RPシステム部 橋爪 康晃 |
e-Manufacturingとは
EOSが提唱する新しいものづくりのコンセプト。
定義は「迅速に、柔軟に、低コストで、デジタルデータから直接製品を自動的に生産する手法」
はじめに
このコラムでは、3次元CADデータからダイレクトに製品を造形する粉末焼結型RP(ラピッドプロトタイピング)システムEOSINTシリーズについて、ご紹介しています。今回は、最新の活用事例などをご紹介します。
e-Manufacturing パートナープログラム
2005年からEOSは「e-Manufacturingパートナープログラム」を開始しています。目的は、特定のアプリケーションにおける先行的な研究開発、そしてその有効性の実証です。RPを最終製品生産の手法としてより多くの方に認知、採用していただくための課題解決を目指しています。現在4社がe-Manufacturingパートナーとなっています。10台のEOSINT Pを所有するサービスビューローのFKM。ソフトウェアソリューションも提供するマテリアライズ。ウォルバーハンプトン大学。そして、航空宇宙関連製品の開発と生産を行っているモーリステクノロジーズです。このプログラムの研究結果は、今後のEOS製品に反映されていく計画です。
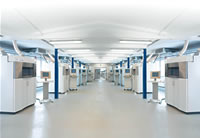
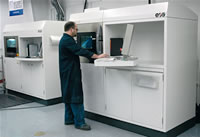
EOSINT Pの活用事例:ウイリアムズF1
2005年、ウイリアムズF1の本社にEOSINTが導入されました。風洞実験モデルを造形するためです。しかし、その後EOSINTは、他の部品製作にも活用できることが再認識され、広範囲での適用が始まります。
ウイリアムズF1は、1987年から光造形機を所有していましたが、造形速度、造形物のもろさ、後処理に必要な手作業の時間、材料が高額であることが問題となっていました。ウイリアムズF1が望んでいたのは、様々な用途に使用できるより強い材料、生産時間の短縮でした。
ウイリアムズF1デジタルマニュファクチャリング部のモジュールリーダーであるリチャード・ブラディ氏は、次のように述べています。
「レーザー焼結部品を使用する前は、モックアップのコンポーネントを光造形で製作し、それを何度も作り直した。扱っているうちに壊れてしまうからだ。しかし、レーザー焼結を適用してからは、一度もそのような失敗は起きていない。レーザー焼結部品は、よく接着でき、より長持ちし、他の工法と比べて交換部品製作に必要な時間も短い。
風洞実験用モデルについては、ブレーキブロック、ミラー、そして他の外装アイテムを現在レーザー焼結で製作し、適用点数も増えています。一方、車両のモックアップ製作でも効果が出ています。数年前まで、1/3スケールモデルは光造形やアルミ、その他の材料で製作されていましたが、現在は、全体がRPによる部品で作られています。2/3スケールモデルもプラスチックのレーザー焼結部品でできています。使用されている材料は、ガラス入りナイロン、ポリスチレン(鋳造用)、アルマイド(アルミが入ったナイロンであり、この材料で作られたものは、金属的な外観を持ち、切削が容易という特長がある)です。
2006年1月27日に公表されたウイリアムズF1の最新モデルFW28のモックアップに搭載されていたほとんどすべてのエンジン部品、ギアボックスは、EOSINT P385を使って製作されました。また、サスペンション、ブレーキなどを含むリアインパクト構造*1、前部および後部のアップライト*2、排気系部品、ヒートシールド*3も同様にEOSINTで製作されています。
*1 リアインパクト構造:衝撃吸収の役割を果たす部品
*2 アップライト:ホイール、ブレーキ、サスペンションアームを取り付ける部品
*3 ヒートシールド:遮熱板
ブラディ氏は、このように述べています。「ボディや電子配線ルーム(ハーネス)などの内部部品は、エンジニアが激しく取り扱うことがあるが、レーザー焼結部品は使用に十分耐えている。
「また、モックアップの品質、外観についても大きな改善ができた。これは、レーザー焼結部品が、ほとんどの場合、完全に勘合するためだ。また、部品を勘合させるための改造に要する時間もほとんど必要ない。」
「このことは我々のレース車両、テスト車両に使われているレーザー焼結部品においても同様だ。現在、8台すべてのFW28間で、自由に部品交換できるようになっている。」今シーズン戦ったすべてのウイリアムズF1 の車両が搭載している約20のノンストレス部品は、レーザー焼結で製作されたものです。これらの部品は、他の工法では、製作が困難であったり、製作に時間を要するものです。代表的な例は、エレクトリカルエンクロージャー、クーリングダクト、アンテナハウジングです。従来これらの部品は、ケブラー繊維を編んで製作されていました。
カーボンファイバー部品の製作には、型を使用しています。これは従来からの生産手法で、リードタイムも数週間になります。しかし、レーザー焼結部品は耐熱性能が不十分であり、このアプリケーションには適用できません。このため、今でも型を用いて製作しています。それでも、カーボンファイバー部品の初期設計段階において、レーザー焼結部品を使って、最終設計が完了する期間を短縮できれば、全体のリードタイムの短縮が可能であり、従来かかっていた改造費用や、型の再製作の費用発生を無くすことができます。
ブラディ氏が好んで話すこのレーザー焼結部品を使ったシンプルな事例は、ドライバーの足の下でシャーシにボルト留めされ、ハイドロリックホースや電子ルームを保持するクランプです。今シーズンの序盤、FW28のハイドロリック系は、次のグランプリまでの1週間以内で、再設計とテストが必要とされていました。このため、その部品に合わせてクランプも再設計し、作り直さなければならない状況でした。
それぞれの車両に合わせて、4種類の異なるクランプを作る必要があり、異なるサイズの扇丈形状部は様々な径のホースやワイヤーを固定し、かつフィットする必要があります。さらにクランプ下部は、コックピットフロアーの形状にマッチするように3D形状に造形されている必要もありました。このような困難な仕事でしたが、8台の車両用とスペア部品用として4種類のクランプは、一夜で完成しました。いくつかあるEOSINTP385の1つを使い、無人で、4時間の造形で、翌朝には準備が完了していたのです。
ブラディ氏は、次のように結論づけています。
「我々は、順調にレーザー焼結技術(EOSINT)を自分たちの生産環境に適用させてきている。そして、その恩恵を受けている。それはコストの低減とCAD画面の中身を現実化するリードタイムの短縮だ。」
「この種類の技術は、一般的にRPと呼ばれる傾向があるが、特にレーザー焼結については、確実に生産に使用できるものであり、RM*4と呼ぶべきものだと考えている。」「私は、このRM技術が従来の生産技術の領域にどんどん進出してくると思っている。この技術の唯一の限界は、その人のイマジネーションであり、CADでモデリングできれば、それを作ることができる。そして、レーザー焼結部品は強度もあり、結果としての多くのアプリケーションで使うことができるものだ。」
*4 RM:
Rapid Manufacturing(ラピッドマニュファクチャリング)の略語。RPということばが試作用途に限定されることから、最終製品にも適用できる粉末焼結技術を区別する場合などに用いられる。
おわりに
EOSは、11月29日よりドイツ/フランクフルトで開催されたEUROMOLD 2006(モールディング製造、機械設備、デザイン、アプリケーション開発のための見本市です)に出展しました。次号では、この展示会の出展内容などをご紹介する予定です。