成熟したノウハウと先端技術を未来に活かし
持続的成長と付加価値向上を目指す
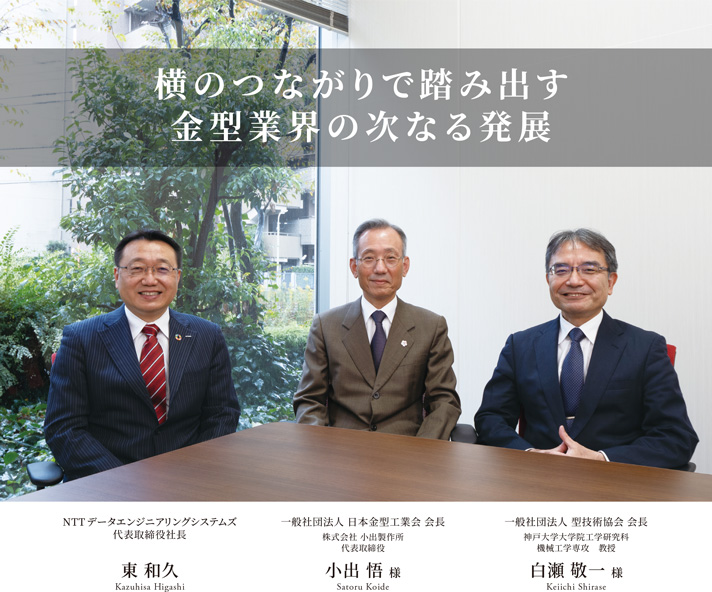
ものづくりの根幹をなす金型。人の技と思考で興隆してきた金型業界では、社会環境の変化に加え技術の進化が目まぐるしい現在、この先進むべき道を模索しています。そこで今回は、金型業界をけん引する一般社団法人 日本金型工業会と一般社団法人 型技術協会から、それぞれ会長の小出悟様、白瀬敬一様をお迎えして座談会を開催しました。金型業界がこれまで培ってきた技術や知見を次代へと継承するとともに金型の新たな価値を創出するため、今何を考え、どう行動を起こすかを探ります。
金型業界を先導する2つの団体
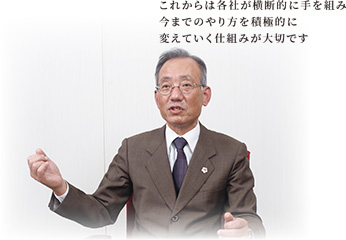
株式会社 小出製作所 代表取締役
小出 悟 様
Satoru Koide

金型年金会館6階
【URL】https://www.jdmia.or.jp/(外部サイトへ移動します)
【設立】1957年11月
【設立の目的】
プレス用金型、プラスチック用金型、ダイカスト用金型、鋳造用金型、鍛造用金型、ゴム用金型、ガラス用金型等に関する各種の事業を行うことにより、金型工業及び関連産業の健全な発展を図り、もって我が国経済の繁栄と国民生活の向上に寄与することを目的とする。
東 私たちは金型業界との長いお付き合いの中で多くのことを学び、設計の2次元から3次元への移行をはじめ、さまざまな変革にも立ち会ってまいりました。本日は、今後の金型業界を切り開く議論の場にできればと、日本金型工業会、型技術協会の両会長にお集まりいただきました。まず各団体のご活動や近況をご紹介いただけますか。
小出 日本金型工業会は主に金型メーカーの会員からなる業界団体で、今年設立65周年を迎えます。会員数は年々少しずつ増え、全国645社ほど加入しています。金型の製造は地域によって取引先や取り扱う種類の特色が異なることから、当初は東部、中部、西部の地域ごとに団体が作られていましたが、海外との競争や国内の産業構造の変化に対応するためにも金型業界全体で一枚岩になっていこうという背景もあり、現在では全国的な団体として活動しています。金型産業は国内で約7,000の事業者、約1.5兆円の市場規模を持つ産業ですから、これを保持するのが私たちの役目だと考えています。
白瀬 型技術協会は産業界と官や学をまたいで人や技術が交流し、経験と知識を融合させることが重要だという考えのもと1982年に設立されました。製造現場で何が起こっているか、研究者が何を考えているか、お互いに理解することで、新しい技術を使った新しいアイデアを生み出したり、共同研究を行ったりと型技術によるものづくりの成長に産学連携で取り組んでいます。ものづくりに正解というものはありませんが、製造業を取り巻く環境が激変する中、これから求められる技術は何か、ものづくりをどう成長させるか、いろいろな観点から議論を交わしています。
東 小出会長は静岡県磐田市に本社を構えダイカスト用、鋳造用金型を設計製作する株式会社小出製作所の代表取締役、白瀬会長は工作機械、CAD/CAM、生産システム、産業用ロボットを研究テーマに神戸大学機械工学専攻の教授としても活躍されています。お二人がおそろいになるのは初めてだと先ほど伺いました。本日は、ぜひそれぞれのお立場から忌憚なくお話しください。
人手不足の中、新たな成長をするためには
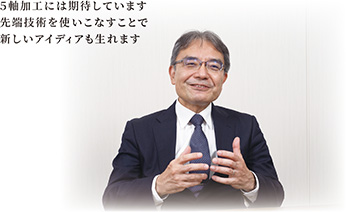
神戸大学大学院工学研究科 機械工学専攻 教授
白瀬 敬一 様
Keiichi Shirase

アブソルート横濱馬車道ビル201号室
【URL】https://www.jsdmt.jp/(外部サイトへ移動します)
【設立】1986年6月
【設立の目的】
型およびその関連分野に関する技術の進歩を図り、会員相互間および関連学協会・団体との連絡提携の場となり、会員相互の支援、交流、その他会員に共通する利益を図る活動を行う。あわせて我が国経済の健全な発展と国民生活の向上に寄与することを目的とする。
東 近年、さまざまな業界団体で会員を集めるのに苦心されている印象があります。日本金型工業会では会員数が増えているとのこと、どのような動機で入会されてくるのでしょうか。
小出 個社単独で活動することの不安がひとつ理由にあると思います。今後のビジネス環境を見据えるのに、自社のみのアンテナでは到底追いつかない状況になっています。腕に覚えがあり技術技能を強みにするだけでは通用しなくなってきて、多岐にわたる視点を持つことが必要です。日本金型工業会が令和2年に策定した金型産業ビジョンでも、「工場から企業への転換」を掲げています。
例えば、現在、金型の取引がある産業は生産金額比で自動車産業が70%強を占めていますが、バブル崩壊前は自動車産業が35%、家電産業が30%だったところ、リーマンショックなどを経てこのような自動車産業に依存した構成になっています。自動車業界が100年に一度の変革期と言われる中、暗中模索ながらも、これから自動車以外の産業の割合を拡大させた産業構造を目指し、手を打つことが求められてきます。
東 工場から企業への転換というところでは、金型業界のお客さまから、収益面で価格競争も大きな問題になっているとお聞きします。
小出 そうですね。仕事を受けるために業界内で下げ合ってきた価格もすでに限界にきています。自分たちでその歯止めをかける努力をしなくてはいけませんし、取引の環境を改善していかないことには今後ますます厳しくなります。金型業界全体が同じ意識を持つとともに、ビジネスチャンスを見つけたり、提案や交渉をしたりするための力を、これまでより高めていく必要があると思います。
白瀬 そのためにも人材育成は課題ですよね。これから発展的なことを進めるには、基礎をしっかり自分のものにした上で考察することが必要ですが、今のように最小限の人手では、若手社員にその基礎を教える余力がないのが現実だと思います。いろいろな経験や失敗をして成長する機会を設けられる時間もありません。
小出 技術面でも、納期に関わる仕事を優先せざるを得ませんから、教育や新しい挑戦に割ける時間の余裕はありません。人材不足の中で金型業界を成長させていくには、生身の人間が必要なところと、ロボットやAIに置き換えるなど自動化できるところを仕分けながら、大々的にやり方を変えていくしかありません。AIやIoT、ファクトリーオートメーションの導入は至上命令のようになっていますが、自分たちとしての答えを持ち合わせた変革が大切です。
白瀬 ロボットやAIはただ導入すればいいものではなく、技術者の思考と親和させ、現場で使いこなす必要があります。今はまだ人が一生懸命頑張って自動化しているところですが、そこを人に頼らなくても自動化できるような取り組みを進めていきたいですよね。
標準化による業界全体の底上げと自社の強みの向上
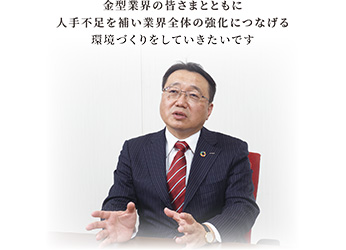
代表取締役社長
東 和久 Kazuhisa Higashi
東 ものづくりの現場で、AIに関する理解を得て導入を進めるのはなかなか難しいと感じています。極端な話、AIで全てやればいいとすると、どの金型メーカーも画一的になってしまいます。白瀬会長もおっしゃるようにものづくりには正解はなく、また、各社の特色豊かな金型製造では、画一化はあり得ません。
小出 実は、製造工程をひも解くと、どの会社でも同じように行っている作業が全体のおよそ6~7割を占めると見て取れます。そうした作業を業界全体で手を組み、AIを活用するなどして標準化し、自動的にこなせるようにすれば、残りの3~4割の各社独自の領域にもっと注力でき、個社そして金型業界としての競争力向上が期待できます。
白瀬 標準化には、他社との差別化が図れなくなる心配はあるものの、全体を一定の水準まで底上げできるメリットがあります。また、その水準やさらに熟練者の手法を示すことができれば、個人の持つ手法や技術を、新たな差別化につなげられる可能性も出てきます。
小出 製造工程を標準化するには、その標準のプロセスをきちんと表現する必要があります。今までやってきたことが、作業者の癖なのか、会社の癖なのか、本当に必要な作業なのか見いだしていくことが重要ですし、その表現のためにもAIをうまく活用できるように思います。
東 私たちはCAD/CAMをクラウド上で提供していますが、その特性とAI技術とを活用し、お客さまの了承のもと作業プロセスを収集、分析して可視化することも将来的に可能になるのではないかと考えています。そうすることで、標準的な手法を皆さまに提供できるほか、誤っている作業や困っていそうなことを察知して解決を示せる可能性も見込めます。クラウドサービスによってお客さまが蓄積されたデータをいかに価値ある情報としてフィードバックしていけるか取り組んでいきたいです。各社の技術や手法を公開できるか、公開可能な範囲と不可能な範囲の判断も含めて、すぐに進まないかもしれませんが、一つの業界内の連携になり得るかと思います。
小出 確かにそうですね。例えば、そのプロセスで本来必要のない作業をした時に注意メッセージが出るだけでも大きな効果です。自分たちにとっては習慣的な作業でもロスや無駄が生まれている可能性がありますが、そうしたことは日々の作業ではブラックボックス化してしまっているので、それを特定できれば改善につながります。
ほかにAIによる標準化が期待されるものに、加工時の火花の色や温度からその時々の加工の仕方を判断したり、直感的に異常を察知したりするような、人の感性や経験に頼ってきたことが挙げられます。こうした従来のプロフェッショナルな技能者が行ってきたことは、もはや伝説の技で、今新たに人が習得するのは簡単ではありません。
白瀬 昔は時間をかけて実際に見て体験し継承してきたのが、先ほども話にあがったように今は一企業がその実践のために割ける時間も余力もありませんし、情報社会で過ごしてきた若い世代としても受け入れにくいですよね。
小出 そう思います。ただ、いわゆる匠の技が生まれた頃は、その様子を映像や音声を使って分析や記録することはできませんでした。ところが今は、それらは可視化することができ、音や匂い、目に入るものを数値に置き換え、コンピューターに保持できますし、経験の浅い社員を教育することも可能になってくるでしょう。
白瀬 先日、型技術協会が広島で行ったワークショップでも、意匠性の高いデザインを実現する金型づくりのために、熟練工の動きをモーションキャプチャーでデータ化して分析し、熟練者との違いを見える化して初心者に習熟させる取り組みの発表がありました。短い時間で的確に熟練工に近づくのが狙いで、そういう動きがどんどん出てきていると思います。
小出 人手が少ない中での育成には、長い時間をかけて経験を積み達成を目指すのではなく、これまでの3分の1や半分の時間である段階までたどり着けることが求められてきます。しかし、例えば異常検知にしても、なぜその異常が発生したのか人が分析して考察する必要性は変わりません。また、数値化や標準化によって表現されたことの意味合いを考え、共通認識することが大切です。そうしたことを、デジタル技術を取り入れ、次世代に引き継ぐのが私たちの責務かもしれませんね。
東 個社だけでなく業界全体で標準化を行うには、まずできるところから進めていき、標準化できない部分はその原因を追究していくことが重要だと感じます。IT領域でも、システム機能開発の要件定義や設計、実装、テストといったプロセスを短期間で反復して作り上げていくアジャイル開発という手法が主流になってきていますが、その考えが応用できそうです。
小出 標準化できそうなことは何かを探り、まずは標準に落とし込んでみて、現時点では人が行う必要があるか否かの検討も含め、一つひとつ進めていくのが良いと思います。また、標準化そのものを目的と捉えるのではなく、その先にある競争力強化のためにも、自社の強みを分析し、理解しておく必要があります。
5軸加工による付加価値の創造
東 製造工程を標準化することで生まれた余力を自社の強化に費やすというお話がありましたが、その取り組みの一つに、新しい製造技術の導入が考えられると思います。
小出 印象の強いものに3Dプリンターがあります。40年ほど前にその元となる装置が日本発で登場し、その後2013年のオバマ米大統領(当時)の演説で注目を浴びた時も、デザインには有効でも物を作るにはまだ難しいというのが私自身の認識でした。しかし、今や金型の部材として使うに値する物が金属3Dプリンターで作れる、削らなくても物ができる、という世界が現れました。今考えている金型製造も変わっていくかもしれません。こうした技術革新は見過ごしてはいけないし、ものづくりのいろいろな可能性を考えていく必要がありますね。
白瀬 最近の動向でいくと5軸加工機ですね。これまで3軸加工でできていたことを5軸加工にする必要があるのかという印象を持たれることが少なくありませんが、その3軸加工でできていたこと自体がこれまでの現場の技能に依るもので、人や部品が変わった時に3軸加工で同じようにできなくなる可能性があります。また、5軸加工を使った新しい型設計をすることで、部品点数を減らす工夫が必要です。今まで3つ4つ5つと3軸加工した部品を組み合わせていたものが、5軸加工ではそのまま一つの部品として加工でき美観や付加価値が上がってきます。これが一般的になれば、普及も進むと思います。
東 3軸加工をただ単に5軸加工に置き換えることは現実的ではありません。しかし、例えば自動車業界ではEVなど大きな変化の中で新しい部品が出てくると見られます。すると、3軸加工では難しく、5軸加工が必要になり、また、5軸加工により提案できる製品の質も向上できると思います。
白瀬 新しい部品に手を広げようと考えた時、5軸加工が扱えるかどうかで可能性が変わってきますよね。Z軸が深くなる加工では、5軸加工の方が高効率、高精度に加工ができます。
小出 小出製作所では、2台の5軸加工機と5軸専用ソフトウエアを導入して、加工の自動化を図っています。ただ、今は専任担当者のノウハウに依るところも多いため、別の人に引き継いだ時に品質を同程度に保つことが難しく、また、段取りのプロセスを作る人員確保の課題もあります。
白瀬 設計者の多くが3軸加工の経験しかなく、5軸加工の知識がないのも一つの問題だと思います。5軸加工の導入に踏み切り、使いこなしていけるだけの環境ができあがっていないというのが現状です。ソフトウエア側を使いやすくする仕組みも必要ですね。
東 私たちもそう感じていて、ものづくりに関わる方々が5軸加工に関する疑問や課題を持ち寄って学べる機会を作っていきたいと思っています。2021年7月、沖縄に開設した「Mold Future Space - OKINAWA」では5軸加工機を導入し、5軸加工専用ソフトウエアと合わせて体験いただいたり、加工ノウハウを習得したりできる場を設けています。
白瀬 5軸加工の良さを知り、今後の加工方法をどう変えるか考えていく転換期にあると思うので、5軸加工を学習でき、また、購入前に試せるのは利点です。高額な機械とソフトウエアを維持して、体験できる場を提供することは大学でも難しいため、大いに役立てられると思います。
東 多くの方にお役立ていただくことで、私たちが提供できるサービスも拡充できます。金型業界全体で加工技術の進展に取り組めるような環境づくりに加担していきたいです。
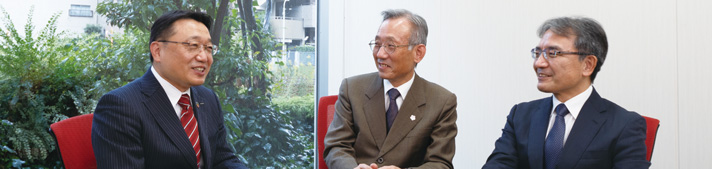
企業間のつながりで探る金型業界の新たな活路
東 ここまでのお話から、金型業界の大きな課題である人材不足、製品の価値向上に対しての、標準化と5軸加工の期待を感じました。
小出 そのために、より実際的な業界内の連携を図ることが重要です。連携によって実現できると思うことはたくさんあり、一つが複数社での高額な機械の共有です。各社が予定通りに使えるよう工程の計画や工夫は必要ですが、どこの会社でも24時間365日機械を稼働しているわけではありませんから、共有することで費用負担を抑えて性能の良い機械を使用でき、製品の価値も上げられます。これは一例で、一つの会社、一つの団体だけで勝負できる時代ではなくなってきたので、横断的に手を組めるような仕組みを築く必要があると思います。
白瀬 私たちも型技術というつながりで、産学や企業間での交流をしていますが、他の領域や業種で何が起きているかを知る機会は少ないです。交流やアンテナを広げることで、これまでなじみのなかった分野からヒントを得られることもあるかもしれません。もちろんそのためには、難しいことや障壁を挙げつらうのではなく、やってみようという気持ちが大切です。
小出 他に業界全体で取り組んでいきたいのが、セキュリティ対策です。金型業界にはサイバーセキュリティやネットワークに精通した人材が少なく、DXの時代を生き抜くためにも、必要な情報や知識を習得して共有し、自分たちに必要な対策を取らなくてはいけません。一方でそこに多額の費用を投資するのも難しいです。
白瀬 セキュリティで重視することは何か、今後5Gで何が変わるのか、など皆さん興味があるものの、詳しい人が社内にいなくて、会社の取り組みに落とし込めていないのが課題ですよね。
東 セキュリティ対策で私たちもお手伝いできることがあります。1社で取り組むのは負担も多く整備も高額になってきますが、例えば日本金型工業会全体に対して、セキュリティに関する体系的な知識やノウハウ、セキュアな環境を提供し、会員企業各社からはそのサービスを使った内容に応じて後から費用を負担いただくような仕組みができるのではないかと思います。
小出 使った分だけ支払いをする仕組みは理解を得やすいと思います。クラウドサービスで利用者のデータを有効活用するとありましたが、そのようにデータを守ることと活用すること、それを私たちにとって価値ある形で提供してもらえることをNDESに期待したいですね。
白瀬 DXの流れにあって、大学教授の立場から課題に感じるのが、学生の興味がITに向いていて、ものづくりを身近に感じたり関心を持ったりすることが少なくなってきていることです。金型業界を目指す人材を輩出するため、学生には魅力ある業界だと思ってもらいたいです。もちろん、いま業界にいる方たちの興味と意欲を引き出せるようにしていきたいです。協会でもいろいろな催しを開いていますが、例えば、先ほどのMold Future Space - OKINAWAで5軸加工を経験するイベントなど、NDESとコラボレーションするのも面白いと思いました。
小出 やはり人が大切ですね。今はリモートでの交流も日常的になり、日本金型工業会でもこれまで対面では気軽にできなかったセミナーや教育の機会を増やせています。一方、育成のためには生の工場を見て刺激や知識を受けることも必要ですから、リアルとリモートを併用して継続的に人を育てていく仕組みを考えているところです。
東 私たちは、日頃「ものづくり分野のお客さまの未来をITで支援します」とうたっていますが、これはお客さまを第3者の立場からサポートすることでなく、一緒に金型づくりに挑んでいくことだと改めて思います。今後も、金型業界の皆さまとのお付き合いから多くを学ぶことで私たちにできる提案を最大限に拡充し、また、皆さまのものづくりの可能性を広げていきたいです。
関連するソリューション
関連するソリューションの記事
- 2025年05月15日
-
最新バージョン
Space-E 2024 R1リリースのお知らせ
- 2025年05月15日
-
東海炭素株式会社 様
5軸加工の優位性を生かし
ファインカーボンの生産性向上と差別化を図る
- 2024年04月01日
-
Space-E 新バージョン 2023 R2
リリースのお知らせ
- 2024年04月01日
-
片山工業株式会社 様
金型技術者の育成強化を図り
成長するグローバル企業
- 2023年07月01日
-
5軸加工 技術情報 連載vol.4
負荷制御を活用した5軸荒取り
- 2023年07月01日
- Space-E 新バージョンCAM 2023、Version 5.11リリースのお知らせ
- 2023年01月10日
-
第31回 日本国際工作機械見本市
JIMTOF2022 出展のご報告
- 2023年01月10日
-
第25回 関西 設計・製造ソリューション展
出展のご報告
- 2023年01月10日
-
5軸加工 技術情報 連載vol.3
CAMの自動中取りと3+2の有効性について
- 2023年01月10日
- 新製品「Space-E/5Axis 2022」のご紹介
- 2022年10月10日
- INTERMOLD名古屋 出展のご報告
- 2022年10月10日
-
5軸加工 技術情報 連載vol.2
東台精機/HEIDENHAINの優位性
- 2022年10月10日
- 新商品「Space-E/CAM 2022」のご紹介
- 2022年07月01日
-
5軸加工 技術情報 連載vol.1
異形工具の活用と効果
- 2022年06月14日
- 「IT導入補助金2022」のお知らせ
- 2022年04月01日
- Space-E Version 5.10リリースのお知らせ
- 2021年07月10日
-
金型づくりの自動化を目指した
「Mold Future Space - OKINAWA」の取り組み
- 2021年07月10日
-
4事業部のご紹介(2)
製造ソリューション事業部
- 2021年03月01日
- 補助金・助成金診断サイト開設のお知らせ
- 2021年01月01日
-
Manufacturing-Space® Version 4.6
新機能のご紹介
- 2020年04月01日
-
大連永華技術有限公司と中国における代理店契約締結
-日軟信息科技(上海)有限公司の閉鎖について-
- 2020年04月01日
-
Manufacturing-Space® Version 4.5
新機能のご紹介
- 2019年10月01日
-
Manufacturing-Space® Version 4.4
サービスインのお知らせ
- 2019年07月01日
-
Space-E Version 5.8リリースのお知らせ
~自動化に向けて進化する~
- 2019年04月01日
-
Space-E
マルチスレッド技術による
特殊隅取りモーフィングモードの高速化
- 2019年04月01日
- Manufacturing-Space® Version 4.3 新機能のご紹介
- 2019年01月01日
-
CAD/CAMシステムオンラインサポートサイト
e-support リニューアル公開のお知らせ
- 2018年10月01日
-
Manufacturing-Space® Version 4.2
サービスインのお知らせ
- 2018年07月01日
-
経済産業省のプロジェクト参加報告
「標準の利用/活用推進委員会」の活動について
- 2018年04月01日
- NTTDATA (Thailand) co., ltd. 活動報告
- 2018年04月01日
-
沖縄マニファクチャリングラボの取り組み
5軸加工機能の強化および実用化に向けて
- 2017年07月01日
-
Manufacturing-Space®が目指す
方向とロードマップ
- 2017年07月01日
-
クラウドを利用した
「ものづくり産業」の生産性向上
- 2017年04月01日
-
Space-E Ver.5.6リリースのお知らせ
~沖縄マニファクチャリングラボの研究成果を反映~
- 2017年01月01日
-
5軸加工への取り組み
沖縄マニファクチャリングラボにおける
5軸加工機能の技術開発
- 2016年07月01日
-
第1回 名古屋 設計・製造ソリューション展
出展報告
- 2016年04月01日
-
Space-E Version 5.5リリースのお知らせ
~生産準備業務の効率化を目指す~
- 2016年02月22日
- ものづくり業界向け「オートサーフェス」サービスを提供開始
- 2016年01月01日
-
沖縄マニファクチャリングラボにおける
5軸加工機能の技術開発
- 2015年07月01日
-
トータルソリューションのご提案(4)
PDMを活用した鍛造解析向けトータルソリューション
- 2015年07月01日
-
Space-E Version 5.4 リリースのお知らせ
~まずは削ることから刷新~
- 2015年04月01日
-
トータルソリューションのご提案(3)
NDESがご提案するトータルソリューションとは
- 2015年01月01日
- マニファクチャリングラボ(沖縄)の取り組みについて
- 2015年01月01日
-
トータルソリューションのご提案(2)
フロントローディングソリューション
- 2014年10月01日
- CAXA社との協業について
- 2014年10月01日
-
トータルソリューションのご提案(1)
STLの活用例
- 2014年07月01日
- Space-E Version 5.3 リリースのお知らせ
- 2013年09月25日
-
金型業界初のクラウドサービス「Manufacturing-Space®」
10月1日サービス開始
- 2013年07月10日
-
東南アジア地域における
Space-E販売代理店の支援強化について
- 2012年10月01日
- 雲をつかむような話し
- 2012年01月01日
-
導入支援レポート(第11回)
Space-E/Moldにおけるカスタマイズについて(2)
- 2011年10月01日
- Space-E Version 5.1 新機能のご紹介
- 2011年10月01日
-
導入支援レポート(第10回)
Space-E/Moldにおけるカスタマイズについて(1)
- 2011年10月01日
-
Space-Eで実現する
デジタルエンジニアリングにおける4つのCサイクル
- 2011年07月01日
-
導入支援レポート(第9回)
Space-Eにおけるプレス金型向けユニット部品構築方法(2)
- 2011年04月01日
- Space-E Version 5.0 新機能のご紹介
- 2011年04月01日
-
導入支援レポート(第8回)
Space-Eにおけるプレス金型向けユニット部品構築方法(1)
- 2011年01月01日
- 5軸加工およびSpace-E/5Axisのメリット
- 2011年01月01日
-
導入支援レポート(第7回)
Space-Eによる3次元金型設計を中心としたシステム構築
- 2010年10月01日
-
3次元CAD/CAM/CAE一体型システム
Space-E/Pressのご紹介
- 2010年10月01日
-
導入支援レポート(第6回)
Space-Eによる3次元金型設計の実現(3)
- 2010年07月01日
-
導入支援レポート(第5回)
Space-Eによる3次元金型設計の実現(2)
- 2010年04月01日
- Space-E Version 4.9 新機能のご紹介
- 2010年04月01日
-
導入支援レポート(第4回)
Space-Eによる3次元金型設計の実現(1)
- 2010年01月01日
- Space-Eの有効活用「電極設計の効率化」
- 2005年07月01日
- Space-E最新バージョンのご紹介
- 2005年01月01日
- Space-E Version 4.3のご紹介
- 2004年07月01日
- Space-E Version 4.2 Modeler & CAMのご紹介
- 2004年04月01日
- Space-E/Global Deformation Version 1.0のご紹介
- 2002年04月01日
- Space-E Version 3.1のご紹介
- 2002年04月01日
- Space-E/STEPのご紹介
- 2001年07月01日
- Space-E最新バージョンのご紹介
- 2001年07月01日
- Space-E/Mold Version 2.0のご紹介
- 2000年10月01日
- Space-E/SolidCAMの紹介
- 2000年07月01日
- Space-E/Moldのご紹介
- 2000年04月01日
- Space-E Version 2.1 のご紹介
- 1999年10月01日
- WindowsNT版 製図支援システム Space-E/Draw のご紹介
- 1999年07月01日
- Space-E Version 2.0 最新機能紹介と今後の展望
- 1999年01月01日
- Space-Eのご紹介