Process Designer / Process Simulateのご紹介
PLM事業本部 営業統括部 営業開発部 ROBCADサポートグループ 酒井 康裕 |
はじめに
昨今、製造業の生産技術部門では、さまざまなITツールを駆使し、作業の効率アップを図ってきました。しかし、各ツールを使うことで個別データが発生しています。例えば、以下のようなデータです。
- 工程設計書(Excel・PowerPoint)
- 設備コスト表(Excel)
- レイアウト設計書(AutoCAD)
- 3Dデータ(CATIA・UG・Pro/E)
これらの個別データは、各部署・各担当者の単位で管理されており、工程計画を行う場合は、データ収集にかなりの時間を費やしていました。また、工程計画を修正する場合でも、個別データの関連性を考えて工程を修正する必要があり、ミスが発生しやすい状態でした。これからご紹介する工程設計・管理ツールProcess Designer(略称:PD)およびシミュレーションツールProcess Simulate(略称:PS)は、このような問題を解決し、開発のリードタイムを短縮、コスト削減を実現します。
溶接領域での作業フローについて
図2は、自動車をスポット溶接する工程での標準的な作業フローです。この作業フローに従って、Process DesignerとProcess Simulateを使用すると、全ての領域をカバーできます。
次に各ツールをご紹介します。
Process Designer (工程設計ツール)
■Process Designerの概要
Process Designerでは、生産技術が必要とするプロセス(工程)・プロダクト(製品)・リソース(設備)の各種データ同士の関連付けを行います。その関連付けられた情報を独自のサーバ(eBOPとeM-Server)とOracleデータベースで管理します。これにより、Process Simulateでシミュレーションするときに、必要な情報を即座に収集することができます。
また、Process Designerには、ユーザ管理機能を備えているので、複数のユーザによる協業作業が可能です。
■Process Designerによる工程設計
Process Designerでは、工程設計でよく使用されるPERT図を利用して工程設計を行います。
例えば、 「 工程1:部品AとBの組立工程」、次に「 工程2:部品A・BとCの組立工程」といった具合に工程の順序を設定します。(図3、図4)
各工程に必要な部品を関連付ける場合は、3Dデータをドラッグ&ドロップすることで、簡単に関連付けられます。また、多数のスポット溶接を行う自動車の工程設計では、ロボットが溶接する打点も各工程に関連付けます。このように、工程ごとに関連する設備・部品・溶接打点などを割り当てていき、その工程を順番に線でつなぎ合わせて、製品を組み立てる全体の流れを設計します。次に各機能をご紹介します。
①PERT図およびGantt Chartの作成機能
PERT図を作成する機能で各工程の順序を設定後、その工程に関連する部品や設備などを登録します。事前に各設備のコストが入力されていれば、設備コスト表を出力できます。また、各工程での許容時間を設定すると、工程のGantt Chartを出力できます。これにより、設計変更などがあった場合でも、必要な書類を迅速に出力できます。(図5)
②In-Process Assemblyツリー作成・表示機能
PERT図から工程順序に従った製品のアセンブリ(IPA)ツリーを自動的に作成します。また、アセンブリツリーにある工程のチェックボックスをONにするだけで、その工程での製品の組み立て状況を表示し確認できます。(図6)
③Webベースでの工程に関するレポート出力機能
Webベースで工程に関するレポート(図7)を表示できるので、コミュニケーションツールとしても使用することが可能です。このレポートは、カスタマイズすることで、さまざまなレポートを出力できます。
④工程データのインポート&エクスポート機能
定義した工程内容を外部データ(独自フォーマットXML)に入出力できます。これにより、従来の製品を流用して新機種を立ち上げる場合、出力したXMLファイルを取り込むことで、迅速に立ち上げることができます。
Process Simulate (シミュレーションツール)
■Process Simulateの概要
Process Simulateは、 Process Designerで設計した工程データを元に、ロボットを使用した自動車などの生産ラインを、ゾーンやステーションごとに以下のようなシミュレーションを行うことができます。
- ロボットや設備の協調制御シミュレーション
- ロボット同士の協調制御シミュレーション
これらのシミュレーションを行った結果、各ロボットの動作プログラムの作成やサイクルタイムを算出することができます。Process Simulateは、3DデータにJTフォーマットを採用しているため、従来のROBCADに比べると、より多くのロボットを同時にシミュレーションできます。
次に各機能をご紹介します。
①ロボット配置チェック機能
②各種データ検索機能
溶接打点や溶接ガンなどを検索する際に、設定されている属性をキーとして検索することができます。例えば、溶接ガンを検索する場合、検討する溶接打点のガン圧の適用範囲を入力して検索することも可能です。これにより、膨大なデータの中から迅速に目的のデータを見つけることができます。(図9)
③溶接ガン適用検討機能
溶接打点に対する溶接ガンの挿入角度のチェック範囲とチェックする分割数などのパラメータを設定することで、溶接ガンの適用性(干渉の有無)を自動チェックします。これにより、その工程での作業に適切なガンを迅速に見つけることができます。(図10)
④溶接ガン自動挿入方向設定およびパイチャート表示機能
溶接ガン自動挿入方向設定機能は、溶接ガンを持ったロボットが、溶接する打点位置で干渉の無い姿勢をとれるよう、自動的に姿勢を変更します。
また、パイチャート表示機能は、溶接ガン自動挿入方向設定機能を使用してもロボットと設備・製品が干渉する場合や、自動で設定した姿勢ではなく、作業者で姿勢を決めたい場合に使用します。この機能は、溶接打点位置でのロボットの姿勢状態(干渉や到達性)を円グラフで表示します。これにより、ロボットの姿勢をどのように変更すればいいかを迅速に判断でき、決定することができます。
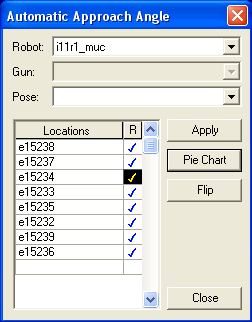
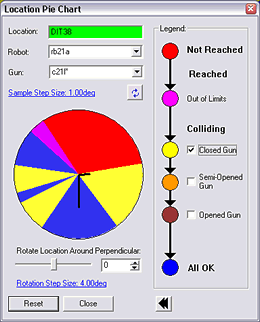
⑤溶接打点配分検討機能
各ロボットに適用されている溶接打点の到達性と干渉の有無を一覧表で表示します。この表を元に、溶接打点の配分を考えながら、適用させるロボットに対してチェックマークを設定するだけで、自由に溶接打点の移動が可能です。これにより迅速に溶接打点の配分検討を行うことができ、各ロボットのタクトタイムを平均化することができます。
⑥イベント型シミュレーションロジック
従来のROBCADでは、時間軸に準じたシミュレーションを行っていたため、あるオペレーションを複数の条件によって実行するようなイベント型シミュレーションができませんでした。
しかし、このProcess Simulateは、イベント型シミュレーションロジックを採用しています。これにより、複数のイベントを論理演算式(ANDやORなど)で条件設定し、その条件が一致した場合に、オペレーションを実行するようなシミュレーションが可能になりました。
例えば、「複数のロボットの協調制御」や「仕様差異の条件シミュレーション」、「規定溶接回数時のチップドレッサシミュレーション」などのシミュレーションが可能です。
⑦バーチャルコミッショニング機能
PLC(プログラマブルロジックコントローラ)の情報を収集しているOPCサーバとの通信を行うことにより、工場の配線工事をする前に、PLCプログラムの確認ができます。事前に確認することで、工場の早期立ち上げを支援できます。また、チェックが終われば、オペレータに対して、事前教育を行うことも可能です。
※ OPC (OLE for Process Control):米国OPC Foundationが策定した規格
⑧新旧溶接打点のマッチング機能
次期開発が従来製品の部分的な仕様変更になった場合、溶接打点の順番や経由点など、再利用できる情報があります。このような場合に、従来の溶接打点と新しい溶接打点のマッチングを行い、新旧の溶接打点を置き換えることができます。これにより、今まで作成したデータを有効活用できるため、短い作業時間でロボットのプログラムを作成できます。
おわりに
このProcess Designerおよび Process Simulateは、現在、生産技術の分野で適用されています。
今後、データベースを設計分野で利用されているTeamcenterへ移行し、設計データベース(E-BOM)と生産技術データベースを1本化することで、設計から生産技術までのデータを集中管理し、ささらなる開発のリードタイム短縮につなげることができます。
なお、ここではご紹介できなかった機能もあります。お気軽にお問い合わせ先までご連絡ください。
関連するソリューション
関連するソリューションの記事
- 2021年07月10日
-
4事業部のご紹介(2)
製造ソリューション事業部