三菱重工業株式会社 原動機事業本部 高砂製作所様は、三菱重工のなかでも大型回転機械専門工場として大きな特長をもった事業所です。エネルギープラントの生産拠点として、高度な技術力を活かし、暮らしや産業の基盤となる電力を産み出すガスタービン、火力・原子力プラント用蒸気タービン、水車、ポンプなどを世界中に送り出すことで、世界中の人々の豊かな暮らしを支え、地球環境の保護に貢献しています。
このタービンに取り付ける部品として燃焼器や翼があり、耐久性を向上させるためにセラミックコーティング加工を行っています。今回は、セラミックコーティング加工でのROBCAD/Paintの運用と効果、そして今後の課題などのお話をお伺いしました。
高砂製作所の概要
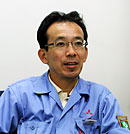
ブレード・燃焼器製造部
部長 川合 渉 様
高砂製作所は、大型回転機械の専門工場として1962年に操業を開始しました。
時代の流れに沿って製品が少しずつ変化しています。最初は火力発電用蒸気タービンからスタートして、日本で原子力発電所の国産が増え始めるという時代を経て、今ではガスタービン、あるいはGTCC(ガスタービン・コンバインドサイクル)というガスタービンと蒸気タービンが合体したシステムがメインになっています。
生産高の比率は、ガスタービン63%、火力/原子力タービン27%、水車2%、ポンプ4%、他4%です。いずれもエネルギー関係の発電機器になります。
発電するためのエネルギーは、天然ガスによるエネルギー、原子炉によるエネルギー、水車によるエネルギーなどの違いはありますが、電力事業に関してさまざまな回転機器の製品を納めています。
主なお客様は、国内外の電力会社様、自家発電をされている事業体様になります。
ガスタービンの新製・交換部品
これまでは一品受注のような仕事が多く、例えば、原子力発電所のタービンなどは非常に大きなもので工期も2~3年かかっていました。お客様にご注文をいただいてから1品ごとに独自設計して作り上げていくような工事です。ところが今の主力であるガスタービンは、年間36台規模で新製している製品です。また、この製品の燃焼器や翼は寿命を持った部品のため、決められた期間でお客様に交換していただく必要があります。この交換部品と新製部品を合わせると年間およそ90~100台になります。
工場の考え方として、原子力発電所のタービンを2年かけて1台作っていた工場から、中量産的なガスタービンのような100台分の部品を作る工場へと形態が変わり、中量産的な製品をより効率的に作ろうということで去年の4月に製造部が2つに分かれました。
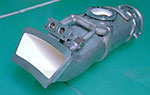

第1段動翼
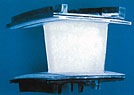
第1段静翼
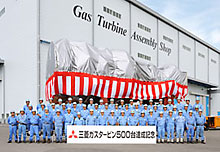
我々のブレード・燃焼器製造部では、蒸気、燃焼ガスなどを受けてロータを回すための翼や、ガスタービンのガスを燃やす燃焼器の部品を作っています。
1963年にガスタービン第1号機を出荷し、今年の7月に累計出荷台数500台を達成しました。
今後も継続的にガスタービンをご注文いただけると、燃焼器、翼をメンテナンスする台数は毎年少しずつ増えてくるという状況になります。このような状況を受けて工場の拡大や設備の導入を定期的に行っており、2008年の秋にアメリカのオーランドに翼を製造する工場を新設しました。また、横浜製作所の中にも翼を製造する工場を建設中で2010年春に稼働予定です。今後、100台が150~200台に増えることを予測すると、生産性の向上はこれからの大きな課題だと思います。
実用化に向けROBCAD/Paintを採用
■採用のポイント
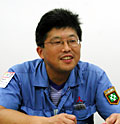
ブレード・燃焼器製造部
生産技術課 TMDIチーム
主席チーム統括
工学博士 原口 英剛 様
工場の生産性をより上げるためには、コーティングプログラムの検討期間を短縮することが必要だというニーズの中で、コーティングシミュレーションを検討することになりました。そこで、導入しているROBCADだけでなく、他のソフトも含めて同じ評価ポイントで比較しました。例えば、膜厚シミュレーションの精度、試験的に出した膜厚分布を計算に流用できるかなど、技術的なインプット、アウトプットを比較した結果、他より優位と判断してROBCADに決めました。また、カスタマイズが簡単にできることも決め手となりました。
以前は、導入支援を受けずに独自で実用化に取り組んでいましたが、今回はNDESから提案があり、事例の紹介とノウハウを教えてもらうことにしました。これでROBCADの使い方のコツなどを教えてもらいながら、ノウハウを取り込み実用化に向けてのプログラムを作ることができました。
■燃焼器と翼のセラミックコーティング
燃焼器、翼には白い部分がありますが、ここにセラミックを300~500ミクロンでコーティングしています。この燃焼器と翼の設置場所は、1400~1500℃の高温燃焼ガスの中です。金属は1500℃では溶けてしまうため、金属の温度を下げるために熱伝導を調整する必要あります。そのため燃焼器と翼にはセラミックの粉をプラズマガンで付着させています。このセラミックは熱伝導が小さいので、ガスの熱を金属側に伝えにくくする効果があります。ところがこの厚みが均一ではないと、厚すぎる部分は耐久性が劣り、逆に薄すぎると期待する効果が得られない。
このセラミックコーティング加工では、プラズマガンをロボットが持ち回転テーブルにセットした対象物にセラミックを溶射していきます。ROBCAD/Paintは、このシミュレーションとオフラインティーチングに利用しています。
以前は、人がロボットを操作してコーティングの位置を決めていました。オンラインティーチングと言って、ロボットを少しずつ動かしながら、ポイントをロボットに教えます。ティーチングした後は、ロボットがコーティングの作業をするのですが、均一な厚みになかなかできないのです。薄い部分、厚い部分、コーティングしていなかった部分があると、その度に人がロボットを操作し修正していたので、設備が変わったり、部品が新設計されると大変な作業でした。
均一にコーティングするには、プラズマガンを対象物に一定距離で面直(90度)に当てる必要があります。コーティングする形状の違いもありますが、人が教えていくと距離や面直は感覚的なものになってしまいます。そこにROBCAD/Paintのシミュレーションを使うことで、品質の向上を狙っています。
ROBCAD/Paintによる効果
■面直や溶射距離の精度向上
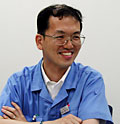
ブレード・燃焼器製造部
生産技術課 TMDIチーム
主任 吉川 順偉 様
プラズマガンと対象面との溶射距離をグラフで表わすと、人がオンラインティーチングしたものは上がったり下がったりが多く、グラフはデコボコになりますが、3次元データのROBCADでは、決めた距離はキープできています。
また、形状に依存しているため面直にできない部分は、どの角度であれば均一に付着できるのかを考慮する必要がありますが、角で曲がっている部分などプラズマガンが真直ぐに入らない場合でも、ROBCADではシミュレーションでのトライ&エラーにより膜厚を一定に保つことができます。
このように従来、人が手でやっていたオンラインティーチングでは膜厚にムラがあったため、膜厚の薄い部分だけを別のプログラムとして追加で作っていましたが、ROBCADでは、プラズマガンの角度や溶射距離を安定させることができるので、膜厚のムラを極力抑えたプログラムを作成できるようになりました。
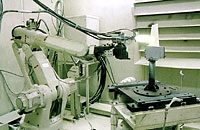
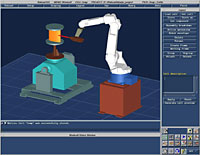
左側:ロボット実機
右側:ROBCADシミュレーション
■大幅な工数の削減
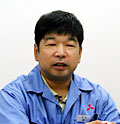
ブレード・燃焼器製造部
生産技術課 TMDIチーム
西 一郎 様
これまでは、ロボットの適正プログラムを作成するには、実機でのトライ&エラーを繰り返して4~5回の追加溶射をしていましたが、ROBCADを使うと2回で済むようになりました。期間的には、人が手で作っていたときは約60日かかっていましたが、ROBCADでは約10日でできるようになり、大幅な工数削減につながっています(図1)。
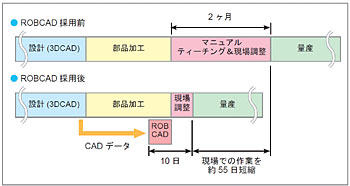
必ず溶射テストを1回行うので、ゼロにはならないのですが、今の2回を1回にしたいと思います。溶射テストが1回になると期間の10日も短縮できる可能性があります。そのために角度、距離の影響による膜厚分布の変化の研究に取り組んでいます。それができれば、膜厚シミュレーションの精度も上がります。将来的には、机上でシミュレーションを確認した後は、現場で修正することなくプログラムが使えることを目指しています。
■複雑な3次元形状にも対応
翼の3次元形状が複雑になってきたのでROBCADでなければ、かなり苦労したと思います。曲率の大きな部分にロボットを回り込ませると、速度が落ちてセラミックを多く溶射してしまうため膜が厚くなり、割れが発生する原因になります。そこをいかに速く回すのかということがキーポイントです。スピードの問題はロボットの実機にも要因はあるので、それは今後の課題です。
■設備の完成前に事前準備が可能
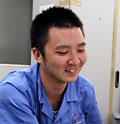
ブレード・燃焼器製造部 生産技術課 TMDIチーム
小牧 孝直 様
工場が変わったり設備の導入時期が異なると、少しずつデータが違います。計画寸法は同じでも微妙に誤差があるので、誤差はキャリブレーションで埋める必要があります。そこが重要です。ロボットから見てマークがどの位置にあるか、外部軸が傾いているかなど、個体差があればキャリブレーションで合わせ込んで変換します。このように、シミュレーションで作ったプログラムをマスターにしてキャリブレーションすることで、別の工場へ展開するときの負荷をかなり削減できます。ROBCADがなければ、工場が完成し設備ができた後でなければプログラムの準備ができなかったのですが、これからは設備が完成する前に準備ができます。今も、横浜工場の事前準備に入っています。
さらなる効率化への課題
■データベースに蓄積
プラズマガンを斜めにしたときの付着度合や、平面の中央と周囲の付着量など、ちょっとしたプラズマの発生具合によって、プラズマの温度分布やスピード、粒の数も変わり面積の広がり方も変わります。条件によって付着する分布を持っているはずなので、面直に当たったとき、斜めに当たったとき、カーブした部分などの状態をデータベースに蓄積して、反映できれば次のステップアップにつながります。
NDESへ
これから工場を増強して立ち上げていくには、ROBCADがさらに必要になり3本目を追加導入したばかりです。今後、さらに増設する場合、価格がもう少し安くなってほしいと思います。
NDESには、導入後の立ち上げ支援でお世話になりました。今後も研究していく中で、我々だけではどうすることもできない状況になった場合、NDESに支援をお願いしたいと思います。
おわりに
ガスタービンの組立工場を見学させていただき、重量300トン、部品点数約7万点というあまりの大きさに、ただ圧倒されるばかりでした。また、敷地内には、ガスタービンなどの製品がオブジェのように配置されていたので、その大きさを間近に感じることができました。
大変お忙しいところ、貴重な時間をさいてお話を聞かせていただき、ありがとうございました。
会社プロフィール
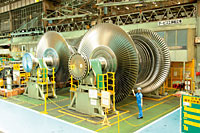
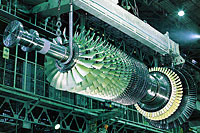
三菱重工業株式会社 原動機事業本部 高砂製作所
本工場 | 〒676-8686 兵庫県高砂市荒井町新浜2丁目1番1号 |
---|---|
操業開始 | 1962年10月 |
資本金 | 2,000万円 |
従業員 | 本工場 4,028名 岩内工場 3名 三菱重工東方ガスタービン 142名 オーランドサービスセンター 503名 高砂研究所 406名 (2009年4月現在) |
主要製品 | ガスタービン、火力/原子力タービン、水車、ポンプ |