他社が追従できないサービスビューローを目指す
株式会社北九樹脂製作所様は、自動車、家電、窯業、医療などのさまざまな分野の試作品を製作しています。
この多様な試作技術は、高精度、短納期、低価格だけでなく、お客様のニーズに合ったプロセスの選択を実現しています。さらに、最新設備の光造形機、粉末積層造形機による試作は、意匠試作の域を超え機能部品の試作へと広がり始めています。
今回は、2009年に導入されたFORMIGA P(プラスチック粉末積層造形機)の導入背景、効果などのお話をお伺いしました。
試作メーカへ進展する
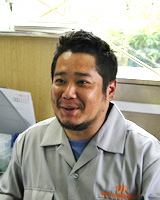
平山 鉄夫 様
以前、「人とシステム」NO.22に掲載していただいたのは、今から9年前の2001年でした。その頃、まだ光造形機は1台しか導入しておらず、そのSTLデータを出力するのにかなり四苦八苦していた時期で、ヒーリング機能があるSpace-Eを導入して、それなりの効果を出していました。
光造形機の導入後3年ほどは、地場のNC加工による金型や生産よりの加工冶具、検査冶具の製作が7~8割で、2~3割が試作でした。それが、最近では売上げ的に試作が7割になり逆転しています。やはり、光造形機による試作をされるところが少なく、当社への試作ニーズが必然的に高くなったのだと思います。
また、当社は鋳物の試作型もできるため、今では、樹脂から金属部品までの試作全般を主業務にした会社になりました。
以前は、大阪、名古屋、東京の試作メーカによるモノ作りネットワークの輪がより強くなっていたのですが、リーマン・ショックの影響により、ここ数年で少し冷え込み、その輪は小さくなってきています。ただ、当社にとっては、モノ作りネットワーク間での仕事のやり取りが比較的多くあり、九州でありながら九州以外の仕事をさせていただいています。当社でもメッキや板金の試作を受けますが社内ではできないため、信頼できるモノ作りネットワークの板金試作メーカに依頼しています。
当社の会長は、昔から仕事に対して信念を持っています。それは、徹夜して努力すればできるものはやる、徹夜してもできないものは断る、ということを実践してきているので、それを受け継いでいます。また、仕事を始めた頃に、このような考え方をされる方々と多く巡り合っているのではと思います。常に、仕事を受けるためには何をしたらいいのかという発想しかないので、協力できる会社とネットワークを組んで素早く対応できるようにしているのです。そのため、モノ作りネットワークの皆で頑張っていくための努力は常にしています。
FORMIGA P のサンプルでお客様の意見を聞く
今まで粉末積層造形は、表面が粗いものしか見たことがなく、細かい形状を含む精密部品には不向きで自動車などの比較的大きな部品に特化しているというイメージを持っていました。それが、DMSの展示会で初めてFORMIGA P を見たとき、今までの粉末積層造形の製品とは一線を画すものだと感じて深い興味を持ちました。そして、試作メーカとして、光造形、切削、真空注型などをしていく中で、強度を持ち寸法精度を出すことができ、さらに超短納期で製作できる機械は、粉末積層造形機しかないと考えました。
DMSで見たときからFORMIGA P の魅力は分かっていましたが、高価な投資になるため導入までに1年半ほど悩みました。当社は、導入前のベンチマークテストはしませんでした。その代り、お客様にアピールするためのサンプルをNDESに作ってもらいました。
そのサンプルをお客様に見ていただき、意見を聞いて回ったのです。従来の粉末積層造形機のサンプルとFORMIGA P のサンプルを一緒に持っていくと一目瞭然で違いが分かります。そして、お客様の7割から良いという判断をいただき、自分の中でもいけるという確信を持つことができたのでFORMIGA P を導入しました。
通常、粉末積層造形機を導入されているところは、自動車メーカ様の試作を目的にされますが、当社は、家電メーカ様の試作を考えていたので、サンプルを見ていただいたのも家電メーカ様でした。今では、自動車メーカ様の小部品も作るようになりましたが、主力はやはり家電メーカ様の小部品の試作です。
FORMIGA P の良さ
営業意欲がわく
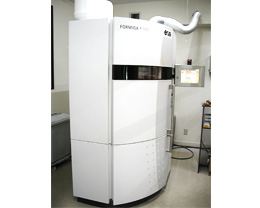
FORMIGA P は、良いものができると認識して導入したのですが、導入してさらにその良さが分かりました。
まずは、営業意欲がわくということです。昔、マキノの工作機械を持っているだけで、高精度で奇麗な加工ができると思われていたのと同じです。FORMIGA P を持っていることがステータスで、この機械でしかできない造形があることで、お客様に信頼していただけるのです。
FORMIGA P による低コスト
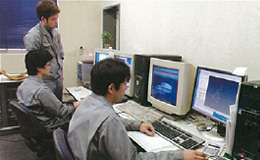
FORMIGA P でなければ、採算が取れないものもあります。大物であれば分割した方が、少ない材料で価格も低く抑えられます。
造形領域が、200mm×250mm×330mmと小さいため、造形する形状を効率よく配置すると材料費が安くなり、さらに小さい部品に特化することでたくさんの仕事量をこなせます。それに、光造形機と比較すると5~6倍の高い造形能力を持っているので、1日に作れる量が絶対的に違います。
また、今の造形が終わらなくても、造形領域に隙間があれば追加できるという利点があります。試作メーカにとって、工程の途中で追加したい部品を割り込めるありがたさというのは、何事にも代えがたいものです。これが粉末積層造形のすごいところです。当社は、1日のうちに工程が2~3回変わります。お客様が希望される納期に間に合わせようと努力すると、柔軟に工程変更して対応する必要があります。たとえば、朝、昼、夕方に工程が変わっても対応ができるのが粉末積層造形です。今のように仕事量が多いときは、造形機の特性をフルに活かせるため、お客様に低価格でご提供できます。
もし、仕事量が少なければ価格が高くなるため、さらにお客様が減るという悪循環になると思いますが、今のところ、順調に仕事をいただいています。そのため、FORMIGA P は導入してから、かなりのサイクルで稼働しています。
試作の選択肢
最初は、既存の光造形の仕事が粉末積層造形に置き換わるだけで売上げは変わらないと思っていました。ところが、お客様にそれぞれの特性をお伝えすることで、造形したい工法を指定していただけたのです。
ある製品の一次試作として、約50点の全部品を粉末積層造形で納品しました。そうすると、2ヶ月後の2次試作では、50点の部品が光造形と粉末積層造形に各々半分に分かれて指定がきたのです。このように、強度が必要な部品は、粉末積層造形が適しているという判断をしていただき、それぞれの特性を有効に活用いただいています。
当社は、光造形、粉末積層造形、切削、真空注型、アルミ鋳造、板金加工、手加工、そして表面処理の塗装・ブラストなど、試作に関するさまざまなご提案ができることをアピールしています。選択肢が多い方がお客様も安心して当社に任せていただけます。やはり、自分が買い物をするときでも品揃えが豊富にあるお店に行くので、それと同じです。特に、その中で粉末積層造形の活躍の場が広がっています。これまで、粉末積層造形を敬遠されていたお客様でもFORMIGA P は気に入っていただいています。
また、強度があり造形後の形状変化がないので、部品の嵌合も問題なく行えます。
FORMIGA P の使いやすさ
機械自体が使いやすい仕様になっています。それなりのノウハウは必要ですが、難しい固有の知識は少なくなっています。当社は、これまで蓄積してきた光造形のノウハウや技術を持っているため、さらに使いやすいと感じました。
また、NDESと最初に機械を調整するための打合せを密にすることで、トラブルもさほど発生していません。教育は、5日間ありました。導入後、スムーズに立ち上がれるようなカリキュラムで教育を受けました。まずは、積層法の勉強をして、実際に造形しながらノウハウを蓄積していくことになります。
表面処理
粉末積層造形が広がらない一番の理由は、表面の手触り感と見た目です。やはり、光造形と比べると粉っぽさを感じ、落雁のように弱くきゃしゃに見えてしまいます。
その粉っぽさをできるだけ改善するために、表面に含浸処理や今まで取り入れていなかったUV塗装を施しました。そうすると、ある程度ツルっとした表面になります。最初のうちは、かなりの割合で含浸処理をしていましたが、素材自体を磨いてもさほどツルツルした表面には仕上がらないので、そのことをお客様にご理解いただくようにしました。お客様には、良いところも悪いところも全てご説明して、どういう試作品ができるのかイメージしてもらうことがとても大事なのです。
水、空気を通さない
当社でも実験をしましたが、従来の粉末積層造形で厚みが2mmになると水や空気を通してしまうため、息を吹き込むと泡が出ていました。それが、FORMIGA P で造形すると、水は表面的に染み込みますが貫通はしません。もちろん空気は通り抜けることはありません。
当社は、水回りのお客様が多いので、見た目は水が通りそうですが、実際は通さないことを説明すると、すぐに使っていただけました。
試作では品質が重要
当社は、試作のコスト、品質、納期の中では、特に品質を重視しています。確かにコストも大事な要素ですが、アイデアを出すことでコストダウンを図れます。また、造形スピードが圧倒的に速いので、納期も問題ありません。それに、造形領域が小さいことで早く冷えるため、品物をすぐに取り出すことができ、次の造形に向けてすぐ暖められることも短納期に有利です。
やはり品質は、造形機の性能で違ってくるので寸法精度が出せない機械に品質を求めても無理です。そのため、特に寸法精度に重点を置いて機械の選定を行ったので、FORMIGA P の品質には満足しています。
冶具にも活用
粉末積層造形は、組立冶具、加工冶具、検査冶具などにも使っています。当社には、5軸加工機がないため、複雑な形状をマシニングセンタで切削すると加工工数がどうしても増えてしまいます。
そこで、マシニングセンタの加工物にFORMIGA P の造形物を貼り合わせる方法で冶具を作っています。FORMIGA P は、複雑な形状でもデータだけで簡単に造形できるため、この方法であれば5軸加工機がなくても、より短時間で冶具を作ることができます。当社は、このようなアイデアを出すことは得意です。
また、粉末積層造形だけで組立冶具を作ることもあり、最近、この仕事も増え始めています。やはり、今までのNC加工であればCADの次にCAM、そしてワークを乗せて切削していく工程だったのが、粉末積層造形であればCADの次は造形なので、工数も少なくなるからです。
リーマン・ショックを乗り越える
ありがたいことにリーマン・ショックを乗り越えられたのは、FORMIGA P のおかげです。
当社の光造形と粉末積層造形は、お客様を引き付ける目玉商品なのです。この設備を持っていることで相乗効果があり、従来の切削加工や手加工の仕事も逆に増えて、売上げが下がりませんでした。
自動車メーカ様の試作であれば、大きなプロジェクトになるため開発時期などから、ある程度の仕事量の予測は付きますが、個々の物件が小さい場合は、先を読むことが難しくなります。最近は、大きい物件よりも、小さい物件を数多くするようになり、事務的な業務は増えて大変ですが、仕事量の波がなくなりました。
また、当社の仕事は難しいものが多く、全体の8割を占めています。その中には、厳しい納期のものもありますが、お客様の意図を察して努力していれば必ず認めていただけます。
今後の展開
大型の造形機
最初は、お客様からFORMIGA P では小さなものしかできないのかと言われて、悔しく感じたこともありましたが、FORMIGA P は小物を精度良く造形する機械で、大物を作る機械ではないのです。
今後は、用途に応じた大型の造形機もほしいと考えています。
個人向けWeb サイト
昔に比べると個人のお客様が増えています。個人的な趣味としてのフィギアや宝飾系の造形です。
今、協力会社と個人向けのWebサイトを立ち上げているところです。造形品の完成度はホームページ上で確認して申込んでいただくようにしたいと考えています。フィギアや宝飾系は、価格、要望などで厳しい面もありますが、それをクリアして数多く作ることを進めていこうとしています。
ソフト面の強化
今年のDMSでは、機械の販売形態が2極化していました。従来のようにイニシャルコストが高い機械に加え、初期投資を低く抑える代わりに、ランニングコストを高くした機械が多く出展されていました。そうすると、機械が手に入れやすくなります。昔は、造形機といえば、かなり高価なもので導入することが難しかったのですが、今はカラーコピー機よりも少し高めの価格で買えるものもあります。
また、NC工作機や造形機、そしてCAD/CAMに関してもハードの改良が進み性能が随分良くなり、逆にハードに頼りすぎていると感じています。これから、光造形機や粉末積層造形機が普及してくると、同じ設備でも他社に負けないためには、ハード以外で差別化を図る必要があります。
今後、試作メーカという位置付けの器は縮小傾向にあり、明るい業界とは言えませんが、試作メーカがゼロになることはありません。このような状況の中で試作メーカとして生き抜くには、ソフト面の充実が必要です。当社は、試作工法の選択肢が多いだけではありません。それぞれの工法を有効に組み合わせた試作品を作るなど、いろいろなアイディアを出して他社が真似できないソフト面の充実を図っています。
最新情報の収集
今までもそうですが、常に最新情報の知識を持っていることが大切だと思います。いつも新機種が販売されるたびに、どこまで投資すべきかを悩みます。設備投資は、経営にかかわる重要な問題なのです。導入した機械で2~3年間はフル稼働で仕事をして、また、3年後はどのような展開になるのかを想定する必要があるのです。情報収集のアンテナを張って業界の動向を見極めながら、設備投資の判断材料にしていきます。
今年1月には、微細造形機を導入して、医療器具の試作も依頼されるようになりました。
NDESへ
NDESは、メンテナンス、サービス面が良かったと思います。導入前に、FORMIGA P の長所、短所を隠さず教えてもらったことで、安心して導入できました。
NDESには、今までと同じように定期的に最新情報を教えてもらいたいと思っています。また、Space-E、Darwin Vueも導入していますので、今後もいろいろなサポートをよろしくお願いします。
おわりに
平山社長は、人と人とのつながりを大切にされています。たとえば、いろいろなメーカと付き合うことで幅広いつながりができ、さまざまな情報収集ができるだけでなく、各々の相乗効果もあるそうです。
大変お忙しいところ、貴重な時間をさいてお話を聞かせていただき、ありがとうございました。
会社プロフィール
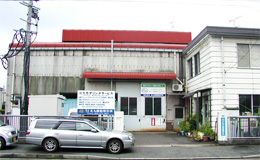
株式会社北九樹脂製作所
所在地 | 〒800-0211 福岡県北九州市小倉南区新曽根2-10 |
---|---|
創業 | 昭和45年6月 |
資本金 | 15,000,000円 |
営業品目 | ラピッドプロトタイピング(光造形法、粉末積層法)、3次元モデリング(CAD/CAM)、金型(NC加工・デジタイジング)、木型(鋳造用/多々種)、樹脂型(鋳造用/多々種)、アルミ試作・鋳造 |