![]() |
---|
![]() |
株式会社キヤノン 生産本部 成形金型開発センター センター所長 畠 淳一郎 様 |
---|
![]() |
株式会社キヤノン 生産本部 成形金型開発センター 部長 田原 均 様 |
---|
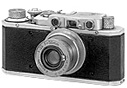
「KWANON(カンノン)」試作
この名前は、観音様の御慈悲にあやかり世界で最高のカメラを創る夢を実現したい、との願いを込めたものです。
-「世界一のカメラを作りたい」が始まりだった-
「われわれ日本人だって、高級カメラがつくれるはずだ。」ライカやコンタックスなどドイツ製の高級カメラが人気を集めていた時代、自分たちの手でカメラを作りたいという夢を持った日本の若者たちがいました。
1933年、彼らはみずからの思いを実現するために、東京・六本木のアパートの一室に小さな研究所を設立。試行錯誤と地道な取り組みの末、1年後に試作品「KWANON(カンノン)」を完成させます。
キヤノンの歴史はここから始まりました。
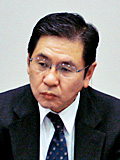
代表取締役社長
木下 篤
木下 2001年に阿見工場でSpace-Eのカスタマイズの件でお伺いしてから、10年のおつきあいになります。
本日は、成形金型開発センターでの新技術開発や今後の取組みなどについてお話をお伺いしたいと思います。
グローバル優良企業グループ構想
木下 私どもにとって、御社の商品イメージとして、カメラのイメージがとりわけ強く、メイドインジャパンの精密機械の代表作という印象があります。まず御社の主力商品についてご紹介いただけますか。また、グローバル企業として積極的に海外展開をされており、国内と海外売上の比率などの状況はどうでしょうか。
畠 主力製品は事務機です。インクジェットプリンタやカメラなどのコンシューマ向け事業と事務機などのオフィス向け事業と半々くらいです。
地域別の売上高では2009年の実績で、国内22%、米州28%、欧州31%、その他19%ですから、8割くらいが海外です。
田原 2010年は、国内は20%を切り、少しアジアのほうが増えているという状況です。
畠 これは以前から欧米に支店を出してきましたので、その結果が今現れているということです。
グローバル優良企業グループ構想でキヤノンも変わりまして、今でこそこういう利益体制になっていますが、それまでは本当に技術オンリーで、利益の少ない会社でした。1995年と比べると、2007年には、売上が2倍強になり、純利益が約9倍弱にまでなりました。トップの判断がすごかったのでしょうね。どうしてこのような体質になったかというと、コストに対する意識が全社的に変わり、原価率も57%から49%(2007年)に下がっています。内製をして自分たちで汗を流して稼ぐという方向で、今後も内製を増やそうとしています。
木下 売上状況や原価構造などを「見える化」へと変革したということですね。
畠 そうですね。こういうことがきちんと見えてきて業績が良くなると、やはりみんなその気になりますから、経営という観点でそれぞれの事業部が運営をしだしたということだと思います。今までは、本社の統制機構がなかなか事業部の中に入っていけなかったので、事業部の中の利益の出ない事業などもそのまま放置されていることもありました。それをある程度見直したというのもあります。また、海外生産であまり円に頼らない体質になっていると思いますので、今の円高でも利益は出ています。
成形金型開発センター
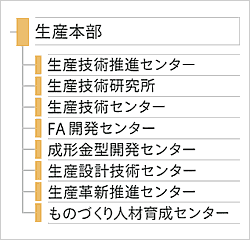
木下 現在統括されている「成形金型開発センター」の役割についてお話いただけますか。
畠 成形金型開発センターは、生産本部に所属しておりまして、ここ川崎が生産本部の拠点です。生産本部には、1つの研究所と8つのセンターがあります。
その中で成形金型開発センターは、プラスチックの成形技術と金型の加工技術を開発しております。
プレスについては、以前キヤノン精機という関係会社が内製していましたが、15年位前にやめてしまい、それからプレスはやっていませんでしたが、ここにきて川崎でプレスの加工技術開発を再開しています。ただ金型を作るまではいかず、金型作りは協力会社ですが。
全般的にはプラスチックが多く、それぞれの事業で新製品がたくさん出ますので、年間でプラスチックは1万型を起こしています。プレスはその半分くらいです。そのうち内製は、金額ベースで30%、台数ベースで10%弱です。
内製部門は国内が中心ですが、高耐久と超精密に的を絞っていまして、プラスチックでは、キヤノンモールド株式会社(URL:http://www.canon-mold.co.jp/)が内製の90%を造っています。成形金型開発センターで金型の技術を開発し、キヤノンモールドで設計製造しているということです。
一般的な構造物の成形でも、サイクルと材料削減、いかに薄くしていかに早く作るか、この部分を中心に取組んでいます。毎年新製品が次から次へと出てきますので、今年はどの製品のどの部品に新技術を導入するかを決めて、それぞれの事業の金型技術の担当者と一緒に立ち上げています。2機種目からは各事業が独自で展開できています。
光学精密金型のダイヤモンド切削加工の事例
畠 成形金型開発センターで取組んできた超精密の事例として、DO回折レンズとその金型、ダイヤモンド切削加工について紹介します。
キヤノン内製の光学金型
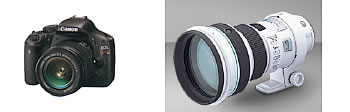
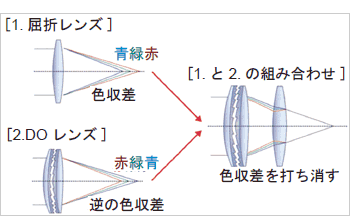
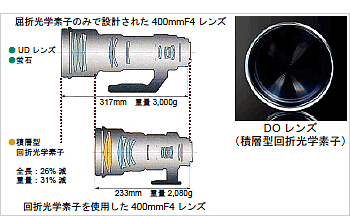
・DO回折レンズ
畠 カメラ用「DO(Diffravtive Optics)レンズ」は、回折光学系と屈折系では色収差がまったく逆に発生する性質を利用し、ガラスレンズの表面に精密な回折格子を接合し、数μm精度で近接、階層構造にした、キヤノンが世界で初めて開発したレンズです。
金型は鏡面ですが、よく見ると中に線が切ってあり、表面がキザキザしていまして、これが回折格子で色収差の補正に使っています。対向した2面にキザキザをつけると、光の回折現象により通常のレンズと逆方向に色ずれが生じます。赤と青が反対になり、組み合せることにより合理的に色を消すことができます。望遠レンズの小型化と軽量化を実現しています。
・DOレンズ成形(レプリカ法)
DO型の表面にUV(紫外線硬化)樹脂を重ねて、上からレンズ基材を接着して金型形状を転写し、硬化させます。
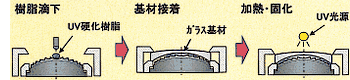
このようにして作成したDOレンズを対向で凹と凸とを作成して2対使用して色収差補正を行います。超精密の製品ですから、精度が大変重要です。研磨ができませんので、切削だけで鏡面を出します。
キヤノンでは微細形状をもった金型の加工技術、樹脂の性質や物性について研究を重ね、ナノメートルオーダーで微細形状を制御して転写する技術を完成させ、現在は種々のレンズ製造が可能となっています。
・ガラスモールド技術
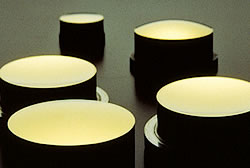
超精密加工を施した非球面の金型でガラスを直接熱プレスします。キヤノンでは、ガラス材料、金型素材などの検討を重ね、温度と寸法変化についてシミュレーションを行い、高温でも狂いのない金型を実現しています。ガラスモールドでつくられたレンズは、屈折率などの自由度が高いことから数多く使用されています。
加工・計測装置技術
・超精密5軸同時制御加工機
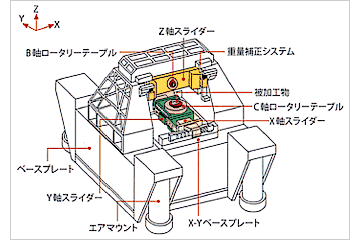
畠 レンズやプリズムなどの光学素子は、設計技術の進歩とともに球面から非球面へ、軸対象から自由曲面へと進化をつづけています。nm(ナノメートル)の精度を必要とする光学素子において、曲率変化の大きい自由曲面の加工には独自の加工・計測装置の開発が必要となります。
田原 UV用の装置も社内で作りますし、使用するUVの樹脂や成形の条件も、その開発部門で見極めています。
木下 レンズ成形用の金型を製作するために、加工機自体も自社で作られたということですか。
畠 そうです。やはりここは絶対に強い、負けないというところがないとね。どこにも負けない技術を1つ持つと強いと思います。
田原 数式にのっとり形状を加工しているので、磨くと数式が崩れてしまいますから、切削だけです。
畠 最初の頃は磨きが前提でしたが、光学の精度が厳しくなって、だんだん磨きレスになってきました。
木下 磨きというのは職人さんの感性ですね。曖昧さもありますし、数式でこうだという話でもありませんね。数式を保証できる機械加工機を作ることによって、精度を保証したというイメージでしょうか。
畠 そうですね。加工機の精度をどんどん上げてきたということです。
ダイヤモンド切削加工
田原 ダイヤモンド切削の加工方法には、フライカット、旋削、ミーリングがあります。
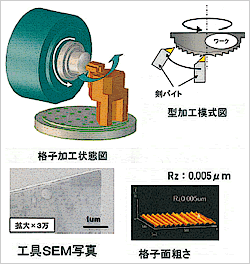
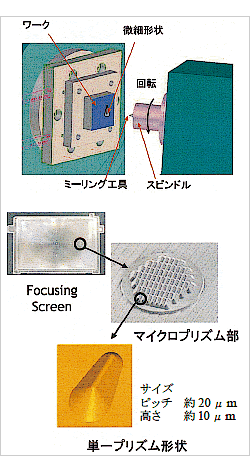
・回折格子旋削
田原 DOレンズの金型は、回転するワークの半径方向にダイヤ工具(剣バイト)を走査し、同心円の格子形状を加工します。格子面の粗さは、0.005μmです。
・ミーリング
畠 一眼レフカメラの中にピントを確認するためのピント板が入っています。このピント板をよく見ると、小さなプリズムをたくさん作っています。ピントが合った時に光る赤いLED光を反射させているのです。これは約20μmのピッチです。
自由曲面加工ではさらなる高精度を目指し、微細形状加工ではL/Dや複雑形状対応が必要で、そういう範囲を広げるために、装置の世代を変えて開発しています。要求精度が高くなると、また新しい加工機を開発しなければいけないということになります。
・加工精度
畠 加工精度では、現在の限界精度は、形状精度は30nm、表面粗さは3nmが業界相場です。今後はさらにその精度を上げないといけないですね。
このクラスになると一般の金属加工とは別世界のイメージです。銅とかニッケルを削っているのに、豆腐を削っているような感覚らしいですね。治具に固定するだけでも、ワークが数nm曲ってしまうわけです。振動、気圧、熱なども影響しますので、こういうノウハウがいろいろありまして、それをシミュレーションできちんと確認した上でやっています。
複写機読取り用ミラーのモールド化技術
畠 従来、両面原稿を高精細で読み取る場合は、原稿をフィーダーで反転して片面ずつ読み込む必要がありました。これを、構成が複雑で部品が点在していた光学系を1つにまとめ、フィーダー側と原稿台の両方にスキャナユニットを搭載し、1回の読み込みで両面原稿を同時に高精細で読み込むことができるようになりました。
このスキャナユニットには、キヤノン独自の自由曲面ミラーを採用しています。これにより、スキャナユニットの小型化に成功し、複合機本体の省スペースにも貢献しています。
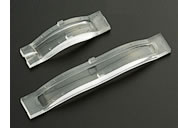

トナーカートリッジ生産システム
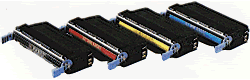
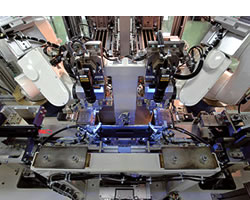
畠 生産システムの自動化は、生産スピードや品質の向上、ならびに低コストを実現するために非常に有効な手段です。キヤノンのレーザープリンター用トナーカートリッジの生産では、部品加工から組立て、検査、梱包に至るまで数百もの工程を自動化した独自の「一貫生産システム」が稼動しています。
キヤノンのトナーカートリッジは、感光ドラム、帯電器、クリーナー、現像器などが組み込まれた独自の「一体型」トナーカートリッジで、取り扱いがしやすいため、メンテナンスが簡単でリサイクルが容易にできます。
トナーカートリッジは消耗品で大量に出荷されますから、これをかなりのハイサイクルで製作しています。サイクルタイム短縮の技術を成形金型開発センターで開発し、キヤノンモールドでその技術を金型に入れて内製しています。
カートリッジの全長は30cmほどあるのですが、ロボットアームで瞬時に取るため、キャビ間の誤差は数十μmしか許されません。高速でハンドリングしていますので、製品の公差とは別に自動組立機用の公差というのがありまして、自動組立用部品は精度がとても厳しいのです。そのため金型も内製で高精度で製作し、成形条件もとても厳しく管理してます。
田原 トナーというのは細かい粒ですから、ちょっと隙間があっても漏れが出ます。いろいろな部品の組合わせでもしっかり封止しなければならず、1種類の自動組立機でやりますから、溶着の条件も毎回変えるわけにはいかないので、キャビ間の相互精度が要求されます。
畠 面精度やそりについても精度は厳しいですね。
現在は、「完全無人化ライン」の実現に向けた世界最先端の技術開発に挑戦しています。
世界最適生産体制の確立
畠 今年から「グローバル優良企業グループ構想」フェーズⅣがスタートし、主要戦略のひとつに「世界をリードする世界最適生産体制の確立」があります。
これは、内製化と自動化と消費地生産です。
生産から販売、さらにはリサイクルまでを地域内で完結する自己完結型の消費地生産です。
現在は、リサイクルをそれぞれの拠点で行っています。回収した製品をわざわざ日本まで戻すわけにはいかないので、回収をすれば再生もその国でやらなければいけないという、消費地完結という新しいニーズが出ています。
米国のキヤノンバージニアでは、トナーカートリッジの消耗品をすべて回収して、再生産に回しています。一番先行している国です。日本や欧州、中国でも、リサイクルは十年来取組んでいますがまだ課題は多いです。
木下 リサイクルはすごくコストがかかりますよね。
畠 リサイクルは社会的責任として果たすべきことですからね。
キヤノンは、世間でリサイクルといわれる前の1990年からリサイクルに取組んできました。まだ使える部品をどうして捨てなくてはならないのか。回収すべきだと、回収プロジェクトが発足したのです。やっと世の中もリサイクルのほうに向いてきたと思います。
リサイクルは、製品を使用した国の中で回収が進むのが一番いいと考えています。回収分は費用がかかりますが、それは仕方のないことです。今は、リサイクルをして再生する製品と新規で作る製品とほぼ同じ費用で生産できています。
木下 金型も各拠点で生産しているのでしょうか。
畠 金型の生産については、国内が2009年で45%、中国を中心とした海外が金額ベースで55%という状況で、年々変わっています。アジアはやはり中国から調達して、タイ・ベトナムに持って行って成形をしています。
もちろんローカルの成形メーカーに出しているところもありますが、型の調達は中国中心になっています。
木下 中国の金型メーカーというのは、キヤノンさんの現地法人ですか。
畠 ローカルの金型メーカーです。中国とは2000年くらいから始めて、最初の頃はとんでもない金型だなあと思いながらも段々よくなってきて、今ではほとんど何でもできるという状況になってきています。
海外にも最新の金型を生産できる拠点を作りたいと思っているのですが、今のところはタイと台湾、米国に少しあるぐらいです。それ以外の国に対して、金型を供給できていないということは課題としてとらえています。
新成形技術を展開していく、海外の型拠点がまだ十分できていません。新製品は、やはり年末商戦に向けて一気に出てきますから、各事業部の中に金型部門がないと、仕事の山谷を吸収できず、商売としては成り立たないのです。それもあって、事業の中で金型もつくるという形をとっています。台湾もタイもそれに近いかたちで、忙しいときは製品型の仕事をバンバンするけれども、暇なときは工具の仕事を入れるなどをかみ合わせています。金型設計製造の合理化や無人化・自動化ということを積極的にやっていかないと、とても中国に追いつかない状況です。
NDESへ
木下 私どももこれまで約10年いろいろお手伝いをさせていただいて、その間の弊社への感想や今後期待したいことをお伺いできればと思います。
田原 Space-E/CAMを導入してから10年になりますが、国内でCAD/CAMの開発をされているので、われわれのやりたいことを理解してもらって、すぐに動いていただけるというところでお世話になりました。
内製で金型を作っていますが、社内だけですむかというとそういうわけではなく、協力会社さんにもお世話になっています。これから一番期待したいところは、われわれのような製品メーカーと協力会社さんとをうまく繋いで業界を盛り上げるような役割をお願いしたいですね。技術やソリューション、ツールもそうですし、そういうところを強化していっていただいて、うまく展開していただきたいと考えています。
JETIA(社団法人電子情報技術産業協会:http://www.jeita.or.jp/japanese/)の三次元CAD情報標準化専門委員会(http://home.jeita.or.jp/3d/index.htm)で、3D単独図の活用について検討しています。
社内で3D単独図を使うといっても協力会社さんに渡せないと前へ進めないのです。NDESにも三次元CAD情報標準化専門委員会に入っていただいたので、そういうところを一緒に盛り上げていければありがたいですね。
畠 御社は、CAD/CAM関連商品を販売するのが目的ですね。ITの専門的な知識をお持ちなのでその前の段階でコンサル、提案をしていただくというところを期待したいと思います。
お客様が強く望むのであれば、当然それは商売につながっていくと思います。
今われわれのところはCADシステムが固定されていますので、なかなか今以上のことはできない状況ですが、そうは言っても、御社はCADの開発をされていますので、こういういいやり方がありますよということをご提案いただければ、それに対して弊社でもプラスアルファになるものがあって、一緒にできるような可能性もあるのではないかと思います。
木下 加工や生産技術というところはわれわれには難しいですが、その手前のCAD/CAMシステムとしてどうあるべきか、どういうデータをもらってどういうデータを渡せばいいのか。そういったことについてはいろいろなお客様にお手伝いをさせていただいています。私どもも、パッケージ販売というよりは、お客様の業務を知った上で、望まれていることや要求されているシステムは何かということを受け止めてご提案できるようにと考えています。
畠 いろいろな事業規模がありますから、大きな事業をしているところはそれでいいのですが、小さな協力会社さんまで全部NXを使うように徹底するかというと、それは無理です。データ変換をしていろいろなシステムに持っていくという、そのようなソリューションはこれからまだまだあると思うのです。そういうところでいろいろなご提案をしていただけると助かります。
木下 われわれもいろんなシステムにまで手を広げることはできませんから、CAD/CAMというところで、ベースのシステムからきちんとデータを取って受け渡すということを、今は地道にやるべきところだと思っています。
本日は、まことにありがとうございました。