高精度・長寿命の金型で一層の差異化を図る
![]() |
三豊機工株式会社 代表取締役 舟橋 佳孝 様 |
---|
三豊機工株式会社は、独自の冷間圧造工具「ダブルヘックス」を武器に、ボルト・ナット・パーツなどの製造における成形用工具において国内外で高いシェアを誇る冷間圧造工具の総合メーカーです。生産拠点である鹿児島工場は業績に合わせて増築を重ね、関連企業では農園やゴルフ練習場も経営されています。
NDESとは、長くお付き合いいただいております同社の舟橋佳孝社長に、現在のビジネスの状況や新規事業を創造するアライアンスなどについて、お話をお伺いしました。
商社から金型メーカーへ
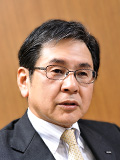
代表取締役社長
木下 篤
木下 御社とは3軸加工機の導入に合わせて、当社のSpace-Eを採用していただいて以来の長いお付き合いになります。はじめに御社の創業からの経緯について、お聞かせください。
舟橋 1965 年6 月の創業で、去年の6月に50周年を迎えました。ネジ用加工機の販売商社として事業を始め、十数年は商社として活動していました。当時、日本のネジは切削が主流で、圧造による量産を行っているメーカーはほとんどありませんでした。そこに海外から圧造技術が入ってきたのですが、加工機はあっても、金型がないということで、金型を調達して加工機とセットで販売をしていました。
ボルト・ナットの金型は消耗工具ですから、リピートの注文があります。そこで、自分たちで金型を作ろうということになり、1979年には本社のすぐ近くに工場を建て、本格的な金型の製造に乗り出しました。
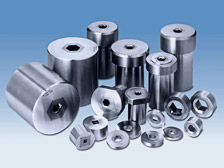
ラインアップ
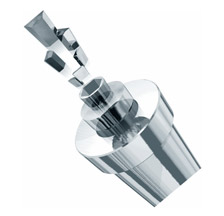
木下 御社の冷間圧造工具「ダブルヘックス」はボルト・ナット製造における最終工程の成形用工具として、現在では国内シェアは70%にも達するといわれています。その工具が誕生した時期とも重なるのでしょうか。
舟橋 工具を開発したのは1980年です。六角のボルト・ナットは丸い材料を塑性変形させて、3工程も4工程もかけて作っていきます。最後に六角の金型で変形させるわけですが、その金型の角部が短期間で割れてしまうことが課題となっておりました。それで、お客さまから「もっと寿命の長い金型はできないか」と相談を受け、いろいろ試行錯誤する中で、逆転の発想なのですが、「割れるのであれば、最初から分割しておけばよい」と考えました。そして実際に分割した6ピースの部材を組み合わせて金型を作ったら、寿命をとても長くすることができました。当時、特許も取得し、35年たった今ではその特許も切れていますが、製法に特殊な部分があるので、他社はまねすることはできないと思っています。
木下 まねできないというのは戦略上大きなポイントですね。
舟橋 見た目は同じでも、製造ノウハウがあります。大きさやバリエーションもたくさんあって、開発当初は六角だけでしたが、今では四角形や長方形などもありますし、特に角部に応力がかかるものはお客さまと相談して作り込んでいきます。
木下 海外でも高い評価を得ていると聞きました。
舟橋 丸型などスタンダードな単純形状の金型は生産も比較的容易ですから、コスト面で海外の安価な製品には勝てません。
しかし、ダブルヘックスは価格が高くても売れております。お客さまは製品寿命を含めたトータルコストで判断しますから、イニシャルコストが高くても、寿命が長ければ最終的にコストは下がります。特に海外のお客さまにとって、製品名のダブルヘックスは、社名の三豊機工よりも知名度が高いようです。
全工程を内製
木下 ネジはあちこちで使われているので、つい見過ごしてしまうのですが、製造業全般でとても重要な役割を果たしていると思います。
舟橋 その通りです。ものとものを結びつける締結ということで考えると、ネジだけでなく、テープ止めや接着、ホチキス止めなどさまざまな方法があります。その中で、一番安全で耐久性があり、使い終わった後の分解もたやすく、一番需要が多いのがネジ止めです。ネジが一番多く使われているのは自動車関連ですが、家具や建築関連、家電品、時計、メガネなど、ありとあらゆるところに使われています。製造業分野では、鉄は"産業の米"といわれて、ネジは"産業の塩"といわれています。
(参考: 産業の基盤・中枢となるもの、という意味で「産業の米」が、産業を活性化するのに不可欠なもの、という意味で「産業の塩」がそれぞれ使われます)
木下 用途によって、強度や材料も変わるのでしょうか。
舟橋 自動車、建築関連、家電向けなど、その納入先によって求められる要求が異なってきます。例えば、自動車のエンジン関連のように重要保安部品となるボルト・ナットは、大変厳しい基準で精度が求められます。
木下 そうしたそれぞれ異なる要件に対応する形で金型の発注を受けるわけですね。
舟橋 当社は金型を100%内製しており、鹿児島工場ですべての金型を生産できる体制を整えています。材料の切断から、粗加工、熱処理、仕上げまで、最後のコーティング(表面処理)も依頼があれば対応可能です。
材料の切断から行う金型メーカーはほとんどありませんが、それも手掛けております。熱処理にもこだわりを持っていて、15kg、30kg、50kg、100kg、300kgの5タイプ、合計11 基の炉を持っています。そして、材質はもちろん、大きさ、肉厚をできるだけそろえて熱処理を行い、硬度は抜き取りではなく全数チェックして、合格したものだけを後工程に回しています。
木下 金型は熱処理によって寿命が変わってきてしまうそうですね。
舟橋 よく料理に例えるのですが、カレーを作るときに、ジャガイモを同じ大きさに切って煮込むとどれも同じように煮えます。しかし、小さく切ったジャガイモと切っていない丸いままのジャガイモを一緒に煮込むと、小さい方は溶けてしまい、丸いままの方は生煮えになってしまいます。金型の熱処理も同じで、大きさが違うものを一緒に処理してはいけません。利益を重視すれば、大きな炉でひとまとめに処理することで、製造コストを下げることができますが、金型寿命に差ができてしまいます。金型は寿命が一番大切なので、この工程にはとてもこだわっています。
圧造機メーカーと協業
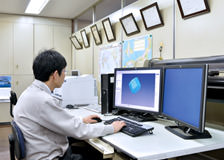
木下 最近、ヘッダー・フォーマーなどの加工機メーカーである、株式会社 中島田鉄工所様(福岡県)とアライアンスを組んで、チタンネジ用金型の開発に取り組んでおられると聞きました。どのような経緯で始められたのでしょうか。
舟橋 中島田鉄工所様とは1年ほど前から協力してチタンネジ用金型を開発していますが、圧造機メーカーと一緒に取り組むことは初めてです。中島田鉄工所様が米ボーイング関連の企業と取引のある会社から金型についての相談を受けられ、当社に声がかかったことがきっかけでした。
そこで、当社で中島田鉄工所製2D3BホットフォーマーNP121HF型を導入して、一緒に対応しようということになりました。ホットフォーマーは冷間圧造も可能で、加熱用のスイッチが付いていてヒーターを入れれば、温間や熱間もできるようになっています。
航空機などに使われる64チタン合金やインコネルは高い強度がありますが、64チタンは約650~700℃という高温で加熱しないと成形できません。昔から材料として64チタンはありますが、64チタン製のネジが市場に受け入れられなかったのは、切削加工では価格が高くなってしまうからです。それを圧造で量産できるようになれば、コストも下がり新たな市場が生まれてくると考えています。
今年は三菱航空機株式会社の小型旅客機MRJが初飛行しますし、米ボーイングや欧州エアバスなどに代表される航空機産業は安定的に拡大していくとみておりますので、これから20年は成長する市場になるのでは、と思っています。自動車向けのように大量のネジを作っているメーカーからすれば航空機産業の市場は小さいかもしれませんが、当社のような規模の企業からすると、とても魅力的な市場です。航空機産業向けの64チタンやインコネルのネジが量産化できれば、自動車でも高い強度が要求されるエンジン部分などへの適用が進み、新たな需要創出につながると考えています。
木下 両社(貴社と中島田鉄工所様)のアライアンスは、その成長産業への進出に向けたキーテクノロジーの創出に不可欠と思いますが、進捗はいかがですか。
舟橋 この1年間で4件のテストを行いました。いろいろな問題が出てきて、自分たちだけでは解決できないので、中島田鉄工所様の智恵を借り、相互に協力しながら進めています。
今後、当社単独では金型の開発が難しいケースがたくさん出てくるとみています。例えば、材料メーカーとの協力です。試作用に圧造機を導入しましたが、まず材料が必要になります。そこで、64チタンを買おうとしたら、材料メーカーは300kgの量から販売するというのです。
私は「64チタンは鉄の6割くらいの比重ですよ。鉄にすると、600kgも買うようなものではないですか。現状ではテスト段階なので、せいぜい50kg程度しか使いません」と事情を話して交渉し、小分けしてもらった15kgを購入できました。自分たちの言い分だけでなく、売れるようにするために協力し合うことで需要も伸ばせるという話をしたら、材料メーカーも協力してくれるようになりました。
木下 自動車向けのプレス型メーカーの話では、最近の高張力鋼板(ハイテン材)だと過去の経験がまったく生かせず、金型を作るのがとても難しいといいます。
そうすると、材料メーカーから、金型メーカー、自動車メーカーまで皆で協力し合わないと、グローバルでの競争に勝つことはできません。
舟橋 おっしゃる通りです。新しい材料、新しい工法などに挑戦するためには、関連企業とコラボレーションというか、アライアンスを組まないとやっていけない状態になっています。
技術の伝承のために工場建設
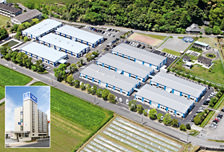
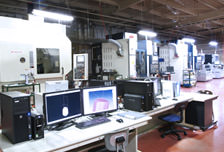
木下 現在、生産はすべて鹿児島工場で行っているとおっしゃられましたね。
舟橋 鹿児島工場は、1991年4月操業開始ですから、もうすぐ25年になります。
木下 どうして鹿児島に工場を作ったのでしょうか。
舟橋 当初、愛知県の本社から近い春日井インター近くに工場があり、NC化をはじめとして自動化に積極的に取り組んでいました。しかし、技術の伝承を考えたときには、体で覚えなければいけない部分がたくさんあります。そうすると、若い労働力をきちんと確保することが必要になります。ところが、この辺りでは大手自動車メーカーや大手自動車部品メーカーの人気が高いので、新人の採用が困難な状況でした。技術者を送り出す側の学校の先生たちも大手の有名企業に入れたいと思っていますし、生徒の意識も就職ではなく、就社になりがちです。
そこで、若手の労働力があるところはどこかと考えて、単純に寒いところより、暖かいところの方がよいと、新工場の候補地を九州にしようと決めました。福岡県はかなり成熟しているので、熊本県、宮崎県、鹿児島県の3県から選ぶことにしました。当時名古屋から飛行機の便が一番よかったのが鹿児島県で、日帰りができました。
そこで、薩摩半島で鹿児島市と枕崎市の中間にある鹿児島県川辺郡川辺町(現南九州市)に工場を作ることにしたのです。川辺町は仏壇の町で、全国の7 割くらいのシェアを持っていて、川辺仏壇として知られています。仏壇作りでは彫金や細かな手作業がたくさんあります。
育った環境の影響は大きいので、実際にやったことはなくても、仏壇作りを見て育ち、手作業が好きな若者がたくさんいるのではないかと考えたのです。
国内生産へのこだわり
木下 25年間で、鹿児島工場はどのように発展してきたのでしょうか。
舟橋 最初に3,000坪の土地を購入し、建物1 棟と社員17名で操業したのですが、現在では社員数が180名と約10倍になりました。建物は増築を重ね、1994年、1996年、1998年にそれぞれ1棟ずつ建てて合計4棟となり、購入した土地がいっぱいになりました。それで隣の土地を3,000坪ほど買い足して、2003年に300坪の建物を2棟、150坪の建物を1棟、2005年にさらに2棟建てたら、またいっぱいになってしまいました。
木下 私が知っている限り、私たちの得意先である金型メーカーは円高影響などもあって、取引先のメーカーが海外に進出するのに合わせる形で、海外進出に取り組んでおられます。御社は海外には出て行かず、25年間鹿児島でやってこられているわけですが、何か理由があるのでしょうか。
舟橋 どこの国に出て行っても、日本と同じレベルの精度と耐久性をお客さまに保証しなければなりません。
例えばタイに工場を開設したとします。タイで金型を作ったから、日本と比べて少し精度が劣るのですとは絶対に言いたくありません。
木下 Made in Japanであっても、Made in Thailandであっても、品質と精度は同じでなければいけないと。
舟橋 そうです。そう考えると、海外に出て行って、100%内製で一貫生産のものづくりを追求することは相当難しいことです。それに国内で金型をたくさん納入させていただいている企業もありますが、一方で納入実績が少ない企業も多々あります。そう考えると、まだまだ市場開拓の余地がある、国内でも伸び代があると思っています。
木下 自動車バンパーなどのプレス加工メーカーが海外へ進出すると、現地でデザイン・インすることになる金型メーカーも一緒に海外へ進出していくことになります。しかし、御社は、国内で精度の高い金型を作っていれば、海外に出て行く必要はないのかもしれません。
舟橋 最近では、お客さまは北米でも欧州でも現地で調達できるものは現地で調達されています。しかし、高い精度が必要で、この金型メーカーが作った金型の方がよいというものは日本から送り込んでいます。高い精度が要求される肝になる部分は日本の金型メーカーのものを使って差異化を図ろうとしているわけです。当社は常に高い精度の金型を作っていますので、お客さまが海外のどこに進出されようとも、お客さまの高度な要求にお応えできる体制を整えていきます。
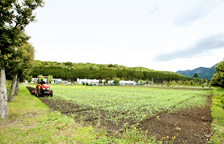
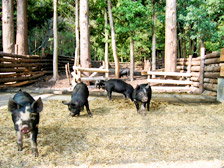
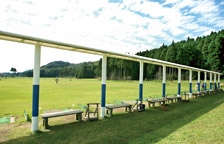
木下 2009年に、「人とシステム」のカスタマーズレポートの取材で弊社担当者が鹿児島工場を訪れたことがあります。当時も舟橋社長はじめ社員の皆様に応対していただきましたが、鹿児島工場の近くでは、農園やゴルフ練習場を経営されていると聞きました。本業とはまったく異なる分野ですが、これは地域貢献のお考えから始められたのでしょうか。
舟橋 バブルの崩壊後、塩漬けになっていた30 万坪の土地があり、それを購入したのがきっかけです。ちょうど食品の産地偽装が大きな問題になっていた頃で、私の父親である会長が偽装問題に憤慨して、それなら本物の黒豚を飼って、おいしい黒豚肉を販売しようじゃないかと言いだしました。ちょうど、工場の敷地の片隅で、名古屋コーチンも何羽か飼っていたので、それも増やして鶏肉や卵を販売しようということになりました。
現在では、薩摩農園という別会社にして、約50 頭の薩摩黒豚、約200 羽の名古屋コーチンを放し飼いして、黒豚肉や鶏肉、卵を直販しています。
ゴルフ練習場は、30万坪ある土地を遊ばせておくのはもったいないと、2012年に南北200メートル、東西500mの10万平米の土地に、天然芝でネットがない450ヤードのゴルフ練習場「三豊ゴルフクラブ」を作りました。ゴルフは今、子どもから女性、年配者まで誰でもできるスポーツになっているので、地域の人たちが集まって情報交換したりする場所にもなっています。今年の3月15日には、LDA世界ドラコン選手権日本予選 鹿児島大会が「三豊ゴルフクラブ」で開催されました。そういった意味では、地域の皆様へのささやかな貢献になっているかもしれません。
現状維持は後退だ
木下 今後の展開についてですが、どのような方向を目指しているのでしょうか。
舟橋 当社が安田工業製の5軸加工機を初めて導入したのが2008年で、その後追加導入し、現在5軸加工機は6台になっています。近年では形状が複雑な金型が増えており、5軸加工機でなければ加工できない金型がたくさん出てきています。放電加工でやっていたものでも、5軸であれば直彫りできるので、5軸で加工が可能なものは置き換えています。放電加工はよいところもあるのですが、加工部分に微小な割れが入ってしまうことがあります。最終工程で磨きをかけますが、本来の素材の特性を活かしきれないこともあります。それに対して、5軸の直彫りはそうした問題はありませんし、金型の寿命が長くなるので、お客さまにもメリットがあります。
また、当社にとっても、リードタイムを短くして、品質も向上させることができます。
木下 金型寿命をさらに伸ばすなど、他社との差異化を出すための努力を続けていきたいということですね。
舟橋 他社との差異化を一番意識しています。簡単なものでも他社と作り方が違えば差異化になり、売り上げにつながります。究極は"闘わずして勝つ"です。偉そうな言い方ではありますが、それを目指して、さまざまな取り組みを進めています。
社員に対しては「現状維持は後退だ」と口を酸っぱくして言っています。売り上げに変化はなくても、中身が変わっていればよいのですが、中身も同じであれば、衰退していくだけです。ですから、現場から上がってくる設備計画なども、以前と同じ理由で何も考えた様子が見られない場合は認めません。いろいろ検討した結果、前と同じだという場合は承認します。どんなことでも、ともかくチャレンジしていこうということです。
木下 最後にNDESへのご意見などありましたら、お聞かせください。
舟橋 3軸加工機からNDESのSpace-Eを利用していますが、その後5軸加工機用にSpace-E/5Axisを追加したときにも、いろいろなことを教えてもらいました。
当社は一人の技術者だけでは使い方がその人の流儀になってしまうので、メーカーさんから複数の技術者に直接指導していただくようにしています。
NDESには、技術者にCAD/CAM操作を丁寧に教えてもらったのでとても助かりました。また2013年秋から利用を開始したManufacturing-Spaceクラウドネットワークライセンスサービスは経費の削減にも役に立ちましたし、営業が客先でノートパソコンを使ってシミュレーションして見せることもできるのでお客さまにも評判がよく、他社との差異化のポイントにもなっています。
木下 当社の製品が御社のお役に立つことができていると伺い、私も大変うれしく思います。本日はお忙しいところいろいろなお話を伺わせていただき、ありがとうございました。
会社プロフィール
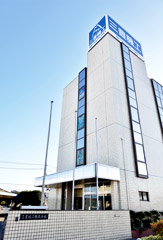
三豊機工株式会社
URL http://www.mitsutoyo.co.jp/(外部サイトへ移動します)
本社 | 〒486-0816 愛知県春日井市東野新町1-4 |
---|---|
設立 | 1965年6月1日 |
資本金 | 3,840万円 |
業務内容 | 冷間圧造工具の製造販売 |
鹿児島工場 | 〒897-0202 鹿児島県南九州市川辺町清水1542-1 |
関連するソリューション
関連するソリューションの記事
- 2025年05月15日
-
最新バージョン
Space-E 2024 R1リリースのお知らせ
- 2025年05月15日
-
東海炭素株式会社 様
5軸加工の優位性を生かし
ファインカーボンの生産性向上と差別化を図る
- 2024年04月01日
-
Space-E 新バージョン 2023 R2
リリースのお知らせ
- 2024年04月01日
-
片山工業株式会社 様
金型技術者の育成強化を図り
成長するグローバル企業
- 2023年07月01日
-
5軸加工 技術情報 連載vol.4
負荷制御を活用した5軸荒取り
- 2023年07月01日
- Space-E 新バージョンCAM 2023、Version 5.11リリースのお知らせ
- 2023年01月10日
-
第31回 日本国際工作機械見本市
JIMTOF2022 出展のご報告
- 2023年01月10日
-
第25回 関西 設計・製造ソリューション展
出展のご報告
- 2023年01月10日
-
5軸加工 技術情報 連載vol.3
CAMの自動中取りと3+2の有効性について
- 2023年01月10日
- 新製品「Space-E/5Axis 2022」のご紹介
- 2022年10月10日
- INTERMOLD名古屋 出展のご報告
- 2022年10月10日
-
5軸加工 技術情報 連載vol.2
東台精機/HEIDENHAINの優位性
- 2022年10月10日
- 新商品「Space-E/CAM 2022」のご紹介
- 2022年07月01日
-
5軸加工 技術情報 連載vol.1
異形工具の活用と効果
- 2022年06月14日
- 「IT導入補助金2022」のお知らせ
- 2022年04月01日
- Space-E Version 5.10リリースのお知らせ
- 2021年07月10日
-
金型づくりの自動化を目指した
「Mold Future Space - OKINAWA」の取り組み
- 2021年07月10日
-
4事業部のご紹介(2)
製造ソリューション事業部
- 2021年03月01日
- 補助金・助成金診断サイト開設のお知らせ
- 2021年01月01日
-
Manufacturing-Space® Version 4.6
新機能のご紹介
- 2020年04月01日
-
大連永華技術有限公司と中国における代理店契約締結
-日軟信息科技(上海)有限公司の閉鎖について-
- 2020年04月01日
-
Manufacturing-Space® Version 4.5
新機能のご紹介
- 2019年10月01日
-
Manufacturing-Space® Version 4.4
サービスインのお知らせ
- 2019年07月01日
-
Space-E Version 5.8リリースのお知らせ
~自動化に向けて進化する~
- 2019年04月01日
-
Space-E
マルチスレッド技術による
特殊隅取りモーフィングモードの高速化
- 2019年04月01日
- Manufacturing-Space® Version 4.3 新機能のご紹介
- 2019年01月01日
-
CAD/CAMシステムオンラインサポートサイト
e-support リニューアル公開のお知らせ
- 2018年10月01日
-
Manufacturing-Space® Version 4.2
サービスインのお知らせ
- 2018年07月01日
-
経済産業省のプロジェクト参加報告
「標準の利用/活用推進委員会」の活動について
- 2018年04月01日
- NTTDATA (Thailand) co., ltd. 活動報告
- 2018年04月01日
-
沖縄マニファクチャリングラボの取り組み
5軸加工機能の強化および実用化に向けて
- 2017年07月01日
-
Manufacturing-Space®が目指す
方向とロードマップ
- 2017年07月01日
-
クラウドを利用した
「ものづくり産業」の生産性向上
- 2017年04月01日
-
Space-E Ver.5.6リリースのお知らせ
~沖縄マニファクチャリングラボの研究成果を反映~
- 2017年01月01日
-
5軸加工への取り組み
沖縄マニファクチャリングラボにおける
5軸加工機能の技術開発
- 2016年07月01日
-
第1回 名古屋 設計・製造ソリューション展
出展報告
- 2016年04月01日
-
Space-E Version 5.5リリースのお知らせ
~生産準備業務の効率化を目指す~
- 2016年02月22日
- ものづくり業界向け「オートサーフェス」サービスを提供開始
- 2016年01月01日
-
沖縄マニファクチャリングラボにおける
5軸加工機能の技術開発
- 2015年07月01日
-
トータルソリューションのご提案(4)
PDMを活用した鍛造解析向けトータルソリューション
- 2015年07月01日
-
Space-E Version 5.4 リリースのお知らせ
~まずは削ることから刷新~
- 2015年04月01日
-
トータルソリューションのご提案(3)
NDESがご提案するトータルソリューションとは
- 2015年01月01日
- マニファクチャリングラボ(沖縄)の取り組みについて
- 2015年01月01日
-
トータルソリューションのご提案(2)
フロントローディングソリューション
- 2014年10月01日
- CAXA社との協業について
- 2014年10月01日
-
トータルソリューションのご提案(1)
STLの活用例
- 2014年07月01日
- Space-E Version 5.3 リリースのお知らせ
- 2013年09月25日
-
金型業界初のクラウドサービス「Manufacturing-Space®」
10月1日サービス開始
- 2013年07月10日
-
東南アジア地域における
Space-E販売代理店の支援強化について
- 2012年10月01日
- 雲をつかむような話し
- 2012年01月01日
-
導入支援レポート(第11回)
Space-E/Moldにおけるカスタマイズについて(2)
- 2011年10月01日
- Space-E Version 5.1 新機能のご紹介
- 2011年10月01日
-
導入支援レポート(第10回)
Space-E/Moldにおけるカスタマイズについて(1)
- 2011年10月01日
-
Space-Eで実現する
デジタルエンジニアリングにおける4つのCサイクル
- 2011年07月01日
-
導入支援レポート(第9回)
Space-Eにおけるプレス金型向けユニット部品構築方法(2)
- 2011年04月01日
- Space-E Version 5.0 新機能のご紹介
- 2011年04月01日
-
導入支援レポート(第8回)
Space-Eにおけるプレス金型向けユニット部品構築方法(1)
- 2011年01月01日
- 5軸加工およびSpace-E/5Axisのメリット
- 2011年01月01日
-
導入支援レポート(第7回)
Space-Eによる3次元金型設計を中心としたシステム構築
- 2010年10月01日
-
3次元CAD/CAM/CAE一体型システム
Space-E/Pressのご紹介
- 2010年10月01日
-
導入支援レポート(第6回)
Space-Eによる3次元金型設計の実現(3)
- 2010年07月01日
-
導入支援レポート(第5回)
Space-Eによる3次元金型設計の実現(2)
- 2010年04月01日
- Space-E Version 4.9 新機能のご紹介
- 2010年04月01日
-
導入支援レポート(第4回)
Space-Eによる3次元金型設計の実現(1)
- 2010年01月01日
- Space-Eの有効活用「電極設計の効率化」
- 2005年07月01日
- Space-E最新バージョンのご紹介
- 2005年01月01日
- Space-E Version 4.3のご紹介
- 2004年07月01日
- Space-E Version 4.2 Modeler & CAMのご紹介
- 2004年04月01日
- Space-E/Global Deformation Version 1.0のご紹介
- 2002年04月01日
- Space-E Version 3.1のご紹介
- 2002年04月01日
- Space-E/STEPのご紹介
- 2001年07月01日
- Space-E最新バージョンのご紹介
- 2001年07月01日
- Space-E/Mold Version 2.0のご紹介
- 2000年10月01日
- Space-E/SolidCAMの紹介
- 2000年07月01日
- Space-E/Moldのご紹介
- 2000年04月01日
- Space-E Version 2.1 のご紹介
- 1999年10月01日
- WindowsNT版 製図支援システム Space-E/Draw のご紹介
- 1999年07月01日
- Space-E Version 2.0 最新機能紹介と今後の展望
- 1999年01月01日
- Space-Eのご紹介