![]() |
ムツミ工業株式会社 代表取締役社長 近藤 哲典 様 |
---|
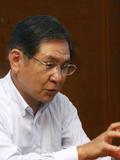
代表取締役社長
木下 篤
木下 近藤社長は数学的な、あるいは物理的な根拠を持って、製品設計や金型設計にアプローチされていらっしゃいますね。
本日は、そのお考え方や、3Dを核としたものづくり、今後CAEを武器としてどう活用されていくのかなど、お話をお伺いしたいと思います。
ムツミ工業の主張
近藤 当社は、1949年に父親が設立した会社で、世の中の産業が大きく変革する中で柔軟に対応を続け、今年で創業63周年を迎えます。
本社を名古屋市に置き、名古屋・小牧と二つの工場で事業を行っています。名古屋工場では、機械事業部として組付け機・試験機等の専用機を設計・製作、小牧工場では、型事業部としてプレス金型の設計・製作・製造を行っています。
当社のビジネスモデルは、製造工法の開発から工程設計、機械、金型の設計、製作、流動テスト、出荷、現地支援とメーカーとしての一連の事業に係わり、お客様の生産を支援することです。また、国内外を問わず生産支援の一環としてお客様から人員をお預かりし、設計要員・保全要員との交流、教育も行っています。
「良い製品を安く、早く作る」モノを提供するのではなく、「作る」コトを提供し、支援させていただいています。
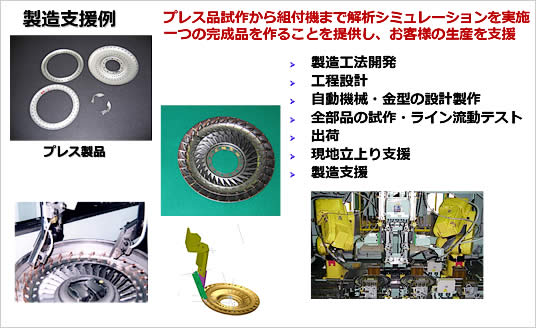
理想の金型づくりとは
木下 2011年6月の型技術者会議2011で「数学で金型を創ろう」というタイトルでご講演されていますね。このお考えをお聞かせいただけますか。
デジタル化への歩み
近藤 名古屋大学の工学部で塑性加工を研究していました。夏休みになると父親が、塑性加工屋になるなら実習に金型工場へ行けと、小牧の金型工場に行かされました。学生時代の4年間は、夏休みと春休みに金型屋さんというものを実習しました。
卒業後、父親の経営するこの会社に入社し、金型工場で実習をしていました。その後、管理職の仕事をしなさいと言われましたが、金型屋の管理職というのは実は何もできないのです。
ひとりの職人さんが自分で全部采配してやるわけですから、その職人さんが帰ってしまえば、今日ここまでやらないといけないことができなくなります。納期が迫れば徹夜・休日出勤。職人さんの機嫌を損ねれば、職人さんを探し回って連れ戻す。
これでは納期管理も原価管理もあったものではないです。それでも儲かったのが昭和の50年代です。
そんなときに、こんなことをしていてもとても仕事にはならない。CADで図面を描いて、CAMでNCデータを出して工作機械で切削し部品を加工して組み付ければ、とりあえず電車の時刻表のようなものが書けるのではないかという思いを持ったのが29~30歳頃でした。
お客様もCADを導入されるようになり、昭和63年の3月にGRADEを導入しました。先代の社長に、これを導入したらいくらの投資効果があるのだと言われたのが一番困りました。計算できないですね。最後には、仕方がない、道楽息子に付き合おうと導入に至りました。ただ、スーパーミニコンに端末をつないでいた時代ですから、ゼロがひとつ多くて間違っているのではないかと先代の社長に言われましたね。
それからCADの試行錯誤からはじまり、だんだん工作機械の精度もよくなり、思いが少しずつ実現できるようになりました。
数学で金型を創る
木下 金型を製作する上で、先代の社長のやり方と、コンピュータを使って金型を作る近藤社長と、考えが違っていたのでしょうか。
近藤 先代社長は、型というものはそんなに難しいものではないという考え方でしたが、私自身は倣いフライスでさんざん苦労しました。木型を作って倣いフライスで削り、デコボコをひたすらサンダーで潰す。結局最後はみんな徹夜の仕事です。そういうものの作り方でいいのかと疑問でした。しかもAさんとBさんが作った金型が違うなんてそんなバカなことはないと感じていました。
当時ちょうどワイヤーカットも出始めたので、これはいい武器だな、そこへつなげていこうとやり始めました。
そもそもプレス加工、プレス成型は金属板材を金型、ツール(金型工具)を用いてプレス機内で塑性変形させ加工することです。塑性加工である以上は物理の論理に基づき解明することができますし、物理を実証する手段として数学があります。塑性加工を専攻しましたから、数学で金型を作っていけばいいのではないか、というのがひとつの発想です。
数学で金型を作るためには何をためていくのか。支配方程式、例えば微分方程式はわかっても、境界条件、初期条件の設定は、どうするのか。そもそも解析解は、あるのか。なければ数値解をどのような手法で求めるのか。など、さまざまな数学的アプローチの中で必要な物理情報の収集や形状データの作成・変更、そして実際の試作結果との整合性や数学モデルの妥当性評価など、種々のデータの分析や取捨選択が重要となりますね。
金型を「家業」ではなく「産業」として
木下 数式は表現の形であって、実際現象とあわせるために、物理現象の実験値や高切削材料特性と結びつけるのがミソですね。この考えが欠落して短絡的に考えると、数学で表現をしたら、金型は誰でも作れるのかということにはならないでしょうか。
近藤 そうです。誰でも金型が作れるということを目指しているのです。数学の論理を追求すれば、自然にものができるようになるというのが、金型の理想です。というのは、AさんとBさんが作った金型が違う、個人の技能に頼っているというのは、これはいわゆる先祖伝来の「家業」といった類と同じですね。
金型というのは大量生産をするための道具であって、それ以下でもそれ以上のものでもありません。そうすると、ひとつの企業体として、金型を「産業」として受け止めるのであれば、いつも同じ品質のもの、同じレベルのものがアウトプットされてくる。そうでないと産業とはいえないと思います。
理論に裏付けされた技術をもってものづくりにあたる必要があります。当然、勘や経験といった技能は知識とともに重要ですから、いかに勘や経験を技術の中に折り込むかということです。
3Dを核としたものづくり
近藤 当社では、金型製作システムとしてお客様から3Dデータを受領してから品質保証までを一貫した循環サイクルでものづくりを行っています。
- 受領した3Dデータから製品モデル製作します。
- 次に、ワンステップ法による解析を実行し、ブランク解析、絞り解析を行います。
- ツールモデリングの3D設計を行います。
- 実際に金型で使うツールモデル、諸条件を用いてバーチャルトライを行い、主に割れ・しわ・肉余りなどを評価します。判定基準を満足しなければ、再度、絞りの姿勢やツール形状の変更を行い、再解析・判定を実施します。
- 解析、バーチャルトライにより良質な製品が得られる条件を導き出した後、3D加工し部品を製作します。
- 3次元測定器、自動測定プログラムにより実加工品の測定を行います。測定した面データを3D CADに取り込み、必要に応じて製品へのフィードバックおよび3Dモデルの修正に使用しています。
- 3Dを核としたものづくりサイクルで品質の不一致(解析結果と実加工品との差)を検証することで、品質確保、品質保証に結び付けています。
金型を産業としてとらえ、経営者として企業を多少でも発展させようと思うと、この製品が何時間でどんな形になるのかが未知数では経営はできないのです。これは管理の問題ではなく、実際どういう形だったらできるのかが前もって分かれば、金型工場の経営としては非常に楽になるのです。
そういう面では、CAD、CAE、CAT、CAMというのは、一連の作業の中でどこで切れるものでもありませんし、これから先もなくてはならないものです。
木下 製品設計では、CATIAやJSTAMPを活用して、割れや肉厚変化などの製品の成型性をCAEを利用した評価を行い製品形状を定義する、そして金型設計では、Space-E/Pressを使用して、製品形状をきちんと成型できるように金型形状、つまりプレス工具を定義する。
この金型工具の形状作成においても、Space-Eに内蔵された簡易CAE 機能を使ってスプリングバックを考慮した工具の設計に取り組まれている。
いずれの設計においてもCAEを有効に活用して、CADで製品形状を定義し、CAMで金型設計を行っている、ということですね。
近藤 そうですね。今それで3D設計に取り組もうとしています。
システムが高度化していて、システム間のつながりが余計に難しくなってきているような気がします。
たとえばCADからCAMの世界は延長線上にありますから比較的簡単にいきます。ところがCADからCAEの世界、CAEからCADの世界というのは、まだけっこう手間がかかりますね。
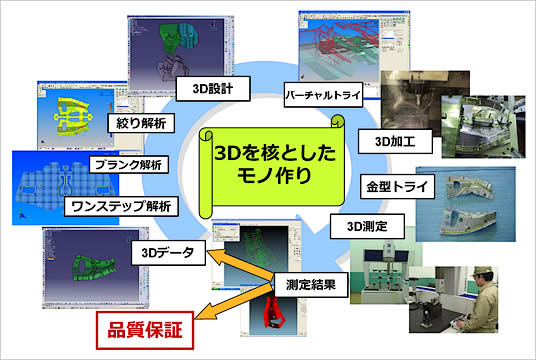
解析システムの活用
木下 解析(CAE)システムの活用事例についてお話いただけますか。
近藤 解析は、中がブラックボックスで、ただ単に形状データや材料データをインプットすれば、結果が出るだけでは、われわれがCAEを使ったことにはなりません。われわれがCAEを使うためには、ある程度は自由度があって、なおかつちょっとここ直してよということにも対応してもらえるようなソフトである必要があります。それで、JSOLのJSTAMPを使っています。
CAEというのは、あれぐらい職人技のものはないのです。図形を同じように定義をしても、それを解析するために使うパラメータやデータをどう選ぶかで、出てくる答えが違います。そういう面で、CAEもCADもそうですが、誰もが同じ答えを出せるわけではないのです。
絞り工程解析の事例
近藤 多工程に渡って、絞り、バーリング、圧縮と加工を行った際の解析活用事例で、各工程で解析結果と同等な板厚の確保ができ、品質レベルも良好な製品を作製することができました。
解析の活用で絞り加工による板厚の変化に合わせたツールクリアランス設定の最適化が行えましたし、加工に要した荷重も解析値と実行値とで比較的近い数値を得ることができました。
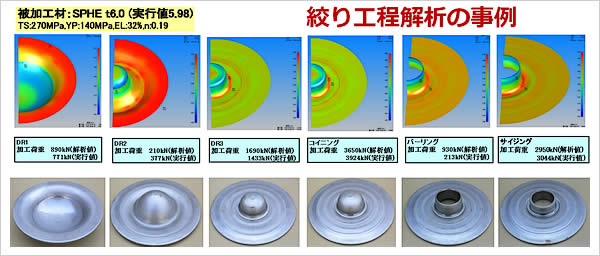
順送工程解析の事例
近藤 順送金型でも工程ごとに解析を実施し、金型を製作した活用事例で、フランジが割れる、大きなしわが溶接面に発生するという課題に対して、解析によるバーチャルトライを行い、フォーム成形とフランジ曲げの間に中間工程を設け、フランジの予備成形を行うことにより、金型のトライレス・修正レスを実現しました。
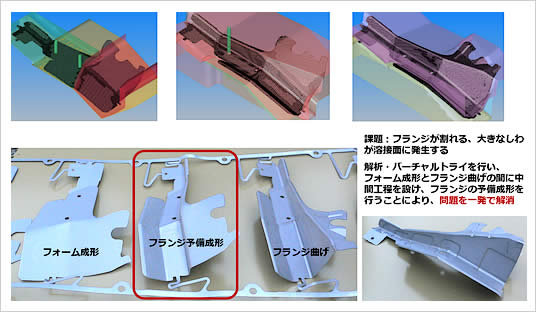
今後の課題
近藤 私たちが今一番望んでいるのは、鍛造解析と板成型解析がひとつのソフトでできることです。
塑性加工の世界では薄い板を絞って肉厚現象を見るのも取らえ方としては減肉鍛造です。でも今は板成型と板鍛造の解析ソフトは別々です。
最近は、比較的肉厚の大きな板厚の増減を伴う加工、いわゆる冷間板鍛造の技術を必要とする加工が増えてきています。
現状では薄い板から増肉や減肉をして鍛造する場合に、Simufact.formingですべて解析できればいいのですが計算時間がかかるため、何をするかというと、まずSimufact.formingでネライ形状を算出し、JSTAMPで加工条件を算出します。そしてJSTAMPで行った条件を再度Simufact.formingに入力し解析を行い検証をしています。
つまり、板成型と板鍛造と解析をする作業が分かれていて、作業を複数回行うことで加工条件を算出するという、非常に手間と時間がかかる作業を行っています。
1つの微分方程式の解を使って次の微分方程式を解くと考えると、後ろの微分方程式の解はそんなに重たいものではないでしょう。流れ学の世界だというとらえ方をすれば解決しないでしょうか。
木下 お考えはよくわかります。一つの支配方程式でさまざまな現象をシミュレートすることは理想的です。ただしその場合、汎用的に記述されているがために、利用側は種々の現象に精通し、またパラメーター定義や数値計算技術にかなり精通している必要があり、数値解の妥当性や数値的なトラブルへの対処にも専門的な知識が必要です。また、何よりも大きな問題は、汎用性が高いことによって、過剰なコンピュータリソースが要求される場合があることでしょう。つまり数百万、数千万のメッシュを扱うような問題に遭遇する場合があるということです。
近藤 同業者の中で話題になるのが、CADにしてもCAEにしてもどうやってソフトを選ぶのかということです。結局は自分たちのものづくりの思想、経営思想に合致するメーカーさんとソフトを選ぶということで、決してどれかがナンバーワンで、どれかがペケではないですよとお話ししています。今などは特にそれぞれに特徴があって、それぞれに十分使えます。
ただ後は自分たちがどうやって使うか。いくら解析をやっても、製品の品質を保証するための加工条件、工具を定義していくことができなければ意味がないのです。自分たちの身の丈にあったものを選ばないと、それはあぶく銭ですし、こんなもの使い物にならないという評価になってしまいますよと言うのです。
木下 ソフトを活用する場合、資産として所有する場合とサービスとして利用する場合の2つがあると思います。受託サービスは後者に相当しますが、状況や条件によっては、丸投げというケースもありますが、やはりコスト面など妥当性や急な対応への利用、ノウハウの蓄積といったことなど多少難点があると思います。一方で、年に数回しか使わないソフトを購入するのか、というのも経営者にとって悩むところだと思います。
こうしたことに対して、今注目されているビジネスモデルとして、クラウドによるエンジニアリングサービスがあり、私たちもその構築に取り組んでいるところです。
専門知識やノウハウ、そしてHPCクラスタやデータサーバーなど人的リソースとコンピューティング環境は、“雲(クラウド)”の向こうにあって、大規模演算でも長時間の演算でも、利用者に環境を提供するサービスです。
これまでのASPなどのベンダー主導型サービスとは異なって、これは利用者主導型の利用サービスで、特に中小企業にとっては画期的なサービス形態になりうる、と思います。長年、ものづくりなどの製造業の皆さんとともに歩んできた弊社としては、早期に立ち上げるべきテーマと考えています。
海外進出について
木下 海外進出のお考えを問題ない範囲でお話いただければと思います。
近藤 タイへ出ようというプランを持っています。自分たちが調べたことが本当に正しいのか、裏づけを取るために調査会社に調査を依頼しています。
円高対策ではないのですが、2009年に60周年を迎えましたが、実はその60周年に海外に展開しようと考えていました。企業もいろいろカスがたまりますし、何か新しい目標をもたないと衰退していきます。60というと還暦ですから、新たなことを一から始めるために、海外進出を計画したのですが、残念ながらリーマンショックで、最後の一歩だけまだ進めていません。
木下 それは取引先がタイに出られていたからその近くにということなのか、あるいは現地のメーカーと取引をされるためなのでしょうか。
近藤 やはり日系企業さんが一番の頼りになりますから、日系企業さんが一番たくさん出ているところですね。出て行くのであれば、資産と命を自分たちで守りやすいところに行こうと考え、タイに決めました。これも数学で金型を創ろうということと同じで、昔から見た夢を一つ実現したいということです。
以前から輸出を先行していましたから、こんなに商品として通用するものであればどこかで作ってみたいというのがひとつの夢で、60周年という区切りでやりたいというのが目標でした。
木下 弊社も数年前からタイに出ていますが、日系企業さんのサポート程度でしたので、もう少し本格的にやろうと、タイの秦日工科大学と定期的にイベントを開催するようなことを今企画しようとしています。
もう一歩踏み込んでテクニカルセンターを創ってサポートできる技術者を育て、現地のローカル企業さんの支援をするような仕掛けも考えて、少し幅広くやろうという構想があります。
近藤 御社のタイの拠点とはもう10年になる長いお付き合いをさせていただいています。先ほどお話のあった秦日工科大学や、御社の日系企業のお客様も紹介いただく予定です。うまく立ち上がれば、われわれも実習工場として使っていただきたいと考えています。お互いにメリットがなければ動けないことなので、お金だけのやり取りの世界ではなくて、日系企業の中でやれることでしたらやっていきたいと思っています。
木下 日本では形状作成やNCデータなどの受託サービスというのがもう成り立たない形になっていますが、中国やタイでは、仕事と道具はあっても、その道具を使える人がいないということが起きています。ですから、技術者を抱えて、受託サービスビジネスがあるんじゃないかなと考えています。タイも同じ状況だと思いますので、シェアできればいいと思います。
近藤 われわれがタイに進出するのもそういう理由がひとつにありまして、比較的日系企業が集積してきましたので、CAD、熱処理、材料なども拡充されてきまして、われわれが行っても商売になるということですね。
もうひとつタイを選択している理由は、製造拠点としての価値もあるのですが、FTA(自由貿易協定)が締結されていますから、ASEAN全体の営業拠点として、中国へ行くのもどこへ行くのも比較的便利だということです。
木下 時期としてはいつ頃をお考えでしょうか。
近藤 2012年を目標にしています。海外進出したことによって本体を食ってしまうようではいけませんから。でも、ここのところタイへの輸出が急激に増えています。危険を回避するために、難しいものは日本だそうです。優位性はなくならないと思うのです。
NDESへ
木下 今日はいろいろお話をお伺いし、CAD、CAM、CAE、CATの4Cサイクルを、ITを使ってものづくりをされている中で、最後に弊社への要望などお聞かせください。
近藤 Space-E/Pressで3次元設計に取り組んでおり、NDESの技術の方ともいろいろやらせてもらっています。
でも、もう少し3次元設計を使えるようにしていただきたいですね。内製の金型を作られるところは使えると思うのですが、我々のように売り型屋の場合、A社、B社、C社それぞれ設計の仕方が違いますし、それぞれにユニットが違うとなると、そのユニットを貯めるだけでも大変です。
これをタイに持っていきたいと考えています。というのは、図面が読めませんので、結局形状で見せるために、3Dの見取り図を描いたような図面が必要だなと思います。もう一歩進んで、テクニカルイラストレーションのような組み立て図面までいきたいのです。現場にPCを置いて組み立てのときに、何番をここに置きなさい、何番はここです、と指示ができるといいと思います。
中国の型屋さんの実力が上がってきましたし、コストと時間の勝負ですから、設計で価格が決まってしまいます。では、設計ってなにかというとCADの使いやすさで決まってしまうと思います。
どこかが圧倒的に先行すると、それがDefact Standardになります。Space-E/Pressは可能性を持っているので、短期間にパワーをかけていただければいけるのではないでしょうか。
木下 これからも、ご要望をお伺いさせていただきながら、3次元システムを活用した設計業務の確立に向けお役に立てるようお手伝いさせていただきたいと考えております。
本日は、まことにありがとうございました。
型技術ワークショップ2011 in 岐阜のお知らせ
型技術ワークショップ2011 in 岐阜で、ムツミ工業様が11月22日の工場見学コースに選ばれています。ぜひ、ご参加ください。
開催日時 | 2011年11月21日(月)講演会 |
---|---|
開催場所 | 岐阜県 じゅうろくプラザ(岐阜市文化産業交流センター) http://plaza-gifu.jp/ |
工場見学会 | 2011年11月22日(火) |
主催 | 型技術協会 |
詳細は、型技術協会ホームページ(http://www.jsdmt.jp)「ワークショップ」でご確認ください。
会社プロフィール
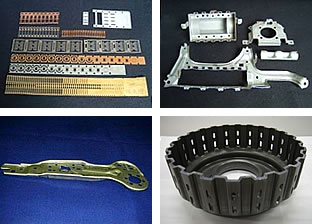
ムツミ工業株式会社様
URL http://mutsumi-industry.co.jp/(外部サイトへ移動します)
発足 | 1949年6月25日 |
---|---|
資本金 | 32,000,000円 |
本社 | 名古屋市北区瑠璃光町5-1 |
製造拠点 | 名古屋工場、小牧工場 |
従業員 | 約100名(平均年齢33.0歳) |
事業概要 | プレス金型及び設備製造ラインの各種専用機械の試作開発・設計・製作 |