RPシステム統括部 営業グループ グループマネージャ 橋爪 康晃 |
RP は生産ツールになった
一般的に使用されるようになったRPシステムは、その名が示す通り、試作品を製作するための技術として登場しました。そして、安価で導入しやすい3Dプリンタの登場やEOSINT/FORMIGAを含むハイエンドRPシステム用新材料の登場などの背景もあり、この数年で普及が進みました。さらにRP技術への理解が深まったことで適用範囲も広がり、もう「試作品を製作するための技術」に用途を限定しない身近なツールになったと言えます。このような現状を受け、RP技術は「Additive Fabrication=付加的製作手法」または、最終製品も製造できる技術として「AdditiveManufacturing」という新しい名称で呼ばれるようになりました。
今回は、EOSINT Mの適用事例をいくつかご紹介いたします。
量産用金型インサート
EOSINT M 270と超強力鋼であるマルエージング鋼の材料との組み合わせによる金型製作の実績が増えて、関心が集まっています。EOSINT M 270は、レーザービームをフォーカスさせ、金属粒子を直接焼結、溶融させて造形する手法を採用しています。この手法は樹脂のバインダを使わないため、造形直後から十分な機械特性を持ち、後工程の焼成、溶浸のときの収縮や変形を補う処理が不要になるので、精度の高い金属部品や金型が直接製作できる点で優れています。
1995年の第一世代となるEOSINT M 250の発売以来、材料、装置ともに改良が繰り返され、着実に進歩してきました。現行機種であるEOSINT M 270の登場以後は、一般的な工業素材を材料として適用するために、その材料およびプロセスの開発が進められてきました。
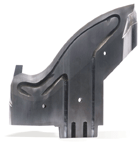
EOSINT M 270で製作したマルエージング鋼製のハイブリット金型インサート
その結果、前世代機種で課題となっていた造形密度、造形物の機械的特性を高いレベルに押し上げています。また、Additive Manufacturingを行う生産ツールとしての操作性や安全性も向上しています。
進化したEOSINT M 270が最も使われているのが量産用金型インサート製作です。これに適した材料としては、マルエージング鋼が用意されています。マルエージング鋼は、高い強度と優れた靭性を兼ね備えた鋼であり、造形品も同様の特徴を持ちます。
また、簡単な時効硬化処理により、引っ張り強度[1,900MPa]、硬度[約55HRC]を達成することもできます。射出成形金型で100万ショット、アルミダイキャスト金型で18万ショットの実績が報告されています。どちらも内部に3次元的な冷却水管を配置した金型です。これは、従来工法とEOSINTの新たな活用方法としてご紹介できるハイブリット金型です。従来工法で製作した金型部品の上に、複雑で立体的な冷却回路を構成する部品をEOSINTで直接造形するというものです。
EOS MaragingSteel MS1 | |
---|---|
最小積層厚(μm) | 20 |
引っ張り強度(MPa,MPIF 10) | 1100 |
耐力強度(MPa) | 1000 |
ヤング率(GPa) | 180 |
硬度(HRC):焼結後 | 37 |
硬度(HRC):熱時効硬化後 | 55 |
比熱容量(J/kg℃) | 450 |
熱伝導率(W/m℃) | 15 |
密度(g/cm3) | 8.1 |
EOSINT M 270で金型を造形する場合、造形ボリューム(特に高さ)に依存する積層の造形時間とコストが課題になります。造形するサイズが大きくなると、製作時間もコストも増えるということです。ハイブリット金型では、複雑な冷却回路を必要とする部分をEOSINTで製作し、それ以外は従来工法で事前に製作することで、時間およびコスト面で大きく効率化を図ることができます。装置、材料ともに進化した結果、実現できた有効な活用事例です。
テーラーメイド金属部品の効率的な生産
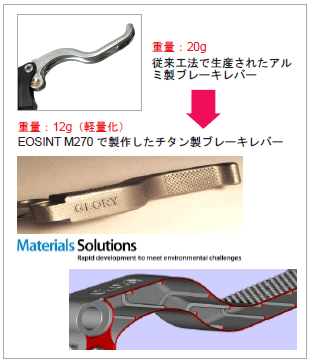
図2は、金属を使用するEOSINT Mで製作したチタン製レース用自転車ブレーキレバーです。これは、ワンオフ製品のテーラーメイドを効率よく行った事例で、積層造形の特長を利用することで、今までにない製品を作りだすことに成功しています。
チタン材料を使用して軽量化を図っていますが、積層造形の特長を活かし、肉厚0.6mmの中空構造でさらなる軽量化を実現しています。指がグリップする部分には、あらかじめ滑り止めの表面デザインを施し、機能性を高めたデザインになっています。EOSINT M270による造形時間は、6部品同時に行い約6時間です。
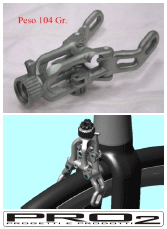
図3も、レース用自転車のブレーキ部品の例です。
このブレーキ部品は、肉厚0.8mmの中空構造で軽量化し、震動を利用した性能アップと材料のコスト削減が、EOSINT M270によるテーラーメイドで実現できています。造形時の積層ピッチは30μmで、1セットの造形時間は約11 時間です。
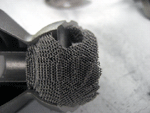
また、中空構造については、一定肉厚で内部を空洞化させることが一般的ですが、EOSINT M270であれば、複雑なラティス構造(図4)によって軽量化と強度を実現することもできます。
以下に材料の機械的特性を示します。
EOS Titanium Ti64 | |
---|---|
最小積層厚(μm) | 30 |
引っ張り強度(MPa,MPIF 10) | 1180 |
耐力強度(MPa) | 1090 |
ヤング率(GPa) | 120 |
硬度(HRC) | 41~44 |
密度(g/cm3) | 4.43 |
EOSINT M金属造形サービス
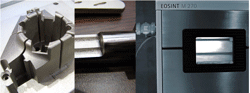
金属材料を使用するEOSINT M 270を設置しているNDES RPテクニカルセンター大阪では、EOSINTM 270を使用した造形サービスを行っています。複雑な機能部品や高機能金型部品などを専門の技術者がEOSINT Mを用いて造形します。造形ご希望のお客様はぜひ、お問い合わせください。