやっていかなくてはいけないと思っています。
ぎりぎりのところを狙って
福武 小松先生はいわきにお住まいですが、1/3は東京、1/6はいわき、1/6は海外、あとは日本全国を飛び回られていますね。
小松 ほとんど出歩いていますので、自分の本拠地はどこなのかわからないような状態です。でも、アクティブに動いているといろいろな情報が入ってきます。大事なことは、真面目に実験をしたり研究をして、物を作って現場で評価するということを放棄したら、だめになると思います。
福武 実験など、現場でのモノ作りは、どこでやっておられるのですか。
小松 クライアント企業でスタッフと一緒に研究をしたり、公的な研究機関等でものづくりを現場主義でやっています。ストライクゾーンど真ん中ではなく、ボールかストライクかぎりぎりのところを狙って、これ以上いったらあぶないなという限界のところをきちんと制御できるのがプロです。その辺の開発をしないと旨味もありませんし、誰でも投げたら入るようなストライクゾーンは、すぐに真似されますから。私のような実務家はそのあたりを重要視しています。
福武 先生のお話をお伺いしていますと、経営者とホントの技術者という両面をお持ちですね。まさに今言われた、誰でもできる技術ではなく、ぎりぎりの領域でうまくやることが一番大事だということはよくわかります。日本がこれから生きていく分野も、そういうところでしょうね。
小松 健全に成長していくには、違法行為や、真似をして知らん振りをして技術を盗んで使うというのは、毅然とした態度をとって、自分で守らなければいけません。ソフトウェアもそうですし、特許権もそうです。ちゃんと自分たちで使っていくということを金型メーカーさん、モールダーさんが認識を持つということが、とても大事だと思います。今までは、特許や著作権は大企業のものでしたが、そうではありません。企業が伸びていくためには、特許権、著作権等についてきちんと理解をして、向かっていかないといけないと思います。
HZSへ
福武 小松先生には、金型の教材E-Trainer「インジェクション金型の設計2」の執筆や、ご指導をいただいています。HZSへアドバイスをいただけますでしょうか。
小松 時代の要請に応えられる金型を開発するためには、現実的な成形加工でのノウハウを反映した金型の設計思想がキーポイントです。ソフトウエアのバーチャルな世界に現実のノウハウを盛り込んだシステム作りをHZSさんにはお願いしたいところです。
また、e-Learningシステムと適切なコンテンツを開発していただければ、金型設計技術者の育成にも大変有益です。遠隔地域間での実践教育に耐えられるものが望まれています。
さらに、ソフトウエア等の著作権や特許権等を適切に保護していただいて、購入されたユーザーさんが安心して使用できる環境整備を率先して示して頂けるようにお願いします。海賊版を違法製造されないような防御手段もグローバル化が進む今後はユーザー保護には重要です。
福武 本日はお忙しい中、大変勉強になるお話をお伺いすることができました。小松先生のますますのご活躍を祈念しています。どうもありがとうございました。