プロセスの3次元化を飛躍的に促進
パナソニックデザイン社様は、より多くの人に使いやすいユニバーサルデザインの実現と、一目見てパナソニック、ナショナルとわかるデザインアイデンティティーの確立の取り組み、「革新デザインの創出」にチャレンジされています。その中でHAデザイン分野様は、プロセスの3次元化による効率化・さらなる生産向上を目指していらっしゃいます。今回は、Space-E CAA V5 Basedを導入された利点や今後の効果についてのお話を中心に、HAモデリング開発担当の、主任意匠技師 畑中由紀夫様、吉田典久様、松本哲也様、原田修様、杉林正一様にお伺いしました。
事業概要
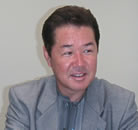
畑中 由紀夫 様
松下グループの社内分社として設立されたパナソニックデザイン社の中で、HA(ホーム・アプライアンス)デザイン分野は、主に家事・調理・空調・設備製品のデザインを行っています。組織の下でなく、インハウスのモデラーとして、製作部署を自主独立形態に近い形で運用していく方向性から、「チーム」という名称でなく「モデリング開発担当」という名前になっています。デザイン部門全体のミッションが、革新デザインの創出、経営革新の実践ですので、それに向けてイメージの具現化の精度向上と、開発費削減、コストダウンを行うべく、3次元化に取り組んできました。
デザイン部門のミッション ~グローバルエクセレンス実現~
- 革新デザインの創出
- 経営革新の実践
Space-E CAA V5 Based導入の背景
【なぜ3次元化が必要だったか】
今までは、手書き、手加工、図面は2次元というのが当たり前でしたが、そこにメスをいれないと効率化はできませんし、品質の向上もできないと考えました。そこで、基本の技術・ノウハウをコンピューターに置き換えようという取り組みを1992年から始めました。つまり、プロセスを自動化していこうということです。単にコンピューターを置くことによって効率化するのではなく、今までの技術をそのコンピューターで発揮させようという取り組みです。全体の構想としては、全てをデジタルに置き換え、それをネットワークで繋いで無駄を省く。メインは製作側の3次元化、加工側の3次元化・NC化です。2次元のグラフィックスについても、デジタルに置き換える。そうすることで、関連部署との間でもデジタルデータでやりとりを行い、それによりミスや認識の違いをなくしていけば、品質が向上するだろうという考えで、取り組んできました。
【3次元化への道】
大変だったのは、今まで、木型加工を行っていた部署の意識改革もさることながら、行動改革も伴うということです。カンナからコンピューターとマシニングセンターを使う、つまり、自分の手ではなく機械の手を借りる、そこに大きな不安がありました。それらを支援するためには、簡単に使えるものを選択しなくてはなりません。
デザイナーは、自分の意図を2次元図面にして、次の段階の担当者や、商品開発に携わる技術者に伝えます。でも現実としては、2次元では正確に伝えられない部分も多いものです。そのような状況から、3次元化することで、次工程への伝達データの信頼性は飛躍的に向上します。また、NC加工によるスピードアップが望めます。例えば、夜に加工をすれば、次の朝にはモデルができあがっている。デザイナーにとって、早く自分のイメージが具現化できると、おかしいなと思うところはすぐに修正ができますし、つまりはデザイン制作の品質向上に繋がります。そのようなことから、3次元化の効果はとても大きいです。
もう一つは、デザイナーがモデルを創るということです。デザイナーの専門性の中には、「ものをつくる」という専門能力があります。現在のモデリング開発メンバーは、そのほとんどがデザイナーです。
アナログからデジタルへ
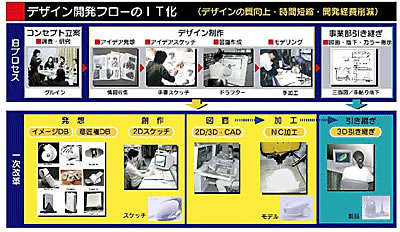
■情報蓄積とアイデアの質向上 |
|
■アイデア発想の効率化(修正・加工) |
|
■アイデア資産化・意匠権管理 |
■内製化率の向上 |
■画材費の削減 |
■引継ぎ精度の向上 |
■モデリング時間短縮 |
■設計時間短縮 |
■具現化精度の向上 |
シェル化時間半減 |
【Space-E CAA V5 Based】
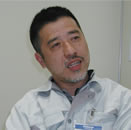
吉田 典久 様
今まで使用していたシステムは機種も古く、それに変わる、それ以上の効率化を図ることができるツールは何かを調査していくうちに、Space-E CAA V5 Based CAM(以下、Space-E V5 CAM)にたどり着きました。当時、汎用のCAMにはほとんどCADの機能がなく、CADとCAMの機能を備えたシステムを導入したいという思いがありました。様々なシステムを検証した中で、CATIAとSpace-E V5 CAMであれば、今までとあまり変わらず、非常に近い環境でスムーズに作業ができるだろうというのが、大きなポイントでした。計算が速いという点では、他にも候補となるシステムはありましたが、後々続けていく中で作業環境の重要性を考えて、CATIAとSpace-E V5 CAMを導入しました。
導入の効果
【時間短縮】
特長的なのは、計算時間です。本当に計算時間が苦になりません。例えば、エアコンの吹き出しの細かいリブ部分を加工しようとすると、以前は、帰宅する前に計算の仕込みをしても、翌朝できるかどうかでした。一度に計算すると重いので、マシン3台に分けて計算させるような工夫をしないと、本当に何時間もかかっていました。それが、Space-E V5 CAMでは、1/10の時間、もっと速いときもあります。早く結果が出ると、その分だけ時間ができますから、他の作業に取りかかることができます。
2年前に2名でSpace-E V5 CAMを使い始め、この2年間で十分に運用できていると思います。以前使用していたシステムを導入した時は、CADを使いこなすまで半年から1年、そこからプログラムの失敗が減るまで2~3年かかり、軌道にのるまで足掛け3~4年はかかりました。Space-E V5 CAMでは、導入から軌道にのるまで1年もかかりませんでした。やはり、使いやすいということでしょうね。計算時間も早いので、試行錯誤ができます。前システムでは1日かけてやらないと習得できないことが、Space-E V5 CAMだと瞬間に結果がでるからすぐに分かる。だから習得スピードも速くなりました。計算時間が10倍早くなったということは、10倍早くシステムを理解し、経験を積んでいけるということだと思います。
【オートマチック車】
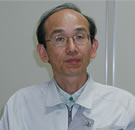
原田 修 様
Space-E V5 CAMは、よくできたオートマチック車みたいですね。オートマチックは、誰が乗っても、そこそこのスピードで走れるから、その点の安心感があります。
以前のシステムはマニュアルだったので、注意をしていないと、ミスが出ます。面を拾い忘れる、というようなミスが全く発生しませんから、0からスタートして、ある程度のスピードまで上げるのは簡単です。素人でも、ギアをいれたら簡単に運転できるので、あまり難しいことを考えなくても運用できるというメリットがあります。極端な話ですが、CADはできなくてもCAMのプログラムは作成できる、そういうシステムですね。
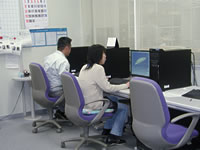

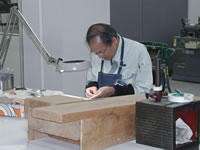
今後の取り組み
【さらなる生産性向上をめざして】
現在、社内で需要のあるモデルのうち、35~40%あまりを内製していますが、もっとたくさん製作できればと思います。モデルをつくる方法論はいろいろあるのですが、その中でプログラム作成にかかる時間というのは、以前は、手で仕上げている時間と半々くらい、もしくはそれ以上に時間がかかっていたかもしれません。計算時間も含めて、加工が終わるまでの時間を考えると、Space-E V5 CAMを導入してから、かなり短縮できました。また、人の手が空く時間は確実に増えましたので、その時間を仕上げにまわすことで、非常に生産性が上がり、効率のよい仕事ができるようになりました。今はマシンを増やさないと、プログラム製作に追いつかない現状も出ています。それだけソフトウェア側で効率化ができているということですね。
【今後の課題】
最終段階で人の手が介在するので、現在手で仕上げている部分をどこまで効率化するかというのが、今後の課題になってくると思います。ただ、現状ではデザインモデルという特性上、必ず最終的に人の手が入るので、そこの部分の能力差が、モデルの出来映え等に反映されます。そういう意味では、まだまだ職人技が必要とされる製作物でもあります。仕上げを省くために、プログラムでとことん加工精度を上げ、細かいところまで追い込んでいくことが、プログラム作成上での次のステップであり、全員でトライしているところです。そういう意味では計算してもすぐに計算し直すことができるシステムを利用すること、つまり、試行錯誤できるということは、ツールとしても非常にレベルが高いのではないかと思います。
ワーキングモデルを製作されている会社さんの中で、仕上げをされているところは少ないのではないかと思います。弊社では、最終表面処理をする前にペーパーで研いて、きれいにしていかなくてはなりません。社員全員が、かなり高いレベルでプログラムができ、安定したものづくりを行うことができれば、手仕上げはかなり効率化できるのではないかと思います。
【デザイン全体の取り組み】
デジタル化は、まだまだ奥が深いと感じています。もともとコンピューターはノウハウを置き換えるため、プロセスを自動化するためのもので、それによって新しい手法、新しいプロセスを産みだせればと考えていました。そういう意味では、新しいプロセスになったのは、木型からNCに変わった試作だけであって、デザイン全体はなかなかできていないと思います。プロセスの3次元化による問題の早期解決、商品開発全体のリードタイム短縮のためには、デザインの曖昧な部分を正確にデータにすることが大事だと思います。今後はIT、インフラがさらに整備されていきますので、もっとバーチャル的なことに取り組んでいかなければとも考えています。
HZSについて
【マニュアル車】
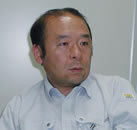
松本 哲也 様
前にオートマチック車の話をしましたが、欲を言えば、もう少しマニュアルの部分があればいいなと思います。
データ通りではない、ここだけイレギュラー処理をしたいという時があるので、決まった加工以外のアレンジができればもっと活用できると思います。誰が使っても同じ加工ができることを目的にして開発されたシステムだとは思いますが、ぜひとも実現してもらいたいです。
【さらなる自動化】
さらなる自動化が、失敗がなくなることに繋がると考えています。ある店の牛丼は、美味しい・早い・安価の3つのポイントを完璧に押さえていますが、Space-E V5 CAMであれば、例えば、きれい・早い・安価の3つを押さえ、突き詰めていって欲しいと思います。また、昔から言われていることですが、デザイナーが使えるCAM、デザイナー自身が機械のボタン1つ押しさえすれば加工できる、そんなマシンがあれば、デザイナーは、もっと時間短縮できるのにとも思います。加工したいと思ったときにすぐにできれば、デザイン全体としては非常に効率化すると思います。現在は理想に近づいてきているとは思いますが、まだまだ専門知識が必要です。
【HZSへの期待】
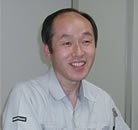
杉林 正一 様
弊社では、金属ではなくアクリルやプラスチックなど欠けやすい、割れやすい神経質な材料を使用します。金属は割れませんが、アクリルなどは欠けやすい素材です。そんな材料を利用するときには、オートマチックではない加工方法が必要となります。加工方法の基礎は金属であったとしても、違う素材に置き換えたときに、同じ方法で通用するのかどうかは、御社の中でも、業界の中でも検証されていないように思います。そこは我々でもわからない、調べることができないので、日常手探りで経験値による加工を行っています。そのノウハウがSpace-E V5 CAMの中での加工機能として搭載できれば、我々のような業界でもっと活用できると思います。今の加工方法は金属ベースだと思うのですが、それだけで十分だろうかと思います。システム開発・販売を行うだけでなく、そういう部分まで踏み込んで欲しいですね。現実の加工と加工機・ソフトウェア、その接点がこの業界にはあまりないので、HZSに頑張ってもらい、我々に教えていただけたらと思います。
Space-E V5 CAMが、トップを走り続けるために、今後いろいろなデータベースを持つようになれば、我々としても、もっと使いやすくなると思います。
おわりに
HAモデリング開発担当の皆様には、業種は全く違っていても、同じメーカーとして、お客様の声を聞くこと、自分達の製品をうまく伝えることの難しさ、大事さを改めて教えていただいたように感じます。大変お忙しいところ、貴重な時間をさいてお話を聞かせていただき、ありがとうございました。この場を借りてお礼申し上げます。
会社プロフィール
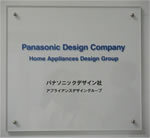

パナソニックデザイン社
松下電器産業株式会社
本社 | 大阪府門真市大字門真1006番地 |
---|---|
設立 | 昭和10年12月(創業 大正7年3月) |
資本金 | 2,587億4,000万円 |
従業員 | 290,493名(連結)51,340名(単独) |
売上高 | 74,797億円(連結)40,814億円(単独) |
パナソニックデザイン社 | |
本社 | 東京都港区新橋6丁目17番15号 |
HAデザイン分野 | 大阪府豊中市神州町1番2号 |
設立 | 松下電器産業株式会社の社内分社として2002年4月1日設立 |
従業員 | 304名 うちHA分野 約100名 |
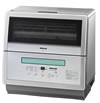
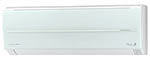
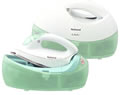
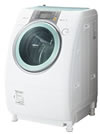
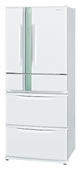
関連するソリューション
関連するソリューションの記事
- 2021年07月10日
-
4事業部のご紹介(2)
製造ソリューション事業部
- 2019年01月01日
-
CAD/CAMシステムオンラインサポートサイト
e-support リニューアル公開のお知らせ
- 2017年01月01日
-
3DEXPERIENCE Platform ENOVIA V6による
プロジェクト管理のご紹介
- 2016年10月01日
-
3DEXPERIENCE Platform ENOVIA V6による
BOM管理のご紹介
- 2016年07月01日
-
CATIA V5 ENOVIA V6
バンドルパッケージ(ASO3X-JP)のご紹介
- 2014年10月01日
-
トータルソリューションのご提案(1)
STLの活用例
- 2010年07月01日
- Space-E CAA V5 Based 新機能のご紹介
- 2010年01月01日
- Space-E CAA V5 Based R18 Update1 新機能のご紹介
- 2010年01月01日
-
導入支援レポート(第3回)
「経験」に基づいた導入支援におけるカスタマイズ方法
- 2009年10月01日
-
導入支援レポート(第2回)
「経験」に基づいた導入支援における金型テンプレート構築方法
- 2009年07月01日
-
導入支援レポート(第1回)
「経験」に基づいた導入支援の進め方
- 2009年01月01日
- Space-E CAA V5 Based R19 新機能のご紹介
- 2008年07月01日
-
PLM技術レポート(第7回)
CATIA V5を使用した設計業務におけるカスタマイズ事例
- 2008年04月01日
- Space-E CAA V5 Based R18 新機能のご紹介
- 2007年10月01日
- Space-E CAA V5 Based R17 Update2 新機能のご紹介
- 2007年07月01日
- Space-E CAA V5 Based R17 Update1 新機能のご紹介
- 2007年01月01日
- Space-E CAA V5 Based R17 新機能のご紹介
- 2006年10月01日
- Space-E CAA V5 Based R16 Update 新機能のご紹介
- 2006年10月01日
- 新商品Space-E CAA V5 Based 5Axis のご紹介
- 2006年01月01日
- Space-E CAA V5 Based R16 新機能のご紹介
- 2006年01月01日
-
PLMレポート(第4回)
「型設計効率50%UPを実現させるために」
- 2005年10月01日
-
PLMレポート(第3回)
「型設計効率50%UPを実現させるために」
- 2005年10月01日
- Space-E CAA V5 Basedの新たな取り組み
- 2005年10月01日
- Space-E CAA V5 Based R15 新機能のご紹介
- 2005年07月01日
-
PLMレポート (第2回)
「型設計効率50%UPを実現させるために」
- 2005年04月01日
-
PLMレポート(第1回)
「型設計効率50%UPを実現させるために」
- 2005年01月01日
- Space-E CAA V5 Based R14 のご紹介
- 2004年04月01日
- Space-E CAA V5 Based CAM 今後の開発について
- 2004年01月01日
- Space-E CAA V5 Based R12 新機能のご紹介
- 2003年01月01日
- Space-E V5のご紹介
- 2002年10月01日
- PLMソリューション CATIA V5のご紹介