EOSINT P730 とともに挑戦
株式会社栗本工業様は、高価な最新鋭のラピッドプロトタイピング装置を次々に導入して、新技術をいち早く確立された試作専門メーカです。そして、「どこよりも短納期・低コストであること。」「どこよりもハイクオリティであること。」を常に追求され、最新設備とそれを使いこなす技術力により、お客様に付加価値の高い製品をご提供されています。
今回は、市販されているレーザーシンタリングシステムの中でも最も大きいクラスであるEOSINT P730をご導入いただき、造形機による試作のあり方、今後の取り組みなどのお話を中心に代表取締役 栗本英有様、技術G 造形MANAGER 樋口健様にお伺いしました。
栗本工業の強み

当社は、光造形、粉末造形、真空注型、RIM注型、試作金型など、あらゆる工法の試作を作ることができます。今の自動車業界で使われている試作工法を内製できる設備、技術を持っているので、そこが他社と比較したときに当社の強みになります。お客様のニーズに合わせて、試作が1台の場合は粉末造形で、10~20台であれば真空注型、それ以上の数が必要な場合は、金型を起こして試作金型でやりましょう、といろいろなご提案ができます。
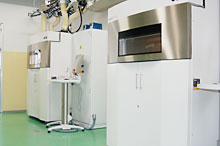
また、営業マンは見積と納期をスピーディに出せるように教育しているので、お客様がいろいろな工法の見積、納期を尋ねられたときに、常に即答できる体制を取っています。
設備の面では、異なるメーカの造形機を複数持っていることも強みのひとつです。光造形機は、主要3メーカの造形機を5台。粉末造形機は、EOSINT P730 2台と他メーカを6台。その他にも金属粉末造形機を所有しています。
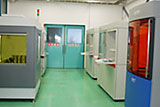
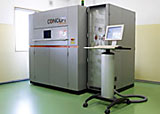
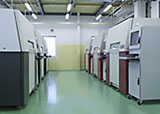
異なるメーカの造形機を使うことで、機能のメリット/デメリットや、メーカの良いところ/悪いところがよく分かります。実際に機械の性能を比較すると、それぞれには一長一短あり、造形する製品に応じて造形機を使い分けることができます。もちろん短納期、低コストを考慮して造形機を選びます。
同じ造形機を購入すれば、他社でも同じようなものができると思いますが、当社は、その造形機をいかに使いこなすかという技術の他にも、造形したものをより本物に近くなるように仕上げにも力を入れています。そういう後工程の仕上げにもキャリアのある優秀なスタッフがいることも強みだと思います。
毎年、スタッフを募集すると若いスタッフを中心に優秀なスタッフが集まってくるので、若手の育成には力を入れています。
毎年、定期的な設備投資
毎年、設備投資は2 億円を目安に行っています。この5 ~ 6 年はずっと続けています。この不況の中、前年度も2 億円の設備投資を行いました。
今年度もまた設備投資をしていきますが、工場のスペースがなくなってきたので、新工場の建設を計画しています。来年には新工場へ移って、そこで設備投資をやっていきたいと考えています。これまでは、ラピッドプロトタイピング(以下、RP)の造形機に設備投資してきたので、これからは、金型設備に同じぐらいの金額を設備投資していく予定です。
やはり、昨年は大打撃を受けて売り上げは5 割ダウンしました。利益も相当ダウンしましたが、設備投資を償却しても黒字を確保できました。それは、前半にいい時期があったからで、全期通して落ち込んでいたらかなりの打撃でした。
来年度も設備投資はしていきます。もちろん、設備を使いこなしていく技術も向上させていきます。
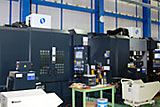
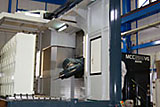
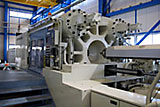
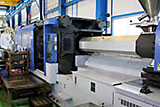
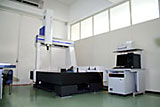
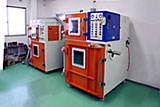
EOSINT P730 の導入
すでに粉末造形機は使っていたので、サイズの大きな大型機がほしかったのですが、他メーカの大型機は未完成状態でした。そこで、EOSINT P730 と比較した結果、EOSINT P730 の方が信頼度は高く、造形サイズも気に入ったサイズだったので導入を決めました。ランニングコスト的にもEOSINT P730 には魅力がありました。
また、EOSINT P730 を導入することで、異なるメーカの造形機を扱えるので、それぞれの造形機のメリット/デメリットが見えやすくなります。まず1 台導入して、すぐに2 台目を導入しました。
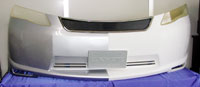
大型機は造形時間がかかるので短納期の対応には難しいため小型機を2 ~ 3 台使って分割して造形すれば納期短縮はできます。ただ、お客様から分割ではなく一体で造形してほしいという要望がある場合は、造形寸法として一番使い勝手が良いEOSINT P730を使います。
EOSINT P730はドイツのEOS社の製品です。使い勝手やアフターのことを考えると日本人の感性に近いのはドイツの製品だと思います。
RPによる試作の発展
試作のもの作りとコンピュータ上でのバーチャルシミュレーションは、いつも技術の追いかけっこです。バーチャルシミュレーションの技術が発展してくると時間がかかる試作はいらないと言われ、試作が短納期でできるようになると、試作を使ってみようかという話になる。
実際、試作が無くなるのではないかという時期が以前にありました。試作メーカから量産メーカへ転職する会社もたくさんあり、試作メーカの数も減りました。そのときに試作が残ったのはRPの造形機が登場したからです。この造形機が登場しなかったら、おそらく試作はここまで発展しなかったと思います。
しかし、これまでは試作の短納期、低コストに貢献してきたRPの造形機も、今はそれが当たり前になってきています。技術はいつも追いかけっこで、他の技術も進化しています。バーチャルシミュレーションの技術が進んで画面だけで確認するだけでいいようになれば、また試作はいらないという時期がきます。ですから試作の技術も進化していかないといけないのです。
いつまでも造形機に頼っている時代が続くとは思っていませんが、今の技術の中では、短納期で一番簡単にものができるのです。造形機に頼ってばかりいると新しい技術を見逃すので、常に新しい技術に目を配るようにしています。
より付加価値を高める
当社のお客様は、自動車が9割で残りの1割が家電、住設、アミューズメント関係です。この経済危機で自動車業界以外への業種のシフトも考えましたが、されど自動車というところはありました。あれだけの部品点数と製品の大きさは自動車以外では難しいと思います。今は、たとえ自動車メーカ様の経費削減で仕事が少なくなっても、それに取って替わる業界はないのではないでしょうか。
しかし、いつまでも同じことをやっていては、だんだん仕事は無くなってきます。同じ造形機を使った造形品でもいろいろな工夫をして付加価値を高めていかないと、「造形機で作りました。」だけでは、こんな試作は無くなっていきます。お客様から依頼され費用を払っていただくかぎり、その費用に見合った試作品の価値を高めていかないと依頼が減るでしょう。
やはり、コストが高い、納期が遅いというのは論外です。当然精度が良いという条件のもとでスピードが速いのか、あるいはすごく安いのか。それとも両方なのかという価値を高めていかないといけないのです。
確かに試作の仕事量が半減して業界全体が打撃を受けていますが、本当に技術があるところは、こういう経済危機がきても生き残っていけると思います。
正規の量産品に限りなく近い試作品
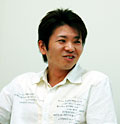
MANAGER 樋口 健 様
お客様は、試作品として正規の量産品と同じ本物を求めています。今の技術で本物を作るのには、金型を起こして成形する必要があり、納期、コストがかさむため、今は、短納期でできる造形機で対応していますが、欠点は正規材料でないということです。見た目、さわり心地は手仕上げで本物のようにできますが、材料の物性自体は変えられません。本物の正規材料の物性でなければ、いろいろな試験に使えないのです。
今後は、いかに量産の正規材料に近い物性にできるかだと思います。もちろん、さわり心地、見た目も重視して、短納期、低コストでご提供していかないといけないのです。そのためには、造形機メーカに努力してもらって本物に近い物性の材料を開発してもらう必要があります。これは最優先で取り組んでいただきたい。そうすれば、試作としての価値もあがってくると思います。
究極は、正規の量産と同じものを造形機で作ることです。それには、造形機で本物の材料が使えるようになることは必須です。そこまでやっていかないと試作自体の意味がなくなり、衰退していくと思います。
1品だけでも本物ができるのであれば、お客様に重宝していただけます。さらに、この本物をより短納期で作る技術を確立すれば、試作は当分の間生き残っていけると思います。
電気自動車の普及
先進国で自動車は普及していますが、将来的にはアジア、アフリカでの自動車の普及が増えてくるので、自動車の時代は当分続くでしょう。やはり、人の移動手段として自動車は便利だと思います。
将来的に環境面で温暖化への対策として100%電気自動車が普及していくでしょう。燃料のガソリンから電気への移行は世界的な流れだと思います。
電気自動車になると、ガソリン関係の部品が不要になるのでエンジンなどの機能部品は減り、燃料電池関係の部品に代わるため、それに関わる試作の依頼もあると思います。
タイへ進出
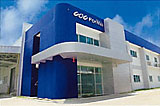
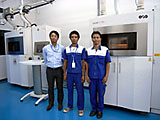
EOSINT P390とスタッフ
タイで粉末造形サービスを始めようと計画して、当社とCBC株式会社で出資したCBC Forma Co., Ltdを2008年7月に設立しました。この計画の後に今回のサブプライム問題、リーマン・ショックにより景気が悪化したので出端をくじかれましたが、1年間延期になっていた工場の開所式を2009年5月に行い本格的な稼働を始めました。
まだ採算は取れていませんが、今後はタイでの2輪、4輪の試作需要が期待できるので、徐々に仕事が増えてきています。
CBC Forma Co., LtdにはEOSINT P390を2台導入しています。
NDESへ
試作業界は、もともとニッチな世界です。今以上に造形機がどんどん売れて、造形機のサービスビューローが増えていく状況ではないと思います。
光造形、粉末造形など、どの造形機でも、新規で台数が増えることは今後期待できないと思います。新規の販売よりも、今よりも使い勝手がよく優れた造形機を提案し買い替え需要を促進するのです。そのためには、今の造形機よりもスピーディでより綺麗なものができる造形機を作ることです。そして、ある程度コストを安くすることが必要だと思います。
今、インクジェット方式の低価格な機械が進歩してきているので、これでいい材料が出てくると、すぐに高額な造形機は取って代わられると思います。
造形機、材料もそうですが、低価格にするという努力をしてもらいたいと思います。
また、情報交換の場が必要です。メーカさん主催の情報交換の場はありますが、メーカさんの枠を超えて同業者の人たちと造形機や材料などの情報交換の場が持てたらといいと思います。
おわりに
「技術はいつも追いかけっこだから。」と淡々と語られる栗本社長。常に将来を見据えた高額な設備投資、最新技術の修得は、試作専門メーカとして生き残る術を追求していくという強いパワーを感じました。2台のEOSINT P730だけでなく、数多くの造形機が整列したところを見学したのは初めてでした。
大変お忙しいところ、貴重な時間をさいてお話を聞かせていただき、ありがとうございました。
会社プロフィール

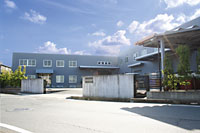
株式会社 栗本工業
本社 | 〒491-0834 愛知県一宮市島崎1丁目14番5号 |
---|---|
設立 | 平成2年9月 |
従業員 | 50名(平成20年12月現在) |
営業品目 | 自動車用樹脂部品(試作)、設計・光造形品・粉末造形品・金属粉末造形品・真空注型品・金型・成形品、その他試作関連全般 |