株式会社中島田鉄工所様は、あらゆる工業製品に組み込まれるネジ・ボルトの部品を製造するプレス機械であるヘッダー、フォーマーの世界屈指のメーカです。時代とともに複雑化、多様化するニーズに対応できる独自技術と優れた一貫生産体制を確立し、より高性能なヘッダー、フォーマーを各業界へ送り出されています。
今回は、SPACE-Docの導入の背景、効果や現状などのお話を中心に代表取締役専務 中島田正宏様、技術部 機械設計課 課長 酒井康行様、技術部 設計課 田中伸弥様にお伺いしました。
事業概要
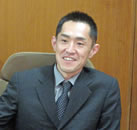
中島田 正宏 様
1911年(明治44年)の創業当初から、肥料の配合機や番傘の骨格となる竹材の量産機械など、その当時のニーズに合った機械を製作してきました。1936年に当社の礎になる研削盤の生産を始めて、1960年に今の主力製品であるヘッダーの生産を開始しました。そして現在は、ヘッダー技術を応用して段数を増やし、複雑な形状を製造するフォーマーも生産するようになりました。当社は、材料の直径1mm以下の超小型、6~16mmの中型を得意としています。主なお客様は、自動車業界ですが、腕時計、携帯電話、パソコンなどの非常に小さい金属部品の電子部品業界では、高いシェアをいただいており、この超小型サイズでは、国内の競合メーカはほとんどいません。おかげさまで、4年ほど前から増収増益になり、前は非常に苦しい時代もありましたが、現在は良い状況にあります。
また、海外への販売も1970年代から始めており、アメリカ、ヨーロッパを中心に、アジア各国などへ販売網を拡大してきました。主力は自動車関係ですが、この2~3年は飛行機関係が伸びています。
製品生産の現状
■ヘッダーとフォーマー
ヘッダーという名前は、ネジやボルトの頭を作るという意味です。コイル材を伸ばして切って、ネジの製品になるまで成形します。簡単なネジであれば、金型が予備成形と製品成形の2段になりますが、形状の難しいものは段数を多くして、穴を開けたりしています。当社では、段数が多いものをフォーマー、少ないものをヘッダーという分け方をしています。複雑な部品になると5段、6段になり、これから生産に入るものには7段があります。
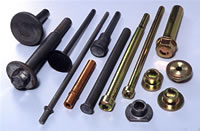
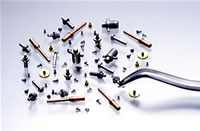
時計用の極小金属パーツ
■生産効率
当社は、カタログモデルだけでも70以上の機種を揃えています。この豊富な機種でお客様の幅が広がっているのですが、そこで問題になっているのが生産効率です。通常は、6~8ヶ月の納期で完成していましたが、今は16ヶ月先まで納品する機械の受注が決まっている状態で、それが最短納期になっています。こういう状況になったのは、この10年間で初めてです。ご注文いただけるのはありがたいのですが、これは嬉しい悲鳴ではなくなってきています。ひとつは材料の値上げの問題で、1年半後の価格が分からないまま、ヘッダー、フォーマーの価格を設定するというリスクが伴います。
それから、お客様が欲しいと言われる納期と当社で作って納める納期とのギャップが大きくなっています。特に携帯電話やゲーム機は流れが早く、サイクルが3ヶ月ぐらいです。どうかすると図面が流れてきて、部品が作れるかトライ&エラーをしている間に終わってしまいます。3~6ヶ月先までに納品できれば、注文していただけるお客様も多いので、そこのタイミングを合わせたいと思っています。今の状況は、受注に生産が追いつけないため納期が長くなっているので、売上げには反映できていません。そのため、いかに効率を上げて工数を削減して短納期で、ボリュームを上げるかに取り組んでいます。
■生産計画の見直し
いつ、どの機種のご注文をいただけるか分からないので、生産計画をその都度作り直しています。少量多品種で、ある機種だけは在庫を持ちながらになるので、生産計画を立てるときに、いつも思案するところです。ある程度先読みして、生産予定にしていた台数を減らしたり、違う機種を入れたりと調整する必要があります。本当はフレキシブルに対応するために、できるだけ在庫を持つのがいいのですが、ニーズがかなり流動的なので、在庫を持つリスクもあります。特に小型部品は、10年前のITブームで携帯電話、パソコンなど需要が増え、当社も一番小さいネジを製造する機械が半年間で100台売れたことがありました。でもブームが終わると、32台を売るのに2年もかかりました。
■部品内製と組み立て技術
当社は、部品の内製率が7割を超えています。世界中でメジャーな競合メーカは10社ありますが、ここまで部品を内製しているのは当社だけです。他社は内製しても4割ぐらいで、あとは外注の機械加工部品を使ってアセンブリするのが主流です。当社の工場は、3/4が機械加工で、残りの1/4が組み立てになります。
一般的な部品をアセンブリするのであれば、納期の短縮もできるのですが、精度の高い機械を作ろうとすると、やはり組み立てる担当者もそれなりの教育が必要になります。この組み立て時には、耐久性を高めるために「きさげ」という摺動面をすり合わせる作業があります。このため、最低でも3~4年は現場に入り、組み立ての技術を習得しなければ精度の高い機械はできません。高精度の部品を内製し、組み立ての技術を保持していくことで、当社の特徴である高精度の製品が生産できるのです。
SPACE-Docの導入と効果
■導入背景と開発の流れ
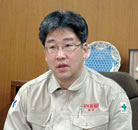
課長 酒井 康行 様
1機種あたりの部品数は、平均して600~800点になり、図面では700枚ほど発生します。1年間に、35~50機種を合計180台作るために、違う図面をラインに合わせて一気に出図することになります。そうすると1週間に約1機種分の図面を出す必要があります。今までは、A1からA4までの紙の図面が原紙としてキャビネットに納められているので、明細表に沿って必要な図面をキャビネットから選び出し、1枚をコピーして700枚の図面を揃えるという作業をしていました。
まるで神経衰弱的な作業で、肉体的、精神的にもかなりの負担があり、この作業を何とか改善したいと考えていました。この状況の中でNDESに相談したところ、SPACE-Docであれば改善できるのではと提案されたので、非常に良いタイミングでした。技術部は20名で、Space-Eを10台、AutoCADを10台使って、開発、図面作成などを行っています。データとしては、形式の異なるSpace-EとAutoCADになるので、サーバも含めて別々に管理していました。それがACE-Docであれば、一緒に管理できるということで、渡りに船という感じでした。他社の売り込みもたくさんありましたが、Space-EとAutoCADの図面を同時に管理できないので、当社に合った運用を実現するにはSPACE-Docだと判断して導入することにしました。
2005年1月にSPACE-Doc導入の意思を伝え、その3月に現状の説明をするため担当営業と打合せを行いました。そして、5月からSPACE-Doc中島田仕様の開発を始め、7月には検収を上げるというスケジュールを立てました。しかし、実際にはそう簡単に進まず、当社の中でも整理が必要でしたので、問題をひとつひとつクリアしながらの開発になりました。その中で、当社の図面枠も一新しました。そして、1年半かかり当社の要望通りにカスタマイズしてもらい、実際の運用を開始したのは2006年の夏でした。
■SPACE-Docの特長と効果
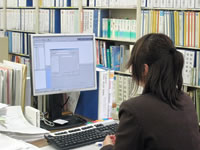
これまでは、図面はただの紙切れだったのですが、SPACE-Docに入るとそれが電子情報の固まりになります。図面のある指定された位置の文字が全てデータになり、属性(図面番号・部品名称・材質・個数・兼用機種)が自動抽出されて、自動出図や個々の検索や選別(標準部品or特別部品)が瞬時にできるので、当社にとっては画期的な機能と言えます。図面出図をするときは、機種を入力するだけで、該当する全ての図面を検索して700枚揃った時点で自動出図します。
検索された図面がSpace-E、AutoCADの違いや用紙サイズの違いが混在していても一度の操作で自動出力できます。それから、出図作業も今まで1機種が3日間かかっていたのが、SPACE-Docの自動出図では1時間でプリントアウトが終わるようになりました。その1時間のプリントアウト時間も別の作業ができるので、その後の折り曲げの作業を入れても半日ぐらいで1機種が終わるようになり、作業時間の短縮につながりました。
そして、これまで図面管理自体が非常にルーズだったのが、ルールを破ると自動出図できなくなるので、技術メンバーも統一されたルールを守るようになりました。その他には、AutoCADでしか見れなかったサムネイルがSpace-Eでも見ることができたり、サーバの一元化として、Space-EとAutoCADの図面が混在しても、ひとつのフォルダで管理できるようにもなりました。
SPACE-Docで、よく使う機能は、全てメイン画面上に配置してあるので、アイコンでファイルの状態、チェックイン/ アウト状況や履歴情報も確認でき、図面検図欄自動押印機能で、承認済/ 未がひと目で分かります。その他には、生産計画を変更した場合、1週間かけて揃えた図面が無駄になることもあったので、担当者の労力のことを考えると結構気になっていました。それが、SPACE-Docだと気兼ねなく生産計画を変更できます。これで精神的にかなり楽になりました。
■図面のCAD化
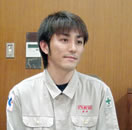
田中 伸弥 様
もうひとつの効果が、今回のSPACE-Doc導入と同時にNDESに依頼した図面のCAD化です。これまでも機械の担当者から図面のCAD化の要望はありましたが、目先の仕事に追われてできない状況でした。それが今は、現役機の全部の図面をCADデータにできたので、それも大きな成果です。これまで、3000枚強をNDESにお願いして本当に助かりました。
今でもCAD化できていない機種があるので、それは手作業で図面を揃えています。やはり、その作業が大変なため、まだ図面がSPACE-Docに全部入らないのかと担当者によく聞かれます。通常使っている図面は7000枚ぐらいで、後はめったに出ないものですが、今も毎月300枚ずつの図面をNDESにCAD化してもらっています。
当社の特長でもありますが、部品の保証期間は無期限にしているので、過去の図面は全部永久保存して、当社の製品を使われている限り、保守は行います。通常ヘッダー自体の生産ライフは、平均20年ですが、出荷した後、お客様のところでは平均30年は使われています。お客様からは、スペア部品がすぐ手に入ると言われ、そういうことも信用につながっています。保守で部品依頼が入ると、この10~15年の機種であれば、CADデータの図面検索で簡単なのですが、古い機械の部品は、手描きの図面や青焼きした古い図面から引っ張り出しています。それが30年前のもので、その当時の方がいないと図面を探すのが大変なので、今後も図面のCAD化は続けていきます。
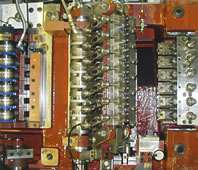
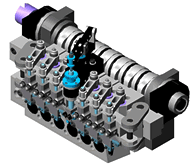
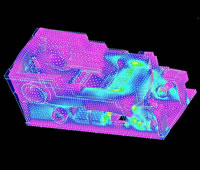
今後の展開
■工程管理にバーコードを利用
SPACE-Docと図面のCAD化で、計画の半分が実現できたので、今後は図面から工程管理まで行いたいと考えています。生産現場では作業日報としていつ何を加工したのか、仕掛り前と後の時間を記述して手作業で集計結果をパソコンに入力しています。これを自動的にボタンひとつで集計したいので、図面枠にバーコードを載せようという計画を立てています。このことは、製造部門からの依頼で、図面を印刷するときにバーコードを入れる欄を図面枠に設ける必要があるため、一緒に進めることになりました。
生産現場でバーコードを利用して、工程管理が一括管理できれば、作業者が1つの部品を仕上げるごとに時間を記述する作業もなくなり、正確に集計できます。また、工程状況を把握することで、加工途中の部品も容易に探すことができ、お客様への受注部品の納期回答も正確な日にちをお伝えできます。
■お客様の利益優先
やはり、利益率の高い機械を作りたいと思っています。それには、まずお客様の利益を優先して作るということです。お客様が作られているネジ1本の価格から、いかに安く、そして精度を出すかという検討をします。単に効率をアップしてコストダウンにつなげるだけでなく、ある形状を追加することで売上げが伸びるようなご提案をしていきたいと思っています。単純なネジだけでは中国に価格で負けてしまうので、付加価値を付ける部品にする必要があります。そのためは、機械もおのずと付加価値を付けることになります。その付加価値が、サイズであったり段数であったりしますが、当社が一番こだわっているのが、精度の高い機械を作ることです。まず、お客様の利益を優先に考えていくと、おのずと当社にとっても良い方向に進みます。
今後は、これまでの技術を応用して横展開をすること、そして特注でワンオフの機械や専用機械にも力を入れたいと考えています。
NDESへのメッセージ
もともとNDESとは、旧HZS時代からの長い付き合いですので、いつもサポートしてもらい大変助かっています。SPACE-Docの件では、NDESによく問合せをしていました。中島田仕様にも関わらず、図面枠抽出方法、仕様用途などの質問に対して迅速な回答をしてもらえたことに感謝しています。そのサポートがあったおかげで、私たちも個々に仕事を持っていたにも関わらず、運用まで対応してこれたと思います。それもあって、この度のSPACE-Docのカスタマイズは、他のお客様にこの技術が応用できて、何らかのお役に立つのであれば、是非NDESに営業していただきたいと思っています。
今後も、できるだけ設計に専念したいので事務処理に時間をかけないための機械化、電子化を実現するために、引き続き良い提案をお願いします。
おわりに
一時雇用や派遣社員は雇用の対象にしない方針で、従業員の140人中、パートは2人だけで138人は正社員だそうです。「社員に格差を付けず、同じ土俵で仕事をする」と語られていた中島田専務。社員一丸となって世界に誇る高精度の製品を作り出す意気込みが伝わってきました。
大変お忙しいところ、貴重な時間をさいてお話を聞かせていただき、ありがとうございました。
会社プロフィール
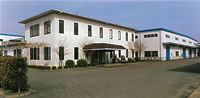
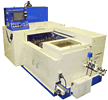
株式会社 中島田鉄工所
本社 | 〒834-0196 福岡県八女郡広川町大字日吉1164-4 |
---|---|
設立 | 昭和26年10月(創業:明治44年5月) |
資本金 | 45,000,000円 |
売上高 | 32億9,000万円(2006年度) |
従業員 | 140名(2006年現在) |
事業内容 | 工業製品(腕時計・携帯電話・コンピュータ・自動車・飛行機など)に組み込まれる部品、ネジ・ボルトを製造するヘッダー、フォーマーの開発・設計・製造・組み立て・販売・サポート |
関連するソリューション
関連するソリューションの記事
- 2021年07月10日
-
4事業部のご紹介(2)
製造ソリューション事業部
- 2010年10月01日
- 個人の失敗を大事(おおごと)にしないために
- 2010年04月01日
- 継承可能な管理運用ノウハウ
- 2010年04月01日
- かんたんPDM、ドキュメント管理 SPACE-Doc V3 のご紹介
- 2008年10月01日
-
PLM技術レポート(第8回)
各種システムによるPLM連携の強化について
- 2007年04月01日
-
図面・文書管理のフレームワーク
「SPACE-Doc」のご紹介