型技術協会新会長に聞くIoTとAIで変わる設計・デザイン
![]() |
一般社団法人 型技術協会 会長 慶應義塾大学 理工学部 システムデザイン工学科 教授 工学博士 青山 英樹 様 |
---|
型技術協会は1986年に設立され、型技術に関する研究発表や講演などの開催を通して技術向上を図り、研究者および企業や学生など、型技術に関わる全ての方が参加できる協会として2016年に30周年を迎えました。NDESも法人会員に加入しています。このたび、型技術協会の第16代会長に慶應義塾大学教授の青山英樹様が 就任されました。そこで、青山様に協会運営の抱負、IoTやインダストリー4.0で大きく変革しつつある製造業における今後の金型とは、そして大学で取り組まれているCAD/CAMの研究などについて、お話をお伺いしました。
30周年を迎えた型技術協会16代目会長の抱負
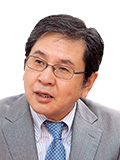
代表取締役社長
木下 篤
木下 2016年6月に型技術協会の16代目会長に就任されました。まずは、会長としての抱負をお聞かせください。
青山 会長就任にあたり、大きく三つの柱を打ち出していきたいと考えています。
一つめは、会員サービスに力を入れることです。基礎教育講座の充実やシンポジウムの開催など、会員向けのサービス向上を目指します。また、協会をさらに幅広く知っていただくための活動も企画する予定です。この企画を検討するにあたり、会員の皆さまの要望を積極的に取り入れたいと考えています。例えば、事務局長が個別に会員候補企業を訪問し、型技術協会の活動内容を広報する活動があってもいいのではと考えています。
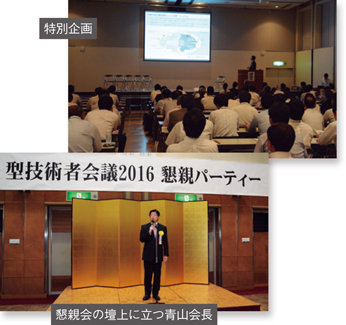
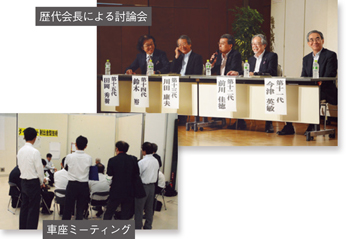
二つめは、会員数の増強です。現在900人前後で推移している会員数を1000人に増やすことを目標にしています。一概に会員数を多くすることがよいこととは限りませんが、会員数の増加により、安定した収入が得られます。それにより、会員の皆さまのサービス向上につながると考えています。
三つめは、予算の健全化です。型技術協会の予算は安定しているとは言いがたいところがあります。これまで以上の支出削減は難しい状況ですが、今まで以上に予算の収支を監視する体制に取り組みます。その一例として、業務のマニュアル化を進め効率を向上させることで、事務経費の支出を抑えます。
木下 昨年、型技術協会は設立30周年を迎えられ、お祝い申し上げます。その記念イベントを開催されたということですが、いかがだったでしょうか。
青山 2016年9月21日に型技術協会設立30周年記念大会を開催し、盛況のうちに終えることができました。会員企業の130社以上が出展した展示会場は活気にあふれ、協会委員が中心となって参加者と語り合った車座ミーティングでは、積極的な参加者の発言もあり、議論が大いに盛り上がっていました。このように有意義な記念大会を開催できて本当によかったと思いました。
30周年記念大会のイベントも無事終わりましたので、次に協会として取り組むことは、理事や各委員会の方々と一致団結して魅力のある協会をつくっていくことです。ぜひ、会員の皆さまの声を寄せていただきたいと思っています。
IoTとAIを活用する金型とは
木下 ところで、型技術協会として、型づくりを技術的に支援する側面もあると思いますが、現在の金型開発はどのような状況にあるのでしょうか。
青山 私が学生だった40年前ごろは、金型は職人技術といわれ、大学で研究している人はいませんでした。その頃、金型メーカーで2次元CAD/CAMが使われるようになり、北海道大学や東京大学の先生たちが金型の研究に取り込もうとしていました。そして、1980年代後半には3次元CADが登場しました。当時の型技術協会では、毎年のように3次元CADが使いものになるかどうかについて議論したことを思い出します。このように2次元CADや3次元CADというデジタル化技術が入ってきて、金型づくりは大きく変わりました。
それから30年近くたち、今度はIoT(Internet of Things)で金型の世界が大きく変わろうとしています。大手自動車メーカーの工場は、10年以内には完全にIoT化され、工作機械やロボットの情報は全てクラウドで管理されると予想されます。そうすると、金型を使用して部品を成形している状況の情報の収集も必要になります。そこで、金型から情報を得るためには「IoT金型」の方向へ進むことになると考えます。
木下 金型から情報を得るというのは、例えば金型を数万ショット打って損傷状態を確認しながら、交換の時期を把握するということでしょうか。
青山 そうです。あるメーカーでは産業用ロボットを数千台導入していますが、それらはIoTとAI(Artificial Intelligence:人工知能)を組み合わせることで、メンテナンスに必要な状況を把握しています。例えば、あるロボットは2週間後に故障する可能性があるという情報が上がってくるので、それを基にメンテナンス計画を立てられます。
そこで、金型もロボットと同じようにIoTとAIを活用することでメンテナンスや交換時期が把握できるようにしなければなりません。それを実現するのは金型メーカーだけでは難しいため、センサーやAIを軸とした情報処理やシステムインテグレーターなどの異分野の企業と手を組む必要があります。そうした流れに対応できる金型メーカーが次時代の中心になっていくのではないでしょうか。
木下 さまざまな分野で取り組みが進んでいるIoTですが、CAD/CAMや工作機械の分野ではどのような動きがあるのでしょうか。
青山 2016年8月、ある産業用ロボットメーカーがネットワーク機器ベンダーやシステムインテグレーター、AIベンチャーと組んで、工場向けIoTプラットフォームを構築すると発表しました。工作機械やロボットのセンサーから情報を集めて、分析したデータを基に不具合の予測や機械同士の協調などを実現するというものです。そのIoTプラットフォームは仕様をオープンにして、他社も含めたさまざまな機械につなげようとしています。もちろんIoTプラットフォームには、CAD/CAMや工程設計などのソフトウエアも含まれるでしょう。この取り組みに同調する企業やつながる機械が増えていくと、さまざまなものづくりに関するデータがそこに蓄積されます。このような動きが急ピッチで進んでいくのではないでしょうか。
IoTの活用が進む自動車業界
木下 IoTへの取り組みは、米国やドイツが先行しています。日本の製造現場はどうなのでしょうか。
青山 確かに日本の製造業におけるIoT導入の動きは米国やドイツほど進んでいませんが、その流れは一気にくると思います。その大きな理由の一つは、トレーサビリティーです。自動車の販売先は、グローバルになっています。もし、リコールが発生した場合、どこの工場でいつ作ったどの部品がどこのお客さまの所有になっているかを追跡する必要があります。このような、状況に迅速に対応するためには、工場のIoT化は必須となります。そうしないと、自動車の部品を管理しきれなくなります。
木下 トレーサビリティーのために、加工機をIoT化するということですね。
青山 そうです。つまり、今使っている加工機でIoTを活用できるかどうかが今後のポイントになります。金型製作にIoTは関係ないと考えているかもしれませんが、そうではありません。例えば、国内の工場だけであれば、何とかなるかもしれませんが、工場は世界中にあります。ある車種の小さなネジ1本でも、いつどこで製造し、どの車に装着しているかを同定する必要があります。そうでなければ、もし問題が起きたときに、同じ車種の部品を全て取り換えることになります。
木下 IoTの活用が進むと、工作機械や製造機械をはじめ生産ラインの情報を全て集めることで、製品の精度は高まります。そうすると、自動車メーカーを頂点とするサプライヤーの階層的な産業構造がなくなるような気がします。自動車メーカーは金型も内製化していくのでしょうか。
青山 金型メーカーはなくならないでしょう。自動車メーカーからすると、金型を100%内製化するような体制を組むための人員配置は厳しいと思います。
木下 そうすると、IoTは産業構造そのものを変えるものではないということですか。
青山 構造を大きく変えることはありませんが、品質の向上とリードタイムの短縮、リピータビリティー(繰り返し性)の圧倒的な向上が実現すると思います。
少なくなる金型のすり合わせ
木下 今後、金型メーカーの仕事はどのように変化していくのでしょうか。
青山 金型のすり合わせが少なくなるかもしれません。あるプレス機で使っていた金型を、そのまま別のプレス機で使おうとしてもうまくいきません。それを調整するために、すり合わせが必要で、熟練した技能工の出番になるわけです。ところが、ある大手自動車メーカーは「すり合わせの作業時間を短縮するため、世界中で全て同じプレス機にしてしまおう」としています。
また、マスター金型を日本で作り、それを基に世界中の生産拠点でマスターと同じ金型で成形してもうまくいかない場合があります。加工機もそれぞれ差があるため、違う加工機に金型を設置したとき成形面の形状が異なってくるためです。そうした誤差を吸収するために、IoTで成形状態や成形面形状のデータを収集することが重要になります。成形状態を分析し、その結果を成形面形状の修正にフィードバックできれば、修正した加工パスを出すことが可能になります。このように、経験や勘に依存した「すり合わせ」を少なくする方向に向かうのではないでしょうか。
工作機械の制御装置の特性をCAMに生かす
木下 それでは、話を変えまして青山先生の大学での研究についてお伺いします。青山先生は、デジタル・デザイン、デジタル・マニュファクチャリング、CAD/CAM分野でのデザイン・設計・生産のためのコンピューターシステムを研究されていると伺っています。まず、CAM分野の研究についてお話しいただけますか。
青山 現在のCAMは、形状の幾何情報を基本としてパスを作成していますが、そこに工作機械の制御装置の特性を反映させると、高速・高精度加工のパスを作成することができます。それを実現するための研究に取り組んでいます。
木下 パス計算時に、工作機械の制御装置の特性を情報として追加すると高速・高精度になりますか。
青山 速くもなりますし、精度も上がります。現在それができていないのは、おのおのの工作機械メーカーが制御装置のパラメーターをオープンにしないからです。
木下 そのパラメーターの情報を開示してもらうことはできますか。
青山 開示するかどうかは分かりません。自社の制御装置に合わせた加工用CAMを出しているところもありますが、エンジニアを確保しなければいけないので、全ての工作機械メーカーはそこまで取り組んでいないのが現状です。
一方で、工作機械の加工送りスピードが出ないという問題があります。この解決には、工作機械メーカーとCAD/CAMメーカーの提携が重要です。例えば、ユーザーから加工スピードが出ないというクレームに対して、制御装置の特性を生かすパスを出すと同時にNCデータを作成することで、その問題を解決できます。
木下 私たちも、お客さまから加工パスなどの計算処理にかかる時間をより短縮したいと言われています。その一つの対策として、クラウドなどのコンピューター技術を使うことで、計算処理の時間短縮は可能だと考えています。その一方で、加工スピードが出ないというのは大きな問題ですが、具体的に発生する問題について教えてください。
青山 今、問題になっているのは曲面を削るときに送り速度が上がらないということです。CAMで加工時間を1時間と予測しても、実際に加工すると2時間かかってしまうことがあります。それは、予測した半分のスピードしか出ていないということになります。
木下 では、私たちCAD/CAMメーカーと工作機械メーカーがタイアップしたら、高速・高精度加工を実現できるのでしょうか。
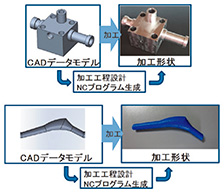
(クリックすると拡大画像が表示されます)
青山 できると思います。加工時に工具を急激に加減速させると、工具および加工機に負担がかかるので、加工精度が落ちてしまいます。逆に加工精度を上げようとゆっくり動かすと、スピードが遅くなります。その矛盾を解決するには、制御装置メーカーが、制御に関するパラメーターなど全てをオープンにすることが必要です。しかし、制御装置の性能を公表することになるため、提携した制御装置メーカーからは、秘密保持契約が求められ非常に高いハードルがあります。
木下 それでは、今後、CAMはどのような方向に進むのでしょうか。
青山 制御装置の特性をうまく引き出すCAMがあると多くのユーザー企業に喜ばれます。それから、工程設計とCAMということで、全部で14軸持っている複合加工機用の自動工程設計およびパス出しの研究開発を内閣府主導のSIP(戦略的イノベーション創造プログラム)/革新的設計生産技術プロジェクトの一つとして取り組んでいます(図1)。
木下 それは、14軸の加工機ですね。
青山 刃物が3カ所にあり、同時に3カ所削ることができます。それが、X、Y、Zの軸で動きますので、3、3、3で9軸、それぞれに回転軸が加わりプラス3軸、それに材料のチャックが二つあるので、合計で14軸です。軸が増えた分だけ、プログラムが難しくなります。
CADから作成する高精度な加工データ
木下 先ほどのお話にもありましたが、制御機器メーカーは、情報全てをオープンにすることに難色を示すでしょう。一方で、時代の流れとしてオープン化が進行していくだろうという予測もあります。
青山 完全にオープンになると、NC制御装置が要らなくなります。NC制御装置はNCデータを受け取って工作機を動かすサーボ情報を作ります。このサーボ情報を機械が動く速度に合わせてリアルタイムに出していかなければならないので、大変な負荷がかかります。ですから、スピードが出なくなるのは計算が追いつかないときです。NCデータは、座標軸上にマップされた点データのみしかないため、NC制御装置はどのような形状に削りたいのか分からないままで、サーボ情報を出しています。そこで、加工形状のCADデータを利用して加工情報を作成すれば、もっと楽にサーボ情報を出すことができると考えています。
木下 一般的には、CADデータからNCデータを作っていますよね。
青山 そうです。NC制御装置は、本当はCADデータが欲しいのですが、CADデータから処理していくと、サーボ情報が間に合いません。NC制御装置の制御パラメーターが全て開示されれば、CADでサーボ情報を作ることができます。そのとき、サーボモーターに直接入れるデータ量は膨大になるため、現在NC制御装置がミリ秒レベルで出している命令よりも大幅な高速化が必要になり、マイクロ秒レベルでのやり取りが求められます。そこで、データ通信がうまくでき、CADから直接サーボ情報を吐き出すことができれば、NC制御装置は不要になります。NC制御装置を使わずに直接CADからNCデータを出力できれば、より精度の高い加工データを出すことができます(図2)。
木下 そうなると、CAD側でデータを出すための計算に時間がかかりませんか。
青山 計算に時間がかかるという課題はあります。
感性から形状を作る「感性CAD」の研究
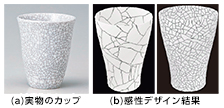
木下 他にはどのような研究をされているのですか。
青山 感性からデザインする「感性CAD」の研究に取り組んでいます。ある製品を見たときにどう思うかというデータを収集し、そのデータを基に、その人の感性に応じたデザインを作成するというものです。
木下 新しい取り組みですね。具体的にはどのようにして実現するのでしょうか。
青山 まず、製品を見たときに人がどう思うかというデータを集めます。今は、製品を見たときの感想をアンケートで集めています。これは、「意識している感性(顕在感性)」です。今後は「意識しない感性(潜在感性)」にも取り組む予定で、脳波を活用したデータ収集も考えています。集めたデータを基に、こういう感性の人にはこのデザインが好まれる、ということをAIで分析します。
このような感性データをたくさん取得すると、平均的な答えが出てきます。しかし、平均的では面白くないので、個人の好みに最適化されたデザインが求められるようにします。そのため、今度は、逆にデザインを入れると感性が出るというAIを使います。そして、その人が形状に対してどのように感じたかを自分で把握しながら、感覚と違っているときにはディスプレー上で数値を変えることで、最終的に最適化された形になるのです(図3)。
木下 面白そうな研究です。人の好みをデザインに反映させるということですね。
青山 これを、デライト(喜び)デザインというのです。例えばiPhoneとアンドロイド・スマートフォンを比べると、操作したときになんとなく違いがあるように感じられませんか。私は違いがあると感じています。はっきり言えないのですが、ボタンをクリックするときiPhoneの方がストレスを感じることが少ないのです。それがデライトです。その上で、先ほど人がデザインを自分で変えていくといいましたが、少しだけ変えるのは感性系のデライトではありません。今、その先を目指した研究をしています。
木下 では、その研究のポイントを教えてください。
青山 デザインなので、自然な印象が持てるようにすることがポイントで、そのためにノイズを入れていきます。ノイズがないものは、自然な感じを持つことができません。例えば、木目のデザインをするときにはコンピューターの中で、木を育てていきます。そのまま年輪を重ねていくだけでは、まん丸の木ができてしまいます。そうなるのはノイズが何もないからです。気象庁のサイトで生育場所と生育期間を調べると、その場所とその時期の毎月の降水量と温度が分かります。その条件を与えて木を育てていくとノイズが入り、そのときの気象条件に合った自然に近い木になります。
木下 こうしたデライトデザインが現実になると、企業が学生を採用するときに問題が起きないでしょうか。昔は早稲田大学や東京大学などに、CAD/CAMを研究している先生たちが数式処理や幾何処理の研究を学会で発表していました。ですから、学生も基礎数学的な領域に入る必要があったのですが、今はどうでしょう。ファジーなどのテーマで研究している学生は、数式などCAD/CAMの基本を理解した上でやっているのでしょうか。
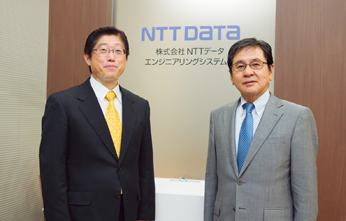
青山 ファジーなものであっても、それを活用する前提において数式を使っています。ですから、学生たちはCAD/CAMの基礎の上で研究しているので心配はいりません。昔、学会で議論していたものは、今では彼らの常識になっていると思います。
木下 若い学生さんたちが基礎的な理論を基にして、さらに新たな領域に挑戦されているのですね。安心しました。
さて、30周年を迎えられた型技術協会は、これからも魅力ある協会として金型業界の活性化を担われることと思います。私たちのお客さまも会員としてたくさん参加していらっしゃいますので、これからもお役に立てますよう、私たちも精いっぱい努めてまいります。
本日は、貴重なお話をどうもありがとうございました。
型技術協会のプロフィール
一般社団法人型技術協会
URL http://www.jsdmt.jp/(外部サイトへ移動します)
所在地 | 〒231-0011 神奈川県横浜市中区太田町6-79 アブソルート横濱馬車道ビル201号室 |
---|---|
設立 | 1986年6月 |
会長 | 青山 英樹(慶應義塾大学) |
副会長 | 高谷 裕浩(大阪大学) 花井 幹雄(トヨタ自動車株式会社) 廣瀨 淳(日産自動車株式会社) |