次の世代を担う技術者が考える
これからの“ものづくり”
![]() |
NDES 代表取締役社長 木下 篤 |
---|
日本の製造業は優れたものづくりで、世界をけん引してきました。しかし、ものづくりの現場では、1980年代後半のCAD/CAMによる革新以来、大きな変化は起きていません。そうした中、多くの企業で、ものづくりの技術の伝承と新たな革新に向けた取り組みが行われています。
『人とシステム』発刊20周年を記念して、今号では自動車メーカーであるトヨタ、日産、ホンダ、マツダと部品メーカー/金型製造メーカーであるケーヒン、南武、ヤマセイの技術者が、今のものづくりの課題と今後について語り合いました(文中敬称略)。
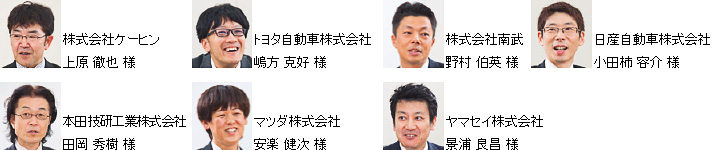
技能をどう伝承し、次につなげるか
―インダストリー4.0と日本のものづくり
技能伝承の取り組み、インダストリー4.0との関わりとは
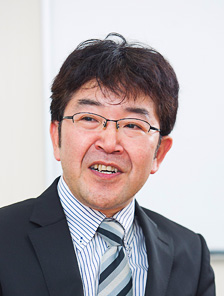
宮城第二製作所 生産本部
生産技術二部 塑型生技課
技師 上原 徹也 様
(ダイカスト金型設計を担当)
田岡 口火を切る意味で、少し挑発的な問題提起をします。2030年になったら、金型はなくなるかもしれないという意見があります。そうすると、金型職人は必要なくなるのではないでしょうか。どう考えますか。
安楽 先日、マツダはロータリーエンジン搭載のスポーツコンセプトカー「RX-VISION」を発表しました。このデザインは、マツダで進めている「魂動」を進化させた新たなカタチの提案です。この艶のあるボディーを作り上げているのは現場の職人であり、卓越した技能が絶対に必要ですから、まず職人がいなくなることはありません。ですが、この匠の技をどうやって伝承していくのかは課題としてあります。
嶋方 トヨタは、マツダの艶やかなデザインとは対照的なデザインでよりシャープで強い顔が特徴です。このデザインも、職人が今までの知見データを集結して作り上げています。どちらかというとトヨタでは、匠の技を残そうと懸命に取り組んでいます。例えば、以前、磨きは専業メーカーで分業化していましたが、今は磨きも我々がやってその技術を残そうとしています。もちろん技術革新もありますが、その上に技能伝承があって、初めて未来感のあるデザインが生まれます。結局、最後の上乗せは人間の力でないとできません。
上原 確かに金型はなくならないと思います。サプライヤーとしてはどう付加価値を付けるかが課題であり、その一つが製品の軽量化で、部品だけでなく金型にもダウンサイジングが求められています。そのためにも職人技を伝承して、金型づくりに生かさなければなりません。これから、若い技術者を育成して、世の中にない金型技術を確立していきたいと考えています。
小田柿 いま付加価値と言われたことは、主観的に言うと、車両の商品性に直結した特別な技術という視点が必要だと思います。自動車メーカーでも金型ばかりを担当している部署では、車両に目を向けなくなってしまいがちです。車両商品性で言うとドイツ車ではシャープな造形再現が進んでおり、特別な再現技術に着目しろと日産では言われています。金型を用いて造形再現するには多様な技術と技能がまだまだ必要です。
野村 今、遅ればせながらですが、社内で「職人技って、何だろう」という議論をしています。工場移転で製造部のベテラン職人の数人が辞めてしまい、以前と同じレベルで良品が出荷できなくなってしまいました。そこで、デジタル制御でどこまでできるかという方向に向かっています。まずは、職人を育てなければと思いましたが、精度を見るとNCの方が良かったりします。間違いなく匠の技を掘り起こす必要はある。では、どういったものを匠の技として守るのか、そして機械で作っていくものとをどう切り分けるのかを考えています。
景浦 当社のNC部門でも、若い人を育てることができなくなっています。一番若い社員でも35歳ぐらいになり、NC職人のようになっています。手順やノウハウを若い人に伝承するためにも、きちんとした規格や定義を行う必要があり、個人の技能を蓄積して共有することで脱職人が進むのではないかと考えます。これで、現場の作業を軽減できますが、職人技が全てなくなるわけではありません。
嶋方 トヨタでは、職人は技を極め、若手技術者がその職人技を数値化するということを一緒に取り組んでいます。例えば、"おっちゃん(職人技を持つベテラン技能員)"が、「音に違いがある」と言うと、若手技術者は音の違いをどうやって分けようかと考え、周波数を調べてデジタル化し、どこかにしきい値があるのではないかと統計的手法で分析します。
我々は、職人を最大限にリスペクトしようと常に考えているので、職人と若手のコラボは頻繁に行われています。
安楽 技能伝承の難しさは、業務の効率性を追求する側面に反するところがあることです。どうしても技能というものを技術化していく取り組みは必要になってきます。けれども、ものづくりの楽しさの本質はトライ・アンド・エラーにあるのではないでしょうか。それがプラモデルのように組み立てられたら、完成したときの達成感は得られないですよね。効率性だけを追求し過ぎるとその結果、ものづくりの魅力を市場に発信できなくなってしまいます。今一番問題だと考えているのは、新卒就職人気企業ランキングで、ものづくりの会社が低ランクに位置していることです。しかし、ドイツを見ると、ベストテンの6~7割はものづくりの会社で、何が違うのだろうかと思います。
そこで、先ほどの嶋方さんの話にあった若手にしかできない技能を技術化する面白さや、職人の技に関してはプライドをくすぐるような取り組みを行って、ものづくりの楽しさというものを市場に伝えることも私たちの役割だと思っています。
田岡 ドイツでものづくり企業が先ほどのランキングでトップにいるのは、車の国なので当然といえば当然です。ただ、本当にものづくりをやっているという意識は彼らにあまりないと思います。
安楽さんからドイツという話が出たので、インダストリー4.0について話します。私は、毎年ドイツで開かれるインターナショナル・オートモーティブ・プレスブリーフィングという会議のボードメンバーをやっています。その前準備のためにドイツへ出向いたとき、インダストリー4.0について、大学の先生に話をしてもらいました。その中で出てきたのは、なんと彼らも2020年以降、技能者がいなくなることを恐れているということでした。このインダストリー4.0はそれに備えて、技能を機械に置き換えることが狙いの一つなのです。ドイツも技能の伝承はできていませんが、日本との大きな違いは産学官で力を合わせて、今後20~30年で技能者がいなくなることに対応しようとしている点です。
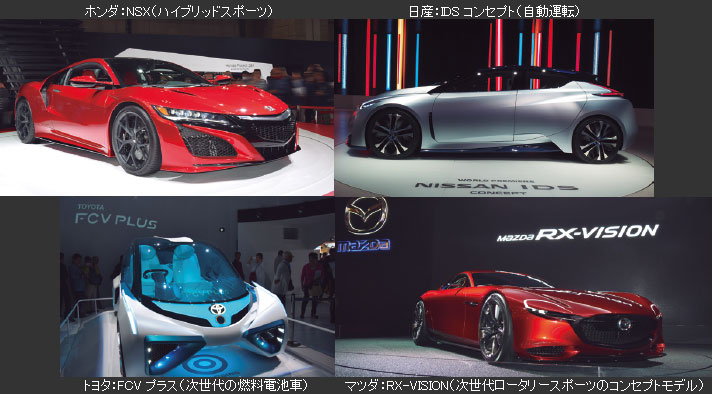
生産技術にこだわり付加価値を高める
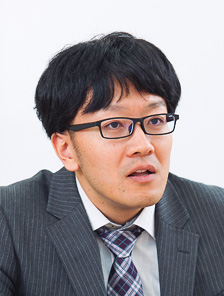
車両工機部 エンジニアリング室
主幹 嶋方 克好 様
(樹脂の金型設計を担当)
木下 そもそも日本は職人技ですり合わせをやりますが、米国はあまり得意ではないため、IoTを言い出して、ビッグデータで標準化をしようとしています。そこで標準化できたら、かなり品質の良いものができるかもしれません。そうすると、生産現場の革新につながります。
嶋方 確かに既にドイツの自動車工場は自動化されていて、同じ工場でもトヨタと比べると少ない人数で作業しています。ところが工程数を減らす考えは全くないようです。トヨタでは金型数や工程数の削減、型の縮小に取り組んでいるので、こだわるところが全く違います。
木下 トヨタさんは、IoT、インダストリー4.0とかの取り組みに対して、この路線でいけば、絶対負けないというのはあるのでしょうか。
嶋方 インダストリー4.0に関しては、今後生産現場が変わってしまう可能性はあります。そうした中で、脅威だと思うのは、グーグルやアップルなど自動車業界の外からライバルが現れていることです。ものづくりの次元ではないところでの競争になると思っています。
田岡 だからこそ、マネジメントが大事なのです。先読みの戦略で、待ち伏せしないと彼らに負けてしまいます。今はどこのメーカーも同じような車になっていて、付加価値がなくなっています。そして、30年後の車には電動化がくるのではと考えます。
そうした中で、日本のものづくりをどうするかを考えていかなくてはなりません。
嶋方 そのとき、IoTが進むと物流も自動化になります。そうすると、グーグルが自動運転をやって物流コストを下げるということもあり得ます。今後、3Dプリンターはそういうことに直結してくると考えられるので非常に興味を持っています。
木下 3Dプリンターは我々も販売・サポートをしています。この3Dプリンターによるものづくりは本来一品受注生産向きですから、量産には向いていません。でも米国は、それを数百台入れれば大量生産になるだろうという発想です。ただ、3Dプリンターは、切削加工とは違う全く新しいものづくりの技術として発展していくので、IoTなどの技術とうまく融合すれば別のものづくりとして期待できます。
自動車メーカーは何を目指すべきか
―日本連合で新たな相手と闘う
最新鋭の未来車は熟練技能員の手づくり
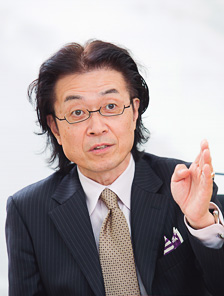
四輪事業本部 生産統括部
生産企画統括部 設備金型企画推進室
室長 田岡 秀樹 様
(ホンダの設備・金型の戦略企画を担当)
上原 今、自動運転が注目されていますが、本当に信用できるかどうか疑問です。例えば、私どもの現場で調子の悪い金型があり、炉の表示温度が680℃だったのですが、溶湯の色を見ておかしいと思い、直接測ると650℃しかありませんでした。結局、人間は680℃と表示してあったらそう思い込んでしまいます。ダイカストは五感で見ていく世界であり、先輩方からは「匂いをかげ、音を聞け、色を見ろ」と教えられました。このような現場でのすり合わせはこれからも続くでしょう。
今話題の水素自動車はどうなのでしょうか。
嶋方 水素タンクは、作るのがとても難しくて高度な技術の塊です。技術者から見ると、本当に安全に走らせるのはすごいことです。ただ職人技で作っているので、私たちから見ると、最新鋭の未来車というよりも職人がよく頑張っているなという感じです。結構泥くさいことも多くあります。
上原 そうだと思います。泥くさい部分はマシニング精度の向上やNCがさらに精密になっても残っていきます。私たちが韓国、中国で金型メーカーを選ぶ時の基準は、研磨機のテーブルを手で触って、黒いカスが手に付くかどうかでした。これを見るだけでメーカーの良しあしが判断できました。このような細かいところで最終的な出来栄えが違ってきます。日本では加工後にテーブルの切り粉を洗い流して、ウエスで拭いて、さらに素手で触ります。そこで100分の1の切り粉があったら寸法が出せるわけがありません。それを素手で触って、確認するかどうかの差が積み重なって最終的な金型の出来栄えの差になります。
景浦 そうです。寸法では見えない部分です。それは、まさに職人技の差だと思います。
嶋方 我々も最後のひと拭きは手で拭きます。これが一番きれいです。
田岡 車が日本のものづくりの代表選手だとすると、付加価値は開発スピードで、よほど早く開発しないと負けてしまいます。今はデザインが決まってから、発売されるまで2年から2年半ですが、その半分以下の1年ぐらいにしないと勝てないと思います。東京モーターショーに出た車が来年同じ時期に発売されるので、予約してくださいと言うことができたら、見に来てくださったお客さまは、きっと予約してくれます。それぐらいのスピードにしないと、ものづくりが少し良くなっただけでは、負けてしまいます。
小田柿 日産はものづくりの原点は日本と考え、金型造りにおいても技術開発、車両開発とのサイマル連携、工程計画は日本で実施しています。ただし、日産は外資系の会社といえ、グローバル体制でものづくりをしています。人材も世界中のリソースを使えばよいという感じです。金型を加工するところや鋳物を造るところは、納める場所に一番近いところが開発期間で優位ですが、デジタル関係など情報でやり取りできるところは、世界中で行っています。最近、生産技術部と人事部がルノーと同じ組織になったので、タレントマネジメントシステムを使って、従業員の持つ能力をグローバルで管理していて、ルノーと日産で相互に補完することを始めています。例えばブラジルで工場を立ち上げるときには、世界中から人材を選んで配置します。戦略的にローカルでやるところ、日本でやるところをすみ分けるとさらに開発期間が優位になると思います。
タッグを組んで今までにない車を作る
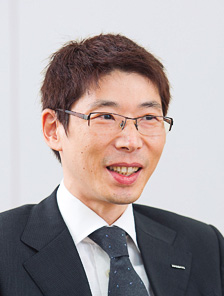
車両生産技術本部 プレス技術部
第二圧型技術課
主担 小田柿 容介 様
(プレス金型の設計を担当)
田岡 以前、日産のゴーン社長にお会いしたときに、役員の半分が外国人でこの多様性が日産成長のカギを握るということでした。さらに、そういう意味では他の自動車メーカーの何年も先をいっているということでしたが、実際はどうなのでしょうか。
小田柿 そうですね。英語が公用語になって10年以上たち我々も慣れてきました。上司を見ても、外国人と日本人が入り交じっていて、英語での会話は当たり前です。もちろん報告書も英語なので、日本人でも英語ができないと業務として成り立ちません。外国人との連携が進むと、一つの企業だけで技術や商品をカバーするのは不可能ですから、アライアンスやグローバルな視点での業務を進めることができるようになりました。
野村 当社もアライアンスの重要性は感じています。自社の強みをさらに強めるためには、外部のリソースをうまく取り込むことがカギになります。日本企業はともすれば自前主義になりがちです。
上原 弊社では新しい金型技術を社外に発信しています。金型は秘密が多くて、他社の金型を見る機会は少なかったのですが、私の発案で特許を取得した新技術を金型に使うことで当社の金型技術をアピールできます。
木下 日本では完成車メーカーを頂点にヒエラルキーがあります。そこで部品メーカーが情報を公開してしまうと、その構造が崩れると思うのですが、どうなのでしょうか。
上原 どの自動車メーカーもグローバル部品を調達していて、いかに部品として魅力があるかが採用される基準になっていると思います。
嶋方 以前はトヨタグループ、日産グループと、縦のつながりしかありませんでしたが、今では他グループ傘下の部品を普通に使っています。先ほど言ったようにグーグルやアップルがこれからのライバルになると考えると、日本の自動車メーカー同士が一つのチームと考えるべきです。そこではメーカー同士がタッグを組んで誰も考えなかった車を作っていく時代になります。
田岡 国内の各自動車メーカーは、方向性と守備範囲が決まってきています。だとすれば、国内でシェアを取り合う意味はありません。だったら日本連合をつくって、部品から、プラットホーム、ドアも共通にしていき、他業種から自動車業界に参入してくる敵に立ち向かうのです。
上原 結局、カップラーメンと一緒なんですよね。新しい商品がどんどんできて、それが売れている。ただその中でも、N社のカップヌードルのように売れ続けている商品はあるわけで、車でいえばミニクーパーのような定番をどう作るかが課題だと思います。
統一コンセプトの下、全社一丸で取り組む
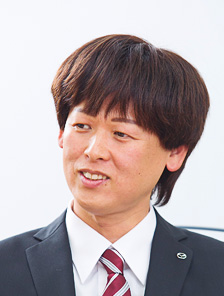
技術本部 ツーリング製作部
ツーリング技術グループ
主幹 安楽 健次 様
(全金型製作に関する生産計画
および技術開発を担当)
田岡 上原さんと全く同じ意見です。その方向性の一つを明確に出されているのは、マツダさんだと私は思っています。“御神体”を作るところから始めるのですよね。
安楽 社内で“御神体”と呼んでいるのは、デザインテーマオブジェのことです。これまでは、デザイナーがアイデアを考え、その2次元スケッチを受けて、クレイモデラーが実車モデルを作るというやり方でした。しかし、このやり方を続ける限りでは、デザイナーの発想力やモデラーの表現力を今以上に上げることができません。また日本の車は、それぞれの車が独立したデザインになっているので、ブランド価値というものをお客さまの中に浸透させるには、そのことがマイナスでした。
そこで第6世代群の車は、デザインスケッチを描き起こす前にデザインテーマを決めて、そこからモデルを作っていくという考え方を採用しました。まず、全体の方向性を具現化した3Dモデルの御神体を作ります。それがチータをイメージした形状でした。デザイナーは、そのチータのオブジェを見ながら車のデザインに落とし込んでいきます。実はもう1段階下に、それぞれの車種専用にテーマオブジェがあり、例えばアテンザであれば獲物を追いかけているチータが一番スピードに乗った最速の状態を表現しようと、アテンザ用テーマオブジェを作りました。それで、アテンザ、アクセラ、デミオとデザインが少しずつ違ってくるのですが、デザインテーマの源流としてのオブジェの思想は統一意思として同じです。
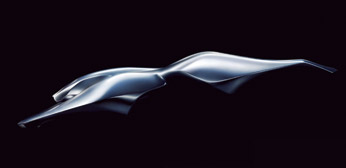
田岡 型も同じような考えで造るのでしょうか。
安楽 我々は、技能に対して深みを出していこうとしています。金型磨きは技能で、ぴかぴかに磨けばよいわけではありません。金型は板金のデザインに直結するので、キャラクターの流れ、ハイライトの流れを忠実に再現するために、どう磨くかまで落とし込みます。その結果、従来の磨き方から変わり、現場でクレイモデラーと磨き担当が一緒に議論しています。クレイモデラーからすると、このデザインで一番大事なのは生命感を感じさせるハリ感なのに、今までの磨き方ではそれがなくなってしまう。「そのハリ感を磨き過ぎて猫にしているよ」とずばり言われて、現場はどうやればいいのかと議論をして、磨きのやり方を模索しているというのが実情です。
そういう深みを作業に取り込んで、他ではまねできない日本のものづくりとして、大事に残していきたいと考えています。
木下 デザイナーからものを作る方まで、統一したコンセプトを持っているということですね。
安楽 全社一体となって、同じベクトルでやれるのは、開発も生産もデザインも広島で固まっているという地勢的な強みがあるからです。エンドユーザーに届ける車づくりのコンセプトを、デザインからものづくりの現場まで皆で共有しながらやっています。それで、ものづくり側がデザイン側の思いを知ろうとしたり、逆をやったりしています。その中で、金型の削り方も変えようとしています。通常は、断面方向の形を出すために走査線パスで加工するやり方でした。ところが、それではデザインが求める形状をうまく作り出せないことが分かってきています。そこでデザインと効率性の両方をブレークスルーするやり方にしようと、加工がベストになるようにNCデータも作り替えています。
景浦 自分たちもそうです。こうやればアウター部品、製品はきれいに仕上がるのではないか、と考えながら作業をしています。以前は、当たりづけ、見込みというのはNC課がこの部分に当たり、見込みが必要だからと付けて、プレスしてできた製品をNC課の人が見て、ここが当たっていないとやっていましたが、それでは効率が悪い。実際にどれだけ磨いたか、その作業者に当たりづけ、見込みを作ってもらうことでより効率的になりました。また、こういうことが、すぐに反映できるようになりました。
技能をデジタル化し、さらに人間が飛び越える
田岡 金型はオリジナルデータ通りにやっても、塑性変形して、スプリングバックしますね。それはどうするのでしょうか。
安楽 それも含めて、見越してやっています。
田岡 同じようにホンダもやっています。スプリングバックなどの不具合を金型でコントロールする量は100分の1ミリ単位ですが、それを見込める金型ができることが日本のものづくりの強みです。非接触式の3次元測定機で測定したデータを基にして、面を盛ったり、張ったりしますが、最終的には技能、高度な技術が必要で、3次元のデザイン面を持ち上げて補正します。金型技術者のモチベーションがないとできません。
嶋方 今までトヨタの車は量産向きで面白くないといわれていましたが、社長が変革のキーワードとして「もっといいクルマをつくろうよ」というキャッチフレーズにしたので、それを受けて皆が考えるようになりました。今までは生産技術の方が強かったのですが、生産技術がデザイナーのところに入っていってコラボレーションし、デザイナーがやりたいことをやらせようとしています。その結果、昔に比べると、シャープで未来感がある車ができてきています。面データをデジタル化して生かしているのは主に海外です。海外で生産している車は型が二つ、三つあります。そこで最初に職人が作り込み、それを3次元測定機でデジタル化して、CAD/CAMに持っていく。このようなサイクルを重ねることで、さらに良いものができます。技能を伝承して、それにデジタルが追いついてきて、また人間がそれを飛び越えていくという関係で、最先端はあくまで技能でやっています。
小田柿 日産もやっている方向は同じで、1番型は匠と共に造り、2番型はデジタルコピー技術を使います。匠の造り込みをデジタル化、つまり数値化することで次につなげます。デジタル化によってある程度品質の良い型ができますが、ロシアとタイでは環境が違いますし、設備や温度などバラツキがあるので、それをデジタル化してさらに改善していきます。そのためには技能が必要で、熟練の技能員はそれに対応できます。
田岡 1980年代後半、CAD/CAMによる金型造りの革命が起こりました。それ以降、それを超える動きは出てきていませんが、今後の方向性を考える上で注目すべきなのはダイハツです。ダイハツの軽オープンカー「コペン」は鉄の骨格構造に樹脂製のフェンダーとバックドアとボンネットを取り付けたもので、フェンダーとボンネットを替えると違うモデルになります。樹脂はさびないので、骨格の塗装ラインも簡単になり、全体的には短い工程で完成車ができ上がっています。ここで今まで話してきたことをひっくり返すような内容ですが、プレス型をなくして、樹脂にすればデザインは自由自在です。
ダイハツは、別の車種でも同じような取り組みをされていますが、このような流れの先には、まさに嶋方さんが言われた、グーグルのようなIT企業との融合があると思います。
人をどう育て、競争力を強化するか
―野心を持つ若者たちに現場の面白さを教える
CAEを絶対視する若手に感じる危機感
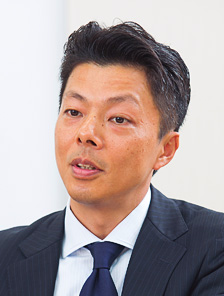
代表取締役 野村 伯英 様
(南武はアルミダイカスト・樹脂向け金型用油圧シリンダーを製造する)
嶋方 話は変わりますが、私たちの世代は、CAEは単なる"まねっこ"だと考えています。しかし、若い人は絶対視している面があって、それに危機感を抱いています。CAEで分かったから、さらにセンサーを入れにくいところに懸命に付けて実験データを集めるのですが、結局そのデータはあまり使われていません。データを取ることで満足してしまっているのです。
田岡 ネット世代といわれる新入社員が入ってくるわけですから、人材育成のやり方も変わってきます。これからは、プレスでもいきなりシミュレーションだという人たちが主流になっていくわけです。
野村 CAEで油圧シリンダーが折れるかどうかが虹色で表現されると、正しそうに思えて、若手社員は信用してしまいます。「あくまで仮説だ」と言っても理解されないので、彼らの言い分を聞きながら、疲労試験をやり、裏を取らせています。そうすると、3万ショットで折れると言っていたのが30万ショットぐらいもつことが分かったりします。試験結果は大手メーカーから性能品質を求められたときの根拠にもなりますし、バーチャルを過信せずに、最後はリアルで裏付けを取ることが大切です。
安楽 マツダでは、新人が生産技術に入ってきたときには、いきなり技術本部の仕事をやらせるのではなく、開発の方に3年間研修に出します。その研修を通じて、開発から生産に至る一気通貫のプロセスを実際に体験させます。その後、生産技術に戻ってきて、クルマとして必要な機能を念頭に置いて、ものづくりを考えてもらうという取り組みです。新人は華やかそうなシミュレーションや設計がいいと言いますが、ものづくりを知らずして、どうして設計ができるのか。でなければ、単なるオペレーターになってしまうので、現場でものづくりの大変さや素晴らしさを実感させています。
上原 昔は図面を見ながらいろいろな知恵を出し合って、時にはぶつかり合いながら信頼関係を築いてものづくりができていました。それが、全体的に見て、コミュニケーションがなくなってきています。「3Dデータを出したから、後はよろしく」という感じです。それに、当社は宮城に工場があるので、栃木の開発では自分が設計した部品がどうやって作られているのか、まして海外で生産されていると手に取って見ることができない。そんなつまらないものづくりはないと思います。現場が近くにあって、怖い職人から呼び出されて怒られながら設計者が学ぶことはたくさんあります。今後はデジタルをうまく融合させながらコミュニケーションも大切にできればと思っています。
私は、若手技術者に、「失敗してもいいから思いっきりやってみろ」と、言っています。チャレンジなしでは伸びないですから。
ものづくり教育に力を入れ、技術員を育てる
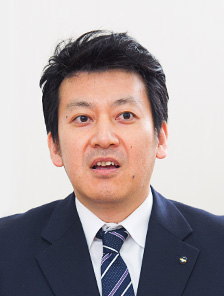
技術部 NC課
主幹 景浦 良昌 様
(板金プレス金型、射出成形金型を製造するヤマセイで、NCデータ作成を担当)
野村 やらなくてはいけないと考えながら、なかなかできなかったのがジョブローテーションです。短期的に見ると、戦力が落ちてしまうので、トップがよほど腹をくくらないとできません。けれども、設計開発をやったら、次は別のことをやるという形で経験した人間が初めて、全体を考えることができるのです。
景浦 当社はNCデータ作成の専任者をモデル作成の専任者の隣に座るという席替えをしたことがありました。そうすると、NCデータが作りやすいサーフェイスの作り方を話し合ったり、簡単なサーフェイスであれば、NCデータ作成の専任者でも作れるようになったりと、お互いの業務の理解が深まり、効率よく作業が流れるようになりました。
田岡 我々はものづくりが好きで会社に入ってきています。これからの人たちは果たして、ものづくりが好きで入ってくるでしょうか。大学院卒で、ネット世代で、親にも怒られたことがないような若者たちを現場で育てていけるのか、大きな課題です。
嶋方 少し前まで大学の後輩に対するリクルート担当をやっていましたが、彼らはゆとり世代といわれていますが、とても野心的でもあります。ぼくたちの頃はものづくりがやりたいという程度でしたが、彼らはグローバルに、世界に通用する車づくりをしたいと考えていて、語学力も優れています。そういう学生たちが多くいて、やっぱり汚れ仕事を嫌う面もありますが、ものづくりの面白さを説明すると納得してくれたりもします。
小田柿 昨年から「モノ造り教育」と題して、技術員向けに開発から図面書き、加工、試作の体験教育を始めました。一連のものづくりプロセスを経験することで、CAEで画面を見てよしとするのではなく、現地/現物/原則に沿った形で判断することや対策などを考えることを学ばせています。
野村 ゴーン氏が日産に来て、15年ぐらいになりますが、会社は変わったとお思いですか。
小田柿 随分変わったと思います。例えば日本企業は結構、なあなあで、多分伝わっているのだろうとお互い考えているところがあります。でも、そういうやり方は外国人は理解してくれないので、相手に分かりやすく伝える能力が身に付いてきて、論理立てて説明するようになりました。日本人は変われるというか対応力があると思います。その意味で、伝統的な日本企業ではなくなっています。世界中の方を相手にして説明して納得してもらう術が身に付いたと思います。もちろん、海外の人たちも変わってきていて、日本の文化を学んでいます。
要素技術の共有と独自技術の差異化
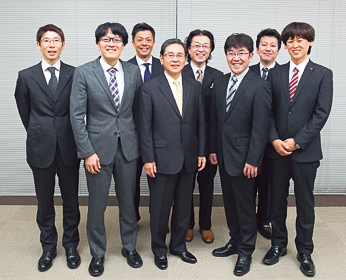
より一層のご活躍を期待しています」(木下)
木下 最後に、これからの展望について皆さまからご意見を頂きたいと思います。
嶋方 これから30年後を考えた時に、日本のメーカーが連合を組む必要がありますが、現状はせいぜい担当者レベルでのつながりだけで、企業間のつながりが非常に弱いのが実情です。ドイツは自動車設備メーカーが集まって、トップが一緒にやろうとなるので、大変なパワーを発揮します。日本のメーカーもお互いの強みを活かせる形での連携をさらに進め、各社の個性を生かしながらグローバルで競争力を発揮し続けることが必要だと感じます。
小田柿 ルノーも日産も、それぞれの部門で横のつながりが強いわけではありません。そこで、今、ベストプラクティスのシェアを結構やっていて、それはルノーと日産の工場をお互いに回るだとか、日本のプレス部門は栃木、追浜、九州にあるので、その中でも情報交換や人材交流を行っています。良いところをどんどん出して使えるところは使おうと、技術指導が必要だったら派遣するし、これで横のつながりが広がってきています。さらにそうした取り組みを強めていきたいと考えています。
安楽 オールジャパンで要素技術をつくったらコモディティー化して皆で使い、それとは別に独自技術をしっかり持って差異化を図り、強みを出せるような取り組みを進めていきたいと思います。そして30年後に作るマツダの車はこうだ、と言えるように我々が積極的に参加し、さらに日本の自動車業界を活性化していく必要があると考えています。
景浦 自動車メーカーには、規格を統一して、ベースは一緒で上物だけを違えて競争していくような動きをしてくれることを望みます。ソフトウェア会社には、CAMの自動化を進めていただき、前工程のシミュレーションによる見込みや当たり付けに時間を費やせるように、また後工程の材料が入ったらすぐ加工が始められるように、変換機レベルでNCデータが出力されるCAMソフトの開発をしていただきたい。
また、会社としては何でもできるということを売りにしていかないといけない。今までは板金だけでしたが、親会社がビューテックになってインジェクションも始めました。最終的には、板金とインジェクションの両方のアッシーを納品できるようになることを目標にしています。
上原 ダイカストや他の金型技術をミックスさせると、新しい技術が生み出せるのではないかという期待を持っています。今は日本へ金型技術を残し、進化させていく正念場にきていると思います。日本最古の通貨の和同開珎(わどうかいちん)は型で作られたわけですから、1300年以上経った今も型がなくなってないと考えれば、今後技術を進化させながら日本の金型は30年後もものづくりの肝として残っていくと思います。
野村 残していくべきものづくりの技術があることをあらためて確認できました。その上で、海外に目を向けて、グローバル体制を強化し、ハードウエア販売にとどまらず、顧客企業の品質向上を支援していきたいと考えています。
田岡 ホンダは今まで唯我独尊でやってきましたが、既に他社ででき上がっている技術や、似たような技術を自社のみでこれから開発しようと思っても、スピードについていけません。ただしホンダらしい商品の開発は今後も自らが行っていくべきだと考えます。今日は皆さんの話を聞いて、ホンダに足りないことが見えてきたように思います。
木下 自動車産業に対する新たなライバルの出現や人材育成の話など、2020年、30年に向けてキーになる言葉が出てきて、とても有意義な座談会になりました。自動車分野だけでなく、造船をはじめ、日本のものづくり産業全体にも役立つ話し合いができたと思います。本日は長い時間、ありがとうございました。