株式会社松岡鐵工所 取締役副社長 高野 輝雄 様
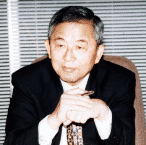
本日の座談会の司会を務めさせていただきます高野でございます。
当社は、ダイキャストの金型メーカですが、20%ぐらいはプラスチック型も製作しています。
私自身は、小さい金型、プレスの打ち抜きからプラスチック、精密金型など、いろいろな分野の金型に三十数年携わってきまして、今はダイキャストであると同時にGRADEユーザの一員でもあります。
この座談会で、皆様方が考えておられることをぜひお聞かせ願えればと思います。
株式会社メルコ 金型事業部 技術課 課長 堀川 喜久雄 様
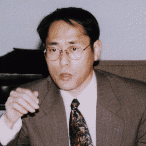
当社は、静岡県天竜川の東側の豊岡村にあり、業務内容は、自動車、オートバイの内外装部品を中心にプラスチック、ダイキャスト金型の製造販売です。比率はプラスチック型85%、ダイキャスト型15%です。
従業員は75名、CAD/CAMシステムはGRADEを中心に自社開発含め25台です。
私は金型製造という職業についてちょうど20年になります。所属する技術課は型の生産準備を担当しています。客先との打ち合せから始まり、型設計、モデリング、NC情報作成、トライ立ち会い、設計変更、修正フォローまで一人で担当できるエンジニアの育成を目標に進めています。
株式会社米谷製作所 システム課 米谷 強 様
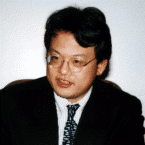
当社は、新潟県の柏崎市にあり、自動車エンジン部品を主とした鋳鉄、アルミ鋳造金型をメインに製造しています。社員は、今年の4月で110名になります。
CAD/CAMシステムは、大部分がGRADEで、その他のシステムもあわせて30台あります。
自動車部品は、シリンダーブロックのアルミ化、ハイブリッドシステム、EV(電気自動車)などによって、アルミ部品の比率が増えています。それに伴い、ダイキャストのトライマシン(2500t)を導入し、ダイキャストの金型にも注力しています。
私自身は、金型に携わって4年足らずですので、今回は、先輩諸氏の貴重なお話をお伺いできればと思っております。
九州池上金型株式会社 製造部 技術副長 白石 龍二 様
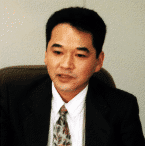
当社は、福岡市のとなり糸島郡にあります。プラスチック型専業として営業しています。従業員は58名、CAD/CAMシステムはすべてGRADEで、GRADE DASH/DRAW,GRADE/CUBE,GRADE/NC,ICEM SURF合計14台、DNCもHZSにお願いしており、G-LANに接続している工作機が8台、ワイヤーカットが2台で合計10台、実績収集用の端末が6台ございます。3年前から実績収集を始めました。
当社の技術部門は、型設計・モデリング・パス出しの3つに分かれますが、モデリング・パス出しがCAM部隊になります。私は約3年設計を経験し、現在はCAM部隊で7年目になります。最近はCAM以外にも台湾への金型手配、成形立合いなども担当しています。
お客様は家電が多かったのですが、最近は自動車関係が多く、50%ぐらいになります。
金型に何が求められているのか
高野 最初にお客様が皆様の金型に何を求めているのかということをお話いただきたいと思います。
堀川 今、我々に要求されているのは、短納期、高品質です。
以前に比べ、型製作期間は2/3、精度は寸法や外観品質だけでなく、成形性まで要求の幅が広がっています。
ただ指示されたように型を製作するのでなく、製品機能を理解したうえでの型寸法の作り込み、冷却の配置、ゲート方案、型強度など、成形性を踏まえたうえでの型構想と、金型屋に期待する範囲が広くなり、我々の知識、技術も広げないと対応できなくなっています。
米谷 お客様からは品質、納期、コストの順で要求されています。
バリや鋳造欠陥の少ない金型、粗材が一発で取れる金型など、品質が第一条件だと思います。
納期は、シリンダーヘッドで以前は6ヶ月、今は4ヶ月ですね。他の部品も同じ比率で納期は短縮されています。今は、コンカレントで、設計が十分煮詰まっていない段階で受注し、前倒しで生産を始めます。ある程度進んだところで、設計変更が入ると、最初決めた納期から延びることはあります。
コストに関しては、我々も利益を出さないと生きていけませんので、ある一線は死守しています。お客様側でも一発で良品の取れる金型ですと、トータルで見てコストが安くできます。
高野 一発合格はいつ頃からですか。
米谷 それは、私が入る前からやっていますが、鋳造の社内的なトライアルをして、条件を見ながら金型の品質を上げる体制をとっています。
白石 私どもは、家電・自動車・住宅機器などいろいろなものをしていますが、お客様ごとに要求されるものが違っています。
今は、納期が第一だと思います。図面が出てこないのに、納期は変わらないのが一番きついですね。以前は、小さな金型でも最低1.5ヶ月ぐらい納期がありましたが、今は1ヶ月以内、大きいもので3ヶ月のものは2.5ヶ月、2ヶ月のものは1.5ヶ月ですね。
品質とコストに関しましては、相反するところがありますが、コストも下げて品質もいいものをという要求があります。開発期間がかなり短くなっているのは感じます。それに対してお客様の設計者が足りないという現状もわかります。できるだけ、品質を上げるために、お客様の技術の方と十分打ち合わせをして、ある程度の設計変更、形状変更の要望を前もって出して、仕事を進められればいいのですが、出てきた図面ですぐ金型を作ることが多く、対応できていない状態です。
あるお客様では、週に一度、質のいい金型作りを考慮した設計の技術指導をしてほしいという要望もあります。
お客様との協力関係
高野 耐久消費財の陳腐化のスピードがものすごく速いわけですから、新製品による創業者利益をどのようにして確保するかという戦いの世の中です。皆様のお話を聞いていると、品質は当たり前で、納期、納期といわれる時代ですが、そのためにお客様とどのような協力関係を作ろうとされていますか。
堀川 そうですね。作り易い金型(シンプルな金型)=トラブルの少ない金型につながると考えれば、仮製品図ができた時点で、お客様と必要な形状、機能の作り込みの打ち合せを行い、白石さんのお話にあったように、金型の作りにくいところや形状変更の必要な部分をVA(Value Analysis) / VE(Value Engineering)提案し、図面に織り込んでいただく。そういうことに対応できる金型メーカに仕事が出てくるという感じを受けますね。
米谷 そうですね。特にCAD/CAM側では、3次元ソリッドデータをマスターに金型を作ってほしいという要求もあります。実際にソリッドデータをもらって金型を作りましたが、一番問題になったのが、設計変更に追従できないということですね。
ちょっとしたことなら、お客様も図面で指示をしたほうが早いですし、我々金型メーカも基本的には図面でできます。もともとソリッドデータでの設計はお客様のほうでされますから、設計変更のフィードバックが追従できなくなります。結局最後は、図面が正になりますね。どういう出し方をすれば、お客様と金型屋が助かるかということをいろいろ打ち合わせしている段階です。
お客様のほうも技術者不足のうえ、3次元のモデリングはかなりスキルがいる作業です。金型の設計、図面から形状を読む力、加工のノウハウ、熟練度を要求されますから、お客様できちんとそこまでデータを作るのは難しく、金型屋の我々のほうでやりましょうかという提案をする場合もあります。
白石 堀川さんがお話されたこと以外にも、私どもは量産型を製作しており、自動車関係では試作型を必ず作ります。試作型を一緒に作って、そのデータを量産型に活かして、納期が短縮できないか、コストが安くならないかという要求がでています。これを実現しているのはまだ数少ないですが、試作型の受注は難しく、コスト、納期にもなかなか対応できていないのが現状です。
これからの5年
高野 金型の専業者さんがCAD/CAMを使い始めたのが、20年ぐらい前ですね。CADはCAD、CAMの世界は自動プロのようなものでした。10年ぐらいたったときに、HZSさんのような会社が、CADデータにCAMのデータをうまく合わせ始めた。CAD/CAMと称することができる状態が10年ぐらい続いてきまして、今は米谷さんのお話のように、お客様のデザイン設計のデータから金型までを流していく試みが始まり出した。これからの10年は、これを世の中が必死になってやっていく時代になると私は感じていますが。
技術者として描いておられるこれからの5年ということをお話いただきましょうか。
堀川 先ほど米谷さんが3次元データでという話しをされましたが、我々もあるお客様と10年前から図面ではなく、CADデータを正に物作りをしましょうとやってきていますが、未だに図面と3次元データがごっちゃになって出てくるというのが現状です。
きちっと煮詰まったものがなくて、最後には改訂番号がついた図面が正になる。それは何故かというと、製造側が作る情報と設計側が作る情報との間に違いがあるからです。製品として満足するものと金型屋サイドが要求するものは異質です。
伸び尺も含め、抜き勾配だとか、プラスチック型では成形性、ダイキャストでは鋳造性を考慮した条件の織り込み、そういったところが現場でのノウハウです。
5年後でも、支給される3次元データですべて処理できるというのは難しいかもしれませんね。だんだん金型屋が前にいかざるを得ないのは間違いないと思います。
プラスチック型では、意匠部品をデザイン承認というイベントをなくして、支給された面データを正に加工させてくださいとお願いしていますが、未だにデザイナーがモデルを触って承認しないとGOが貰えない状態です。せっかくのデジタル情報もデザイン承認というイベントで、手仕上げが介在して、支給面データと製品形状は違った物になっていき、図面が正のアナログの情報に変わってしまう。加工、成形、鋳造のノウハウを織り込んだデータが、お客様に戻るかというと、必ずしもそうではないと思いますが。
高野 それを持っているのが金型屋のノウハウです。
米谷 おっしゃるとおりだと思います。
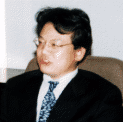
試作型の場合、改造することが目的の型ですから、最初に作った型と最後の型は違います。何をマスターにして金型を作るかということを一番注意しないといけませんし、そのようにしています。
マスターは、3次元データでも、図面でも、どこをどう直したかという書類でもいいでしょうが、ここを確かに直したということを必ず残す。金型屋も情報企業の仲間入りをしていくと思います。CAD/CAMのデータ以外に流れている情報はたくさんありますので、常に最新の情報を的確につかんで、お客様からの電話一本で即答できるような情報体制が必須だと思います。
5年とはいわず、あと2~3年後には、そのような社内システムを作っていかないと、世の中に追いつけなくなると思います。
高野 図面なりデータをいただいて、逆にどんどん提案をするという部分はスムーズにできておられますか。
米谷 図面から細かい問題が発見できるのは、モデリングがほとんど終了した段階です。中子と中子を合わせてみると肉厚がないなど、モデリングの最終段階でしかわかりません。たとえば、4ヶ月のうち、2ヶ月はモデリングに使ってそこで問題が起こっても、あと2ヶ月しかないわけですから、トッカン工事になってしまいます。これは、モデリングがいかにスピーディーにできるかということが重要になってきます。
高野 いただいたデータはスムーズに流れましたか。
米谷 お客様で抜き勾配やフィレットをきれいに付けてあるデータはそのまま流せばいいのですが、付いていない場合、フィレット、勾配などをいちいちチェックして訂正していると、最初から作ったほうが早いのではないかということもあります。いただくデータの素性でぜんぜん違いますね。
ソリッドのニーズが進まないのは、ソリッドで簡単にモデリングができないからです。簡単にモデリングできるようなシステムですと、変わってくると思います。
白石 以前は木型で倣い加工で作っておりましたが、3~4年前、GRADE/CUBEを導入し、NCデータで加工ができるようになりました。お客様の内部でもソリッドで作られていまして、解析も行われています。そのデータを金型屋さんに渡して、納期が短くならないか、開発期間が短縮できないか、ということでデータをいただいています。ただ、それでも、モデル承認はきちんと行わないとだめです。
高野 承認のためのモデルをわざわざ作るのですね。
白石 はい、ケミカルウッドで削ります。中には明らかにNGだというモデルをいただいたこともありますが、最近ではだいぶよくなったと思います。細かいフィレットまではいただけません。まず、意匠形状だけですね。キャビティー面のモデルでも外側だけですね。金型のコア側は、すべてこちらでモデリングをしますが、いただいたデータですので、修正、R付け、オフセットをするとずれたり、その辺の苦労は、当社で一からデータを作るのとは比べ物にならないくらい手間がかかります。最初からデータを作ったほうが、後々は楽ですね。
高野 今の状況では、データでいただくより図面でいただいたほうがいいということでしょうか。
白石 ただ、意匠面だけはデータを作るのもなかなか大変ですし、以前は承認に、2度3度削り直して持っていったことがありましたので、意匠面はデータがあったほうがいいですね。
ソリッドへの流れ
川下 ソリッドモデラーのメーカのキャッチフレーズは、ソリッドのモデルデータを使ってコンカレントエンジニアリングの流れにのせて金型造りがもっと効率よくなるということです。それは、おそらく上流の設計の世界のことで、金型を作るというところまで枠を広げたときに本当にそういうことができるのか、常々疑問を持っております。
高野 これからいろいろ成長して、充実していくと思いますが、皆様はどう考えていらっしゃいますか。
堀川 プラスチック型の場合、ソリッドデータでの支給はまだありません。サーフェイスの世界です。
我々のソリッドモデラーの使い方は、モデリングでは、実際、鋳造型のような2次元図面から3次元化していくところで使用していますが、レベルはまだ低く、ソリッドでメリットがでるところだけ使って、残りはサーフェイスで逃げるのが現状です。今のところ、お客様にデータを戻すわけではないので、設計変更が入ったらソリッドでなくても早くできるモデラーがあればサーフェイスで張り直せばいい。型設計においては、まだ使っていませんが、母型やベース、標準部品のようにある規格に基づきパラメトリック機能をうまく利用して、レイアウト設計あるいは流用設計に使っていきたい。これも、設計とモデリングが同時進行の型製作においては、現状のソリッドモデラーでの製品形状モデリングを待って設計していたのでは間に合わない。金型屋サイドで早くモデリングできるか、またはお客様から製品形状のソリッドデータの支給ができるか、いずれにしても、モデラーのスピードアップ、機能の充実に期待したいですね。
米谷 自動車業界に関してはI-DEASが台頭してきていますから、I-DEASの生データでくるところもあります。IGESで面におとしていただいて、フィレット、勾配付けをして、金型にするというのが現状です。高速加工で直彫りをやっていますが、今までは、電極加工用のデータとして作っていたのを、直彫りですから、モデルを反転しないといけないという問題が出てきています。ソリッドの機能でサーフェイスのオスメス反転を一括でやってくれるような機能があれば実用的と思います。
高野 ソリッドデータは、成形された部品の形ですので、それを金型展開するフィレット付け、勾配付けが、大きな課題になると思います。そうしないと、本当の意味での金型屋のCAD/CAMとはいえないと思います。
米谷 そうですね。お客様側では、実際には、フィレットを張りません。ボスとボスの底にフィレットをかけておいて、ボスが動くとフィレットとフィレットが干渉して定義できなくなる。最初からフレットを付けていないほうが製品設計としては、変更し易いということです。他のシステムでも似たり寄ったりだと思います。いくら干渉しても問題なく追従できるモデラーが出てくれば解決できると思います。
白石 私個人としてはソリッドに注目しています。
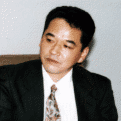
恥ずかしい話ですが、社内の不良の7~8割は設計、CAMで出している状態です。型設計中の不具合に対して、平面図は直したけれど、断面図は直していなかったなど、お客様の図面にも社内の図面にも、そのような箇所があります。
3次元設計ではそういうミスがなくなるだろうと思います。形状を作成するのに2次元の図面情報では足りないですね。3次元で設計して図面に展開するやり方が正しいと思います。材料の手配、レイアウト、型の大きさなどはソリッドのほうが時間はかかると思いますが、トータルで考えれば、3次元で設計したほうが早いのではないか。今そのなかで、金型にあうようなソリッドのシステムはまだなく、製品設計がメインのソリッドのCAD/CAMばかりではないかと思います。
高野 対金型屋向けにソフト開発をされているHZSさんのご意見はいかがですか。
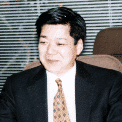
川下 GRADE/CUBEIIを使って今と同等のモデリングの効率が認められるまでやっていかなければいけないと思いますが、今年度の早い時機に目処がつくと思います。それから、2次元への展開を具体的に考えていきたいと思っています。2次元に展開するための準備も社内的には進めています。
米谷 話の腰を折るようで悪いのですが、理想は、図面はなくなる方向ではないでしょうか。
白石 図面がなくなるのは理想ですが、お客様からの図面提出の要求はありませんか。
米谷 今はありますね。図面がなくなるためには、すべてで3次元データが正にならないとだめでしょう。
高野 モデルがなくならないのと一緒で、思い切ってモデルをなくす時代までは、図面はあるでしょう。
白石 そうなっても、図面が残る必要があるような気がします。成形屋さんがわざわざCADで金型の寸法をチェックするわけではなし、図面を開いて見るわけですね。現場サイドの作業者もそうでしょう。図面はなくならない。ただ、現場の機械加工においては簡単な基準だけあればいけるというのを目指していくのでしょうね。
堀川 最終的に図面の内容が変わるということでしょう。表現の仕方が細かく書いているところを必要なところだけ満足していればいいという形になると思います。
HZS 今使われているソリッドモデラーはほとんど欧米製です。日本の金型で使われているCAMシステムの大半は日本製ですね。これは、システム的に見たら溝があり、絶対に良くならないと思います。
その溝をなくす一番いい方法は、欧米でソリッドモデラーを作っている企業と、日本のCAMをやっている人達が手を組めばいいと思うのです。そういう方向のコミュニケーションが進んでいくことがひとつの流れとして必要ではないかと思っています。
高野 私もそのことを提案したかったのです。
私の意見を申し上げますと、まず、自動車にしても家電にしても、商品を開発するところがデザイン設計でのソリッドデータを生かして、全体の物造りの効率化を図ろうというのが第一点だと思います。何のためにソリッドをやるかは、お客様と線を結ぶためだけであって、自分のところの金型作りにコスト的にあうのか、労力がかけられるのかということは、大変疑問だと思います。
もう一点は、この世界のソフト開発は、ずいぶんお金がかかると思います。2次元から始まってサーフェイスになってさらにソリッド、一社で何から何までこなすのは無理ではないでしょうか。お話のあったように、ソリッドのソフトの進んでいるところとつながりながら、下流の金型のところは任しておけという関係でやっていかないと、時間がかかりすぎ、金型メーカとしては不満足になります。そこは、HZSさんとしてお考えいただくひとつのポイントだと思います。
もう一点は、金型造りでは、製品形状部を加工して金型を作るということがメインですが、それに付随したいろいろな仕事があり、まだ技能に依存しています。
是非、金型メーカの仕事を分析していただいて、HZSのソフトが取り入れる分野もお考えいただくと、大変面白い展開になると思います。
社内展開
高野 今度は、社内展開、たとえば、外注さんとの情報のやり取りなど、皆様の自社の中で、CADデータからCAMデータ、NCデータに対する展開についてお話いただきたいと思います。
白石 今は台湾のほうへ全外作を発注しています。インターネットmailで3次元データや2次元データを送ります。向こうでモデリングした場合は、データをこちらにmailで送ってもらって、形状をチェックして作成しています。台湾の外注先にもGRADEを入れて、台湾に行ったときに形状確認をして内作するようにしています。そのとき、データを送る際にはデータができるだけ小さいほうがいいですし、同じGRADEならいいのですが、まだ台湾のほうで立ち上がっていない状態なので、インターフェイスの部分は大変重要になってきます。できるだけ、データを圧縮して必要な物だけ送るということができればいいですね。
米谷 当社は、モデリング、NCのパス出しまでは、100%内製です。外注先に関しては、足回り部品、プレート物の加工を出しており、きっちり図面を書いてアナログで送っています。せっかくCADで図面を書くのですから、外注先も巻き込んでNCデータを作成すれば、外注さんも助かるでしょうし、当社も外注さんが穴のピッチを間違えるといったこともなくなるので、お互いメリットでしょう。外注先も巻き込んだデータの一元化を進めていかないといけないと思っています。
ただ、外注さんも5~10人の規模ですから、当社と同じGRADEを入れてくださいと投資を強要するわけにもいきませんので、難しいところです。
高野 NCデータ、加工についての課題にしていらっしゃることは何かありますか。
米谷 鋳造金型のパス出しで、一番時間がかかるのは荒取りです。それは、形状の山谷が激しいためです。荒取りの最適化、一番効率のいい荒取りのやり方は何かということを今後我々も考えていかなければなりませんし、システム化をしていかなければなりません。熟練した人が効率的に荒取り加工をするのに比べ、GRADEなり他のCAMシステムで出した荒取りを見ていると、効率の悪いところがいろいろあります。変な荒取りをすると工具に負荷がかかり、マシンも痛むきらいがありますので、荒取りに関しては、有人で昼間行っています。コストを下げるためには、いかに無人化比率を上げるかということを考える必要があります。
堀川 無人化、効率を上げる取り組みとして、生産準備、工場の人のバラツキをなくすための標準化を進めています。生産準備では、パスの走らせ方の標準設定、工場では、作業者に対して、例えば荒取り加工での使用工具、回転数、送り、切削油の有無などの条件を決めて、テストをし、その加工のチャンピオンデータを作り、切削条件、工具寿命を数値で表現し納得させ、今までの経験や勘、コツの世界から脱皮し、標準に沿った仕事の仕方に変えていくようにしています。
高野 チャンピオンデータを元にしながら、加工条件の標準化をされていると思いますが、何%ぐらい標準化が進んでいますか。
堀川 プラスチック型では生産準備の加工標準が概ねできていますが問題はあります。加工のところでは、荒取りの部分だけです。ダイキャスト型については、熱処理後の加工もあり、クランクケースを中心に50%位まで標準化が進んでいます。あとは材質、製品形状が深くなったり、複雑になった時に少し変えるという程度で、パターンは決めてやっています。
CAMの自動化
高野 CAMの自動化についてはいかがですか。
米谷 工具、加工方法を決めてやれば、ある程度パス出しの自動化はできますが、それを決めるためには熟練が必要です。
高野 私は、熟練は技能だと思います。コンピュータで解決していくのは、技術です。
白石 実際に金型のワークをそのままモデリングしてこれを作りたいですね。完全にモデリングをして、それにパス計算すれば終わりかというと、そうではなくて、削るためのサーフェイスを作っているのが現状です。
高野副社長が削るのは技能とおっしゃいましたが、その部分の安定度はシステムで解決できると思っていますので、工具を選んでボタンを押すだけのシステムが早くできればいいと思います。
高野 工具も選ばせていいと思いますよ。
白石 そうですね、工具とワークの材質と。
高野 工程の負荷は工作機ごとに違い、設定していた工作機と違う工作機になることもありますから、使用する工作機の能力を含めた自動化ですね。
白石 実際の送り速度は現場で編集して加工担当者が決めています。この人は、こういう速度と回転でやるとか、昼間人が付いていてやるのと、夜かけて帰ってやるのとは違うので、CAM側で送り速度を入れようとしましたが、現場サイトから止めてくれといわれました。それで、なかなかシステム化できていないのが現状です。
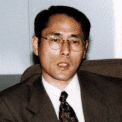
堀川 私の夢は「眠らない工場」です。でも現実にはそれを実現しようとすると「眠れない生産準備」になってしまいます。
自動化が一番遅れているのが、CAD/CAMを使っての生産準備ではないかと思います。人が端末の前にいないと仕事にならない、確かに夜間バッチで処理しても、後の結果を見て判断し、かつ編集する作業が残っています。どのシステムでも100%ではなく、チェック、編集の比率が多いシステムと少ないシステムがあります。
「眠らない工場」の実現、でも私達は眠りたいので、そこを自動化できるようにしてほしいと思います。
工場で問題になるのは、自動化の妨げとなるホルダーの干渉、工具寿命などです。工場にある工具の管理状態を把握して、パスを走らせることができれば、理想ですね。
CAD/CAM+工具干渉、条件設定、工具管理などの技術が必要になってきます。予定した機械に乗らず、別の機械に乗ったときなどの既存データの変更、最適化ができるシステムがほしいと思います。
米谷 干渉を見るだけでなく、干渉が解決する最適刃長を教えてくれるシステムがあるといいですね。
今、VERICUTを入れて検証しています。最近だいぶ早くなりましたが、帰る前にかけて朝見ます。パスの不具合を探すだけではなくて、ここはこう直したほうがいいよと自動的に判断してくれるといいですね。
高野 CAMに対して加工条件まで整えていかないと、自動出力のプログラムが出ないということですね。
米谷 CAM側に加工条件をINPUTする受け皿がありません。ある程度標準化はできても、それをどうやって表現するか、具体化するかということでしょうね。
高速加工
高野 高速加工機についてはいかがでしょうか。
効果の問題、ソフトとのバランス、この二点についてはこれから高速加工機を導入しようとお考えになっているところの検討課題ではないかと思うのです。
米谷 当社も高速加工機がありますが、形状によっては、放電のほうがいい場合もあり、使い分けています。放電加工の場合、間に電極を挟みますので、電極を測って、検査して承認を得るということができますので、ワンクッションあるだけでもミスの低減になるというメリットはあります。
堀川 熱処理材の加工は、少ない取り代で速く削るということが不可欠で、高速加工機のメリットはでています。ただ、効率を上げようとすると生産準備側がついていけない。
工場を効率良く動かすためには、データが多量に準備でき、機械の負荷に合わせてワークを選べれば一番いいのですが、今は、間に合わせるのがやっとです。
高野 それと、加工条件の蓄積がないというご苦労もあるんじゃないですか。
堀川 ありますね。どこまで加工できるか?どういう加工が一番良いのかもわかっていないので、試行錯誤しながらやっているのが現状です。一品物が多くデータの蓄積ができないのが悩みですね。
白石 もともと家電でしたので、放電が多かったのですが、浅いリブはできるだけ彫るようにしています。福岡県の金型研究会でも、高速加工機についてはいろいろ論議がなされていますが、実際に福岡県で進んでやっているところはないですね。加工担当者からすると、大きな刃物で、大きなピッチで削ったほうが早いという認識があります。高速加工はあとあとの中仕上げの段階においてはかなり有効ですが、工具がどこまでもつのかという問題と、切子の排出の問題もありまして、なかなか進んでいないのが現状です。
今、8000回転が一台ありますが、リブ彫りぐらいで、実際の加工は通常の部位でやっているのが現状ですね。
放電加工
堀川 荒取り、仕上げで放電ギャップを決めて出しています。ダイキャスト型は製品の深さで工具の最小径を決めています。熱後にすべて正寸加工、削り残した部分はマルチ放電加工です。プラスチック型では、キャビ側は荒取り後マルチ電極放電、コア側は直彫り加工後部分電極加工。小さな電極は多い型では200以上になることもあります。入れる部位によっては、荒、仕上げを作ったりギャップを変えたりと非常に苦労しています。
高野 金型を設計して製作していくときに、樹脂型ですと、収縮率の問題が出てきて、電極も作らなければいけない。では、放電前の荒取りをどうするか、その辺はどのように解決していますか。
白石 放電の現場サイドにしてみれば、できる限りNCで仕上げてくれということです。
加工データも仕上げ加工まできちんとしたデータを作らないといけませんし、電極も必要になってきますから、電極も作る。グラファイトがありますので、できれば電極だけ作って入れてくれると一番助かるのですが、なかなかそうはいかない。
電極だけでやろうとするときに、段取りが変わって、別のギャップでクリアランスを置く、電圧を上げる場合もありますので、その時にすぐ作り替えということもあります。今、冶具を3R使っていますが、データ作成は、全部センター基準で作らされているのが現状です。現場が間違えないように、分かりやすいように全部盛り込んで作ってやるのが大変ですね。
また、急遽バタバタ作らないといけない時に、汎用電極か、ワイヤーカットで切った電極か、どのグラファイト電極か、実際決めているのはCAMの担当者、個人の頭の中です。それで電極の漏れが発生します。GRADE/CUBEIIで、加工残り、仕上がっていないところが出てくるようになったら電極の漏れもなくなると思います。
これによって工程がかなり乱されているのも現状です。
電極作りの後は、電極用のモデルを作っているのですが、電極もワークと同じ方向ではなくて、傾けて加工する場合もありますし、そのときの対ワークに対する干渉チェックを実際やっていないので、電極のほうが逃げていなく、加工したら形状が消えてしまったなどがあり、そのチェックがなかなか難しいです。
VERICUTを導入しましたので、VERICUTでデータの不具合は直していこうと思っています。ただ、電極のデータのチェックはどのようにされているのか教えていただけたらと思います。
堀川 できあがった電極をチェックします。小物(ダイキャスト型)の一体電極は3次元測定機、大型(プラスチック型の承認モデル)の一体電極はオンザマシンで測定確認しています。単品電極は、正直言って難しいですね。一個一個測る、その度に何かしらの情報は出さないといけないので、現実測れていないです。
白石 米谷さんのところは、電極のデータにもVERICUTを使われていますか。
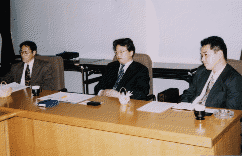
米谷 使っています。
堀川 パスの確認ですか?
白石 ええ、そうです。
堀川 全くしていません。
(GRF上の目視チェックのみ)
米谷 すばらしいですね。
堀川 電極は数も多いので割きりをしないと。
白石 今のところ当社もそうです。えい、出してしまえでやっているのです。
米谷 3次元測定は、面から出した測定データで測っても、工具の逃げしか測っていないので、当面は図面が正になるのでしょうが、図面寸法でワークの寸法をうまく、もれなく測れる方法があったらと思います。
白石 3次元測定機を入れているのですが、ワークを測定する時間がありません。電極にしても電極の測定データを提出しなければならないお客様もありますし、持っていってすぐ使うという場合もありますので、工程に乗ってこないですよね。
今、金型研究会で、オンザマシン計測というようなことを研究されていますが、その辺で、いいのがあれば紹介していただきたいなと思います。
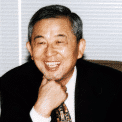
高野 せめて、ワークは検査しなくても、電極で保証できればいいのだという形を取っていかなければいけませんし、電極になるとギャップの問題が出てくる、数値が違う、その辺を自動的にどうやっていくかということだと思います。
製品部の形を追い求めていて、周りの分野が取り残されていると思いませんか?これが解決できれば金型向けのソフトとしてすばらしいものになると思います。
CAE
高野 CAEはどうでしょうか。
堀川 社内ではやっていないですね。お客様でやってきていただきます。プラスチック型は、成形メーカさんの工場のほうで、MOLD/FLOWなどを使って、面データに対してゲートを落とす位置など、方案設定をお客様がされます。海外に出すものは、製品保証なので、ゲートの設定も全部うちでやって、製品として保証しなければなりませんので、ここがネックになってきています。
我々は成形技術というところで、経験がないので、そこは今取り組んでいるのですが、MOLD/FLOWでやるところまで進んでいません。いずれはやらないといけないと思いますが。
高野 お客様で方案をシミュレーションして持ってこられる。御社の設計の方の経験値と比較、対比されて差はありますか。もう一点はお客様の方案設定で金型を作って、トライに入りますね。そのときに、合格点が取れるかどうか、その辺はいかがですか。
堀川 お客様の方でも経験のあるワークは、トライのときに合格点をとれる率が高いのですが、新しい物は打ってみてどうかというのが多いですね。ゲートの大きさ、ランドルの長さなど、トライで確認して、三点ぐらい落としても、ウエルドがいいところに出ないので、一点止めるとか、板厚で調整するとか、職人的なやり方が残っていますね。トライの回数を重ねなくてはいけないとか、必ず立ち会いして確認をしなければならないというイベントは、いまだに減らず、トライ一発からかけ離れていく要因として大きいと思います。
高野 バリと金型強度との兼ね合いは。
堀川 金型の強度は大きな影響があります。必要な剛性を数字で管理できれば。
ソリッドのいいところは、計算ができるところ。うまく使いたいです。
高野 ソリッドデータは、お客様で部品の解析、強度解析などをするための目的もあると思いますし、金型サイトでも最適設計をするためにそれを活用していかなければならないと思います。
米谷 鋳造の流動凝固解析をしています。一番効果が出たのは、アルミホイルの低圧鋳造ですね。
高野 形が規則正しいのですよね。
米谷 ホイールというのはスポークが方案なんです。一発目それで解析をして、指向性が取れてない、ここに欠陥が発生しそうだ、といった場合に、肉盗み形状を変えてくださいなどの提案をして、鋳造品質が向上したという例はあります。これが一番効果がありました。
ヘッドとかブロック、ダイキャストもやっていますが、これに関しては、ホイルのような先行型の解析ではなく、後検証です。
鋳鉄の砂型の解析のほうがむしろ進んでいまして、砂型は方案が命ですので、あるお客様では鋳鉄系の砂型については全品解析をして承認をしてからでないと型設計に入りません。お客様で解析できない部分を当社に依頼してくるのですが、鋳鉄の場合、溶湯上に酸化して浮いてくるごみのノロが悪さをします。これが製品に入ってはいけないので、方案で止めなければいけません。今、解析では材質が一種類しか決められませんが、そこを何とか解決するために、ノロと溶湯つまり2種類の材料が混在したときの解析ができるソフトがないか探しています。
高野 やはり、一発合格の要求は非常に強くなってきていますね。
白石 研究型はお客様で解析してこられます。解析が、解析どおり流れているか、流動解析がどこまで信頼できるかを確認するようなレベルだと思います。家電関係では、以前、ハイサイクル型ということで、増し型、増面ですね。これを作る際に樹脂メーカに解析してもらってゲート位置を変えたりしたことがありますが、社内では解析はまだしていません。
高野 解析の普及についてどのようにお考えになりますか。
堀川 方案の変更もトライの回数を増やす要因のひとつです。型保証から製品保証へだんだん要求が厳しくなっていて、自前で解析し提案する必要が出てくると思います。
HZSへの要望
高野 最後にHZSさんへの要望についてお話しを願います。
白石 設計とCAMの担当が別れていて、重なった作業をしています。せっかく全員GRADEを使っていますので、設計からパス出しまで、ひとつのソフトで簡単にできればと思います。パス出しの方はある程度自動化されたものがあって、設計に専念できるようなCAD/CAMにしていただきたいなと思います。
HZSさんはいろいろなソフトを扱っていらっしゃいますが、各商品とのリンクをもっとスムーズにしてほしい。ICEM SURFや、VERICUTなど、GRADEからうまく使えるように他商品とのリンクを考えていただきたいと思います。
高野 トータルで上手に説明のつくものですね。
米谷 PCのCAD/CAMで、60MBぐらいあるウォータージャケットのモデルをテストしましたが、十分使える速さでした。
そろそろPCも実用化の時期にきたと思いますので、導入コストの面でPC化を積極的にお願いします。
堀川 CAD/CAMを使っていく中で考えていかなくてはいけないのは、機械加工側とのリンクです。生産準備側での情報、その情報で加工したワークを、各工程でしっかり検証していかないと、どの工程が悪さをするのかつかめなくなります。これはHZSさんにお願いしたいことですが、まずモデリングデータと図面情報をきっちり検証ができるようなシステム。現状はモデリング職人の腕です。次にモデリングデータと加工情報、加工が終われば測定することを要求される。加工されたワークをモデリングデータを使って測定、評価する。金型の測定情報をお客様へもフィードバックし、次の金型、解析などの資料にする。そうしていかないとお客様も製品データを出すメリットがない。計測、データのフィードバック、そういったところもサポートしてほしい。
データ変換では、お客様との間だけではなく、社内でもいろいろなシステムを使っているので、どんなシステム間でも気にせず変換できるようにHZSさんのような業界できちっとやってほしいですね。仲良くオープンに。
高野 業界で仲良くね。ライバル意識はもちろん持ってもらって。
堀川 当社の場合、一人の担当者が複数の工程(設計、モデリング、パス作成)をこなすのでひとつのシステムで完結できるようにしたい。ソリッドですぐには全部実現できるようになるわけではないでしょうが、ソリッドデータでもサーフェイスデータでも問題なくやり取りできるような、データ授受に強靱なシステムにしていってほしいですね。
あとは生産準備から工場まで、自動化できる包括したシステムを考えてほしい。生産準備の分野へはかなり入ってきてもらっているので、これからは加工の現場に足を踏み入れ、現場を見ながら開発されると、他のCADメーカとの差別化ができるのではないかと思います。
高野 そうですね、その差別化という言葉はいいと思うんですよ。金型向けのCAD/CAMということからすると、今、おっしゃったとおりだと思いますね。
川下 今日は、いろいろ教えていただき、ご要望も承りました。モデリングが速くできるということに関しては、永遠のテーマだと思います。結果としてGRADE/CUBEIIのほうで、答えを出させていただきたいと思っています。
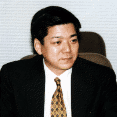
CAM自動化に関しましては、各社で自動化システムは、全部違うと思います。私どもがトライできる範囲としては、個々のお客様に自動化の枠組みをご提供し、標準化されたものをデータベースとして使える、データを種々選択して、ある条件をシステムの方から提示するという仕組みを目指していこうと考えています。その第一ステップは、GRADE/CUBE-NC V9で、加工工程設計という機能をご提供させていただきます。
自動化へ向けて更にどういうものが必要か検討していきたいと思いますし、逆に皆様からも、自動化するためには何がいるかということを教えていただいて、自動化の枠組みをもっともっと充実させることができる環境をご提供していきたいと思っています。
HZS 本日お話しいただいたように、金型には他にもいろいろなお仕事があり、本当の意味での金型用のシステムはこれからだと思います。我々がこのことを実現しようと思うと、お客様との議論、ご教授がなければできません。今後とも是非、ご指導をお願いします。