―あらゆるお客様のニーズにお応えするために―
![]() |
---|
![]() |
昭和精工株式会社 代表取締役 社長 木田 哲朗 様 |
---|
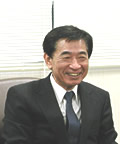
代表取締役社長
渡辺 雅治
渡辺 昭和精工様は、最新の設備を揃えられ、品質を重視したものづくりをなさっています。
本日は、木田社長に事業概要や得意とする技術力などについて、お話をお伺いしたいと思います。
創業から55年
木田 1954年に東京の大森で創業し、設立5周年を迎えました。
創業者は父親で、設立当時は、電線、管、棒を成形する超硬合金を素材とした引抜き用のダイスという精密工具を製作していました。
このダイスには金属の表面を鏡状に磨くLAP技術が使われており、その技術を展開・応用して、現在は精密プレス金型の設計製作を行っています。
さらに、その金型の技術を使ってリチウムイオン電池の電極箔を成形するロール成形機やフライアイレンズを自動磨きするLAP-UPマシンなどの専用機も開発・製作しています。
LAP-UPマシンは、プロジェクターに使われているフライアイレンズという複眼のレンズを作る金型を磨く自動研磨装置で、このような専用機も手掛けています。
創業当時は父親の話によりますと、戦争による社会的にインフラが整っていないときで、破壊された電線などを整備するのに、ダイスの需要が多くあったそうです。
国道沿いに工場があったそうですが、そこを往復すると仕事がいただけたようです。
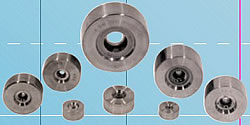
ダイスは、摩耗に強くないといけないので超硬材という非常に硬い材料を機械加工します。
また、引抜く際に抵抗を少なくするために鏡のように磨く技術も必要です。
機械加工の技術と金属を磨く技術、なおかつ高度な寸法精度の必要がありますので、精度を管理する技術がダイスにも求められていました。
その技術は今でも当社のコア技術として連綿と続いています。
その後、将来の発展性を考えて、ダイス製作の技術を活用して金型の製作に取組みました。
渡辺 金型の製作に取組まれたのは、いつ頃からでしょうか。
木田 創業から15年目の1970年です。先代の社長はもともと自動車メーカーの工機部で金型に関連する仕事をしていましたので、ゆくゆくは金型を製作したいという思いがあったと思います。
国際見本市でファインブランキング金型に出会って、ダイスから、ファインブランキング金型の設計製作にシフトしたという経緯があります。
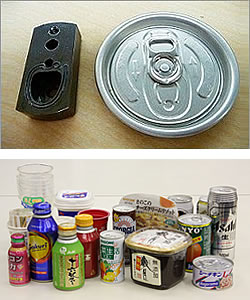
ファインブランキング技術は自動車関連等で多く使われる工法ですが、同時期に缶ビール、缶コーヒーなどの缶を作る金型を作り始めました。
従来、瓶が主流でしたが、大阪万博で缶コーヒーが見本で配られ、飲料缶が大きな話題になり普及のきっかけとなりました。
その当時、製缶メーカー様から当社に缶の金型をやらないかという話がございまして、製缶用の金型も手掛けるようになり、現在もずっと続いています。
金型をやり始めたころは、お客様からのご要望があって、金型と名前のつくものであれば何でもお受けしようと粉末冶金や射出成形用金型なども製作したこともあります。
お客様のご要望があればそれにお応えしたいという思いがあります。
金型はサポートインダストリーと言われていますので、当社はお客様のものづくりをサポートし、お役に立つために当社ではできないことでも、協力会社にご協力いただいて昭和精工から総合的なサービスをご提供するという、良い精神が今も続いています。
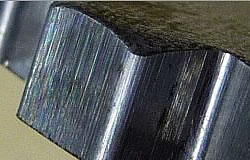
渡辺 大阪万博の缶コーヒーのお話がありましたが、自動車部品はどういうものを扱われていたのですか。
木田 当時はディスクブレーキのブレーキパットで、板状の5~7mmの板厚のものを打抜くファインブランキング金型の製作が多くありました。
現在はトランスミッション金型の製作に移行しています。
精度の追求
渡辺 どちらも複雑さ、精度が求められる製品ですね。
木田 常に精度を追及してきました。創業当時の大森から保土ヶ谷に移り、その当時はスレートの工場でしたが、一部屋コンクリートで恒温室を作って、測定機を入れて検査を行っていました。
概観はスレートでも中に恒温室を作って、精度にこだわっていました。
ホームページにも「あくなき精度への追及」と掲げていますが、昭和61年に現在の横浜金沢区に移り、このような建屋になったからということではなく、創業当時から精度を追求するという姿勢で取組んできました。
ここに移転してきた当初は、管理棟と工場棟でしたが、平成4年に4階建ての研究開発棟を増築、平成17年にはトライ用のプレス成形機を導入するために、研究開発棟B棟を建てました。
金型は技術開発的な要素が強いのですが、今までは、お客様の要望を満たすためにお客様と当社との間で技術開発をし、いろいろな金型の技術を高めてきました。
今後は当社独自で技術開発をして、それをお客様にご提供できるようにしたいという思いがありまして、トライプレスの設備を導入しました。
工場内は金属の膨張、収縮による寸法変化、加工精度への影響、防錆対策のため集中管理システムにより、常に一定の環境を保持しています。
防塵対策として精密加工室前に前室を設け、出入り口に二重扉を採用し防振構造の建物となっています。
熱交換器を介し、新鮮空気をとり入れたり、高窓による自然採光をいれるなど健康面やエコに対する考えも取り入れています。
新たな分野への取組み
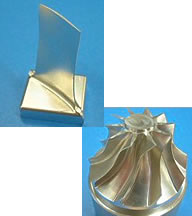
渡辺 航空宇宙の分野にも取組まれているようですが、これはいつ頃からでしょうか。
木田 航空宇宙は新しい分野で、5年前です。
航空機用の部品は、独特の複雑な3次元形状ですので、5軸のマシニングを導入し、タービングブレードなどの、航空部品で難作材の部品加工や薄物試作品、医療関連の人工骨など高精度の5軸加工にも対応しています。
この金沢工業団地にも、航空宇宙関連の企業も多く、今後も取組んでいきたい分野です。
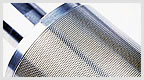
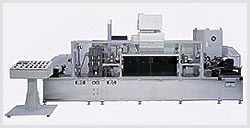
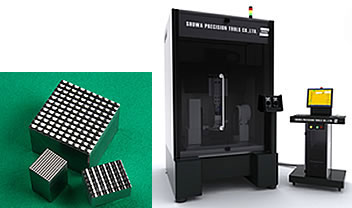
LAP-UPマシン「KENMA」(右)
金属箔ロール成形機というのは、リチウムイオン電池の中にある金属箔に無数の細かい穴加工をする自動機で、多くの電気をためることができる箔を成形する装置です。
ロール成形製法は従来より、高い生産性を実現しています。
今後は、ハイブリッドカーや電気自動車により、リチウムイオン電池の需要が伸びると言われていますので大きな期待をしております。
当社のLAP-UPマシンで成形されるフライアイレンズはプロジェクターに入っている光を均等に拡散させるレンズですが、今後は、環境ビジネスである太陽光発電集光用レンズやLED の反射板に応用するなど新しいマーケットに対する研究開発も進めております。
これらも金型を作る技術を応用展開したものです。
今後の取組み
渡辺 容器関連の受注量は安定していると思いますが、自動車関係はいかがでしょうか。
木田 リーマンショック以降、受注量が従来の3割という状態が続きました。
当社は、昨年の3月ぐらいから自動車関連の受注が落ち込みましたが、秋口からは少しずつ受注が増えてきています。
このような極端な落ち込みは、バブル崩壊のときもありました。
バブル崩壊の時は500mlのペットボトルが新製品として出てきたことも重なり、缶の需要も大幅に落ち込みました。
現在は生産量としてはペットボトルの方が多いのですが、缶はビールやコーヒーなど需要はありますし、リサイクル性、保存性、冷やすのにも効率がいいので需要は安定した状態です。
バブル崩壊後、当社が持っている技術を何かに活かせないかと、微細加工、ロール成形機、LAP-UPマシンなど専用機の開発に取組み、徐々に景気が回復してきていたのですが、その後リーマンショックで再び大打撃を受けました。
リーマンショック前に、さらなる発展性ということを考えて、中期経営計画を立てたのですが、リーマンショックの影響により、残り1年を残して、現在は、新しい中期経営計画で新しい経営戦略に取組んでいます。
【海外戦略】
木田 基本的スタンスは、お客様とよくコンタクトを取って、お客様のご要望をお伺いしてそれに応えられるようにしていくということです。
新しい中期経営計画にありますが、今後は、海外市場を目指すということで、昨年はドイツのEUROMOLDに出展しました。
弟の副社長が営業部を管理しておりまして、海外戦略に取組んでいます。
海外への展開は従来から考えていましたが、リーマンショックの景気後退を受け、さらに加速して海外展開をし、海外から仕事を多くいただけるようにと動いております。
その戦略の一つとして森鉄工様のファインブランキングプレスを導入しました。
当社自らが海外に行ってお客様を開拓していくというところは、まだまだ対応力が弱く、森鉄工様とタイアップしてお客様に当社をご紹介していただき、需要を取込んでお互い良いコラボレーションになるようにという判断があります。
森鉄工様は海外にもプレスの機械を納められていまして、プレスの機械にはもちろん金型が必要ですし、当社でトライもできますのでお互いの利点になれるようにと考えています。
渡辺 海外に拠点を作るという話はよく伺いますが、このようなコラボレーションの話をお伺いしたのは初めてです。
木田 お客様とご一緒にという形ではないのですが、日本から海外に昭和精工のブランドを発信するという形です。
海外戦略として昨年の9月に英語版のホームページもリニューアルしました。
渡辺 海外でのお客様は日本企業というわけではないでしょうから、言葉の問題が大変ですね。
木田 言葉の問題は大きいと考えています。
現在、社内で英会話セミナーを立ち上げまして、35名の希望者が研修しています。アレルギーをなくすという意味でもいいのではないかと思っています。
人材育成
渡辺 ホームページを拝見すると、『優れた人材の確保と育成』、『優れた製品を生むための設備と環境』、『厳しい品質管理』という3つのキーワードがございますね。
木田 社是は、「事業は人なり」です。人の成長なくしては、企業の成長はないという思いがあります。
事業を支え発展させるのもそこに働く従業員の努力ですし、仕事に取組む姿勢で事業の拡がりができます。『従業員を大切にし、その力が発揮できる職場環境を大切にする』という姿勢です。
技術研修については、年間教育計画を立てて、スキルマップを作成し、OJTで研修を行っています。
仕上げ、磨きに携わる技術者の場合は10年おきに配属し、教育方法も、40代の人が30代の人を教え、30代人が20代の人を教えるというように、技術が伝承できる仕組み作りを行っています。
社内設備は最高性能の設備を導入して技術力を活かすインフラと、職場の中も広々とした空間作りを行い、柔軟な発想ができる環境にしています。
このように、技術面では、技術の伝承と技術力のアップが図られるような仕組みづくり、文化ができあがっています。
一方、階層別ではベースになる人間力をもう一段高めるような研修をしたいという思いがあります。
今は、個別に外部研修機関に受けに行くのですが、習ってきたことを実践するのに統一性がないように感じていまして、同じ時期に同じ空間で研修を行えるようにしていきたいと考えています。
階層別の研修では、自分で発想する力などをもっとスキルアップしていきたいですし、新技術を作りあげていき、会社全体の視点で改善をしていくなど、プロジェクトマネージャとしての知識も必要になりますし、それらを総合して経営的な視点の教育も必要になると考えています。
英会話教育は、社員には無料で参加できる仕組みを作っています。
技術面と階層的な研修と相乗効果を生めるような仕組みづくりを図っているところです。
渡辺 研修はOJTをいかに補完するかということだと思っておりますが、マネージメントの教育は、外に刺激を受けないと社内では難しいですね。
私は教育の中心はOJTだと思っていて、OJTで部下をどううまく育てるかが一番のキーだと思います。
木田 社外で勉強して他社の人と触れあうメリットもありますので、そういうところは残して、社内に外部から講師に来ていただいて、組織的に教育を行い、OJTの際に、教える方のレベルを上げて、それから教わる人を育てていくという、OJTとOFFJTを合わせた良さを教育で行っているところです。
渡辺 QCサークル活動も取組んでおられるのでしょうか。
木田 QCサークルというわけではないのですが、現場改善という意味でアイデア展示会を実施していまして、各職場で創意工夫したことを発表しています。
渡辺 方針展開で、施策方針を各マネージャまでおとしていかれているのでしょうか。
木田 当社では、3年間の中期経営計画を踏まえて年間の部門別戦略計画を立てます。
それを各部署のグループに落とし込み、さらにグループ内で個人の行動目標を立てて、週に1回チェックするという形で展開しています。
技術を伸ばしておけば販売につながったという時代もありましたが、今は顧客ニーズ、海外のニーズなど情報合戦のようなところもあると思いますので、そういう視点に立って戦略なども立てています。
ただ、急に外国から仕事が入ってくると、図面も日本のものと違い、現場では抵抗感があります。
そういうところを変えていきたいですし、いろいろなことに柔軟に対応できるマネージメント力も養っていきたいですね。
品質管理
渡辺 技術を高めるため、新たな研究開発のために、いろいろな設備を導入されていますね。これは設立当初からのお考えでしょうか。
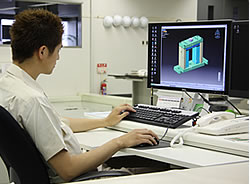
木田 精密加工、生産性という点では、設備の力は非常に大きく、金型メーカーは設備力に依存するところがあります。
人が持っている技術力を活かすインフラ設備が整っていないと顧客ニーズに応えていけませんので、絶えず設備を見直しするという必要性があります。
渡辺 一方では、どのようにして稼働率を上げるかという課題もあると思いますが。
木田 それは当社の今の課題です。機械を導入するにあたっても過去は順調に仕事がありましたが、今後は、マーケティングなどよく吟味して導入しなければならないと思っています。
昔は、熟練加工者が手作業でやっていましたが、NCになりますと機械の精度に依存しますから、効率の悪い機械の見直しも必要です。
渡辺 金型の設計から製造までの品質管理の手法は、どのようにされていますか。
木田 品質については、ISO9001の規格にのっとり品質マニュアルを作成して実施しています。
品質を一番重要視していまして、今期も「絶対品質」ということで、「顧客クレームゼロ」を掲げています。
これまでは、品質保証は製造課で検査という部署で行っていましたが、それでは品質保証という意味からして弱くなってしまいますので、品質保証室という新しい部署を作り、そこで全体の品質を見るということで品質保証体制を新たに立ち上げたところです。
各現場では、後工程に不良なものは流さないという仕組み作りをしていますので、非常に検査器具が多くあります。
2008年の検査時間の集計では、生産時間の18%を検査に使っています。品質保証室には5名を配置しています。
自分たちが作っている製品がどの程度の精度で作れているのかということを把握しないと品質を高めていけませんので、検査に費やす時間を多く使っています。
渡辺 御社は、検査に費やす時間がどれくらいかを分析されており、きちんと管理をされていると感じます。
木田 このようなデータを取るということ自体が大変です。
生産性を見るためにDr.工程を導入していますので、データを取って分析できるようになっています。
NDESに期待するところ
渡辺 弊社に対して、ご意見ご要望などございましたらお聞かせください。
木田 当社では、一番重要な部分であるCAMにおいてSpace-Eを使っていますし、設計では、CATIA V5を使っています。CATIAは、今までと違って非常に複雑な形状を設計する際に使っています。
今までに比べ、金型の構造が複雑化していますし、金型によって立体的な部品を作るという点においても、3次元CADは使いこなす力をつけていかなければならないと考えています。
渡辺 導入していただいた後に、さらなるステップアップとして、お客様が現状どうされているか、今後何をされたいのか、やはりキャッチボールをする必要があると思います。
ヒアリングをさせていただいて、弊社からこういうことをしてみませんかと、提案をさせていただくようにしたいと思っています。
木田 システムを導入する側の立場で難しいと感じるのは、CATIAのように世の中で実績があり、お客様が使っているものであれば、リスクが低く、価格が高くても導入しやすいのですが、開発しなければならないソフトウェアであったり、社内の改善のために投資するソフトウェアの場合は開発前に内容がつかみにくかったり、導入して果たして結果が伴うのかということ、導入後に社内に浸透するのかどうかも判断がつきにくいのでリスクがあり、敬遠しがちになりますね。
機械に関しては、実際にテスト加工をした製品を検証すればわかりますし、パッケージのソフトもデモを見ることができます。
開発型のソフトウェアには開発をしないと成果物がありませんから、GOをかける難しさがあると思います。
渡辺 新たに導入するときは、検証しないとだめですね。業務フローがどうか、生産性が上がるかなど弊社がそのようなことをご提供しなければならないでしょうね。
木田 人がすごいところと、システムが強い部分と、「人」と「システム」の棲み分けが使う側には重要になってくるのでしょうね。
渡辺 計算時間やデータの連動などはシステムに任せるところですが、使う側は人ですからね。
お伺いしたことにお応えできるようにしたいと思っております。
いろいろ頑張りますので、これからもご指導いただければと思います。
本日は、お忙しいところを誠にありがとうございました。
会社プロフィール

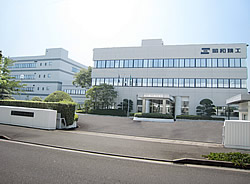
昭和精工株式会社
URL http://www.showa-seiko.co.jp/(外部サイトへ移動します)
創業 | 1954年(昭和29年)1月 |
---|---|
所在地 | 神奈川県横浜市金沢区福浦1-4-2 |
資本金 | 8,000万円 |
社員数 | 85名 |
事業内容 | 精密プレス金型、精密樹脂金型等、金型の設計製作、精密治工具、自動化機器、専用機の開発、設計製作 |