人工関節手術ガイドをカスタムメイドで商品化へ
日本では、今後ますます進む高齢化社会にともなって人工関節の需要が高まりつつあります。ナカシマメディカル株式会社様は、より多くの患者様に快適な生活を送っていただくことを目指して、日本人の骨格や生活様式に適した人工関節の開発に日々注力されています。
今回は、日本人に最適な人工関節への取り組み、 FORMIGAの導入背景とその効果、さらに R&Dセンターの役割などのお話を伺いました。
船舶用プロペラから新たな分野へ
創業87年の船舶用プロペラメーカー
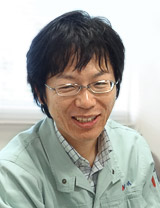
プロダクトマネージャー
開発部 設計グループ
課長代理 博士(医学)
山本 慶太郎 様
ナカシマグループの原点は、船舶用プロペラメーカーであるナカシマプロペラ株式会社です。1926年に中島鋳造所として創業してから87年もの歴史を持ちます。
船舶用プロペラは、モーターボート用の手のひらサイズから、大型タンカー向けの直径10メートル超級まで、あらゆる種類を一品受注生産でお届けしています。その一品受注生産のカギとなるのは、職人技とデジタル技術の融合です。この技術は世界一を誇り、マーケットシェアではナンバーワンという実績もあります。
2005年に船舶用大形プロペラを製造する玉島工場を竣工し、そこに大形プロペラのモノづくりを集約させました。また、国内だけでなく、よりグローバルな視点で製品をお届けするため、フィリピン、ベトナムにも製造拠点を保有しています。ナカシマプロペラは、世界の海を航海する船に、信頼ある船舶用プロペラおよび推進機器をご提供しています。
ナカシマメディカルの設立
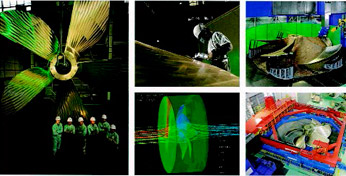
ナカシマグループは、人工関節の分野に新たに進出して、2008年の分社化により「ナカシマメディカル株式会社」を設立しました。これにより、人工関節、骨接合材料などの医療機器の専門メーカーとしてお客様の細かいニーズに対応する体制が整いました。
なぜ、船舶用プロペラの会社が整形外科製品の人工関節につながったのかというと、それは、我々が長年培ってきた船舶用プロペラのモノづくりの技術を人工関節に活かすことができるからです。プロペラと人工関節の製造工程はよく似ており、設計、鋳造、機械加工、仕上げ、研磨を行います。我々は、プロペラで培われた複雑な3 次元曲面加工や、職人技である鏡面研磨を人工関節へ応用することにしたのです。そして、人工関節の製品化により、一人でも多くの患者様の豊な生活の支えになることを目指しています。
我々の得意とする鏡面研磨は、表面に曇りがなく照明の光の線がまっすぐ映る技術です。この技術は、世界のどの人工関節メーカーにも負けないという自信があります。
日本人に最適な人工関節
正座を目指した人工関節
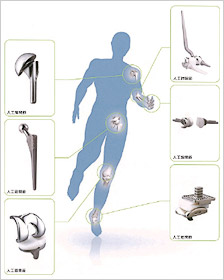
日本人に最適な人工関節のデザイン構築にも取り組んでいます。現在の日本における人工関節のマーケットシェアは、約9割弱が欧米からの輸入品です。
それは、医師の方が留学先のアメリカで学んだ技術を日本に持ち帰って臨床応用する中で、アメリカ製の人工関節を使うことが多いからです。
アメリカ製の人工関節は、全世界をターゲットに商品化されていますが、基本的な思想はアメリカ人向けの人工関節がほとんどです。アメリカ人は、椅子の生活が多いため椅子から立ち上がろうとしたとき、膝は110度ほど曲がれば生活に支障をきたさないという概念でデザインをされており、また患者年齢層が若いため軽度なスポーツ等を視野に入れ安定性を重視しています。
ただ、日本人の場合は、床、畳の上で生活することが基本なので、110度では不自由があります。そこで、正座ができる製品を目指し、最低でも和式トイレが使えるように膝が130度以上曲がる人工膝関節をご提供できるように努力しています。現在、日本人に最適なこの人工膝関節は多数の施設で使用されており、高い評価をいただいています。
また、日本人に比較的近い骨格を持つアジアの患者様にも最適な人工関節をご提供していきたいと考えています。
個別化医療に向けた技術構築
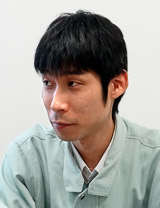
主任 花田 敏久 様
日本は、誰もが同じ水準で医療が受けられる貴重な国です。しかし、さらに付加価値の高い医療を目指すべきだと考えています。最近、国の経済産業省、厚生労働省では、個別化医療に向けた施策を示しています。我々もその個別化医療に対応するため、さまざまな周辺技術構築を行っています。2008年には、内閣府のスーパー特区(先端医療開発特区)認定を受けて、パーソナライズドインプラントという呼称を掲げて取り組んでいます。いわゆる個々の患者様に最適なカスタムメイドの人工関節ということです。ここ数年は、パーソナライズドインプラントの実現に向けた技術構築を行っています。
耐久性のある材料の商品化
人工関節は、生体適合性の高いチタン合金、コバルトクロム合金といった金属と緩衝及び摺動材として超高分子量ポリエチレンを組み入れて関節を機能させています。独自の技術でこの超高分子量ポリエチレンにビタミンEを混ぜた材料も開発し、2010年から世界初の材料として販売しています。
体内に埋入された超高分子量ポリエチレンは体液などの影響により酸化劣化してしまいます。そこで、ビタミンEを添加して酸化劣化を防止し材料特性を維持することで、耐久年数は20~30年になることが期待されます。
近年は人工関節の手術を受ける患者様の低年齢化が進んでいますので、これまでのポリエチレンであれば、10~15年後には再手術が必要になる患者様もいましたが、20~30年の耐久年数が実現すれば2回目の手術が不要になるという利点があります。
このように、材料を工夫することで人工関節の機能をさらに高めています。
FORMIGA導入と効果
FORMIGA導入の背景
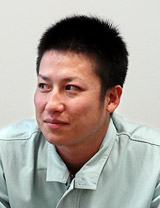
佐宮 大吾 様
近年、高齢者人口の増加にともなって変形性関節症を発症する方も増えています。それにより、人工関節へ置換する手術を受けられる方も年々多くなっています。個別化医療を目指したパーソナライズドインプラントを目指すことは最終的なゴールとして重要なのですが、さらに重要なのは手術に用いる手術器械です。
人工関節の手術には、骨を切る作業が伴います。大工道具のようなノミ、電動のこぎりなどを使って、人工関節を入れるために正確に骨を切る手術です。そのため従来の手術では、骨を切るための多くの手術器械が必要になり、実際の人工膝関節の手術では、250点ほどの手術器械を揃えていました。
これは、患者様の骨のサイズに合わせるため、実際使うものは1つですが、同じ器械をS、M、L、2Lなどのサイズバリエーションを揃えて、小柄な方から大柄な方まで全ての方に対応するためです。従って、手術中に医師や看護師が的確なサイズの手術器械を選択し、正確に骨を切るには、経験、技量が求められていました。
このような煩雑な手術を改善するため、最近では、コンピューター支援手術が採用されています。これは、患者様の骨のどのあたりを切ろうとしているのかをコンピューター上の画像で示して視覚的に位置を確認できるツールです。ただ、コンピューター支援手術は、正確に手術ができる利点はありますが、導入には2~3千万円という多額の費用が必要になります。手術数が多い大学病院などは導入できると思いますが、年間の手術が10~20例の病院では導入は難しいのが現状です。
そこで、比較的安価に提供可能であり、理想的な位置に人工関節が設置できるように個々の患者に最適な手術器械をカスタムメイドで作ろうと考えました。まず、個別化医療として比較的安く迅速にカスタムメイド手術器械の製作が対応可能な積層造形機を検討しました。さらに、実際の手術現場で使うには滅菌処理が必要になるため、滅菌処理の高温高圧に耐えうる材料であることも条件の一つでした。その結果、材料、装置とも我々のニーズに一番マッチしたのはNDESのFORMIGAでした。
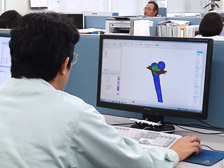
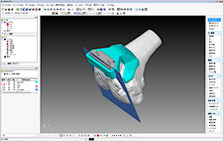
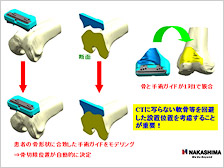
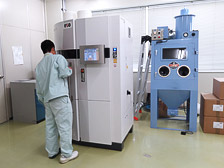
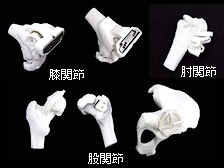
Space-Eによるモデリング
個別化医療では病院で撮影した患者様個々のCTやMRIのデータから3次元的な骨のモデルデータを構築します。モデリングするためのCADシステムもNDESから導入したSpace-Eです。術前計画を行い骨を切る位置、手術器械の形状などは、医師より指示があるので、その情報をもとにSpace-Eを使って設計しています。
曲面を得意とするSpace-Eは、カスタムメイドの手術器械を設計するとき、骨の表面形状と一致する面が作れるので非常に有効です。
FORMIGA導入の効果
Space-EのモデルデータをFORMIGAにインプットすれば設計通りの形状を造形できます。FORMIGAは、工業界では試作品だけでなく、最終製品を生産する装置としても使われており、複雑な曲面の高精度な造形がメリットだと思っています。
また、滅菌処理では高温になると樹脂の種類によっては溶けたり、変形したりしますが、FORMIGAには高温にも耐えられる材料があり、強度の高い材料を使えることも利点です。また、生体適合性に関しても、人の皮膚、体内に接触してもアレルギー反応が出ない安全な材料です。生体に使う材料には、さまざまな制限があり、それをクリアした材料ということもFORMIGA導入の要因です。
FORMIGAでは、主に膝関節、股関節、などの人工関節を正確に設置するために重要な骨を切る手術器械をカスタムメイドで作っています。現在、いくつかの施設と共同研究を行っており、さまざまな部位や治療で依頼があれば、その都度最適な製品をご提供できるよう、医師と相談しながら研究を進めています。骨を切るための手術器械をカスタムメイドでご提供できれば、手術中にサイズを選択することや骨を切る位置を調整する煩雑さは回避できます。それにより手術時間が短縮され、かつ高精度な手術ができることから、医師、患者様ともに負担が軽減されます。
さらに、初期投資と流通コストを考えると個別化医療という方向性には大きな社会的意義があると確信しています。
R&Dセンターの役割
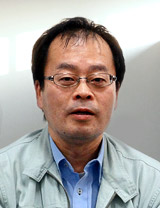
課長 技術士(化学)
西村 直之 様
産業技術研究開発施設整備費補助金を受けて、2010年6月に「R&Dセンター(先端イノベーション拠点)」を開設しました。
R&Dセンターでは、「基礎研究」「臨床研究」「モノづくり」「医師の手術トレーニング」などを相談に応じながら実施しています。手術練習室やCT撮影室を備えているので、医療機器の研究開発だけでなく人材育成の拠点としても、大学の先生や学生など医工学の研究者にご利用いただいています。博士課程の研究テーマであれば、遠くは旭川から1週間滞在されることもあります。さらに、年間1,000人の見学者も来られています。
我々は、日本全国の大学や研究機関とR&Dセンターで共同研究をしており、スーパー特区に認定された「パーソナライズドインプラントの実現」を目指しています。その研究成果により個別化医療に対応する人工関節などの製品をご提供するため、金属造形機、樹脂造形機を積極的に導入しています。
近い将来、金属造形機により造形を行った人工関節の商品化を目指しています。さらに、希少な症例に向けた医療機器開発の取り組みを始めています。
今後の課題
設計のコストダウン
造形のコストダウンは進んでいるので、今後は設計のコストダウンが課題です。医療機器、CT、MRIなどの画像解析ソフトはビジュアル化するだけなので、今後はそれを医療機器開発につなげ、治療に応用したいという新しい展開を考えており、画像解析ソフトのデータを直接CADで設計していくシステムが必要です。そのため、NDESには総合的な医療システムの開発に進んでほしいと思っています。
ネットワークシステムの構築
現在、地域医療ネットワークにより病院間で医療情報の連携を行いつつあります。将来的には、新しいビジネスモデルとして病院と医療機器メーカーが連携し、治療に必要なデータの連携が見込まれます。そのデータの取扱いやセキュリティに課題はありますが、医療機器、ソフトウェアも含めたネットワークシステムを開発できればと思っています。
日本政府は、官民一体となって病院ごと医療サービスを輸出しようという動きを本格化しています。日本の医療分野は世界的にも評価が高いため、積極的に推進されていくでしょう。さらに、病院、及び医療サービスと一緒に医療機器の工場も輸出できればと考えています。
おわりに
年齢とともに、自然と筋力は衰えてしまいます。そうなると背骨が曲がって前かがみになり、前かがみの姿勢が続くと股や膝などの関節に負担が加わります。人工関節のお世話にならないための一番の予防は、筋力を維持することだそうです。
大変お忙しいところ、貴重な時間を割いてお話を聞かせていただき、ありがとうございました。
会社プロフィール
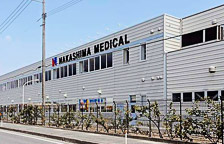
ナカシマメディカル株式会社
URL http://www.medical.nakashima.co.jp/
(外部サイトへ移動します)
本社・工場 | 〒709-0625 岡山県岡山市東区上道北方688-1 |
---|---|
R&Dセンター | 〒701-1221 岡山県岡山市北区芳賀5322 |
創立 | 2008年9月3日 |
資本金 | 1億円 |
従業員 | 172名(2012年12月1日現在) |
事業内容 | 人工関節、骨接合材料等の医療機器の開発、製造、販売 |