株式会社ニューテック様は、特殊製法によるアルミニウム・マグネシウムの鋳造部品や真空注形法による樹脂部品のエンジニアリング専門会社として設立され、プラスターモールド工法の短所である機械的強度の低さを特殊工法で解決されるなど、常に技術開発に取り組まれ、新しい分野に挑戦されています。今回は、独自の技術やノウハウによるものづくりツールとしてご活用いただいているEOSINT P385、P390を中心に、製造技術部 課長 市川和義様、製造技術部 主任 宮寺健様、製造技術部 土屋一紀様にお話をお伺いしました。
事業概要
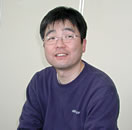
課長 市川 和義 様
株式会社共立という草刈り機やチェーンソーなどの林業機械、農薬の散布や肥料の散布を行う農業機械などを製造販売している会社の100%出資子会社として1987年2月に創立されました。
最初は、商社的な業務から始め、親会社から仕事を受注していましたが、その仕事の中で外注に出すよりも内製化した方が早い部分もあり、社内で注形品を製作するようになりました。親会社で扱う製品は手で持つ機械が多く、軽量化が課題となっていましたので、今まで金属で製作していたものを樹脂化していきました。最初は、ウレタン注形を行っていましたが、親会社の試作に対応するためナイロン注形も始めました。ウレタン注形は競合会社が多く、価格競争になってしまうため撤退し、現在は、ナイロン注形だけを行っています。
砂型鋳物も取り扱っていましたので、アルミニウムやマグネシウムなど非鉄の鋳造も社内に取り込もうと、石膏鋳造も始めました。マグネシウムは、石膏鋳造だけでなく砂型鋳造でもできるのですが、薄肉のものを製作するには石膏鋳造の方が適しています。
親会社からの仕事は、シリンダーやクランクケースなどのエンジン関係が多かったので、親会社の仕事だけでなく、外の仕事も四輪や二輪関係のお客様に営業に行っていました。現在、親会社とそれ以外のお客様からの仕事の比率は1:9くらいです。やはり四輪や二輪、家電関係が多く、製品としては、エンジン回りの鋳物を多く扱っています。EOSINT Pを導入してから、シリンダーヘッドや仕様が少しずつ違う吸排気系のパイプを少量造形することなどにも対応しています。材料はアルミニウムを利用することが多く、マグネシウムを利用したレース用の部品やカバー造形の依頼もあります。また、石膏鋳造はほとんどが手のひらサイズですが、大物も製作してほしいという声に応えています。中には1mを超えるサイズのものを鋳造したこともありますし、他社ではやっていないことにも対応できるようにしています。
EOSINT導入の背景
【さらなる納期短縮を目指して】
お客様から「もっと納期を短縮できないか」というご要望を多くいただき、社内業務においても納期短縮につながる方法やツールを検討しました。試作品を1、2個だけ製作してほしいというお客様からの要望もあり、その解決策は粉末の積層モデルを製作し、それを消失するという方法が有効だと考えたのです。
それまでは、型を製作しないと「もの」はできないので、樹脂を切削してマスターモデルを製作していました。しかし、それでは時間がかかってしまうので、光造形にもトライしましたが、最終的にはシリコンゴムで反転したゴム型を製作する必要がありますから工期がかかり、納期に間に合わなくなってしまいます。
また、光造形品を消失させる石膏鋳造を行ったのですがうまくいかず、材料が悪いのか条件が悪いのか、といろいろ試行錯誤しました。エポキシ系の樹脂を利用するので消失温度が高く、消失時に膨張して鋳型が壊れることもありました。
環境問題も無視できず、エポキシ系を消失するにはそれなりの設備が必要です。ポリスチレンなど環境問題になりにくい材料であれば大丈夫かもしれないと、完成したプラモデルを鋳型の中に入れて消失させたこともあります。
やはり、プラスターモールドの枠を超えた納期短縮を目指し、利用する材料を考慮すると、その解決策は粉末による造形しかありませんでした。システムのワークサイズに収まる範囲内であれば、一度に多数造形できることも光造形と大きく違う利点でした。
【1年間でEOSINT P 2台を導入】
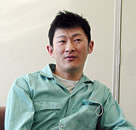
宮寺 健 様
他社のRPシステムも検討しましたが、ポリスチレンが材料として使えるシステム、しかも短納期となると、EOSINT Pしかありませんでした。EOSINT Pの一番の特長は、ダイレクトにものが製作できることです。ダイレクトですから工程が少なくなる=時間の短縮につながります。また、初期設計の段階において画面で3次元モデルを視覚で確認するのではなく、その質感や形を実際に手にして確認できますので、設計者は試作品を確認し、問題があれば初期段階で仕様を変更することが可能です。しかし、高価格だけに、目先の判断だけで導入することはできませんから、最初はサービスビューローさんに造形をお願いし、ある程度のシミュレーションをしました。
ポリスチレンを材料とした造形をお願いするのですが、造形を依頼するのは当社だけではありませんし、ポリスチレンは、あまり頻繁に利用する材料ではないらしく、ナイロンによる造形が一段落するまで待たされることもあり、納期が確定しませんでした。それでは消失鋳造の一番の良さである「納期短縮」を実現することができなくなると考え、今後の需要と社内で十分使いこなせると判断した2006年10月にEOSINT P385を導入しました。導入してみると、試作の性質上、納期が集中して対応しきれないこともあるため、また故障などのバックアップ用も兼ねてEOSINT P390を2007年9月に導入しました。
【生産性の向上を目指して】
EOSINT Pは、扱いやすい面も扱いにくい面もありますが、造形が始まると、途中経過を時々確認するだけで造形が完了します。P385の起ち上げには少し時間がかかりましたが、P390はすぐに稼動しました。P390は完成度が高く、ハードウェア・ソフトウェアともに操作が簡単なシステムだと思います。
P390とP385を比較すると、1日の作業で約1時間、1回の造形で約3時間の差がでますので、この差を生産性の向上に活かせるように、P390の方が早く造形が終わる分作業量を増やし、P385と同じ時間に造形が終了するように工夫しています。
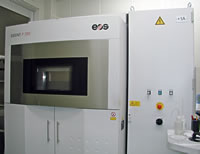
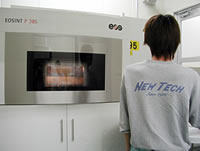
さまざまな技術をEOSINT利用に活かす
【独自工法の確立】
石膏鋳造のノウハウがあったからこそEOSINT Pもスムーズに導入できたのだと思います。EOSINT Pによる造形物の精度に関しては満足しています。もちろんここに至るまでには、いろいろトライアルを重ねましたが、社長自らがいろいろなアイデアを出し、私達にトライさせてくれたのが良かったのだと思います。
現在は、少量の試作であれば短納期で型製作が必要でない消失鋳造、ある程度の数が必要なら石膏鋳造、量産であればダイカスト、というように、お客様のニーズに合わせた工法で対応しています。新規顧客を開拓するよりも、既存のお客様に対して今まで対応できなかったニーズに応えることを優先してきましたので、お客様数は変わりませんが、仕事量は増えたように感じています。「高強度が必要な機能部品を製作する場合、石膏鋳造は砂型鋳造より精度は高いが強度が低いのが難点」というお客様のお声をもとに、高強度の鋳物を製作できる石膏鋳造技術をお客様と共同で開発し、さまざまな技術改善を実現しています。
技術と環境
【長野という環境】
長野に来たのは4年前です。会社が創立された当初は親会社のある青梅に居たのですが、会社の方向性が見えてきたところで製造を行っている工場に近い方がいいだろうと横須賀に移りました。そして、親会社の組織変更で長野に居た部署が移動し、建物にスペースができたため、長野に引っ越してきました。もともと当社は、親会社で設計や実験を行っていた技術部門が独立した会社で、規模も技術力も2度の移転とともに拡大しています。
長野はやはり寒いです。社員は、皆雪が降る地方の出身ではないので、最初は雪の多さにびっくりしたのですが、今では慣れました。寒いですが、その分湿度が低いので鋳造に適していると思いますし、EOSINT Pのシステムと材料を良い状態で保管できます。乾燥すると静電気が問題になるのですが、材料の保管条件が悪いと造形物にも影響がでてしまいます。
【環境問題への配慮】
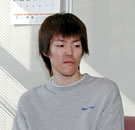
土屋 一紀 様
最近、ダイカストや砂型鋳造、石膏鋳造などで使われていたマグネシウム合金が、環境問題への影響で使用できない場合もでてきました。マグネシウムを利用することに問題はないのですが、強度を高くするための添加物が、ダイオキシンなど環境に影響を及ぼす可能性があるからです。製造上の環境配慮もありますし、お客様から使わないよう指示されることもありますので、問題にならないように気をつけています。マグネシウムの強度をカバーするための合金もいろいろあり、当社では、イギリスのマグネシウム合金メーカとライセンス契約を行い、その会社のマグネシウム合金を使用しています。この合金であれば、問題になる添加物なしで強度を出すことが可能です。マグネシウムを使っている鋳物会社でイギリスメーカの合金を使っているところは何社かあると思いますが、そのほとんどが砂型鋳造用で、石膏鋳造でマグネシウムを使う会社は当社以外あまりないようです。
今後の取り組み
【鋳物の加工にチャレンジ】
鋳物の加工ができるメーカは、非常に少ないです。ブロックからモデルを削り出すことは可能でも、鋳物の加工には技術が必要です。図面の基準と加工の基準は分けて考える必要がありますので、その点をきちんと理解し、経験豊富で信頼のおける会社にしか依頼できません。ですから鋳物の加工をお願いするメーカを探すのは大変です。
当社が加工を依頼している会社には、他社からも当社と同じような加工の依頼が集中するので、急ぐ仕事でも依頼しづらい状況です。鋳物製作までは早いけれど、その先の2次加工で2~3週間とられてしまうと納期短縮の意味がなくなってしまいます。
これからは、社内での加工にもチャレンジし、複雑な形状の加工も行えるようにしたいと考えています。
【今後の課題】
まだ細かい問題はあるのですが、お客様に納品できる完成度には到達したと思います。
お客様にもご満足いただいていますが、現状が当たり前になると、さらなる精度向上の要望がでてくると思います。お客様からの要求が厳しくなるのはこれからですから、それにどう対応していくかが課題です。
また、積層の後をどのように消去するかもこれからの課題です。光造形では削ればいいのですが、粉末積層ではそうはいきません。エンジン部品は一般の人からは見えない部分なので、表面の精度はあまり問題になりませんが、電気関係や家電関係では、表面の滑らかさが求められます。部品は1mmくらいの薄肉なので、モデルには高い強度が要求されますし、表面を仕上げると精度に影響がでる可能性もあります。次の工程である加工にも影響がでますので、どのように処理していくかが、これからの検討項目です。現在は、表面を独自の方法で仕上げているのですが、どうしても手がかかってしまうので、手のかからない方法を模索しています。
モデルの時に手をかけるか、金属になった後に手をかけるかのどちらかですが、やはり積層の精度が高ければ、それに越したことはないと思います。
NDESについて
技術はいつも迅速に動いてくれますし、要点を押さえて説明してくれているので助かっています。
要望としては、まず材料のコスト低減です。やはり値段が高いと思います。鋳造マスターの場合には、材料費が直接費用に響いてくるので、国内での調達など検討してほしいと思います。
それから材料です。最近、EOSINT P用の材料が新しくなりました。静電気に関しては改善されていますし、精度に関しても以前と遜色ないのですが、造形したモデルの強度が以前より低くなっているのではないかと思いますので、さらなる改善を要望します。技術的に解決が可能であれば、提案いただきたいと思います。
また、システムの保守に関しても、部品の交換の費用や日数、部品が壊れたときの補償など、もっと細かくメニュー化してもらえるといいと思います。部品はいつかは交換しなくてはいけませんから、例えば、使用期間などを設定してもらえると、年度の最初に予算を組み交換に備えることができます。
当社は「短納期」を売りにしていることもあり、急に造形の依頼を受ける場合も多くあります。仕事の依頼が重なると、タイトなスケジュールを組んでマシンを稼働させますので、部品交換などでシステムが止まってしまうと仕事が進みません。
粉体という技術をどう利用していくかが、今後の生き残る道になると考えています。今まで以上に充実したサポートや新しい提案を期待しています。
おわりに
企業秘密でお話しいただけない特殊技術をいくつもお持ちでありながら、現状に留まらず常に新しい技術にチャレンジし、お客様からのご要望に応えていきたいという姿勢がお話の端々に感じられました。大変お忙しいところ、貴重な時間をさいてお話をお聞かせていただき、ありがとうございました。
会社プロフィール
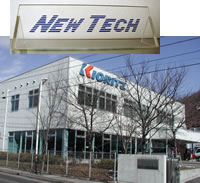
株式会社ニューテック
本社 | 〒381-0101 長野市若穂綿内1136-18 |
---|---|
設立 | 1987年2月15日 |
資本金 | 2,000万円 |
従業員 | 35名(2008年1月現在) |
事業内容 | 自動車部品や電子機器部品など、特殊製法によるアルミニウム・マグネシウムの精密鋳造、試作品の製作 真空注形法による樹脂部品(特に樹脂注形) |
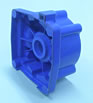
工法で利用する
マスターモデル
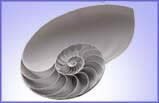

により高い強度を実現
したシリンダーブロック
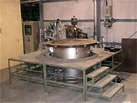
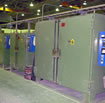