AMトランスフォーメーション(意識改革)が必要である
― EOSジャパン設立でNDESと共にお客さまサポートをさらに手厚く ―
![]() |
EOS Electro Optical Systems Japan株式会社 Regional Manager 橋爪 康晃 様 |
---|
欧米では、ハイエンド3Dプリンターを活用したアディティブ・マニュファクチャリング(以下、AM)による製品製造が一般化してきています。一方で、世界的に見た日本のAM導入は遅れているといえます。そういう現状の中、NDESが日本の代理店を務めるEOS GmbH(本社ドイツ・ミュンヘン、Dr.Adrian Keppler CEO、以下EOS)様が、日本国内の事業強化のために日本法人であるEOS Electro Optical Systems Japan株式会社(以下、EOSジャパン)様を設立しました。金属および樹脂用のインダストリアル3Dプリンティング分野において世界をリードする技術サプライヤーであるEOS様とNDESの今後、さらに日本のAMの未来に関して、EOSジャパン Regional Managerの橋爪康晃様にお話を伺いました。
長年の強固な関係をさらに加速する
EOSジャパン様の門出
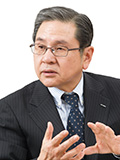
代表取締役社長
木下 篤
木下 NDESはEOS様と1993年に正式契約を交わし、以来25年にわたって同社製品の国内販売、保守メンテナンス、導入支援、技術サポートを担当してきました。昨秋、日本法人を発足されて、さらなる日本市場への協業体制が整いました。今年は、日本のAMにとってエポックメイキングな年になると期待されますが、この節目に、EOSジャパン様の取り組みとこれからの製造業におけるAM導入への期待についてお話を伺いたいと思います。はじめに、EOS様とNDESの関係を振り返っていただけますか。
橋爪 EOSの設立が1989年で、NDESには設立当初からご協力いただき、1997年からは日本の総代理店を担ってきていただいていました。これまでEOSは、全世界で3,000台以上の3Dプリンターを納入してきましたが、そのうち約160台が日本市場での販売で、すべてをNDESに販売していただいています。現在、世界12カ国の拠点に67の代理店があり、その中でもNDESは、販売だけでなく導入支援、開発、保守メンテナンスまでを全方位的に担当できる、EOS全体としても数少ない大切なパートナーです。
木下 今回、EOSジャパン様を設立されたのは、どのような背景があったのでしょうか。
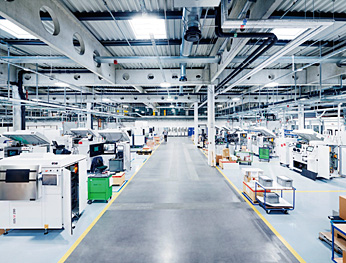
橋爪 日本はNDESのおかげで事業が進み、支社も不要と考えてきましたが、今後のグローバル化と日本市場の急成長を見越し、NDESのバックアップ体制を整えるためにEOSジャパンを設立しました。NDESには引き続き日本市場のEOSの代表として、今までと変わりない活動を期待しています。
木下 具体的には、どのような活動を考えているのでしょうか。
橋爪 EOSの製品は、現在、金属系と樹脂系の2つがあり、金属系の世界シェアにおいてはトップです。世界的な利用の割合としては金属対樹脂が4:6で、次第に5:5に近づいています。日本の場合は金属系の製品の方が先行していますが、今後は樹脂系の利用拡大も期待されます。これまで、航空、宇宙などを中心に金属系分野を得意としてきたNDESには引き続き金属系に注力をしていただくため、新たに樹脂系のニーズが発生した場合は、EOSジャパンがサポートするなどの協力体制を構築していきたいと考えています。
日本のキーアカウントへの
アプローチも協力体制
木下 お客さまへの対応はどのように考えているのでしょうか。
橋爪 お客さまの窓口は変わらず、NDESに担当していただきます。ただ、日本の「キーアカウント」である自動車、航空、宇宙、重機、防衛などの主要産業のお客さまの場合、世界中の複数拠点向けの同時購入や、購入元は日本でも海外拠点へ設置するなどのケースも発生します。このような場合は、NDES単体では対応しきれない可能性があるため、NDESと合意の上でEOSジャパンもアプローチをしていきたいと思います。
クライアントの事業規模やプロジェクトごとの事情に合わせた協力体制が、お客さまへの幅広いサポートにつながるのではないでしょうか。
木下 お互いにAMのエキスパートとして情報共有しながら、お客さまのAM導入に尽力していきたいと考えていますが、EOSジャパン設立によるお客さまのメリットはどのようなこととなるでしょうか。
橋爪 AMのアプリケーション開発に関しては、世界的にみてもNDESは先行していますので、そのノウハウはEOSにとってもプラスです。一方で、EOSには世界中のAM導入に関する最先端の実績が集まってきますので、NDESとEOSがそれぞれの強みを補い合えることは大変大きな力になると考えています。そうすることにより、これまでNDESが蓄積した日本市場における経験、知見を生かしながら、EOSジャパンがもたらす各国の先行実績の情報を加味して対応ができるため、日本企業のAM導入の失敗をなくすことができると思います。
木下 AMに関連する一連のサポートが整ったということですね。
橋爪 3Dプリンターを売るだけでなく、お客さまと常にノウハウを共有していきたいというスタンスです。EOSは、3Dプリンターのメーカーとしてだけでなく、アプリケーション、材料、プロセス、ソフトウエア、保守等々、AMを含む製造プロセスのすべてを提供できる総合的なソリューションプロバイダーになる必要があると考えています。
世界的な広がりを見せる
AMの適用範囲
木下 3Dプリンターの適用分野は、この10年ほどで大きな変化を見せてきました。切削加工や塑性変形だけだった製造現場に変革をもたらし、加工のバリエーションを増やしていますが、EOS様から見て、世界的なAMの現状はどのようになっているでしょうか。
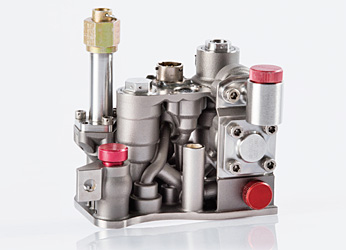
Source: Airbus, Liebherr Aerospace
橋爪 3Dプリンターが出はじめた頃は、試作品向けのイメージが強く、その後も簡単な形状の部品などに使われる程度でした。それが今や、航空機(図1)、F1(Formula One)、ロケット、歯科インプラントなど、ハードな使用環境にも耐えられる重要な部品を作る工法として、製造工程の一翼を担う存在になっており、多くの業種で生産技術の一部になっています。
これまでの製造工程への導入経緯を見ると、簡単な形状の部品や耐久性が求められない部品などでテスト生産を行うフェーズから入り、少しずつ適用範囲を広げていき、その後、最もAMが能力を発揮できる部分を見つけて最適化することで、製造工程に組み込まれていくという流れを見せています。
木下 今までの認識では、3Dプリンターによる製品生産は、一品一様、あるいは少量生産向けで、大量生産は金型を作るものという認識が強かったと思います。その現状も変わりつつあるということでしょうか。
橋爪 変わるというより、3Dプリンターの適用範囲が広がりを見せていると考えています。
ひとつの事例として、世界的な自動車メーカーが、旧タイプの車のスペア部品を3Dプリンターによるオンデマンドで供給するサービスを開始しました。設計図面があればそこから造形できますし、もし残っていなくてもリバースエンジニアリングを用いて古い部品から3Dデータを作成し、3Dプリンターで再生することができます。これは、部品そのものをコピーするようなもので、小ロット生産の極みといえますが、今までの製品生産の概念にない発想といえます。
もうひとつは、3Dプリンターで大量生産を行っている事例です。小型のデバイスを複数並べ、それをまた複数の列、層に並べた設計を行うことにより、2,400個のデバイスを一度の造形で生産しているメーカーがあります。
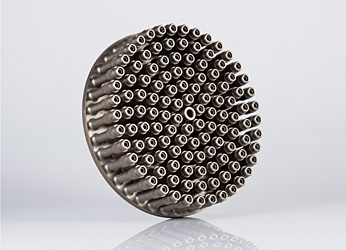
Source: Airbus Defence and Space /Airbus Safran Launchers
木下 これまでの大量生産とは異なりますが、今までの生産方法より生産メリットがあったということですね。
橋爪 もちろん、そうです。ほかにも検討段階の事例ではありますが、トラックの大型エンジンを改良している事例では、どの部品を3Dプリンターで作ればメリットがあるのかを見極めることにより、強度を保ったままでより軽量な形状の部品に変更する作業を行いました。結果として、強度を保ったままエンジン1台で200部品の削減と120キロの軽量化を実現しています。また、ロケット部品の事例では、それまで248の部品を組み合わせて製作していた製品を、AMにより1つの造形物で制作するにすることで、部品点数の削減と軽量化、50%のコスト削減につながった事例(図2)もあります。
このように、これまでの製造工程では製作できなかった形状も可能になるため、新たな設計思想を取り入れることができれば、大幅な性能の向上やコスト削減を実現することができます。また、これを既存の製造工程に組み込めば生産メリットは爆発的に大きくなると考えます。
AMの導入を成功させる道しるべ
EOSのADDITIVE MINDS
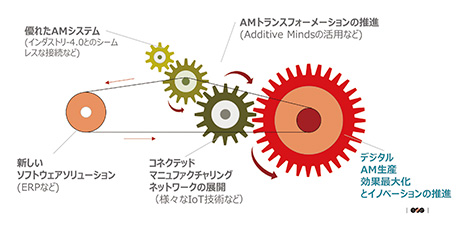
木下 ご紹介いただいた事例のようにAMを製品の製造に適用させ、しかも生産メリットを出すというのは簡単なことではないと思いますが、いかがでしょうか。
橋爪 これまでEOSでは、「AMテクノロジー(技術)を活用するためには、AMトランスフォーメーション(意識改革)が必要である」との理念のもと、"AM活用の準備"から"本格的なAM生産"に至るすべての局面でサポートを行う、「ADDITIVE MINDS」というコンサルティング支援を行ってきました(図3)。わずか数年で、世界25カ国で250のプロジェクトに適用されてきた経験をもとに、日本でもAMが定着するように全面的な支援を行っていきます。
木下 そのADDITIVE MINDSの内容をお聞かせください。
橋爪 ADDITIVE MINDSは、「コンサルティング」、「カスタマーアカデミー」、「イノベーションセンター」の3つのサービスで構成されています。中でもコンサルティングは、お客さまにAMの概念と具体的な製品への適用ノウハウを知っていただき、個々の製造環境やニーズに合わせたプログラムを作成して、3Dプリンターを活用するためのご協力をするというサービスとなります。
木下 具体的にはどのようなことをされるのでしょうか。
橋爪 AMを導入するためのプロセス構築サイクル(図4)に、「準備の完了」、「アプリケーション開発」、「生産の立ち上げ」、「認証の取得・生産の拡大」の4つのフェーズがあります。例えば、「準備の完了」の一つである「パーツの選定」は、どの部品やどの部署がAM導入に向いているのかを検証するフェーズです。一つの部品の製造工程を変更するだけでも、設計などの前工程から研磨などの後処理まで、多方面への影響が出ますので、経営層をはじめ、さまざまな担当者からの理解が必要ですし、本当にその部品をAMで製作するメリットを見いだす必要があります。このようにAMを導入するための全方位的なサービスを全世界の成功事例をもとに、NDESと協力をしてお客さまに提供していきたいと考えています。
AM活用には欠かせない
デジタルマニュファクチャリング
木下 AMの活用のメリットは、今までの製造工程では作れない形状や材質に対応し、これまでにない付加価値を付けるものと考えており、今の生産システムに取って代わるものではないと思いますが、どのようなすみ分けが考えられますか。
橋爪 従来の金型による製造工程のうち、一部の部品を3Dプリンターに置き換えるといった、ラインの一部を代替するセルという考え方が一般化しています。ただやみくもにAMを導入するのではなく、どのような利点があり、何を低減できて、新たな価値は何なのかを見定める必要があります。
また、高付加価値の製品をニーズに合わせて低価格で提供するマス・タカスタマイゼーションを実現するには、デジタルデータを活用した柔軟なシステムが必要です。そういう生産環境には、AM導入が最適といえるでしょう。
木下 それは、Industry4.0へも結び付くのでしょうか。
橋爪 ドイツ発のIndustry4.0の考え方では、製造工程全体をデジタル化することで効率化を実現する、デジタルマニュファクチャリングが推進されています。基幹システムから製造現場までがダイレクトに結ばれる環境です。セキュリティーなどの課題はあるものの、実現すれば新たな産業革命になることは間違いありません。EOSでも製品製造のルールや規約にIndustry4.0の考え方を取り入れていますが、3Dプリンターはデジタルマニュファクチャリングの中心になると考えています。
木下 マシンがつながる、工場がつながる環境ですね。M2MやIoT、さらに品質管理まで包括した製造の仕組みとして、デジタルデータでのつながりを求められる時代が来ているということでしょうか。
橋爪 世界的には実現しつつありますし、日本でも、そういう環境が求められると考えています。すでに給与や人事などの事務業務やサプライチェーンなどをアウトソーシングするBPOは常態化していて、それが製造現場まで来るのではないかと考えています。日本の大手企業はグローバルネットワークを構築済みで、すでにデータ共有の仕組みはあるのですから、ルール作りや活用法を考えて実践する時期に来ていると思います。
大企業と中小企業とのつながりと
Industry4.0の可能性
木下 大企業と中堅・中小企業とのつながり方としてのIndustry4.0は重要だと考えますが、それを、日本の企業文化にどう取り入れていくかが今後のテーマになると思います。そういう意味で、海外の中小企業の情況は如何でしょうか。
橋爪 欧米の中小企業は、すでにAMの導入と活用に積極的に取り組んでいます。日本の大手企業でも、AMを活用できるサプライヤーを探して海外の企業に外注するケースがあるようです。AMを本格的に活用している企業が日本には少ないため、海外に仕事が流れているという現状です。見方を変えると、海外の下請け中小企業が、場所を変えずに日本に進出しはじめているということでもあります。デジタルマニュファクチャリングではそれも可能で、そういう危機感を抱いている日本の大手企業も少なくないようです。
木下 日本の製造現場は擦り合わせが得意です。意識あわせが当たり前で、それで高品質を維持してきましたが、これまで情報としては残ってきませんでした。日本ならではのノウハウが見える化できれば、大きな差別化にもなると思います。その可能性が、AMやIndustry4.0にはあるのではないでしょうか。
橋爪 日本の中小の製造業にとってAMは非常に親和性が高いですし、AMの導入が広がれば中小企業のIndustry4.0になると思います。AM技術を活用することでイノベーションが起きますが、すでに日本の現状はその一歩手前まで来ています。例えば研磨は日本の中小企業の得意分野で、AMでも後工程の仕上げに欠かせない技術です。3Dプリンターだけでなくその周辺の関連技術も含めると、日本の中小企業には大きな飛躍のチャンスがたくさんあります。
木下 AMの導入により日本でもIndustry4.0が起こるということですね。
橋爪 世界的な動向を参照すると、2020年くらいには日本でも急激な変革があり得ると思います。EOSでは、今後5年で自動車産業向けの樹脂系3Dプリンターを1,500台以上販売する予定です。これまで、何か1つの部品が3Dプリンターで製造できる事例が生まれると、その事例をもとに企業がこぞって導入を進めてきました。最初の成功事例が重要で、日本のキーアカウントである大手メーカーが3Dプリンターを導入すれば、他の関連企業も必要となります。その時に、失敗せずにスムーズに導入できる環境を提供していきたいと思っています。
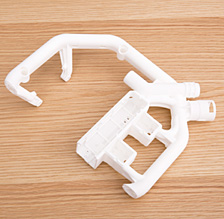
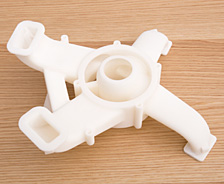
お客さまとのさらなる
関係強化を目指して
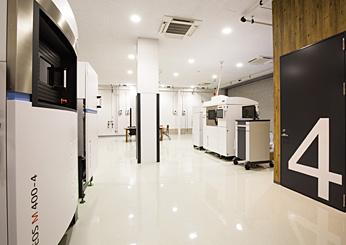
木下 NDESでは、大阪にあるAMデザインラボを中心に、AMの研究開発、各種サポートやセミナー開催等を続けてきました。EOSジャパン様が新横浜にテクニカルセンターを開設されましたので、関東地方のお客さまを招待しやすくなります。
橋爪 両社の拠点が大阪と新横浜の二カ所にあることで、よりお客さまへの密接なサポートにつながればと思いますし、NDESには新横浜のテクニカルセンターを新たな拠点として使用していただければと思います。
木下 ありがとうございます。この2拠点は、今後、お客さまとのコミュニケーションの場になると思うのですが、他に取り組みたいと考えていることはありますか。
橋爪 今まで、EOS本社やEOSアジアパシフィック本部が対応してきたことをEOSジャパンで対応できるようになるため、EOSの技術者を日本に呼びやすくなると考えており、サポートの充実を図れればと思っています。また、既存のお客さまとの関係強化にも取り組みたいと考えており、例えば、国内のユーザー会を定期開催して、お客さまのノウハウや事例を共有したり、最新情報を発信する場を作ったりしたいと考えています。
木下 ユーザー会については、ぜひ、開催したいですね。
それでは、最後にEOSジャパン様の今後の抱負と目標を聞かせてください。
橋爪 EOSジャパンは、まだ生まれたばかりです。日本でAMを成功させるためには、お客さまに認めてもらえるような実力を身に付けていくことが必要と考えます。何がAMに向いているのか、どうすればメリットがあるのか、お客さまのことを第一に考えて、NDESと攻めの姿勢でタッグを組んでいけたらと思っています。
また、今後の目標としては、2020年には現在の5倍の1億ユーロ規模まで、日本の市場を拡大することを目標としています。ただそれには、NDESの協力が無ければ決して達成することはできないと考えておりますし、NDESをサポートするためにEOSジャパンを設立したと考えていますので、ご協力をお願いします。
木下 私どもは、3Dプリンターは日本のものづくりを阻害し駆逐する存在ではなく、人手不足などの弱点を補い競争力を増すツールであるという確信のもと、長年にわたって事業を推進してきました。今回のお話からも、我が意を得たりと心強く感じております。国内のAM浸透のためにも、今後ともよろしくお願いします。本日はありがとうございました。
会社プロフィール
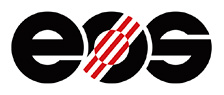
EOS Electro Optical Systems Japan株式会社
URL www.eos.info(外部サイトへ移動します)
本社 | 神奈川県横浜市港北区新横浜3-22-11 |
---|---|
設立 | 2017年8月28日 |
事業内容 | AMに係る各種機器、装置並びにそれに関する各種原材料、部品、技術サービスの販売及びマーケティング |