ものづくりに一貫して取り組む
モットーは「つくれないものはない会社を目指す」
![]() |
原田車両設計株式会社 代表取締役 原田 久光様 |
---|
原田車両設計様は、企画・設計・ものづくりから品質管理まで一貫して対応する企業です。モットーは「つくれないものはない会社を目指す」とし、『狭く・深く』で得意分野の業績を伸ばしています。自動車用ワイヤハーネスの設計から始まり、現在では車載組み込み開発でも実績を重ね、さらに分野を広げて航空設備機器、介護医療機器の開発にも取り組んでいます。2014年2月には「日経トップリーダー」の『本当に稼げる中小企業ランキング』で、運輸・サービス部門1位に選ばれています。同社の代表取締役 原田久光様に、創業の経緯や得意分野を生かした事業拡大の背景、今後の展開などについてお話を伺いました。
哲学を学び
エンジニアから経営者になる
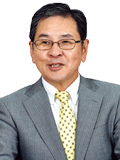
代表取締役社長
木下 篤
木下 創業の経緯についてお聞かせください。
原田 東海大学海洋学部を卒業して、水族館の就職を希望していたのですが求人募集がなく、地元の愛知県に戻って派遣として自動車部品の設計の仕事に就きました。ここでは、自分で描いた絵が自動車の部品になるので、もともと絵を描くことが好きだったこともあり、作る面白さを感じていました。
しかし、エンジニアといっても派遣社員のままではモチベーションが続きません。開発を自分でやれるようにしたいと考え、「駄目もとでやれるところまでやってみよう」と1993年に個人事業主として創業しました。その後、1998年に法人化したのですが、それから日本を代表する大手企業と次々に取引が始まりました。どういうわけか分かりませんが、運が良く、やることが自分の思うように進みました。そして、5年後の2003年には社員数が現在の規模にまで成長したのです。
木下 順風満帆、悩みなど何もないというような成長ぶりですね。
原田 実はそこから悩み始めたのです。私はもともとエンジニアなので、急に大きくなった会社の経営者として、自分に資質があるかどうか悩みました。加えて、そもそも何のために会社をやっていくのか、大義名分がなくては、大勢の社員を引っ張っていけないと考えたのです。そこで、今までの経験を基に良い会社の条件として、「1.給与、賞与が高い会社」「2.設備投資を惜しまない会社」「3.経営者が真面目に働く会社」「4.社員と経営者の気持ちがつながっている会社」の4つを考えました。
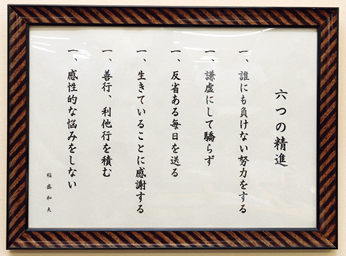
ところが、設立7年目の2005年、年間売上額よりも昇給額が上回ってしまい、このままでは経営が成り立たなくなってしまうという事態に陥ってしまいました。創業以来、良い会社をつくろうと苦楽を共にしてきた仲間には本当に申し訳なかったのですが、コンサルタントにお願いして、賃金体系を見直し、賞与額も変更しました。
木下 思い切った決断をされたわけですね。
原田 経営について何も分からなかった自分が行き着いた自業自得の結果でした。それで落ち込んでいた2005年のある日、出張先の博多駅のキヨスクでたまたま『稲盛和夫の哲学』を買い、一読して大変感動しました。そして、稲盛氏が塾長を務める企業家のための経営塾「盛和塾」に入会し、アメーバ経営を実践、2008年のリーマンショックも切り抜けることができました。その稲盛氏の「六つの精進」は、社長室に飾っています。
得意分野を広げる転機は3Dプリンターの導入
木下 2007年に樹脂を材料とする3Dプリンター「EOSINT P 385」をご導入いただきましたが、導入の背景をお聞かせください。
原田 設計だけを受けていると本当に適切な設計かどうか分からなくなるため、社内で部品まで製作したいと提案がありました。また、その当時から自動車部品の分野では3Dプリンターを活用して、型を使わないものづくりが推進されてきました。取引先のお客さまからも、3Dプリンターによる製作のオーダーが来るため、その都度パートナー企業に製作をお願いしていたのです。このような背景から、16年ほど前にものづくり部門を立ち上げて、社内で設計した部品を製作しています。そうして、3Dプリンターのニーズが高まってきた2007年5月にNDESから「EOSINT P 385」を導入したのです。
木下 翌2008年秋にリーマンショックが起こります。自動車業界も大変だったのではないでしょうか。
原田 自動車部品メーカー様からの3Dプリンターによる造形のオーダーも一時ストップという状況になりました。3Dプリンターへの投資額は大きかったので、長引いたらどうしようかと正直心配になりました。けれども逆に時間ができたので、頭を切り替えて3Dプリンターを使って何かやってみようと考えました。その中で、知り合ったデザイナーの方と、灯籠が回転すると花弁を模した歯車も動く「カラクリトウロウ」を作りました。これはテレビ番組に取り上げられ話題になりました。また、大学・医療関係者が参加するイベントで、名古屋大学や名古屋市立大学の先生方と知り合いになり、そこで先生方から「超精密な内臓を作ってほしいが、できますか」と言われました。そこで「3Dプリンターがあるので、CTスキャンデータを取り込めば作れます」と答え、連携が始まりました。そうした経験を積む中で、3Dプリンターを使えば要件が違うだけで何でも開発できることが分かり、視野が大きく広がりました。リーマンショックが、車から別の分野へと業態をチェンジさせる良いきっかけになったのです。今では車一本足打法の事業から抜け出すことができました。
木下 そうすると、今は複数の足を持ってバランスの取れた事業展開になっているのでしょうか。
原田 まだ多くの足を持っているわけではありませんが、航空、日用品など非自動車分野に広がっています。いずれもお客さまから「こういうものを作れませんか」と依頼があったものです。中でも、航空機のコックピットを再現した地上訓練装置は、お客さまから大変高い評価を受け、それがきっかけになって航空機そのものをやってみようとJIS Q 9100(航空宇宙)認証も取得しました。
木下 航空分野もそうですが、医療分野はハードルが高く、難しいでしょうね。
原田 医療分野は大学との交流がきっかけで、肺の奥に薬を直接届けるデバイスを開発しました。例えば、インフルエンザ治療薬のタミフルは通常粉薬で、飲んだときに9割以上が喉や気管支に張り付いてしまいます。それを直接肺の奥に送ることができれば、薬は少なくて済みますし、薬の量も調整できます。
2016年4月、日本薬学会のイベントでブースを出して展示すると、製薬会社や大学の先生たちが「原田車両設計」の社名を見て自動車関連の企業が何をするのかと不思議がっていました。事業内容と社名がだいぶ異なってきているので、社名変更も考える時期に来ていると感じています。
航空関連やパーソナルモビリティーなど
幅広く開発
木下 3Dプリンターの導入が大きな転機になったことがよく分かりました。私たちもそのお役に立つことができ、大変うれしく思います。
原田 もし3Dプリンターがなければ、ここまでさまざまな分野の人とつながり、その分野の事業を成長させることはできなかったと思います。
木下 現在の主な事業を教えていただけますか。
原田 主な事業は、「つくれないものはない会社を目指す」をモットーにしていて、自動車、ものづくり、介護医療、航空、制御の5つに分けることができます。
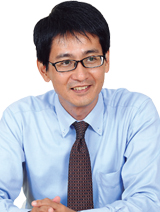
製造部 部長
新垣 龍太郎 様
新垣 まず自動車では、3次元CADを使った設計技術を根幹に、ワイヤハーネス、内外装部品、シート、ドアロックなどさまざまな製品の設計および課題解決にも対応しています。
また、パーソナルモビリティー(電気自動車)はお客さまの開発に参加しています。今まで手掛けてきたものは、2005年から開発してきた1人乗りの「i-swing」、セントレアで実証実験に使用した警備用1人乗りの「i-REAL」、東京で今シェアリングサービスをしている前輪2輪で後輪1輪の1人乗りの「i-ROAD」などです。
さらに、プリウスの前モデルまで対応する100V/1500W発電可能な後付けの外部給電装置「LifePlug」も製造・販売しています。これはプリウスのガソリンが満タンであれば、一般家庭で必要な電力を5日間賄えるもので、緊急時の非常用電源として使うことができます。
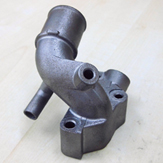
木下 16年前に立ち上げられたものづくり部門では、どのようなことをされているのでしょうか。
新垣 幅広い分野で、3Dデータを使った試作品・量産品を製作しています。注型、切削、インサート成形、金型、3Dプリンターによる粉体造形、表面加工処理、樹脂型、真空注型、植毛加工、ウレタン切削などを行っています。ものづくり部門では、樹脂を材料にする3Dプリンター「EOSINT P 385」2台、そして金属3Dプリンター「EOS M 290」1台があり、ものづくりに欠かせないツールとなっています。
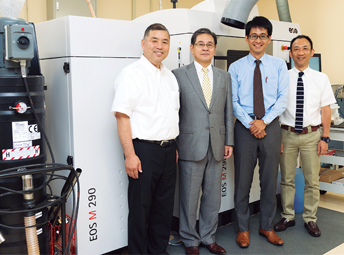
当社のように「設計・開発」と「ものづくり」の技術の両方を兼ね備えた会社は業界内でも極めて珍しく、「こんなものを作りたい」というアイデアを出発点に、試作品として形にするまでのプロセスを一貫して担っています。さらに最近では量産への体制も強化し、3次元測定機を用いて、高品質な製品を提供しています。
木下 その具体的な事例を教えていただけますか。
新垣 介護医療の分野では先ほどお話しした肺や血管の模型だけでなくフット爪ケアモデルも製作しています。これは看護師や介護士が、足病変や爪の変形に悩む高齢者に対して爪のケアを適切に行うための訓練用のモデルです。また、航空分野では2013年のコックピットの地上訓練施設を手始めに、7件の航空機地上設備を手掛けています。さらに制御分野では、車載組み込み開発の中で、ブレーキの開発に取り組んでいます。
ものづくりを大変革する
3Dプリンターに大きな期待
木下 3Dプリンターで、最適化というのはとても重要なポイントです。従来の作り方は、職人の経験や機械からこういう形でしかできないと制約されています。ところが3Dプリンターでは、今までなら考えられなかった形状ができます。そうすると、これまでとは全く違った世界で、最適化をする必要が出てきます。
原田 わくわくしますね。本当にいろいろな可能性があります。今後、3Dプリンターがさらに大型化すると、バイクのフレームも作れるのではないかと期待する声もありますので、夢は大きく広がります。
木下 設計から携わるのは大きな意味があります。昔の金型のように、工作機械を使って削り出すという話だと、「形ありき」でやってしまいます。設計ではデザイナーが「こんなものができたらいいな」と空想からスタートしますから、結果的にさまざまな形に進むことができます。
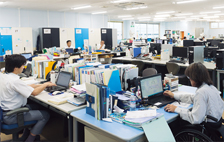
原田 私たちはもともと設計をする会社だったので、ものづくりといっても、内製化できたのは3Dプリンターを導入してからです。先ほどお話ししましたが、設計だけやものづくりだけ行っている会社はたくさんあります。けれども、両方やっている会社は少ない上に、自動車の重要な部分の設計から入らせてもらい、ものづくりを行っている会社は日本の中でもそれほどありません。そうしたことから、当社がプレゼンテーションをすると、多くの企業に興味を持ってもらえています。
目標は得意技術を生かした
人工股関節の商品化
木下 これから、3Dプリンターでどのような製品を作っていこうとお考えですか。
原田 今後、車などの部品だけではなく、自社のオリジナル商品を作り出していきたいと思います。
金属3Dプリンターは早くから興味を持っていたのですが、ようやく2015年に「EOS M 290」を導入しました。NDESから勧められたのが大きな理由ですが、導入してよかったと思います。
その金属3Dプリンターで作りたいと考えているのは人工関節です。私の父は、85歳で畑仕事に精を出していますが、両膝と両股関節に人工関節を入れています。大学の整形外科の先生の話では、日本人は70歳代後半になると、膝と股関節がだんだん変形してきて、両膝と両股関節を人工股関節にしなければならない人の比率が高いと聞きました。
木下 ほとんどの人工関節が輸入だそうですね。
原田 日本の企業で人工関節を製造しているところは少なく、輸入品が80%以上を占めています。輸入品は欧米人の骨格に合わせて、大きく作られていますから、日本人だと通常は骨を削ったりして、埋め込んでいます。そこで、日本人の骨格に合った人工関節を作ることができれば、骨を削らなくて済みます。私たちは、CTスキャンで撮ったものをCADデータで加工するのは得意ですし、それを社内で製品化していきたいと考えています。当然、医療品としての認可が必要になり、参入するための高いハードルはありますが、これができれば、一般の人と3Dプリンターが結び付く重要な製品になると考えていますので医療機関との連携を望んでいます。
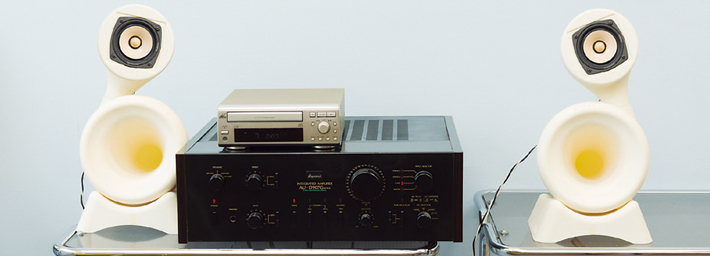
成長のカギとなるのは強固なパートナーシップ
木下 最近は中小企業でも海外進出する企業が増えていますが、海外展開は考えられていますか。
原田 ぜひ進めていきたいと考えています。不思議なことに海外展開に取り組もうと考え始めて2~3年したら、海外企業からコンタクトが来たのです。スペインの上場会社からのオファーや、最近ですとイギリスの最適化ソフトの開発会社から連絡がありました。
そのきっかけとなったのが、ナゴヤドームで行われた企業のマッチングに参加したことでした。そのときに地元テレビ局の取材を受け、それがテレビで放送されたのです。それを見た、たまたまこの近くに住んでいた最適化ソフトの開発会社で働くイギリス人からメールが来ました。その会社はイギリスの自動車メーカーと関係が深いのですが、設計ができないので、私たちと組むことで軽量化の解析ができるようになるのです。それで一緒にやろうと、この2016年6月24日、EUを離脱するかどうかの国民投票の日にイギリスに行き、今後の協業の進め方を話し合ってきたところです。
木下 最後に今後の事業の展開についてお聞かせください。
原田 今、ものづくりを担う製造部がどんどん成長していて、売り上げで見ると、エンジニアリングが6割、製造が4割くらいの比率になっています。設計の売り上げは時間単価で伸び率は限られるので、製造部門の成長に期待しています。今期の売り上げは5割で将来的には、エンジニアリングが1割、製造が9割くらいの比率を目指しています。そのために、ものづくりのネットワークを開拓していて、そのパートナー数が増える努力をしています。
営業は5人おり、週に1社を新規開拓し、「つくれないものはない」と受注を取ってきます。そして、当社と協力してくれる企業を探していると、素晴らしい能力を持ったものづくり企業と出合うことができます。そういう企業とお互いを評価して、お互いが仕事を出し合う関係になることで、パートナーシップがさらに強固になります。そういう好循環で成長していければと考えています。
木下 私どもの製品導入が、御社の事業発展への転換につながったことはとても大きな喜びです。我々も3Dプリンター分野でのさらなる技術の研鑽(けんさん)に努め、御社のご期待にしっかりと応えてまいりたいと思います。本日は貴重なお話をどうもありがとうございました。
会社プロフィール
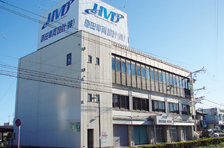
原田車両設計株式会社
URL http://www.hvd.co.jp/(外部サイトへ移動します)
【本社】 | 愛知県みよし市三好町中島24 中島ビル |
---|---|
【設立】 | 1998年6月1日(創業1993年10月1日) |
【資本金】 | 3000万円 |
【従業員数】 | 95名(2016年8月現在) |
【事業内容】 | 自動車部品、航空機、介護医療機器の設計・開発、設計請負(開発委託)、ものづくり(試作・量産・品質管理)、制御開発(ソフトウエア)、技術者派遣 |