~EOSINT Mによる金属部品・金型製作~
RPシステム部 橋爪 康晃 |
e-Manufacturingとは
EOSが提唱する新しいものづくりのコンセプト。
定義は「迅速に、柔軟に、低コストで、デジタルデータから直接製品を自動的に生産する手法」
はじめに
3次元CADデータから直接製品を造形するラピッドプロトタイピング(RP)技術は、製品の開発期間の短縮及びコスト削減の手段として、自動車、家電業界を中心に広く活用されるようになってきました。RPシステムの多くは、樹脂材料を使用するものですが、「粉末焼結型RPシステム」であるEOSINTシリーズには、「人とシステム」No.39(以下、No.39)でご紹介した樹脂材料を使用するEOSINT Pの他に金属や鋳造用の砂などを材料として使用する機種があります。今回は、金属材料を使用するEOSINT M250 Xtended(写真1)及びEOSINT M270(写真2)を使った「金属部品製作、金型製作」と「新しい分野」についてご紹介いたします。
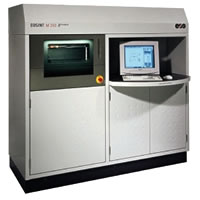
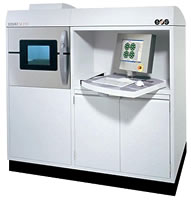
表1は、EOSINTを使用した製品を、「プラスチック部品の製作」と「金属部品の製作」に大別したものです。今回はEOSINT Mの活用に関して事例などをご紹介します。なお、プラスチック部品の製作に関してはNo.39をご覧ください。
製品 | 材料 | 材料名 | 主な用途 | 機種名 |
---|---|---|---|---|
プラスチック | ナイロン ガラス入りナイロン アルミ入りナイロン |
PA2200 PA3200GF Alumide |
意匠検討モデル スタイリング用モデル 機能試験用試作モデル エンドユーザー製品 |
EOSINT P385 EOSINT P700 |
金属 | ポリスチレン | PrimeCast100 | ロストワックス 鋳造用消失モデル |
|
ブロンズ系合金 鉄系合金 鉄系合金 |
DM20 DS20 DSH20 |
試作用射出成形金型 量産用射出成形金型 金属部品 |
EOSINT 250 Xtended EOSINT M270 |
|
シェル砂 | 鋳型(主型、中子) | EOSINT S750 |
EOSINT Mの特長
EOSINT Mは、金属粉末材料を直接焼結(溶融)させて積層造形するDMLS(Direct Metal Laser Sintering)法を採用しており、金型や試作部品、最終製品を金属で直接造型できるRPシステムです。
その特長は次の通りです。
- 100%金属材料
使用する材料は、粉末を固着させるための樹脂バインダーなどを含まない100%金属材料であること - 十分な強度
量産用金型や最終製品にも適用できる十分な強度を持つこと(硬度HRC40相当を実現) - 複雑形状の造形
従来工法では製作が困難、または不可能な複雑形状を金属で造形できること
EOSINT Mの進化
EOSINT Mの主な用途は、金型、金属部品の直接造形です。このためEOSINT Mは、強度、表面品質、造形時間といったことを主な課題として進化してきました。当初は50ミクロンだった最小積層厚は、20ミクロンになり、より微細な表現力を得ています。約70%ほどであった造形後の密度も、ほぼ100%に近いものになっています。これらの改良の結果、従来工法で製作したものと同じ要領で後加工ができ、金型として使用する場合も特別な処置を施すことなく、従来と同様に成形工程で使用できるようになりました。また、量産用金型や最終製品に、高い硬度が必要な場合に対応できる高硬度材料も登場し、適用範囲が拡大しています。
新材料の登場とともに装置も改良されてきました。EOSINT M250は、Co2レーザーユニットを高出力のものに変更し、それに合わせた造形環境の改良を施され、現在のM250 Xtendedにアップグレードしてきました。そして新たなラインナップとして、Ybファイバーレーザーを搭載したM270がリリースされています。0.1mmまでレーザースポット径を絞り込むこことができるため、表面品質、細部の表現力が向上しています。また、今までに無い材料への挑戦が可能になったという重要な役割も担っています。
EOSINTの事例...金型
当初より、EOSINT Mを金型製作に活用したいというニーズは非常に多かったのですが、当時の材料特性では適用範囲に制限がありました。その後、新しい材料の登場やお客様に数多くご活用いただいたことにより、事例が増えてきました。以下にいくつかの事例を紹介いたします。
写真3は、EOSINT Mの活用方法として一般化してきたハイブリット金型の事例です。試作品製作の効率化を目的とし、EOSINTによる造形とアルミの切削加工を組み合わせています。写真4はEOSINT Mによって造形された部品です。170×130×40mmのキャビティとコア双方を13時間で同時造形しています。ベースの加工、中心部品の製作、仕上げを加えた全体の工期は、合計63時間。結果として製作コスト30%削減、工期3日短縮を実現しました。この事例をご提供いただいた富士電工様では、同様の手法で既に30型以上を製作されており、同社の標準的な工法のひとつとなっています。
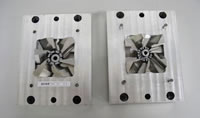
(株式会社 富士電工 様)
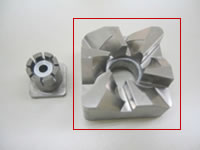
(株式会社 富士電工 様)
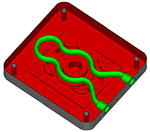
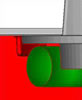
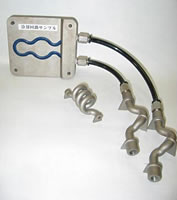
(樫山金型工業 株式会社 様)
写真5は樫山金型工業様での研究事例です。EOSINTの造形方法の特長を活かし、最も効率的な「形状に最適化された立体的な冷却回路」を造形するという試みが行われており、実際の業務でも利用実績があります。今までの工法では直線的な穴しか開けることができませんでしたが、積層造形では、自由な形状で回路を作り出すことができます。これによって冷却効率の高い金型を製作し、生産効率向上させようというものです。
海外でも同様の取り組みは活発化しており、いくつかの事例が公表されています。写真6は、練習用ゴルフボールの金型です。200万個以上の成形に使用され、生産効率が20%向上したと報告されています。写真7は、携帯電話のスタンドの金型です。このような活用は、今後ますます増えていくと思われます。
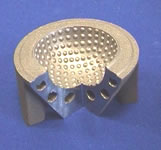
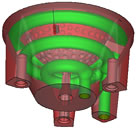
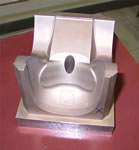
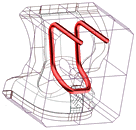
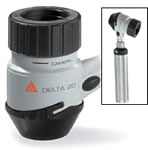
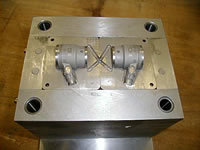
写真8は、医療用機器の量産用金型の事例です。機械加工によるキャビティとEOSINTによるコアを組み合わせて、短納期とコスト削減を実現しています。EOSINTによるコアの造形時間は16時間です。
これらの事例のように、従来の工法やノウハウとEOSINTならではの特長を組み合わせたとき、効果を発揮しています。
EOSINTの事例...金属部品
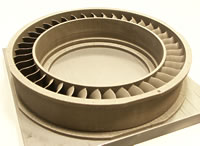
ヘリコプターのタービンブレード
材料の進化によって増えているのが、金属部品の直接造形です。写真9は、ヘリコプターのタービンブレードの試験用試作品です。250℃の環境下、30,000回転で試験されたものです。造形後の処理は機械加工で行っていますが、納期、コスト共に50%の削減を達成したと報告されています。
金属部品製作については、試作に限らず冶具や最終製品まで、適用範囲が拡大しています。
新しい分野
既に最終製品にEOSINT Pで造型したプラスチック部品を活用することについては、No.39でも説明していますが、EOSINT Mによる金属部品についても、ステンレススチール、チタン、コバルトクロムなど、今後リリースされる新材料(発売予定)が可能性を広げようとしています。特に医療業界では、研究や適用が活発になってきています。患者各個人向けに製作するもの、あるいは少量で製作される装置が主な適用分野です(写真10)。NO.38、39でオーダーメイド補聴器、医療用の遠心分離機などEOSINT Pを使用した事例をご紹介しましたが、EOSINT Mに関しても、バイオコンパーチブル金属材料(発売予定)の登場でインプラント治療での可能性がでてくるなど、活躍の場は広がろうとしています。また、医療だけでなく、エアロスペース、コンシューマープロダクツといった業界のニーズに応じる材料が今も開発中です。
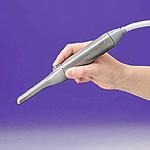
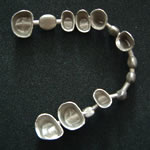
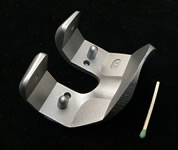
保守部品への適用についても可能性が検討されています。古い金型を処分し、データのみを所有する。必要なときに必用な部品、あるいは金型をEOSINTで製作するというものです。また、データとして設計情報が無い部品をリバースエンジニアリング技術とEOSINTを使って製作するというものもあります。これらの利用法は工法としての有効性だけでなく、結果的に金型の管理費などの削減にもつながります。
最後に
このように金属材料を使用するEOSINT Mも、新たな生産形態のツールとして使用されています。
新しい製造形態e-Manufacturingは、開発・生産コスト削減と、製品のより早い市場投入を実現し、貴社の競争力を向上させる可能性を持っています。
ぜひ、ご検討くださいますよう宜しくお願い申し上げます。