統合でグローバル化を加速
![]() |
ユニキャリア株式会社 開発本部 本部長 シニアヴァイスプレジデント 藤田 伸二 様 |
---|
ユニキャリア株式会社(以下、ユニキャリア)は、フォークリフトメーカーの日産フォークリフト株式会社(以下、NFL)とTCM株式会社(以下、TCM)が統合し、2013年4月に新たに発足しました。「フォークリフト業界世界No.1」を旗印に、現在は統合によるシナジー効果の最大化に向けて、業務系システム、エンジニアリング系システムの統合やグローバル化を加速させるための組織改革、システム化を進めておられます。
NDESは、業務系とエンジニアリング系両方のシステム化においてご協力をさせていただいており、今回、ユニキャリアの統合プロセスやグローバル化を加速させるために必要な取り組み、将来の展望などについてお話をお伺いしました。
補完し合える絶好の両社が統合
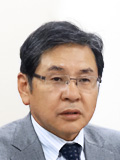
代表取締役社長
木下 篤
木下 御社は2013年にNFLとTCMが統合する形でスタートされました。両社の統合には市場の重複など、いろいろと難しさもあったと思います。統合にあたっての両社の強み、弱みについて、また両者のシナジー効果をどのようにお考えになって、統合されたのか、お話しいただけますでしょうか。
藤田 同業ではありましたが、商品軸でも地域軸でも比較的住み分けができており、それぞれの強み弱みを補完し合える関係で、良いお見合いだったと思います。
まず、地域で言いますと、例えば米国市場においてNFLは工場を持っておりましたし、市場シェアも比較的高かったのです。一方、TCMは、製造拠点はなく販売・サービスが中心でしたので、米国については、開発も含めた生産でシナジーが十分期待できると思いました。また、欧州もよく似ており、NFLはスウェーデンとスペインに工場を2つ持っており、TCMは統合時には、欧州に工場を持っていませんでしたので、同じくシナジーが期待できると思いました。
逆に最大市場である中国は、TCMが安徽省の合肥市に工場を持ち、販売台数も多かったのです。一方、NFLは、中国での販売実績はあったものの、中国の他社に委託生産していたため、残念ながら中国での販売台数は、少なかったのです。
ですから、海外での統合のシナジー効果は高いと判断していました。
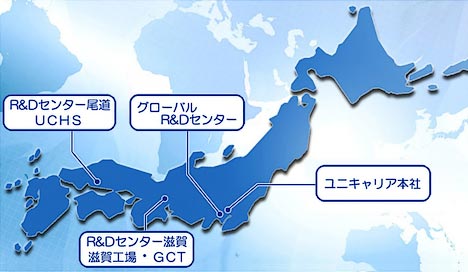
木下 日本国内ではいかがでしょうか。
藤田 日本国内でも、特に生産面で統合のシナジーは得られると判断していました。
というのも、TCMは滋賀に工場を持っておりましたが、NFLは工場を持っていなかったのです。NFLは社名のとおり、日産自動車(以下、日産)の一事業部として2000年までは日産の村山工場内に工場を持っていました。しかし、当時の「日産リバイバルプラン」の中で村山工場の閉鎖が決定し、同時にNFLの工場も閉鎖されたのです。その際に開発は日産自動車座間事業所に移りましたが、生産は高田工業に委託しました。ただ、生産委託をすることにより、製造原価が不利になっていましたので、日本国内に工場がある会社とない会社という意味でも、地域軸では、非常に統合しやすくシナジーも出しやすい環境にあったといえますね。
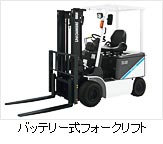
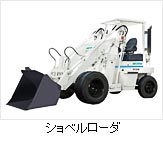
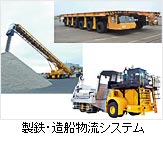
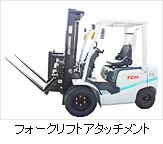
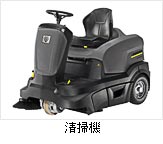
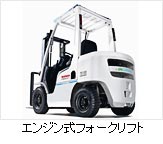
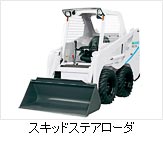
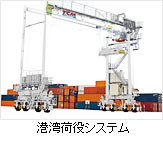
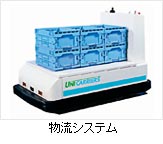
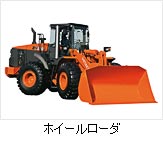
木下 商品の統合はどうだったのでしょうか。
藤田 商品軸で見た場合ですが、TCMの商品レンジは非常に幅広く、フォークリフトで言えば1トンから43トンまでラインナップしていました。一方、NFLは1トンから7トンとレンジが狭かったのです。また、TCMはコンテナを運ぶトランスファークレーンやリーチスタッカー、コンテナターミナルを管理するシステムなどの港湾機器や、無人搬送システムなど特殊車両も扱っており、重複が少なかったのです。このような状況から地域軸から考えても、商品軸から考えても大変良い関係だったと思いますね。
木下 統合による国内の売上高の位置付けはどうなるのですか。
藤田 トップはトヨタL&F、2番手がニチユ三菱フォークリフト、3番手が小松フォークリフト、4番手が我々ユニキャリアとなっております。
木下 フォークリフトの全世界のマーケット規模は、どのくらいなのでしょうか。
藤田 全世界のマーケット規模は、100万台といわれており、中でも最大市場の中国は22~23万台です。
木下 日本国内は、どうなのでしょうか。
藤田 良い時は10万台という時期もありましたが、現在は、6~7万台といわれています。
「世界No.1」を合言葉に意思統一
木下 こうしてお伺いすると両社が統合しやすい条件や環境にあった、ということですね。ただ、実際に統合するとなると、そう簡単にはいかなかったと思うのですが、どのように進められたのでしょうか。
藤田 2013年4月に完全統合しましたが、比較的時間をかけて統合の事前準備はできていたと思います。具体的にどうしたかというと、開発の中でファンクションごとに8つの分科会を立ち上げました。各分科会全てでNFLとTCMから1名ずつを出し合い、合計16名で、まずどのようにして統合を進めるべきかという話し合いからスタートしました。
木下 分科会が統合の現場の中心となったわけですね。しかし、両社とも歴史のある会社ですから企業文化の違いもあるでしょうし、意識面の統一等についても種々の難しさもあったのではないでしょうか。
藤田 単に統合することではなく、シナジー効果を最大化することを徹底させるために、全社的に「フォークリフト業界で世界No.1になる」という旗印を掲げました。そのためにどうすればいいのかということで、開発、生産などそれぞれの分野で、世界No.1を目指そうという視点を持ち、活動をしてきました。統合によって1+1=2になるのではなく、3や5、それをまた2倍、5倍、10倍にしていこうという目標を持って取り組んできました。
設計の考え方の違いに難しさ
木下 なるほど。では商品企画や設計、製造、管理等でご苦労されたことはありますか。
藤田 実は、日本国内が一番大変でした。欧米中は、先ほども申し上げたように、地域性の重複が少なかったものですから、その地域で生産していた商品に寄せるということで比較的スムーズに対応ができました。
一方、日本は生産工場を統合する必要があったため、2013年4月に、NFLの委託先である高田工業の生産を中止し、滋賀工場に全ての生産を移管しました。これはかなりスピーディーにできたのですが、購買や生産の面でやはり混乱は発生しました。
木下 システム面についてもご苦労があったと思うのですが、いかがでしょうか。
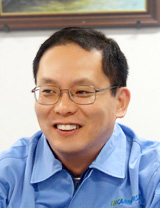
技術サポートグループ
エグゼクティブマネージャー
大塚 誠 様
大塚 まずはNFLの車両を滋賀で生産するために、部品表(以下、BOM)を滋賀の生産システムにまるごと移行する必要がありました。BOMは、NFLとTCMでフォーマットが違ったのですが、やはり同じ業界なので考え方は一緒であり、「比較的似ているな」と感じました。それでも、半年以上かけて移行を行い、2013年4月の統合と同時に滋賀工場で生産を開始することができました。
木下 BOMは、比較的スムーズに移行できたのではないかと感じたのですが、いかがですか。
大塚 そうですね。NFLに移行のノウハウがあったことが、比較的スムーズにいった理由の一因かもしれません。NFLでは、かつて日産のERPシステムを使っていたのですが、2003年にNFLで独立したシステムを持つことになりました。その時に購買、営業、設計等のデータを移行した経験が大変役立ったと思います。
木下 システム統合では業務系システムに加え、CADを中心としたエンジニアリング系のシステムもありますが、その辺の統合はいかがですか。
大塚 偶然ですが、3次元CADに関しては両社ともI-DEAS(一部NX)を使っておりましたので、比較的簡単に移行できるだろうと考えていました。しかし、同じCADを使っていても、設計のやり方は異なるので、思ったほど同じということではなかったですね。BOMの移行よりむしろきつかったです。ソフトは同じですが、考え方の違いは大きく、いまだ道半ばという部分はあります。
木下 尾杉さんは解析のご担当ですが、統合によるご苦労や今、取り組んでいることはありますか。
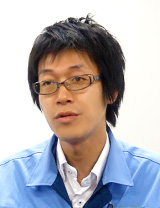
先行技術開発グループ
スーパーバイザー
尾杉 匤哉 様
尾杉 苦労というわけではないですが、昨年は統合の初年度でしたからインフラが整っていない中で、解析グループとして、どういうふうに将来の展望を見据えていくかということに注力してきました。現在はインフラが整ったので、次のステップとして、開発全体のシナジー効果が出せるように、我々解析グループが設計にどうやって関与していくかということが重要だと思います。
木下 具体的には、どのようなことでしょうか。
尾杉 試作前の段階で、いろいろなシミュレーションをしていますが、さらに開発の上流段階から解析グループも参加して、手戻りをなくしていくフロントローディングに取り組みたいですね。難しい部分もありますが、着手しないことには始まりません。上流段階からシミュレーションを行い、開発効率を上げていきたいですね。
藤田 車両の開発着手前に要素技術の開発や解析をしたり、コンポ―ネントの開発をしたりして、フロントローディングをしながら開発期間の短縮を進めています。それは全社的な命題で、例えば先行技術開発の中に解析グループを置くなど、組織もそれに合わせた形で構築しました。
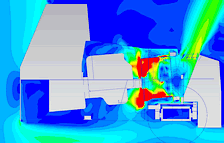
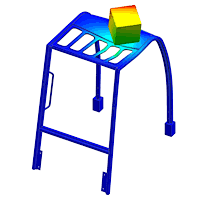
グローバリゼーションとローカリゼーションの融合
木下 御社が目指す「世界No.1」にはグローバル化が不可欠だと思います。今後のグローバル展開についての戦略や考え方についてお話しいただけますか。
藤田 生産の面でいえば、地産地消は大前提です。その中で、開発がどうかかわっていくかが重要になります。それは先ほど申し上げた分科会でも論議を重ねてきた部分です。大きな考え方として、開発を大きく2つに分けて考えています。
まず、ひとつの開発組織として、我々はここ座間のことをGRDC(Global R&D Center)と呼んでいます。ここは工場と一体となっておらず、どちらかというと本社機能の経営陣や営業などに近いところに位置し、営業からの情報をもとにグローバルに商品の開発をしていこうという組織です。その中で、車両開発、先行技術開発、解析、コンポ―ネント開発、実験も含め全てGRDCで取り組んでいます。
木下 もうひとつの開発組織はどういったものでしょうか。
藤田 もうひとつは、RRDC(Regional R&D Center)と呼んでいる組織で、全世界の各工場内か、もしくは近くに設置しており、大きく2つの責任があります。ひとつは米国や欧州など、その地域だけに特化した商品があるので、そういうものを開発すること。もうひとつは、GRDCで開発した商品を各工場で生産した場合、生産開始した後の面倒を見ることです。ですから工場の数だけRRDCがあります。現在は、そのように責任を分担しています。
木下 GRDCが開発の本丸で、RRDCに地域に応じた開発の柔軟性を持たせた形になっているのですね。
藤田 グローバリゼーションとローカリゼーションの融合というイメージです。まだ模索している部分はありますが、基本原則はこれで進めていこうと思っております。特に工場にあるRRDCはお客様に近いので、顧客要望の特別仕様の設計を手がけることが多いです。
木下 そうなると商品企画になるのですが、例えば、中国で特定の大型車両のニーズがあるとします。その場合、開発のゴーサインの判断はどこが出すのでしょうか。
藤田 それは日本の本社側でコントロールすることになります。東京の本社内に営業統轄本部がありまして、その中にマーチャンダイジング(商品企画:以下、MD)の機能を設けています。そこが全世界の中心で、海外拠点にもMD責任者を置き、そこと連携しながら現地の要望を収集し、最終判断をしています。
木下 そういう情報収集も大変だと思われるのですが、いかがでしょうか。
藤田 そうですね。基本的には各地にMD機能がありますので、情報取集は現地が行いますが、本社からも積極的に現地に出かけて情報収集します。先ごろ、ドイツのハノーバーで世界最大規模のフォークリフトショーがあったのですが、本社の営業統轄本部と開発部から数名が出張し、他社の情報収集や欧州の顧客を訪問したり、ユニキャリア欧州のMD責任者と打ち合わせをしたりしています。情報収集のルートはできているので、今後はその情報をもとに商品開発を行いマーケットシェア拡大につなげていきたいですね。
木下 今、苦戦している家電業界では、その国々に応じた商品開発ができていなかった面もあると思います。地域に応じたマーケティングは、グローバル化が進めば進むほど重要になると思います。
藤田 最近だと、バッテリー(以下、EV)式のフォークリフトがその例です。日本ではEV車の割合が約60%、欧州は約80%、米国でも約50%です。しかし、同じEV車でも米国と欧州では、バッテリー自体の引き出し方が異なるので、仕様を分けなければいけません。ベース車両は同じでも設計を変更し、アジャストしなければならないのです。同じEV車でも米国の商品を欧州に持って行っても売れないですし、逆もしかりです。
木下 少し話は戻りますが、商品開発の指示系統を本社に持つことは重要ですが、一方で海外の現地法人に権限委譲をしている部分もあり、御社の考え方や理念を伝え、明確にしていくことも大切だと思います。そのような会議やイベントは開催されているのですか。
藤田 年に数回は必ず開催しています。先ほど申し上げましたMDの部門会議は、全世界から責任者が集まってグローバル会議をしています。その後に、そこで生まれた商品戦略に対してどのように開発するかを決めるためにグローバル規模での開発部門の会議を行っています。
座間―滋賀の手法を世界へ
木下 現場に近い話になりますが、グローバル化を推進する御社では、CADなどのグローバル対応も必要になると思いますが、その辺の対応はいかがでしょうか。
大塚 もちろん、CADのグローバル化という課題に取り組んでおります。しかし、その前に滋賀工場と座間開発センターで設計・生産情報をつなぐことが必要になります。国内でつなぐ仕組みを作り、次に海外でつなぐ2段階になると思います。
木下 それは、どのようなイメージですか。
大塚 現時点ではCADのBOMと生産システムのBOMは異なりますが、CADのBOMがそのままエンジニアリングBOMになり、マニュファクチャリングBOMに連携されるような形態をイメージしています。CADのBOMが生産システムにつながることで、開発業務の効率改善に寄与すると思います。
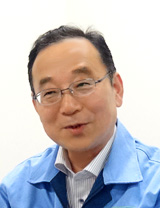
RRDC 滋賀 解析グループ
シニアマネジャー
横山 正文 様
横山 私はずっとCADに携わってきましたが、開発拠点がグローバルに散らばることになり、CADを含めたものづくりの手法を上手くマネジメントしていくことが不可欠だと思っています。そのためにひとつのツールとデータベースを用いて、ひとつのやり方で開発を行うことが必須だと考えています。簡単に言うと、だれが、いつ、どこに行っても同じ設計ができる世界No.1の仕組みを構築することです。
木下 それは、例えば海外で開発した図面を日本で引っ張り出したり、共有化したりできるイメージですか。そうなると、設計思想の標準化も必要ですね。
横山 はい、単純なオペレーションだけでなく、設計の考え方までを含めたCADのマニュアルを作りたいと考えています。3次元データは下流でどのように使われるかわからないので、同じような部品は同じ設計の仕方でなければ困ります。ですから、技を駆使したような複雑な設計データよりも、シンプルなオペレーションで作成された設計データの方がいいと思っています。そのためには、まず海外に展開する前に座間と滋賀の間でしっかりとした仕組み作りをして、問題点をつぶします。その仕組みができてしまえば、それを海外に展開するだけです。ただし時差の問題は国内ではどうすることもできませんが、予想できる範囲で事前に対応していく考えです。その時は、NTTデータグループの知恵やノウハウを活用できるでしょう。
バックアップとセキュリティが課題
木下 システム面で、特にデータ管理といった面で今後注力すべきテーマや取り組もうとしている課題がございましたらお話しいただけますか。
横山 バックアップの仕組みが課題と考えています。当社は以前からバックアップ用のサーバーを置いて、その後テープに移すというある意味、手間のかかる対応をしてきました。なぜそこまでバックアップが重要かというと、技術データは我々の命だからです。つまりユニキャリアの命のデータを預けるハードが安いサーバーだと不安で仕方がないのです。例えば地震や火事が発生したからといって、開発中のデータがなくなったでは許されないのです。そのために設計が止まることは大問題で生産現場、ひいてはお客様に多大なご迷惑をかけることになるからです。ですから、何事があろうとデータだけは消えない上手な仕組みを作りたいですね。また、今後グローバル展開していくなかで、開発の重要な資料にどうセキュリティをかけていくのかという課題も出てくると考えています。
真の世界一を目指して
木下 少し話が変わりますが、最近オリンピックが開催される2020年はどうなっているか、2050年はどうなっているかなど長期的展望をよく耳にします。御社としてはどういう将来展望を描いていますか。
藤田 会社としては、2021年に世界No.1になるという目標を掲げています。それは、NFLとTCMの統合だけでなく、先日、日本国内企業、オランダ企業、中国企業と資本・業務提携を発表しましたが、M&Aも含めての世界No.1です。定量的には世界マーケットシェア20%、売上高比営業利益率10%以上を目指します。この実現に向けて、3年ごとにマイルストーンを設けて進めているところです。2013年度がスタートの年ですので、2013~15年の3年間、2016~18年の3年間、2019年~21年の3年間というように3フェーズに分けて、ホップ・ステップ・ジャンプとなるようにしていきたいと考えています。
木下 商品面で世界No.1に向け、注力すべきところはありますか。
藤田 商品についてはMDと開発が一体となって取り組んでいます。先ほども申し上げましたが、EV車の販売は増えています。特にディーゼルに関しては排出ガス規制がどんどん厳しくなっていることもありますので、EV車とLPG車へのシフトが顕著になっていくと思います。そちらの商品の強化は必須ではありますが、しかし一方で、最大市場の中国は、実は約80%がディーゼル車なのです。そうなると中国を無視はできないので、ディーゼル車にも力を入れていきます。そういう意味ですべきことは多々あるのですが、グローバルではやはりEV車が重要になると考えています。
木下 2021年に向けた世界No.1とエコ技術が大きなテーマですね。その他にもブレークスルーするような技術や方向性はあるのでしょうか。例えば自動車業界であればハイブリッド車などは業界でリーディングを取る分岐点でもありました。
藤田 既に他社でフォークリフトにハイブリッド車を商品化している企業はあるのですが、自動車と違いフォークリフトは原則敷地内だけでしか使用しませんし、走る範囲も限られているので、自動車のように電気供給のインフラを考える必要がないのです。やはりEVにシフトしていくと思います。
木下 建設機械では車両にGPSを搭載し、稼働状況を把握する仕組みがあると聞きますが、そのようなアイディアはあるのでしょうか。
藤田 そこは、注目したいところです。車両の動きを見ることによりメンテナンス情報をモニタリングして、サービス担当者が適切なタイミングで訪問することができると思います。これについては、すぐにでもやるべき課題だと思っています。こういったニーズに合う商品の開発を効率的に進めながら、2021年の世界No.1の目標を達成できるようにしたいと考えています。
木下 当社は業務系とエンジニアリング系両方のシステムを担当させていただいていますので、両方の担当の方々からのご意見をお聞きすることができます。そういったことからも御社の2021年の目標達成に向け、システム面で今後とも全面的にご協力させていただきたいと思います。
本日はお忙しいところ、大変ありがとうございました。
会社プロフィール
ユニキャリアホールディングス株式会社
URL http://www.unicarriers.co.jp/(外部サイトへ移動します)
設立 | 2011年11月 |
---|---|
統合 | 2013年4月 |
資本金 | 187億5000万円(2013年4月現在) |
売上高 | 1,597億円(2013年3月期 連結) |
業務内容 | フォークリフト、コンテナキャリア、トランスファークレーン等、各種運搬機械の開発・製造および販売 |
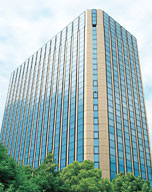

ユニキャリア株式会社
本社 | 〒140-0013 東京都品川区南大井6-22-7 ベルポートE館 |
---|---|
グローバルR&Dセンター | 〒252-8502 神奈川県座間市広野台2-10-1 (日産自動車 座間事業所内) |
R&Dセンター滋賀 | 〒523-0013 滋賀県近江八幡市長光寺町578 |
R&Dセンター尾道 | 〒722-0037 広島県尾道市西御所町14-15 第6堀田ビル7階 |