![]() |
株式会社コイワイ 代表取締役 小岩井 豊巳 様 |
---|
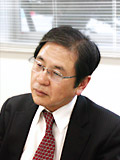
代表取締役社長
木下 篤
木下 御社の事業の現状と、今後どのようなことを考えておられるのか、御社特有の技術とあわせてお話をお伺いできればと思います。また、東日本大震災では、宮城工場が被災され、BCP策定にすでに取組まれておられ、わずか6日で復旧されたとお伺いしました。これについてもお話いただければと思います。
経営理念
木下 御社のHPを拝見させていただきました。HPの最初に御社の"経営理念"が提示され、「鋳造技術の伝承発展に努める」といった表現で、ものづくりを通して自社技術も合わせて後世に広く継承していきたい、との強い意思を感じ取りました。御社のその経営理念の背景と事業への取組みについて、お話いただけますか。
小岩井 コイワイの経営理念は、一番の柱に「鋳造技術の伝承発展」を掲げています。これは、先代が創業した際には明文化されたわけではないですが、私どもが後を引き継いでISO9000を取得するときに、マニュアルの中に理念を掲げる必要がありました。コンサルタントの方から、企業として何に重きをおいて企業活動をしてきたのかという問いかけがあり、私たちの企業活動すべてを網羅する意味合いがある、「鋳造技術の伝承発展」を中心に経営理念を策定しました。
■経営理念
私たちは、鋳造技術の伝承発展に努め
高品質のものづくりを通じて社会に貢献し
価値ある企業として歴史を刻む
先代は、「すばらしい製品を作ることはできるかもしれないが、それは決して自社の技術だけではない。鋳造が世の中に出現してから、いろいろな人たちがその技術に磨きをかけて今日に至っている。その技術を使わせていただいているのだということを十分に自覚したうえで、ものづくりをしていきなさい。」とよく言っていたのです。若いときは、お客様からお仕事をいただいて、お客様に喜んでいただけるものを自分たちが造るということで理解していたように思いますが、この年になってやっとその意味合いが理解できるようになりました。
鋳物の歴史は古く、紀元前4000年ごろ、メソポタミアで始まったと言われています。つまり、鋳造は人間のものづくり技術の中で最古の金属加工技術と言えます。
私は奈良の大仏を見ていると心が休まります。ここに関わった方たちはどんな人たちだったのだろう、どんな苦労を重ねどんな思いで鋳造を行いこの大仏を造っただろう?そして、この技術が1300年を経た現代の私たちに繋がっていることなど、悠久な歴史に思いを巡らせることができます。過去に技術を伝えてくださった方々の鋳造技術を今利用させていただいて、自社が生業を立てている。今度は私たちが積層工法などの現代の技術を盛り込んで、次の世代に伝えていこうと取組んでいます。
コイワイの歩み
創業当時
小岩井 私どもは、先代が脱サラをして鋳物屋を始めたのです。先代はサラリーマン時代は設計屋でしたので、もともと鋳造の技術や作業経験があったわけではありませんでした。資本がなかったために、大がかりな機械装置を導入することができず、鋳造を知らないのに砂型から入ったのは、手作業でできる仕事だったからです。起業時は、先代がサラリーマン時代に培った人脈で部品メーカ、自動車メーカと接点ができ、手作業でできる試作開発の一品物を作る仕事に携わっていました。
高度成長期には、幸いにも多くの車関係のメーカが国内で競争しながらいろいろな開発をしていましたので、私どももそうした仕事に関わっていくことによって、仕事量も増えて横の広がりもできてきました。そのときに先代がよく口にしていたのは、「自分たちが小資本で生きていくには、付加価値の高い試作開発の仕事が一番」という言葉で、私たちはそこに的を絞って営業展開してきました。
第1段階 3DCADの導入
小岩井 高度成長期は、業容を拡大しながら従来の工法だけで鋳造していましたが、次第にお客様からの品質や精度への要求が高まり、どんなに手先が器用でどんなに経験が豊かでも、手作業では限界がありました。ちょうど、3次元CADが出始めましたので導入をしました。当時は3次元で設計ができるということに驚いたものですが、残念ながら初期のCADはものにならず、成果を出すには至りませんでした。
でも、そうした取組みによって、お客様からは高い評価をいただきました。ものづくりも、職人的な技能だけでは時代の要求についていけなくなっていました。
第1段階は、3次元CADを導入しましたが、社内で悪戦苦闘したということです。
第2段階 マシニングで型の加工
小岩井 第2段階は、CADで作成したデータを利用して、マシニングで型を削ろうという方向に入っていきました。協力メーカさんとともにCAD/CAMを使いこなせるようになって、型の加工をマシニングで行えるようになり、マスター型の精度は格段に高まり鋳物の精度も向上しました。
第3段階 EOSINT S の導入
小岩井 2007年にEOSINT S※注を導入しました。この年は、コイワイの新時代への鋳物造りの転換点として、大変インパクトのある年だったと思います。
鋳物製品が複雑化し、鋳物製品を作るためのマスターの型、木型や樹脂型が複雑化していく。それを組み付ける技術も高度化していく。お客様が求めるものを早くご提供するということが求められる業種ですが、残念ながら複雑な型を作るのに多くの工数と費用がかかってしまい、鋳物を早くご提供するということができなくなってしまったのです。そこをRPで置き換えられるようになったというのは、イノベーションだったと思っています。
今になってみますと、EOSINTを導入した当時は、複雑な型を作るときの工数と費用を何とか解決したいと取組んできました。
リーマンショック後というのは、RPがあったから仕事を継続することができたのかなと今になって思います。あの経済危機後は多くのお客様が開発業務を凍結され、試作の領域においても仕事はほとんどなくなりました。その中でもどうしても必要な研究開発では、最低限の費用で試作品を作りたい。必要な鋳物も1個か2個でいいのです。「そういえばコイワイRPあるね。これなら木型作らなくていいんだね。じゃあ、コイワイに依頼しよう。」そうした流れで、お仕事を受けさせていただいたと思っています。
リーマンショック後、量産部門は減産による大きなダメージを受けましたが、試作部門はそこそこの案件で食いつなぐことができました。今となれば、RPを持っていたことがよかったと思っています。また、EOSINT S 導入により他社との差別化ができ、現在RPを活用した鋳造では弊社がトップだと自負しています。
ものづくりのプロセスが変わってきたことによって、新しいお客様に目を向けていただけるようになりました。時間がかかりましたが、国内外の展示会などを通じて繰り返しPRしてきた効果がでてきたと感じています。
※注)鋳砂を使用し、積層技術で鋳造用の主型および中子を3D データからダイレクトに造形するRPシステム
今後に向けて
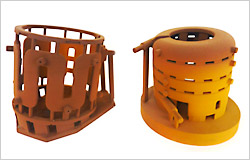
(EOSINT S で造形)
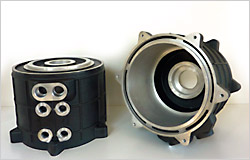
製砂型使用EVモーター
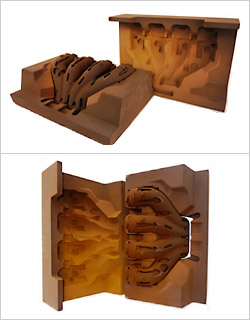
(EOSINT S で造形)
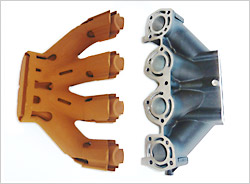
EOSINT S 製中子
木下 最近は私たちもRP(Rapid Prototyping)からAM(Additive Manufacturing)という表現を使い、試作だけでなく量産の現場においても、あるいは医療の分野やアートの分野でも活用できる有益な製造技術を提供できるツールとして、これまでより適用範囲の広い領域での展開を考えています。
小岩井 第3段階は木型がRPに置き換わっただけですので、次の段階は、おっしゃるようにAMの世界に入っていかないと、この装置は活かせないと思っています。
最近、お客様にお願いしているのは、私たちが気がつかないこと、設計段階で鋳物だからこうなるというのではなく、違う見方をしていただきたいということです。そうでないと私たちの良さも高まらないと思っています。鋳物屋=木型があって砂型があって金型があって、ということではなく、世の中になかったような構造や機能を持った製品を造り出せればと思っています。お客様の中にある固定観念を払拭していただかなければとも思いますし、私どももこれまでの技術の上に成り立ってはいるのですが、いったん白紙の状態にして見直し、新たな製品作りに取組まなければいけないと思っています。
EOSINT S による砂型積層鋳造の技術の向上とともに、EOSINT Mを導入して金属粉末の造形についてはなんとしても早く取組みたいと考えています。
木下 造形ですと、サイズに限界がありますね。この点は、どのようにされているのですか。
小岩井 RPの枠内に収まらないからといって、ゼロにする必要はありませんので、RPと既存の技術の両方の良さを組合わせたハイブリッドでいけば、相乗的によりよいものが造れます。
受注する製品のすべてでRPを使うかというと、そういうわけではありません。製品の難易度、大きさ、形状、数量等場合によっては、RPでは原価低減できないところがありますので、従来工法とうまく組合わせて取組んでおります。
震災後の仕事が減った時期、社の雰囲気を明るくそして皆さんの元気を取り戻すため本社工場のリニューアルをしました。この時期に国内に投資することに少々不安もありましたが、RP鋳造の先駆けとして次のステージに向かうため、設備の拡充と作業環境改善を行い基盤を強化いたしました。
その成果の表れとして、実際にRPを通じて新たな業界との接点が生まれ、私どものビジネスチャンスが広がりつつあります。これまで私たちが知りえなかった医療器械、建設機械、電気メーカ等の業界です。これまでは自動車メーカ中心で営業展開してきましたので、他の業界とのつながりが薄かったのです。仕事量が減ってきた中で私どもも各種展示会などでPRしてきましたし、お客様からもRPを使ったものづくりということでご依頼いただける機会を得て、国内の仕事量が減ってくる中ではありますが、多方面でご利用いただける機会が増えてきています。
動き始めたら今まで見えなかった仕事が見えてきて、私たちがやってきた自動車業界の納期、品質を非常に評価していただけるお客様が出てきています。大量生産品ではないし、かなり高機能な製品なので、すぐに海外に持っていくつもりはないということも聞いています。そうであれば、これからも国内で必要とされる場面はあるだろうと思っています。
そのためには、今持っている技術をもっと高めて体力強化をしなければいけないということで、宮城工場と本社地区をこれからもう一度構築しなおして、国内においてRPを使った鋳造技術では、断トツの企業になろうと思っています。
鋳物屋っていずれなくなるのではと社内でも時おり話をするのですが、一方で人間は歴史に学び歴史を作っていくと思っているので、そうすると私の中では、奈良の大仏に行きつくのです。今から1300年前にあれだけのものを作ったという技術があって、幸いにも1300年経っても、鋳造という基本技術が全く消えていないですから、これから先、形は変わっても鋳造という技術は生きていく、残っていくのではないかという期待を持っています。もちろん生き残っていくには、自分たちが時代の中で新しい技術を取り込みながら古い技術と融合させて、それに応じて私たち自らも変化していかなければ"残す"ことはできないと思っています。
大仏は、私の心のよりどころになるところです。鋳造技術が進化する過程において、当時の世界最大の鋳物製品だと言われていますし、当時の世界最高の技術だったと思います。
試作と量産
木下 試作と量産の事業は、どのような割合ですか?
小岩井 2011年の実績では約試作部門65%、量産部門35%です。
生い立ちが試作から始まり創業から20年間ほどは、実用製品を製造する事業には関わっていませんでしたが、あるお客様から、試作だけではなく量産もやってみないかとお話があり、これから先は量産分野の仕事も手掛けていかないと事業規模の拡大は難しいと思っておりましたので、ちょうど良い機会でした。また製造業としてお客様のお手伝いをしていくには、試作品だけでなく量産製品製造についても自分たちが携わっていかなければならない使命感も感じていました。しかし、それには大きな投資も必要でリスクもありましたので、お客様に甘えさせていただき、量産品に関する技術、品質、工程、物流管理など量産の手法をたくさんお教えいただき、現在に至っております。
量産に取組んだのは、お客様からの要求があったということと、社内的には事業拡大を狙うのであれば量産品を手掛けたいということで、受注してからお客様に教えていただきながら勉強しました。
以前は、試作部門と量産部門がそれぞれ50%ずつの比率になれば事業としては2本の柱になりますので、経営の安定につながるだろうという思いがあり、2008年にはほぼ50:50になりました。これでよしよしというときにリーマンショックによる経済危機により、量産分野の仕事が激減しました。しかしRP試作でそこを埋めることができましたので、今はあまり意識して50:50に持っていく必要はないなと思っています。
私たちが将来を展望したときに、コイワイの現状は試作分野、量産分野ともに、東日本大震災のダメージを負ったままですから、当面は比率よりも分野ごとの利益を確保して、しっかり回復させることです。
海外への取組み
木下 インドへ出張に行かれるということですが、海外展開の布石でしょうか。
小岩井 海外ということに関しては、遅ればせながら、インドの企業と接点ができインドへ事業展開をしていこうという段階です。すぐにインドに工場を作って生産できるかというと、現状は資本や人材もあるわけではありませんので、まずは市場調査から始めようと考えているところです。
日本の人口減少というのは避けて通れませんので、人口減少=市場の減少でしかないと思います。過去に人口が減っていって豊かになった国はないと言われていますので、日本でとこだわる必要もないなと思うのです。外に出て多くの人たちと接すると、同じ人間なのだと感じますので、必要とされるのであれば必要とされる場所でものづくりをしたいと思っています。
パートナーに選んだインドの方は、日本人が忘れている儒教の教えを持っていらっしゃいます。27歳の青年ですが、志は大きく、大学のときに2年間日本に来て日本語の勉強をしていました。日本とインドを見ると隔世の感がある。自分が生まれた村では栄養失調の子供たちもいる。学校には満足な教材もない。だから、自分が成長して得られたものは、還元していかなければならないと言っています。実際に少ない収入の中からお金をためて、中学にパソコンを寄付したりしています。彼は日本が好きなので、日本とインドとの架け橋のような仕事ができればうれしいと言っていたのです。
日本から見るとインドは貧しい国だけれど、日本のように豊かな国になりたい。日本の人たちがインドに来て、インドの労力を使って、日本が儲けるだけではなく、インドの人たちの生活を高めるようなこともぜひ考えてほしいと言うのです。これからは、安い労力を使ってものづくりをしようという発想だけでは、海外に出て行っても事業は成功しないのではないかと、彼と話をしていて思ったのです。インドだから安くものづくりができるだろうという発想ではなく、その国の人たちに役立つ企業として進出しないと発展していかないのではないかと思っています。海外に出て行った初期の頃とは違って、企業側も姿勢を変えていかないと難しいのではないかと思います。
木下 Glocalという言葉が出てきていますね。Globalというのは、日本から見た視点。でもLocalから見た視点で物事をやっていかないと、本当のグローバルにならない。現地の人たちと我々の文化がうまく融合できないとうまくいかない。Glocalつまりローカルを含めてやっていかないといけないと言われていますね。
BCP(事業継続計画)の取組み
小岩井 来年で創立40周年を迎えます。東日本大震災はあってはならないことでしたが、事業を見直すという点では良いきっかけになったと思っています。ありきたりの人材教育では得られない、緊急時にどう生き抜き事業継続を図るかということについては、去年の3月11日以降多くの事を学び、現場力が高まったと思うのです。
これは、被災した企業だからこそ体験できたことだと思いますので、そういう部分を大事にしていかなければいけないと思っています。実際に被災した宮城工場の社員の方々と、ここ神奈川では多少ものの見方、取組み方が違いますからね。
木下 宮城工場の被害はどうだったのですか。
小岩井 おかげさまで人的被害は全くございませんでした。建屋の倒壊もありませんでした。
被災したときに展示会の出展で私と常務は香港に、専務は関東のお客様のところにおりました、経営層が3人ともいない中で被災をしました。
BCPの策定に関わった者たちが、本社で対策本部を立ち上げました。BCPのマニュアルでは、まず第1に安否確認という項目をあげていますので、本社の者が努力をして安否確認をしました。私は、被災後、電話では本社との連絡がつかなく大変戸惑いましたが、メールで宮城工場の状況が確認でき一安心し、翌日早朝に香港から戻ってきました。私たちの災害に対する復旧活動が始まりました。おかげさまで工場建屋は倒壊が無く設備の被害も軽微でしたので、ダメージは少なかったのです。私たちが使っている鋳造設備は、特別なハイテクな設備ではなかったので、現地の社員たちで機械の復旧はできました。復旧に時間が掛かったのは溶解炉でした。溶解炉の中で溶けているアルミニウムが停電によって凝固してしまったことと、震度6強の揺れでしたから、るつぼが炉体の中で動いてしまって使用できなくなったということはありました。でも、二次災害としての火災などはなかったものですから、15日の深夜に電気が復旧して、16日からは工場の片づけをして、機械装置に通電をして機械の復旧に努め、17日には一部生産を再開することができました。不幸中の幸いだったと思います。
しかし、残念なことにお客様のサプライチェーンが寸断されていまして、私どもが復旧しても、お客様では他の部品が確保できなくなり、お客様から、コイワイが努力をして最短で復旧したのは喜ばしいことだが、今製品を納入してもらってもこちらは組立てができないから、しばらく納入しないでくれということで、大変がっかりしました。
しなくてもいい経験をしたことによって、仕事をする上での現場力というよりは、緊急時に生き残っていく、社を守るという部分で社員が大きな力を発揮しました。復旧に感謝して、ボランティア活動なども行い、宮城工場は皆の気持ちが結集できるようになりました。これからもいろいろな困難が起こることがあると思いますが、いかなる困難も乗り越えられる強い力を得られたと思います。
木下 トップの3人がおられない中、BCPに基づいて皆さん動かれたということですが、BCPを策定されたのはいつ頃ですか。
小岩井 2010年の5月から取組み2012年12月20日に策定しました。
2007年の中越沖地震のときに、素材メーカの工場被災により部品供給がされずに、自動車メーカのラインが止まりましたね。そのときに、お客様から震災対策はどうなっているのだという投げかけがあったのがひとつのきっかけです。もう一つは、2008年と2009年に宮城工場の若い人たちがインフルエンザにかかり、何人かまとまって休むということがあったのです。
今、BCPというと震災に目が向きますが、私どもは、事業継続計画ということで、感染症に対する対策というのが最初の考えでした。想定しましたのは、社員がインフルエンザにかかり、まとまった数の休職者が出る。この状態が1週間続き、宮城工場は減産を余儀なくされる。その結果、本社が宮城工場の代替工場として生産しなければならない状況になる。これが私どもが想定したBCPだったのです。震災ですとか、他の災害はあまり想定していなかったのです。
たいそうなマニュアルがあるのではなく、感染症に対して何をするのか、社員の安全を守るということから、まずは連絡網を構築する。次にお客様に迷惑をかけない、市場に直結しているのは量産品なので、量産品を生産している宮城工場は絶対に止めてはいけないということから、量産品の復旧を最優先する。三番目は雇用を守るということを考えました。
想定していたのは地震ではありませんでしたが、マニュアル作りの段階では盛り込まざるを得ないので、災害を盛り込んだうえで作っていますが、本社で代替生産するためにはどうしたらいいか、それを作っておこうということだったのです。本社で代替生産するためには、本社にも最低限の量産用機械設備を置いて、鋳造金型には取り付けにあたって互換性を持たせて、社員に順次教育を施して、どちらの工場でも作れるようにしようというのが、私どものBCPだったのです。
BCPへの取組みは、たまたまお付き合いしているシンクタンクの方が、神奈川県の要請で中小企業向けのBCPマニュアル作りのお手伝いをしているということだったのです。マニュアルができたときに、神奈川県の方からBCPのマニュアル作りの取組みをしませんかとお誘いをいただき、神奈川県主催の勉強会に参加しました。マニュアルといってもISOでやるような大量なものではなく、思ったよりもマニュアル作りが難しくなく、これなら自社でも作成できると思ったのです。神奈川県では専門家派遣事業をしていて、派遣費用の一部を県が負担してくれますので、この制度を利用して、あまり費用をかけずにマニュアルを策定することができました。
2010年7月に社内でキックオフをして、5ヶ月かけてマニュアルを作成し、2010年12月20日に完成しました。基本策定後翌年から各工場に浸透させていこうとしていました。2011年1月に、神奈川県から中小零細でBCPを作った事例が少ないので、秦野商工会議所で2月中旬に事例発表してほしいと依頼がありました。BCPに携わった者たちはみんな必死になって発表に向けてBCPのマニュアルの見直しをし、2月中旬に事例発表をしました。そして3月11日の被災だったのです。
木下 実際にそうした局面になると、意識が格段に変わるのでしょうね。
小岩井 BCPのありがたみを感じました。私を含め社員ももちろんです。
県の指導でBCPを作ったコイワイが幸いにも軽微な被災ですみ、BCPを活用して短期間で事業を立ち上げた。これを紹介して中小企業事業所へのBCP導入を進めたいと、行政や関係団体から要請を受けて、昨年から今年にかけて6回ほど、事例を紹介しました。
東日本大震災から1年経ちBCPの見直しを行っています。平成23年度第三次補正に応募して採択いただき、国内企業立地推進補助事業の助成金をいただく機会を得ました。この助成金を使って、西湘工場を中心とした試作事業、宮城工場の量産事業、万が一の時には双方で代替生産できるようにと準備をしています。
木下 今回の震災を機に企業もBCPの見直しや対策に真剣に取組む動きがあるようですね。
小岩井 体験して思うのは、BCPのマニュアルはたいそうなものでなくていいと思いますが、事業継続という意識づけを社員にしておくだけでも、全く違うと思います。いい条件のもとで復旧できたと思うのですが、事業継続ということが頭の中にないと、方向性が違ったと思うのです。なんとしても自分たちの工場を早く復旧させて、そこで生産活動をすることによって事業を継続しようというのが、災害マニュアルとは違うところだと思います。
木下 RPは、新しい加工の可能性がありますね。RPを利用した鋳造技術で変革されようとしている中で、ご一緒にやらせていただければと思います。本日は、御社の経営理念の骨子である鋳造技術の伝承、古の技術と新しい技術の融合、そしてBCPにより震災後速やかに復旧ができそれが社員の皆様の意識を変えることになった、ことなど貴重なお話をお伺いし、まことにありがとうございました。
会社プロフィール
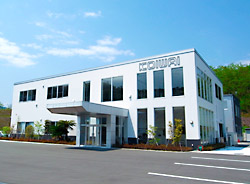
神奈川県小田原市羽根尾244-5
株式会社コイワイ
URL http://www.tc-koiwai.co.jp(外部サイトへ移動します)
本社 | 神奈川県秦野市曽屋60 |
---|---|
設立 | 1973年 |
資本金 | 2,000万円 |
従業員 | 55名 |
営業品目 |
|