医療機器など新たな市場を開拓する
![]() |
八十島プロシード株式会社 代表取締役社長 伊藤 由香 様 |
---|
![]() |
八十島プロシード株式会社 専務取締役 河野 浩之 様 |
---|
八十島プロシード株式会社様は、PEEKやMELDINR(ポリイミド)に代表される高機能性樹脂材料(スーパーエンプラ・エンプラ)の切削加工と最新の3D技術を活用した造形加工を行う国内トップクラスの企業です。1937年の創業から、間もなく80周年を迎えようとする同社は、創業の地である大阪をはじめ、全国に製造・営業の拠点を構え、積極的な事業を展開されています。
2011年にFORMIGAをご導入いただき、医療分野にご活用いただいています。
このたびは、今年6月に就任した同社の代表取締役社長 伊藤由香様と、専務取締役 河野浩之様に現在のビジネスや今後の展開などについて、お話を伺いました。
国内有数の樹脂切削加工会社
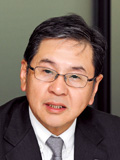
代表取締役社長
木下 篤
木下 御社とは、3Dプリンターとしてプラスチック材料を利用するFORMIGAをご採用いただいてからのお付き合いになります。最初に御社の事業概要について、お聞かせください。
伊藤 八十島プロシードは1937年に創業し、樹脂(プラスチック)の切削加工会社として事業を行ってきました。現在はPEEKに代表されるスーパーエンプラ・エンプラを中心に、高精度で精密な切削加工、3次元加工、溶接、曲げ、ラップ・ポリッシュなどによる各種加工品を製造するとともに、材料の販売も行っています。特に切削加工技術では国内トップクラスであると自負しております。また、2007年には神戸ポートアイランドに医療分野専門部隊である「NextMED開発室」を開設し、インプラント製品をはじめ、医療機器の各製品や部品の製造を始めました。そして、2011年に3DプリンターとしてFORMIGAをNDESから導入し、3Dプリントの受託と3Dデジタルデータ構築にも取り組んでおります。その造形品は、半導体や液晶製造装置、医療機器、自動車、建築、航空宇宙を中心に、プラスチックが使われている全ての分野で高機能部品として使われています。製造拠点は創業した大阪工場からスタートして、九州工場(1994年)、滋賀工場(2002年)、仙台工場(2006年)、そして、NextMED開発室の5カ所、営業拠点は東京、横浜、名古屋、大阪、福岡、仙台、滋賀、神戸の8カ所です。積極的な事業の推進に努めておりますが、健全な経営を心掛けており、大阪府より優良法人表彰を9期連続で受賞しました。今年で10期連続となる予定です。
木下 切削加工が強みとのことですが、具体的にはどのような加工分野なのでしょうか。
伊藤 当社が得意とするのは精密かつ複雑な加工技術で、通常の精密加工から超精密加工まで全てに対応できる体制を整えています。精密加工は、最近でこそ5軸加工が当たり前のように行われていますが、私たちが始めた頃は5軸加工機の方が先行していて、CAD/CAMの方が追い付いていない状況でした。その中で、1カ月かけて5軸加工のNCデータを作成し、加工するというようなことを行っていました。
手探りで医療機器分野に参入
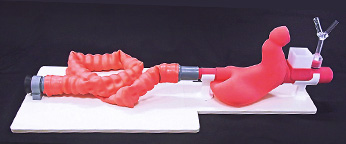

木下 2011年にカスタマーレポートの取材で、弊社社員が神戸のNextMED開発室を訪問したことがあります。あの当時も伺ったかもしれませんが、どのような経緯で医療分野に参入されたのでしょうか。
河野 たまたま、ある医療機器メーカーから一緒に創外固定器を開発してほしいという依頼がきたことがきっかけです。創外固定器とは骨折した時に使う添え木(そえぎ)のことですが、医療機器メーカーの方から、金属製の添え木は重く、レントゲンを撮ると、陰になった部分は見えなくなってしまう、という悩みをお聞きしました。このとき、添え木を樹脂化すれば軽くなり、レントゲンも透過するのでどの方向からでも状態を確認できるのではと考え、医療機器メーカーと共同開発しました。その当時(2007年)、プラスチックは人工関節では使われていましたが、体内に埋め込まれるものはポリエチレンが主で、それ以外にはほとんど使われていませんでした。しかし、今後は医療分野でかなり使われていくのではないかと考え、検討を開始しました。まず、整形外科を中心に全国で開かれるほぼすべての学会に参加して、さまざまな発表を聞きました。その中で、プラスチックの潜在的な需要はあるという確信を持ちましたが、需要を増やしていくには、私たちの側から提案していかなければなりません。そこで、開発拠点をどこに置くのが最適かということを調査検討しました。その結果、神戸のポートアイランドは、研究機関や病院、医療関連企業が集積し日本最大の医療産業クラスターになっているので、提案もしやすいし仕事もあるのではないかと考えました。そして、最初に部屋を一つ借り、積層造形システムも導入していない状況で、NextMED開発室をスタートさせました。
木下 最近ではどんな医療機器を手掛けられているのでしょうか。
河野 現在、かなりの量を作っているのが変形性関節症や関節リウマチの患者などに使用される樹脂製人工関節です。さらにCTデータを基にした骨格や気管支などの人体モデルも作っています。また、最終製品を作りたいという夢を実現したものとして、腹腔鏡手術のトレーニングキットがあります。腹腔鏡手術は開腹手術と比べて患者へのダメージは少ないのですが、手術が難しいため、かなりのトレーニングが必要です。その需要を見込んで商品を企画し、3Dプリンターの粉末積層造形システムを使って人体モデルの製品化に取り組みました。
より付加価値の高い仕事へ
木下 御社は長い間、切削加工に取り組んできたわけですが、積層造形をやろうと決めた理由は何だったのでしょうか。
河野 当社は切削加工用の材料使用量では世界有数の取り扱い規模があり、海外の材料メーカーとも懇意にしています。かつて、会長の八十島と何人かの社員が海外企業の工場を訪問したところ、そこにお面のような担当者の顔模型が飾ってありました。それが会長の目に留まり、「成形品でもない。削ったものでもない。どうやって作ったのだろうか」と質問したところ、「積層造形という方法を使って作ったものだ」という答えが返ってきました。そして、日本に帰って調べてみると、造形手法はかなり進んでいて、現場で十分使えるレベルになっていました。これまで積層造形のことは知っていましたが、実際に使えるレベルになっていることを把握していませんでした。それで使ってみようという話になり、取り組みをスタートさせたのです。
伊藤 当社が強みとする切削加工業は完全な受注生産で、いわば川下の仕事という位置付けです。それに対して、従来とは異なる発想やアプローチで、より付加価値の高い川上の仕事を生み出せないかと考えました。そして検討を重ねた結果、これからはデジタルデータを中心としたものづくりになっていくだろうと予測し、粉末積層造形システムを導入して、川上の仕事が期待できる医療機器分野への本格参入を決めたのです。
木下 参入してみて、いかがでしょうか。
伊藤 医療分野はそれまでの事業分野とは法規制などが全く違うので、まず営業部門を分けなければいけませんでした。また、従来とは異なる業界・分野でしたので、どこに売り込んでいけばよいのか、何があるのかも分かりませんでした。そのため、学会巡りをして、模索しながら事業を立ち上げていきました。
木下 NDESが提供する積層造形システムを医療分野で使えるようにするためには、医療分野における品質管理が必要で、さらに担当者は3年以上の業務経験がなければならないと法律で決まっています。そうした経験を持つ人材がいない企業は、社外から採用して、医療機器の認証を取得しようとするそうですが、法律で規制された領域でのビジネスの難しさはいかがでしょうか。
河野 本当に難しいですね。医療機器の製造販売業の資格を取ろうとすると、5年以上の経験が必要になります。事業を始めたばかりの私たちのところに、そんな経験がある人がいるはずはありません。普通に考えれば外部から人を採用するしかないのですが、当社は5年間かけて経験者を育てていけばよいと考えました。そこで、2009年に仙台工場は医療機器製造工場としての認可を取り、既に5年間がたっていますので、医療機器の製造販売資格を取ることは可能な状態になっています。
木下 その中で、一番苦労したのはどんなことだったのでしょうか。
河野 私たちはもともと製造業なので、早い時期にISO9001認証を取得して運用してきましたが、医療機器ではISO13485という国際規格になります。ISO9001は顧客満足が目的で、製品を同一の規格でつくるためのシステムであるのに対して、ISO13485は薬事法が大きく関係してきます。それが大きな違いなのですが、勉強してみたものの正直よく分かりません。しかし、そのようなことを言っても何も進みませんので、ともかくISO13485認証を取得すれば、品質マネジメントシステムを理解できますし、運用も可能です。そこで、まだ医療機器を製造していない段階で、ISO13485認証を取得し、後々、それが大きな成果につながることになりました。
メディアに出て知名度アップ
木下 ISO13485はいつ認証取得できたのですか。
河野 医療機器に取り組み始めて、1年後の2008年です。ISO9001があったので、足りない部分を付け足す形で、認証取得することができました。あと大変だったのが、医師との人脈作りです。いろいろな先生と共同研究に取り組む中で、CTデータを入手できるようになりました。当初、CTデータの提供を受けるには、その病院の倫理委員会の許可が必要ということで、その許可が出るまで何カ月もかかっていました。それではビジネススピードに追いつかないのですが、ともかく四苦八苦しながら、医師と試行錯誤しながら進めていました。その中でCTデータの個人情報を外して、メタデータの形にすれば、倫理委員会を通さずにCTデータの提供が可能になるというように流れが変わり、比較的容易に3Dデータの構築ができるようになりました。その後、3Dプリンターがブームになりましたが、その頃にはほぼ全ての3Dデータの構築や積層造形に関する技術を当社は手に入れていました。それで多くのメディアにも取り上げられることになり、八十島プロシードの知名度が大いに高まったと思っています。
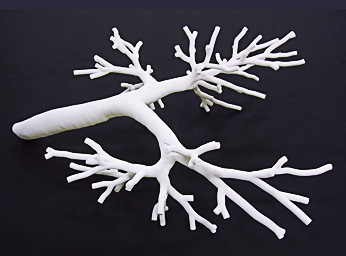
木下 3Dの人体模型がテレビドラマやドキュメンタリー番組でも取り上げられたと聞きました。
河野 「テレビドラマで使えるかもしれない」と会長がいい出して、京都太秦にある東映京都製作所へ営業に行ったのです。そこで、あるミステリー番組のディレクターに興味を持ってもらい、番組の中で、3Dプリンターで作成した造形モデルとNextMED開発室、八十島プロシードの社名などが出ることになりました。
ドキュメンタリー番組の方は、東大病院の若手医師が気管支のCGを作って、いろいろな形で活用する内容でした。その若手医師がCG画面だけではもったいないと言われたので、当社で3Dプリンターを使ってCGデータを基に実物大の気管支の模型を作りました。番組では、実際の気管支と寸分違わない形のこの模型で、病院の医師たちが内視鏡のトレーニングをする様子が放映されています。本物に近い感覚で枝分かれする気管支の中に内視鏡を入れることができ、特に一番内視鏡を入れることが難しく、肺がんができやすい右上葉部にも入れて、がんを取り除く練習ができます。普通であれば練習は無理なのですが、内腔1ミリ程度で複雑な形状をしている気管支をそのまま再現しているため、内視鏡を使った手術の練習ができ、医師たちには非常に好評です。
インプラントから医療機器まで
木下 医療分野では、インプラントから人体各部のモデル、医療機器、内視鏡手術トレーニング模型や関連製品など幅広く展開されています。それぞれ難しさが違うと思うのですが、どうなのでしょうか。
河野 インプラントは切削加工なので、作るのは難しくありません。問題となるのは情報の管理です。原材料の証明から製造過程、最終製品まで全てトレーサビリティを確保しなければなりません。それが一番難しいところです。
人工関節はこすれ合う(摺動)面があるので、表面がつるつるできれいな状態であればよいのかというと、それだけではだめで、先生方と議論を重ねました。
加えて現在、医療機器には切削油の付着が認められておらず、完全にドライな状態で加工しなければなりません。以前は切削油なしに加工するのは不可能だったので、切削油を使うと樹脂は吸湿しますが、それは仕方がないといわれていました。それに対して、私たちが切削油を使わずに加工することに成功したので、今は切削油がつかないことが標準になっています。
木下 売り上げ全体に占める医療分野の比率はどのくらいでしょうか。
伊藤 現在、医療分野は10%ほどの売り上げですが、業界の浮き沈みが少ないので、コアビジネスとして成長させていこうと考えています。この分野は欧米が先行していて、原材料も欧米メーカーから仕入れていますが、今では異業種の多くの企業が医療分野に参入しようという動きになっているので、取り組んでいる方向性は正しいと考えています。あとはビジネスとして、どれだけ成長させていくことができるかです。
働きやすさ重視で、工場・拠点をデザイン
八十島プロシード仙台工場 デザイナー
宮後 浩(みやご ひろし)様
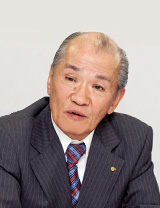
芸術学博士
(株)コラムデザインセンター代表取締役
(株)コラムデザインスクール学長
大阪府首席技能検定委員
近畿大学建築学科 非常勤講師
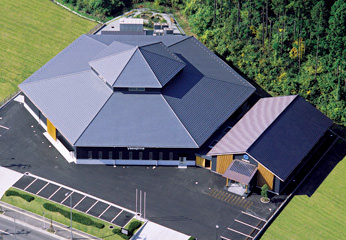
木下 話は変わりますが、お訪ねしたオフィスにしても工場にしても、とてもすばらしいデザインだと感じました。何かお考えがあってのことでしょうか。
伊藤 切削加工の会社というと、武骨なイメージが強いのですが、長年、当社と契約しているデザイナーの宮後 浩先生に、従業員の働きやすさや来訪者が受ける印象などを重視してデザインしていただいています。
工場は、その地域にあった設計にすることを前提に、社員、特に女性の意見を聞いて、テーブルの色からトイレまで全てを決めていきます。九州工場にはスロープがついているのですが、できたばかりの頃、初めて取引する半導体製造装置メーカーの方が検査にいらっしゃいました。その方はスロープに上がった段階で、「ここだったら仕事を出せる」といわれました。その後、工場の中も細かく見ていただくと、ソフト面に力を入れていて、防塵対策も万全な会社だと高く評価していただきました。
特に、2006年に開設した仙台工場は超精密加工をできるようにするために、さまざまな工夫をしました。敷地は東北大学の先生のアドバイスを受けて、砂が一番振動を吸収するということでドライサンドを敷き詰めましたし、岩盤にたくさんの杭を打ち込むことで地震にも強く、外部からの振動を抑えるようにもしました。また、超精密加工では測定が重要になるので、建屋を六角形にして、真ん中に検査室とクリーンルームを置き、どの工作機械からも最短距離で行けるようにしました。
海外展開も視野に、次の百年企業をめざす
木下 この6月に伊藤さんが社長、河野さんが専務に就任されました。今後の抱負などをお聞かせください。
伊藤 当社は、もうすぐ創業80周年を迎えます。私と河野、そして財務担当役員の3人は同じ年齢で、営業、技術、財務とそれぞれ異なる部門のトップとしてトロイカ体制で、創業100周年を見据え、技術、品質、信頼のさらなる向上に努めていきます。当社は目立たない、地味な分野のものづくりを担っていますが、お客さまからは「八十島プロシードの製品はきらりと光っている」と認めていただけるよう製販で連携し技術を磨いております。そして、そのことに社員が誇りを持てるように、次代へつなぐ百年企業をつくり出していきたいと考えています。
河野 当社は、ニッチな業界で量産といっても100個も作れば多い、という究極の多品種少量生産でものづくりをしています。今後、国内でものづくりをするには、多品種少量で、どう効率を上げるのかということが課題になります。そのための取り組みをさらに推し進めていきたいと考えています。
もうひとつ、ものづくりをデジタル化するには、設計部門が欲しいと考えてきました。しかし、受注生産の中ではなかなか難しく、それを何とか形にしようと、人員も集中させて、CAD/CAM化に取り組んできましたが広がりませんでした。それを打ち破る突破口となったのが3Dプリンターの導入です。3Dプリンターで、デジタル化の時代がやってきたわけですが、それだけでは付加価値は上がりません。付加価値を付けるためにはデジタルデータをいかに使いこなすかが重要で、そのためにはデジタルデータの構築が必要になり、それに取り組む中で、設計ができるようになりました。これをさらに進化させることで、高い付加価値を持った強い会社を実現していきたいと考えています。
木下 海外展開についてはどうお考えですか。
河野 現在、香港に現地法人を設立しようとしており、造形、材料、加工が日本で完結したら、それをグローバル展開していきたいと構想しています。納入先企業から海外で部品を供給してほしいという依頼がきたときに、装置を海外に置いておけば、日本で処理して、データを海外に送ることで、同じ造形品を作ることができます。そのための足がかりとして、香港を拠点にまずは調査を行い、技術流出せずに海外でものづくりができる体制を整えていきます。
木下 最後にNDESへの期待などがありましたら、お聞かせください。
河野 積層造形システムの導入がきっかけになってお付き合いが始まりました。今はまだ試作が多いのですが、なんとかして自動車関連などの最終製品を出していきたいと考えています。その時、一番使いやすいのはNDES が扱っているEOS社の積層造形システムだと思いますので、いろいろな情報やアドバイスをいただけるとありがたいです。
木下 当社の製品が最先端の医療機器加工に役に立つことができていると伺い、私も大変うれしく思います。ありがとうございました。
会社プロフィール
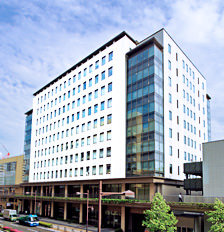
八十島プロシード株式会社
URL http://www.yasojima.co.jp/(外部サイトへ移動します)
本社 | 〒661-0976 兵庫県尼崎市潮江1-2-6 尼崎フロントビル6F |
---|---|
創業 | 1937年7月 |
設立 | 1954年5月 |
資本金 | 3,000万円 |
業務内容 |
|